故障ゼロ
故障ゼロ生産におけるゼロ・ベース発想法の概念。
生産活動では人・機械・物の流れが相関関係にあり、機械設備の故障は全体の流れを止め、致命傷となる。そこで生産保全の考え方として提唱されるのが「故障ゼロ」である。機械設備の故障をなくし、最終的には顧客の要求量に対して稼働率・可動率100%とすることを目的とする。近年のロボット化・FA化・CIM化により、TPMとあわせて注目されている。
故障のゼロ・ベースとは機械が故障してから対処する”事後保全”ではなく、機械の故障を未然に防ぐ”予防保全”が基本。また故障の原因は機械設備の”劣化”であり、この劣化の早期発見「感知する点検」が鍵となる。そのためには次のような取り組みが必要である。
故障ゼロの改善
故障に関する一般的な課題
(1)製造部門の関心が低い
・工数上、作業者に生産以外のことはやらせない
・安全上、設備に触れさせない
・仕組みができてない
製造部門の関心
(2)故障解析の取り組みが弱い
設備故障解析
・壊れた部位のスケッチが十分になされてない
・故障品を分解していない
・故障原因の追究が不十分、交換でのみで終了
・再発防止、歯止め、水平展開がされておらず
・現場での故障解析が不十分
(3)保全システムとその運用が弱い
・点検周期・点検箇所・点検方法・判断基準などの基準不備
・部品交換、給油等が一目でわかる保全カレンダーの不備
・故障の履歴システム
(4)予知保全に対する取り組みが弱い
・予知保全は設備について定期的に状態及び測定値の変化を観測し異常を判定 する方法(簡易診断と精密診断がある)
・簡易診断の定着後、精密診断を実施
・精密診断・・・振動量、電流負荷、タイミング、動作時間、温度、音等を数値化 し、管理し変化点を常時把握できる体制にする
DATAにて予知保全の診断
故障低減の考え方
(1)故障の分類整理
・簡単な故障と困難な故障を分類し、簡単な故障を優先して対策し低減させる
・分類・層別方法・・・ライン/発生箇所/故障モード/原因別等
(2)故障解析
・設備に加わるストレス→機械、電気ストレス+温度・湿度・振動・粉塵
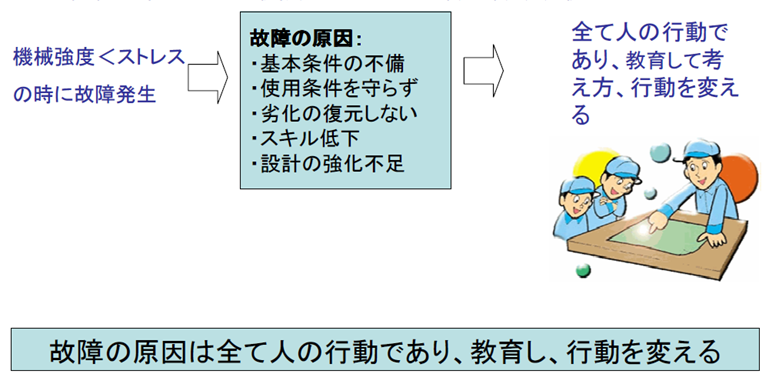
コメント