食品工場のムダの見つけ方
食品工場にある七つのムダ
トヨタ自動車では絞ったタオルをもう一度絞りなおして無駄を無くすと言われており、ムダ撲滅の基本を七つにまとめている。
元副社長の故大野耐一氏が提唱したもので、この思想は食品工場の改善にもそのまま採用できる。材料が異なるだけで、製品の作り方の原理は共通する。
方法としては、現場で今行っている作業を見ながら、七つのムダの概念と独自の着眼点、動作経済の原則の視点から現場を改善する。
七つのムダとは次のようなものである。
①作り過ぎのムダ
②手待ちのムダ
③運搬のムダ
④在庫のムダ
⑤動作のムダ
⑥不良を作るムダ
⑦加工そのもののムダ
作り過ぎのムダーーーー作り過ぎを褒めるな
一つは必要以上に多く作るムダで、例えば注文が百ケースなのに「今日は人手が多かった」「能率があがった」などの理由で百二十ケースも作り、二十ケースを在庫にする場合。
一般に製造現場は、生産に追われるより先行した方が安心できる。そのためどうしても計画より多めに作る傾向がある。上司も不足した時には怒るが、多く作り過ぎても褒めこそすれ叱ることはない。
しかし、作り過ぎは売れない在庫を持つ危険性がある。
もう一つは早く作り過ぎるムダ。生産量は予定を守っていても、早く作り過ぎて時間が余ることがある。また、ラインの能カバランスが悪かったり、各作業者の仕事量と能力に差があると、ラインの途中で中間仕掛品が山のように積まれる。前工程が後工程から追いかけられないように作ってしまうからだ。
それぞれの工程が分かれているとどうしても個々の部品を作り溜めしてしまう。過剰に作った製品は倉庫に保管するが、そのための余分な運搬、保管、管理の手間が増える。売れなりれは廃棄の手間と廃棄損が発生する。
生ものの仕掛品は品質の低下が起き、運搬作業、保管用冷蔵庫、あるいは工程間に仕掛品の置場が必要になる。
作り過ぎや仕掛品の発生を防ぐには後工程の引取方式にし、標準手持ち量を設定し、工程間の同期化、工程の連結を行えばいい。早く作り過ぎる場合は、時間内に物ができればいいので、作業人数を減らし、その作業者を他の作業に回せばいい。
いずれにせよ工場のムダの根源は作り過ぎにあると言って過言ではない。
手待ちのムダ 機械を見ているだけの。閑視人”
手待ちのムダも大きく分けて二つある。
第一は分業の流れ作業で起きる、作業者一人一人に発生する短時間の手待ちである。分業の流れ作業の場合、一人一人の仕事量は同じではなく、仕事の難易度も異なる。そのため各人にそれぞれ短い時開の手待ちが発生する。これを見つけるには「モーションマインド」の目が必要である。
作業者は手待ちを隠すためにわざと動作をゆっくりし、目一杯仕事をしているように見せかける、時開に余裕がある人は左手で取って右手に持ち替えたり、わざわざコンベアの前の方に移動して先取りしたりする。これらは全て手待ちのムダといえる。
第二の手待ちのムダは、どこの現場でもよく見かける光景で、機械のオペレーターが機械につきっきりで作業している状態で発生する。機械が順調に動いているときはほとんど仕事がない。
しかし、トラブルが発生すれば不良品を連続して作ってしまうため、監視の目的で作業員を付けるのが一般的である。こういうオペレーターを「閑視人」と呼ぶ。
機械化された工場でも、機械がトラブルを起こした時に自動で停止しないために人を無駄に使っている工場が少なくない、 機械作業者の手待ちを解消するには自動停止装置が非常に有効である。
運搬のムダ 機械化してもムダは発生する
食品工場にある運搬のムダには次のようなものがある。
・次の作業場が離れているために台車などで運搬する作業。
・次に使うまでの間、仮置きしている状態。
・台車からパレッ卜への積み替え、または積みおろし。
・上下の移動。
・コンベア上からの取りとコンベアヘの戻し作業
これらは、置き台の存在、運搬方法、機械の配置などのレイアウトに起因するものと、作業そのものに起因するものに分けられる。
具の混合機、具送りポンプ、成型機の位置がそれぞれ離れていると、具をコンベア、もしくはパイプで搬送する。見かけは人手がかからず改善されているようだが、後で洗浄の手間がかかる。
特に具送りポンプと成型機の距離が離れており、長い距離を搬送すると、パイプなどに残る具のロスが増え、品種切り替えの時に時間のロスも大きくなる。品質的にもパイプの壁面と具の抵抗が大きくなり、”練れ”が生じて品質低下の原因になる。
これらの改善方法として
①運搬距離をもっと短くできないか。(機械と機械の距離を近づけられないか)
②積み替えをしないように最初からパレッ卜に置くことはできないか。トラックにもそのパレットで積み込めないか。
③ラインバランスをとり、部品の作り過ぎによる中間什掛品を作らない、などの方法を考える必要がある。
在庫のムダ 在庫は諸悪の根源
食品工場の中にも工程間の仕掛品や製品の在庫が多く見られる。
一般的に在庫を持つ目的は、工程の安定か、工程のクッション機能と言われている。
しかし、現実には、在庫は物の流し方、運び方、人員の配置、ラインバランスの取り方のまずさ等から発生するものである。しかも、問題を更に難しくしているのは「在庫は必要だ」という固定観念に捕らわれた考え方である。
大きな倉庫があれば、それが満杯になった時にまた外部倉庫を借りることになる。倉庫に入れなければならないのは作り方、生産計画が悪いのだから、まず出荷に応じた作り方に変えてみることが大切である。
なぜ在庫があるのが悪いのか。
有形的な損失として次のような点をあげることができる。
・資本の固定化-在庫が多いほど資金が固定化され、在庫倒産の危険すら発生する。運転資金が眠り、金利が発生する。
・在庫そのものの問題-ライフサイクルが短い昨今、在庫した商品の陳腐化による廃棄損、長期在庫による品質劣化、鮮度問題、日付け問題が出てくる。
・倉庫建設と維持の費用-倉庫建設のための土地、建物の費用、自動倉庫ならスタッカクレーン、パレット、フォークリフト、電気代などのエネルギー、保管・人出庫のための人件費、伝票、在庫管理のコンピュータ事務経費の発生など。
無形的な損失としては次のようなものがある。
・在庫があるための安心感による生産士気のたるみ。
・他の問題を隠してしまう。在庫があるための運搬のムダ、手待ちのムダ、動作のムダ、設備能力のアンバランス、人員過剰などのムダがあることが見えなくなってしまう。
・機械故障の慢性化、人手不足などの生産システム上の欠陥を改善するアクションが遅れる。
・先入れ、先出しが困難で優先順位も不明になりやすい。
在庫は数えればきりがないほど多くの問題を隠している。”諸悪の根源”である。よく考えて見れば作り過ぎ、買い過ぎの結果が在庫になっている場合が多い。対策としてはサイクルタイムを中心にした生産、溜まりのないレイアウトヘの改善、生産のライン化、引取方式の採用など抜本的な改善が必要である。
工場に在庫を多く持っていると障害物の岩が隠れてしまう(下図)。水面は穏やかだが、障害物を改善せずそのまま在庫を少し減らせば岩が頭を出し、水流を乱すようになり、それだけでトラブルが発生してしまう。ここではじめて工場が抱えていた問題点が見えてくる。
この問題点の障害物を崩し、在庫量の水準を下げるとまた別の問題が現れてくる。そのたびにその障害物を取り除いてやれば、在庫が少なくても川の流れは穏やかとなる。
この様にして改善が進行するのである。
動作のムダー塵もれば山となる 繰り返し作業のムダ
食品工場で動作のムダが最も多いのが繰り返しの多い手作業の部分である。つまりモノを取ったり、置いたり、トレーに入れたり、段ボール箱に製品を詰めたりする作業だ。
例えば一回ごとに手を伸ばし、部品をトレーに入れる作業があるとして、部品の位置とトレーの位置が離れていると手を一杯に伸ばすため0.8秒かかる。手を伸ばす距離を短くして0.5秒に短縮すれば作業は62.5%に減少する。もし、この作業を一日二万五千回繰り返したら一日当たり2時間の差が出る。
また、歩行も無駄な作業である。それぞれの機械を真横に近づければ、度々歩行を繰り返さなくてもいいのに、それをせず、毎回歩行を繰り返している例がよくある。
ある冷凍食品工場では、冷凍されたトレー入りの商品を袋に入れ、それを隣のシーラーでシールし、段ボール箱に詰める作業をしていた。袋入れの作業を行っている所に90センチ×180センチのテーブルがあり、その先に連続シール機が置いてある。そのため袋入れの作業者が二名つき、一人が袋に入れた仕掛品をテーブルの上に置き、それをもう一人が取りに来てシールし、段ボール箱に詰め、毎回数歩の移動を繰り返していた。分業に使うテーブルがあるためにムダな歩行が発生した例と言える。
そこで、「テーブルを除きなさい」と指示すると、作業者は「テーブルがなければ袋に入れた製品を積む場所がなく、仕事ができない」と答えた。テーブルを取り除くだけで作業者を一人減らせる。これなどは典型的な動作のムダ、運搬のムダである。
不良を作るムダ 本当の原因を見つけろ
ある食品工場では「製品歩留りが96%まで上がった、目標管理ができて大変良くなった」という話を聞いた。
私は驚いて「99・6%の間違いではないか」と聞き返した。
通常の成型品の歩留りは99%を超えることを目標としている。最終製品で不合格になると、フルコストがかかっているだけにそのダメージは非常に大きい。
工程内で常時不良品が発生しているのは発生する原因があるからで、真の原因を追求してそれを退治することが必要である。不良品の退治に対症療法は禁物である。
加工そのもののムダ 付加価値のない作業
今の作り方は正しいのだろうか、その加工工程は省けないのか、と常に加工工程に目を向けなくてはならない。
食品工場でよく見られる。加工そのもののムダ”のひとつに、段ボール箱を別に組み立てておき、必要に応じて運んでくる作業がある。
例えば段ボール立て機を入れ、段ボール箱をまとめて生産し、カゴ台車に積み上げ、その台車を作業現場まで運んで置くような作業では、そのために作業現場が狭くなり、多くのムダが発生する。製品が出てきたところで段ボール箱を組み立てながら箱詰めすれば工程がひとつ削減できる。
調味料をバッチずつ、別の部屋で、専門の作業員をつけて計量・配合している風景もよく見かける。ポリ袋に入れ、いちいちその口を結んでいる。
なぜ使う現場で計量しないのかと聞くと「計量ミスが起きる、入れ忘れると大変だから」と答えが返ってくる。
同じ工場内で使用するのに、わざわざポリ袋に入れて封をする必要はないはずである。しかも封をすれば使う時に開封する手間が増え、全く付加価値を生まない仕事を二度も行うことになる。
調味料などはプレミックスしておき、使用する場所で計量すれば小分け作業を削減できる。常に今の工程は正しいかという日で自分の工場を見ることが大切である。
作業改善着眼点の利用
作業改善着眼点図はムダを仕分け分類したもので、図の丸い中に囲まれているのが作業の構成である。その中の主加工のみが主作業で、そのほかの作業と思われるものは付随作業、または不要な作業である。
漠然と現場を見ていると、この付随作業や不要作業も必要な作業のように見えてしまう。作業員の動作の中身を的確に把握して、無駄な動作を排除する必要がある。
その際に活用できるのが 作業改善着眼点図です。
現場の作業改善は、この着眼点の幾つかを利用して解決する。混在しているムダをひとつひとつ解きほぐす手段として利用できる。

作業改善着眼点図
次にそれぞれの改善着眼点の詳細を解説。
エ程連結のレベルを高める
次工程との距離を縮める:
前の作業と後の作業の間に距離があると無駄な運搬が発生する。機械で物を作る場合でも、機械と機械の間に距離があるとコンベアか何かで運搬しなければならない。
品物の滞留をなくす:
生産現場の中で、工程と工程の間に籠などへの横取り品があれば、工程が連結していないと言える。こうしたムダが発生するのは設備能力がアンバランスになっているか、分業が進み過ぎていて、それぞれの所で団子作りをするためと考えられる。
その場加工にする:
例えば段ボール箱を他の場所で作り、組み立てた物を運んできて製品を挿入すると、運搬作業が発生する。段ボール箱は使う場所で、使用する人が組み立てながら製品を入れるようにする。
調味料は計量室で小袋に量って封をし、使用場所に運搬しておくよりも、使用する作業者が自分で計量しながら行う。たまねぎのミンチを予め作っておかないで、使う人が自分で使う時にミンチするのも”その場加工”である。
分業が進み過ぎている:
それぞれの作業を分業で行っていると、互いに自分の能率のみを追求し、他人の作業状況をおろそかにしてしまう。そのため、それぞれの所に仕掛かりの溜まりが発生し、無駄な運搬作業を生み出してしまう。

分業のムダ
設備能力に大きな差がある場合:
例えば野菜のミンチを非常に大きな能力の機械で行う場合、専任の作業者を付けてしまうと野菜処理に集中するために処理し過ぎ、多くの入れ物と保管場所が必要になる。
有効な作業を見つける
人がすべき仕事と機械がすべき仕事を分ける:
食品の生産には多くの機械が使われている。例えば具の混合にはミキサーを、焼売の成型には成型機を使う。
機械で自動的に物が出来るのに、それぞれの機械に作業者がついている。作業者の仕事は、ミキサーであれば原料を投入し、スイッチを押すこと。成型機なら具を供給する、トレーを供給する、不良やトラブルが発生したら機能を止めてトラブルを解消するなどの作業であり、物を加工しているのは作業とではない。機械を監視するのは有効な竹業ではない。
積み替えや容器の移し替えは止める:
パレットや台車に積み替えたり積み直したりする作業は付加価値を生まない。箱に入った半製品をテーブルに移し替えてそこから袋やトレーに入れる作業では、テーブルヘの半製品の移し替えが無駄な作業である。
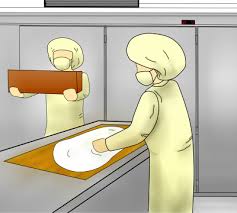
積み替え
ながら作業を利用する:
自動洗濯機や自動炊飯器のような家庭の電化製品にはタイマーがあり、スィッチを入れるだけで洗濯や炊飯ができる。その間に掃除やその他の仕事ができる。工場でも機械が稼働している間、他の仕事ができれるように工夫すればいい。これを”ながら作業”という。
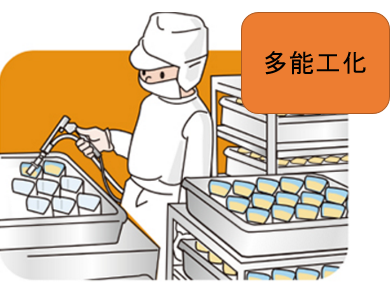
多能工化
持つ、保持する、押さえる作業を止める:
袋を片手に持つ、材料を片一方の掌に乗せてそこから取るなどの作業は片手が仕事をしていないことになる。
目的、原因を追究する
作業の発生原因を追究する:
何故その作業があるのか、その作業は止めることができないのかを考えてみる。
例えば最後の清掃で、機械の外側に食材がついて汚れているために機械全休を水で洗わなくてはならないとしたら、なぜ外側に食材がつくのかを考える。もし外側が汚れていなければ、拭くだけで済む。
不良の発生源を止める:
床に物が落ちていなければ、床から物を拾う必要もなく、水で洗い流す必要もない。
機械のトラブルを減らす:
機械はトラブルを起こすものと決めつけ、そのためにオペレーターをつけているが、トラブルの原因をなくせばオペレーターはいらなくなる。
作業の目的をはっきりさせる:
ベルトコンベアに多くの作業者をつけ分業で仕事をさせた場合、流れる数量が多いと混乱し、整理などを行う人が必要になる。この場合の整理などは有効な作業ではない。

食品工場 分業
作業の発生場所を集めて減らす
離れ小島を作らない:
作業がどんなに少なくても、作業が発生すればそこに作業員がつかなくてはならない。0.3人や0.5人分の作業量でも、離れたところで作業が発生するとそれぞれ一人の作業量として計算してしまう。それぞれの少ない作業を一か所に集めることができれば一人で済む。
その場加工とする:
離れ小島と同様に、作業者が他の作業をするのに十分な余裕があるのに、手待ちをさせて遊ばせている場合が多い。その時には前工程の作業を取り込む様に考える。
多工程持ちにする:
通常は一つの作業発生場所に一人の作業者を配置する場合が多い。しかし、機械にトラブルや異常が発生した時に止まるようにすれば、そこに作業者がついている必要はない。
多台数持ちとする:
多工程持ち同様、一台の機械を同時に持つ場合を言う。これを可能にするためには多工程持ちと同様に自動停止が必要になる
作業の行動範囲を狭くする
次工程の作業や前工程の作業現場が離れていると、移動だけで時間がかかり、作業の進捗がわからない。出来るかぎり狭い範囲での作業とする。

工程間を短く
取り扱い数や部品を減らす
・機械や容器を減らす:
次の工程に移す場合、材料を直接、投入する、ベルトコンベアやバケットコンベアを利用していれば、洗浄や多くの手間が発生する。
補給型作業の回数を減らす:
焼売の自動トレー取り成型機などでトレーのストック容量が少ないと、補給回数が増えて多台数持ちをさせる場合に無理が生じる。その時はトレーのストック容量を多くし、補給の間隔を長くする。
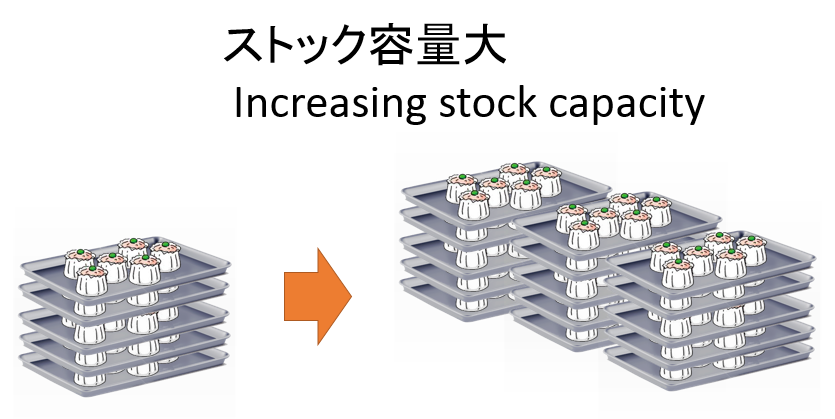
ストック容量大
空間を利用する
平面を使わずに空間を利用する。
工程の連結を上下で行うI天井までの高さが十分あるのに、平而的に機械を並べ、そのために余分な作業を発生させている場合がある。
下図のように縦ピロー包装機の上に計量機が乗ればバケットコンベアが一台不要になる。包装機も計量機も能力に応じて高さ、大きさが異なるが、必要最小限能力の機械を選択すると小型のものとなる。
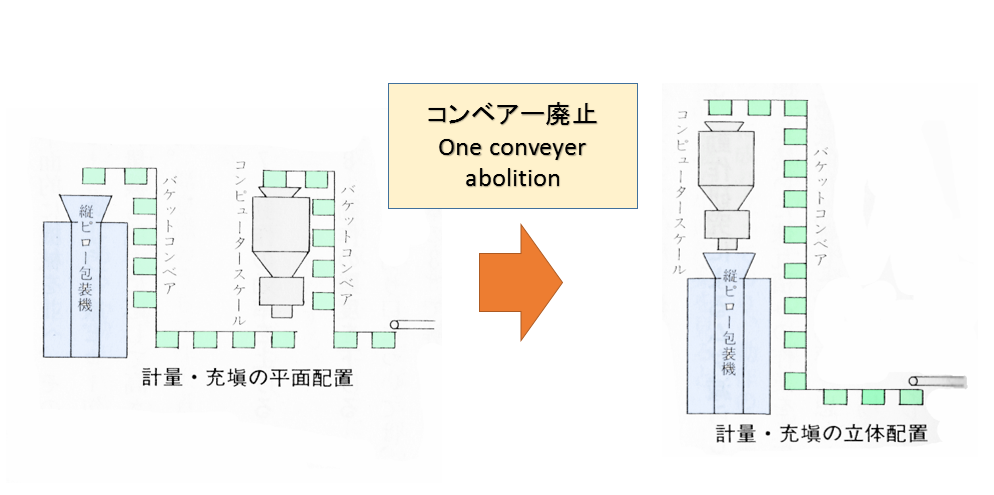
コンベアー廃止
動作の効率を上げる、 動作の難度を下げるについては次に章にて解説。
動作研究によるムダ減らし
四千年続いた煉瓦積みの作業を三年にわたり研究したギルブレスという人物は、この伝統的なやり方を徹底的に改善し、必要と思われていた十八の動作を五つにまで減らした。
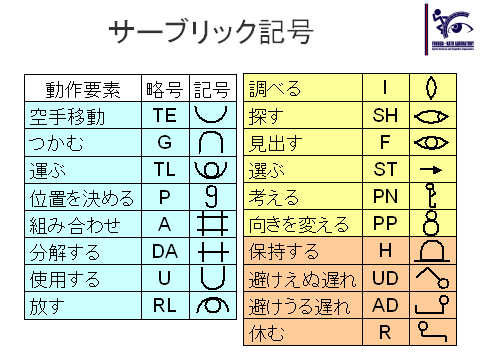
サーブリック記号
この時の改善の体験から「工場の中にある作業のうちで。働きのある作業”は十八の要素動作(サーブリック=Thebrig ギルブレスを逆から読んだ造語)で全てを表すことが出来る。作業改善はこのサーブリックを用い、ムダ、ムラ、ムリを省けばいい」ということを見つけた。
このような微細動作研究(モーションマインド)はギルブレスの研究から始まった。
その後多くの研究者たちにより無駄、無理な動作を排除する研究が行われ、「勁作経済の原則」という作業改善手法が発表された。
食品工場の中の一つの作業にも最も疲労が少なく最大の効果をあげる方法がある。これは一定の法則の上に成り立っており、動作の改善にもこの法則が大変役に立つ。
食品工場の生産作業を見ると、「主作業」と呼ばれる主加工作業で、「型を変える」「質を変える」「組み立てる」「分解する」「使う」などに分けることができる。これらの作業は’働きのある作業’といえるが、一般に工場ではこれらの主加工作業の大部分を機械が行っている。
作業改善着眼点に示したように、主加工の周囲には付随作業として「検査作業」「運搬作業」「停滞」「手待ち」などが存在する。
これらを漠然と見ていると、いかにも仕事をしているかのように見えるが、無くすことができる作業である。
更に、無意識のうちに作業者により行われている動作もある。これは「空動き」「掴む」「手放す」「探す」「選ぶ」「持ち替える」「保持する」などである。
今回の主題である「動作経済の原則」の中から、食品工場に使える原則をあげると次のようになる。
身体の使用の原則
①両手作業は同時に始め、同時に終了する
②両手は同時に反対、または対称方向に動かすのがいい
③手の動きは、仕事ができる最少の動作量とする
④上体や腰を捻るような勣きはできるだけ少なくする
⑤小さな物を填(は)めるような作業は、指先や手のひらでできる動作とする
⑥窮屈な無理な姿勢をしない
⑦体の向きや動きを急激に変えることを避ける
⑧体の重心を上下させることを避ける
⑨動作の順序を自然の流れに逆らわないようにし、適正なリズムで行う
⑩できるだけ注意力がいらない無造作な動作で作業が行えるようにする
この「身体の使用の原則」を食品生産の現場作業に具体的にあてはめてみよう。
両手を有効に使う:
例えばピザのトッピングを行っている状況で、左手の上に具材を持ち、右手でピザの上に乗せている場合、左手は容器の代わりとして使用されてしまう。
両手を使うためには、適当な容器を身近に置き、その中から両手を用いて部品を必要な場所に置くように改善する。
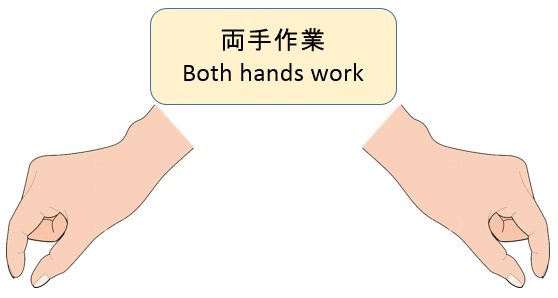
両手作業
手の動きを最小限にする:
大きな作業テーブルの周囲を数人の作業者が取り囲み、手をのばして中央に置かれている部品を収って袋詰めしている作業がある。
この場合、何故目一杯手をのばして作業しなくてはならないのか。
この理由は大きなテーブルを使うため、部品の位置まで距離が離れているために起きる。
改善するには、作業台を小さくし、手を一杯にのばさなくても済むように、全ての作業を狭い範囲で行えるようにする。

作業台の大きさ
体の向きを大きく変える(反転作業をなくす)
ターンテーブルに製品をうけ、そこから次の包装機などに製品を移し換えるとき、身体を180度捻っている。ターンテーブルを廃止し、コンベア等で包装機の投入口の前に物がくるようにし、少なくとも前腕の動きで投入できるように改善する。
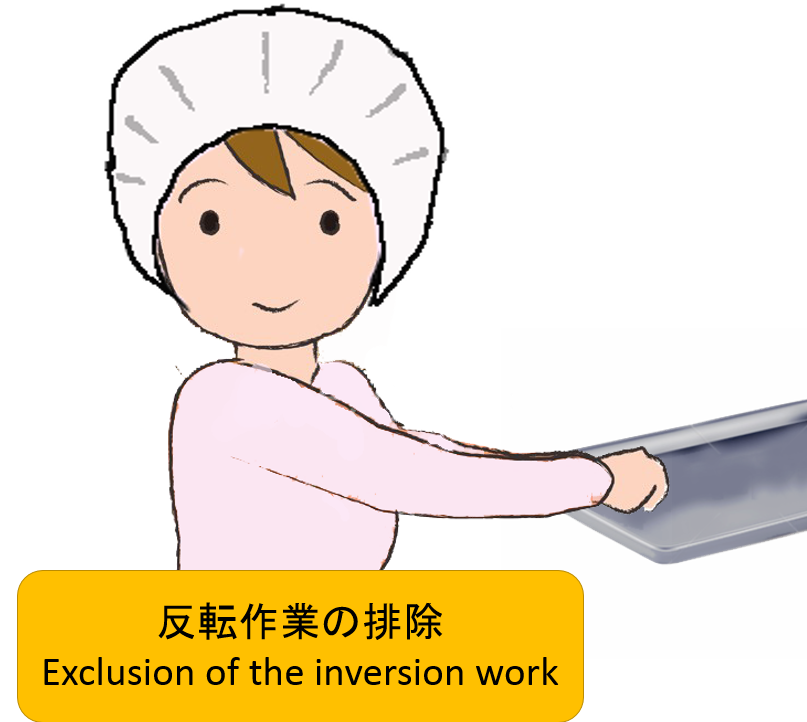
反転作業の排除
体の重心を上下させない
床近くに製品の容器を置き、毎回身体を折り曲げながらそこから製品を取り、次の工程に流す場合がある。次の工程と同じ高さに合わせるだけで生産性は大幅に向上する。
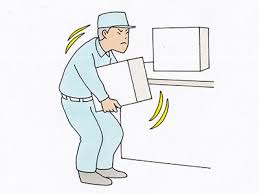
作業時の高さ
無理な姿勢を止める:
コンベアやテーブルの上に乗せた段ボールに製品を入れる場合、無理な姿勢で仕事をすれば、効率が上がらず疲労する。
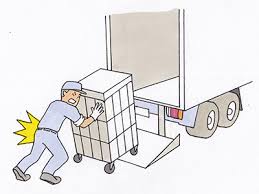
無理な作業
注意力を少なく、無造作に作業する:
盛りつけなどの作業の場合、部品を自分の前面に、盛りつけ順に置いてあれば、トレーごとに同じ手順で盛りつけられ、神経をつかわずにすむ。トレーをテーブルー杯に並べると入れ忘れの発生率が高くなり、神経を使う。
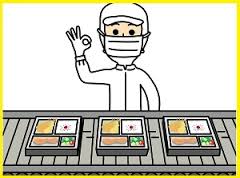
作業が容易
場所と配置についての原則
①材料、部品、トレーなどの容器は全て定位置に置く
5Sの整頓にも通じることだが、部品と作業者との距離が短く、しかも置く位置が決まっていることが、繰り返し作業の効率を上げ、間違いを防ぐコッである。
②材料は次の作業者が楽に作業できるように一定方向に置く。
③材料や部目皿は作業者の周辺に、できるだけ前面の近くに配置する
④材料や部品は動作に最も都合のいい場所に置く
⑤物の移動は出来るだけ上下運動を避け、水平移動とする
⑥物の移動にはそろばん玉のような滑り移動し易いものを利用する
⑦出来るだけ”落とし入れ”にする
⑧作業台の高さは、作業の性質や作業者の身長に適したものとする。また、作業者に合わせた足台を作る
⑨作業に適した採光や照明を考える
場所と配置についての原則を生産現場の作業に具体的に置き換えると、手作業を中心とした盛りつけ作業や挿入作業などにこの原則が利用できる。
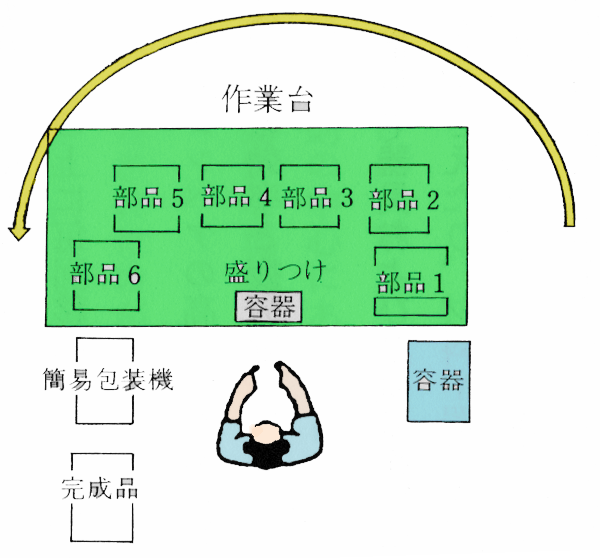
材料や部品は動作に最も都合のいい場所に置く
・部品を定位置に置く
5Sの整頓にも通じることだが、部品と作業者との距離が短く、しかも置く位置が決まっていることが、繰り返し作業の効率を上げ、間違いを防ぐコツである。
・物の移動は水平移動とする
水平であれば持ち上げることもなく、そろばん玉のような滑り易い治具(じぐ)の利用も可能となり、楽な作業となる。
床からテーブルの上に毎回移動させると上下の運動量が大きく、エネルギー消費も時間の消費も大きい。
・テーブル高さ
テーブルやコンベアの高さは作業者個々の背丈には関係なく決められている。そのため長時間作業を行えば、その効率と疲労度が異なる。個人が最も作業し易い高さに調節できる足台を作ればいい。
道具や器具および設備の設計についての原則
①手で袋を押さえたり、材料や器具を保持している動作をなるべく避ける
②フットスイッチのように足の操作を用いたほうが、一層効果がでる仕事の場合は手を用いない。
③二つ以上の工具は出来るだけ組み合わせる。
④汎用式(万能式)の道具は使わず専用型のものを用いる。
⑤テーブルや機械が楽に移動できるようにキャスターを付ける。
道具や器具および設備の設計についての原則を生産現場に当てはめれば、作業改善着眼点図の「有効な作業を見つける」や「動作効率を上げる」などの着眼点とも一致する。
具体的には次の例がある。
(1)手で押さえる動作を避ける
シュートを使い、物を入れる場合、袋を手で押さえ保持するのではなく、手を放しても落ちないよう工夫する。
(2)足を使う
手と足を同時に使用する場合、手で作業しながら足でスイッチを入れる、膝でスイッチを押すなど手以外の身体部分を利用する。
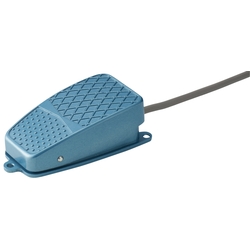
フットスィッチ
(3)機械やテーブルにキャスターを付ける
キャスターが付いていないと小さなテーブルーつでさえ移動しにくい。離れたところで作業している悪い例が非常に多い。
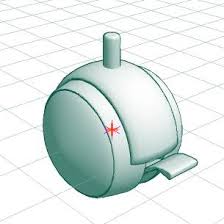
キャスター
(4)高価な汎用機より安価な専用機
汎用機は高速で高価なものになり易い。そのため品種ごとに切り換えて生産しないと機械投資が無駄になる。しかし、今の世の中は多品種化が益々多くなっている。汎用機では切り替え回数が多くなり、切り替えのロスタイムが多くなる。例えば、留め型商品の天ぷらのおつまみなどを400個生産する時、高速のコンピュータスケールを用いると、使用時間10分、掃除時間40分というような無駄が発生する。
MODAPTS(モダプツ) 作業分析方法
動作経済の原則の中心にあるのは”ムダのない作業”をどのようにして作り上げるか”が大切である。
一つひとつの動作を現場で測定しなくとも、時間値が推定できれば、設計段階で要員査定も可能となる。
この目的で開発されたのがモダプツ(MODAPTS=Modulal Arrangement of redetermind Time Standads)いう作業分析方法である。モダプツ法はオーストラリアのハイドが「生産の動作の種類は二十一に集約できる」ということを発見し、一九六六年に発表した。
モダプツは色々な動作を時間値で表しているが、ここでは参考までに指先から肩の動作までの時間値を載せてみる。
この方式によれば、手の部分の動きは図のようになり、指先の動作であれば一方向の動きが0.13秒(MODAPTSでは正確には0.29秒)であるから、往復で0.26秒となる。手を目一杯仲ばした作業では往復で1.3秒の時間がかかる。
 作業分析方法.png)
MODAPTS(モダプツ) 作業分析方法
作業者により作業の速い遅いがあるが、よく見ると手の速さよりも作業位置が悪く、手を目一杯伸ばして作業している人と、手前で作業している作業者とではその効率が大幅に異なってくる。
もちろん腰をかがめたり、体を百八十度捻るような動作が入ればその分だけ時間値が大きくなることは言うまでもない。
「モーションマインドのある人」とは、この動作経済の原則が頭の中に染み込んでおり、作業現場を一目見た時に、それぞれの場面で、それの最も適したやり方がすぐ頭の中に浮かび、改善に結びつけられる人のことを言う。
これは現場で作業を見る目を訓練すれば、誰にでも到達できることだと考えている。
尚、参考までに、良く利用されるモダプツの終局動作記号と時間値を次に示す。
〈さわる、つかむ勤作〉 G0:触れる動作
G1:普通のつかみ
G3:注意力を必要とする複雑なつかみ
〈置 く 動 作〉 P0 :簡単に置く
P2:注意して置く
P3:かなり注意して置く
〈一歩 の 動 作〉 W5:
モダプツを用いた作業分析事例
モダプツ法を用いるとそれぞれの作業に要する時開を事前に計算で知ることができ、必要な作業要員の査定も可能になる。
ここで一つの事例を見てみよう。
下図はある工場の連続冷却機の出口で、ターンテーブルを使いトレー取り包装をしている作業の様子を示したものである。
ここの作業は分業で、空トレーを出す作業員、ターンテーブルに乗った製品をトレーに入れる作業員二名、トレー入りの製品を包装機に乗せる作業員二名の計五名で作業を行っていた。
この商品が前から流れてくる量は1分あたり五十二個だった。
この作業でラインの律速になるのはトレー入り商品を包装機に乗せる作業で、モダプツの記号‐掴む(Grasp)はG、移動(Movement)はM、置く(Put)はPで表すと次のようになる。
簡単に掴む作業はG1、上休を一八〇度回す移動はM5、位置を定めて置くのはP2として、トレーを包装機のヒンガーに入れる作業をモダプツで表すとG1,P2,M5となる。
時間値は0.129×13=1.667秒 即ち一回ずつの作業に約1・7秒かかる。
1分間の作業回数は
60秒÷1.677秒=35.8回となる。
一回毎のトレー挿入動作に約1.7秒かかるために一名では三十六個しか移せない。そのためムダがありながらトレー移動に二名付き、計五名で包装することになる。
ターンテーブルを使用した作業では包装機との間に距離があるため、それぞれの作業を分業せざるみ得ない。そのためトレーを出す人、トレーに入れそこに積む人、それを移す人のそれぞれの所でムダが発生している。
 作業分析方法2.png)
MODAPTS(モダプツ) 作業分析方法
動画 食品工場 カイゼン事例
改善事例の実写映像から「改善定石」を パワーポイントをフル活用して解説!
*不良検知の自動化
*補助具活用
*食品工場のカイゼンについては下記の文献に色々な活動事例等が更に詳細に記載されています。
参考文献:
金をかけずにすぐできる!食品工場改善入門 小杉 直輝 (著)
食品工場のトヨタ生産方式 弘中 泰雅 (著)
続 食品工場改善入門 小杉 直輝 (著)