ムダ取り 実践
「以下のコンテンツについては、『すぐに使えるトヨタ生産方式 導入・実践ノウハウ集』(著者:竹内鉦造)から抜粋したものであります」
ムダ取りとは
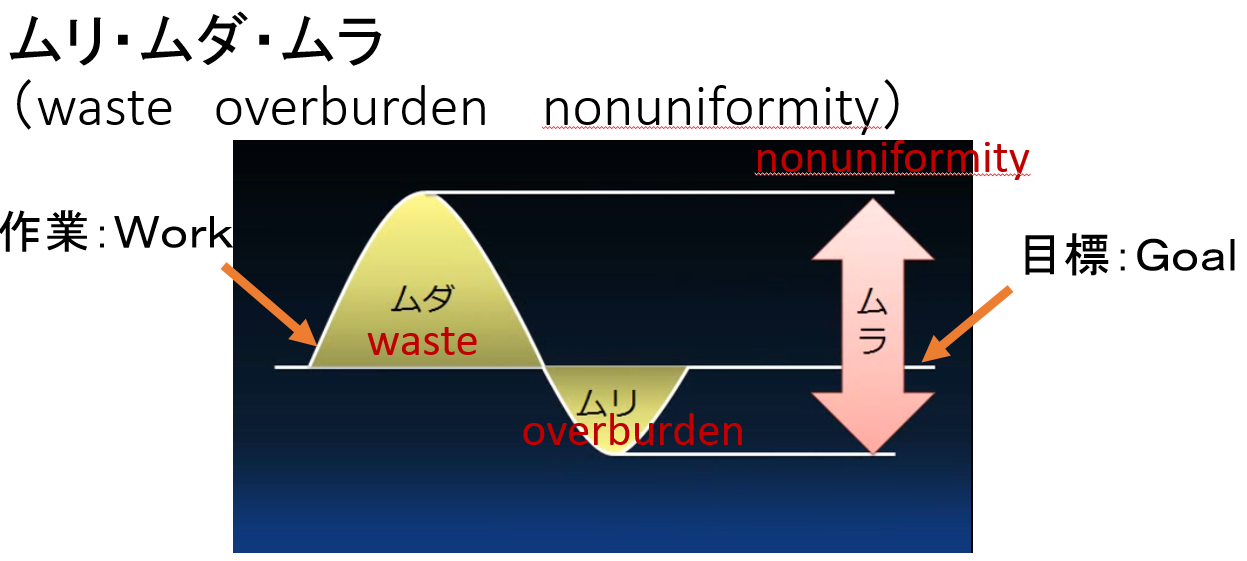
ムリ、ムダ、ムラ
運搬のムダに対する考え方
工程分析の単位でムダを見ていくと、加工(または作業)、運搬、検査、停滞、貯蔵となり、付加価値を生まない工程は、すべてムダな工程です。
製造工程のうち、付加価値の生じるものは加工と検査だけです。運搬、停滞、貯蔵はどんなにがんばっても、付加価値を生まないのです。極端な言い方をすれば、検査も付加価値を生まないのです。
トヨタ生産方式では、運搬はジャスト・インータイムに大きな影響を及ばします。よって、必要なものを、必要なときに、必要な数量だけ、最低限のコストで供給するという思想から、少量運搬が基本になります。
少量運搬だと、その都度、要求に合わせて運搬する必要があります。しかし、距離が遠い場合、少量運んでいたのでは運搬コストのほうが大きくなり、経済的ではありません。また、欠品、不良が生じたらラインに多大な迷惑を及ばします。
作業者は、タクトタイム内に仕事をしなければなりません。しかし、ビスや梱包品の不足等、標準作業に組み込まれていない作業が発生した場合、作業者がいちいち取りに行っていたのでは、タクトタイム内での仕事は困難になります。こんなときは、運搬だけを実施する人を置くほうが効率的です。
作業者が箱に3段詰めされた部品を取るのに、1段目と3段目では、手を移動させる距離も違います。1段目は手を伸ばしたり、体も曲げるため負荷がかかります。
ジャストーインータイ厶を実施するときは、下図のように細かいことも配慮したうえで、職場のしくみを構築する必要があります。
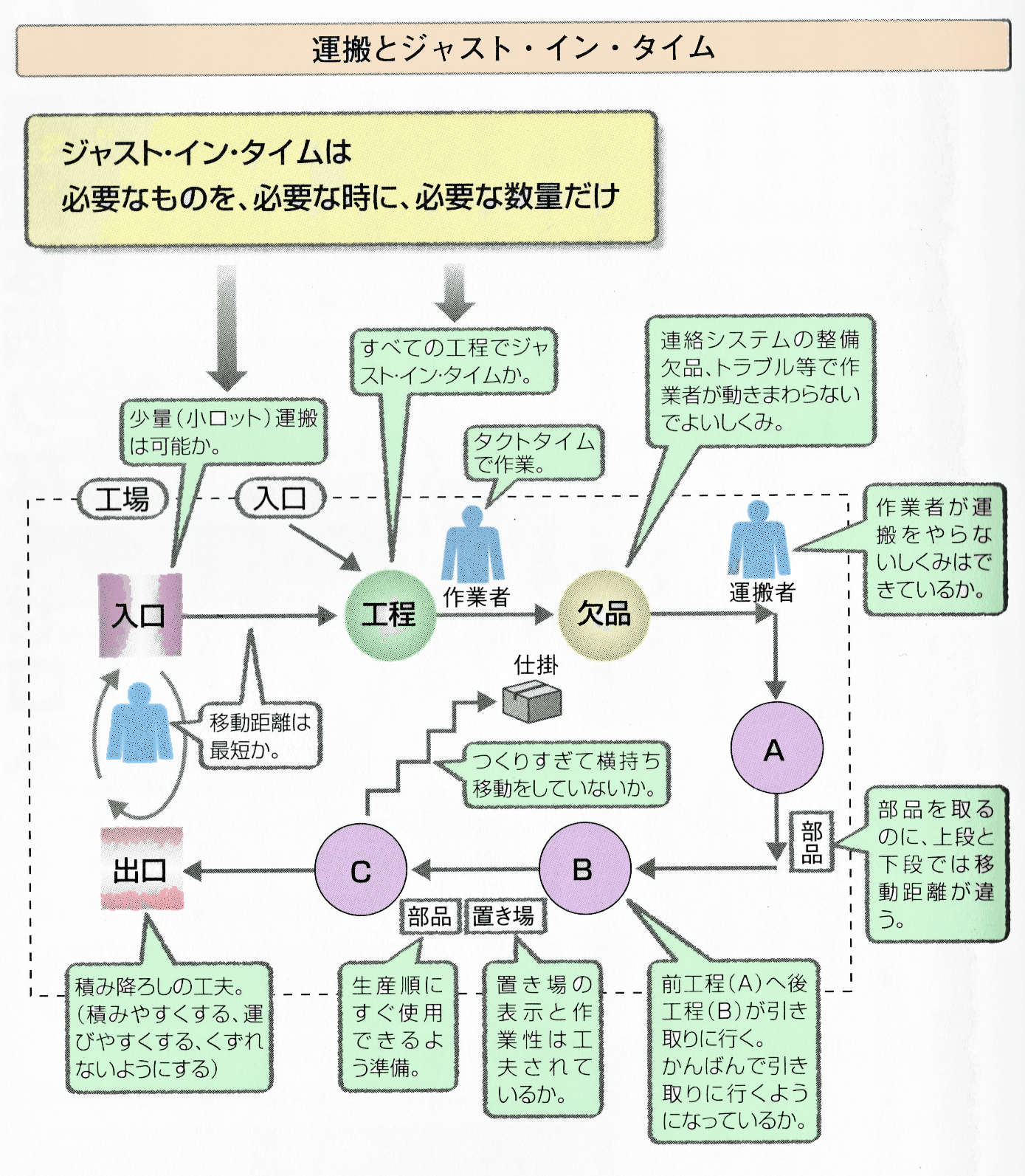
運搬とジャスト・イン・タイム
ポイント
理想は必要数量のそのつど運搬だが、職場の実力、しくみのレベルで、職場に合った運搬方法を使い分けることが重要である。
運搬のムダ排除
トヨタ生産方式は、さまざまなしくみが構築され、繰り返し実施される教育・訓練の中で、それを実施できる人が職場風土として定着してきているのです。
ですから、運搬のムダに対して一度に導入しても、受け入れる職場風土が育っていない企業では、混乱が発生します。まずは、職場内で可能なカイゼンでムダ取りをしていくのかよいでしょう。
運搬は付加価値を生まないと先述しました。付加価値を生家ない工程は、限りなくゼロをめどさないといけません。しかし、運搬に少しでも付加価値を要求するなら、モノと情報を一致させ、多回運搬の流れをよくするなどを考えます。なお、運搬作業者が複数の部品を複数のラインからセットで集荷運搬し、組立てラインに供給するなどの工夫は付加価値をつけた例といえます。

運搬 ムダの着眼点
運搬方式の種類
運搬は原則として「運搬かんばん」で行い、運搬の基本は後引取りでかんばんを使用します。ただ、現実には生産かんばんと運搬かんばんを兼用していることが多いようです。以下に、各種運搬方式を紹介します。
水すまし運搬方式
複数の前工程を決められたとおりに巡回し、必要な種類の部品を集めて運搬する方法です。運搬方法が「水すまし」の動きのように見えたことからこのように名づけられました。
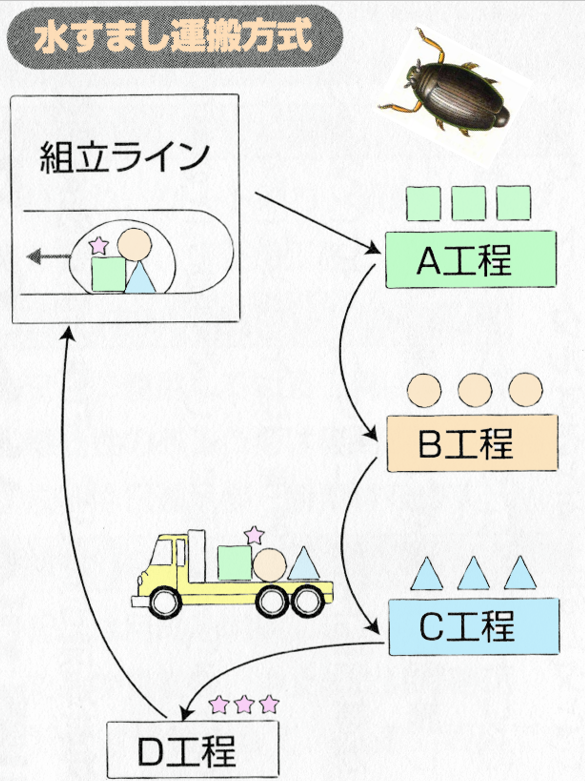
水すまし運搬方式
ハイヤー方式
部品の必要性が発生した場合、必要工程は呼び出し信号を出し、専任の運搬者に知らせます。部品の運搬情報は一箇所の集中管理板に表示され、その指示にしたがって運搬します。顧客の要求で迎えに行くハイヤーに似ているため、ハイヤー方式とも言われています。
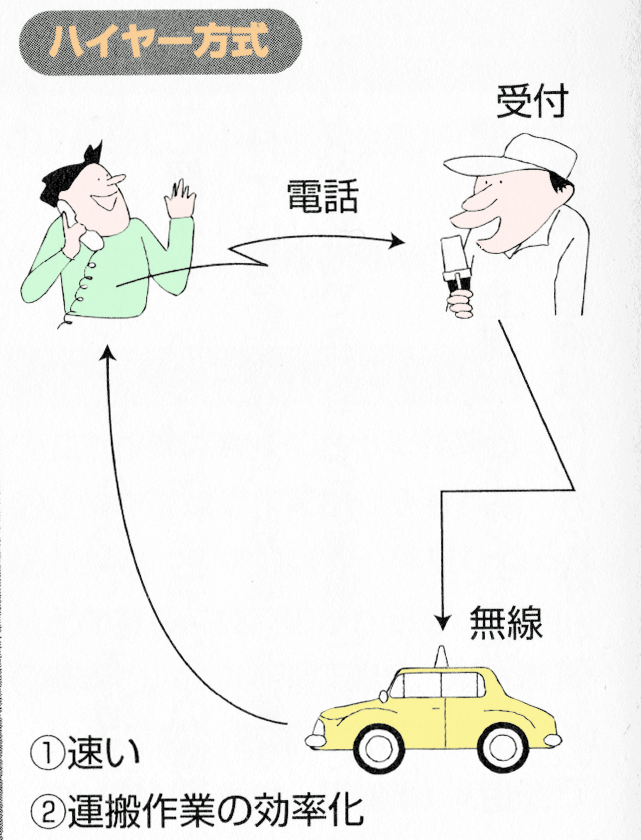
ハイヤー方式
タクシー方式
運搬者が担当区域を巡回し、部品のなくなりそうな工程を見つけ補充していくやり方です。区域を巡回しているタクシーに似ているため、タクシー方式とも言われています。
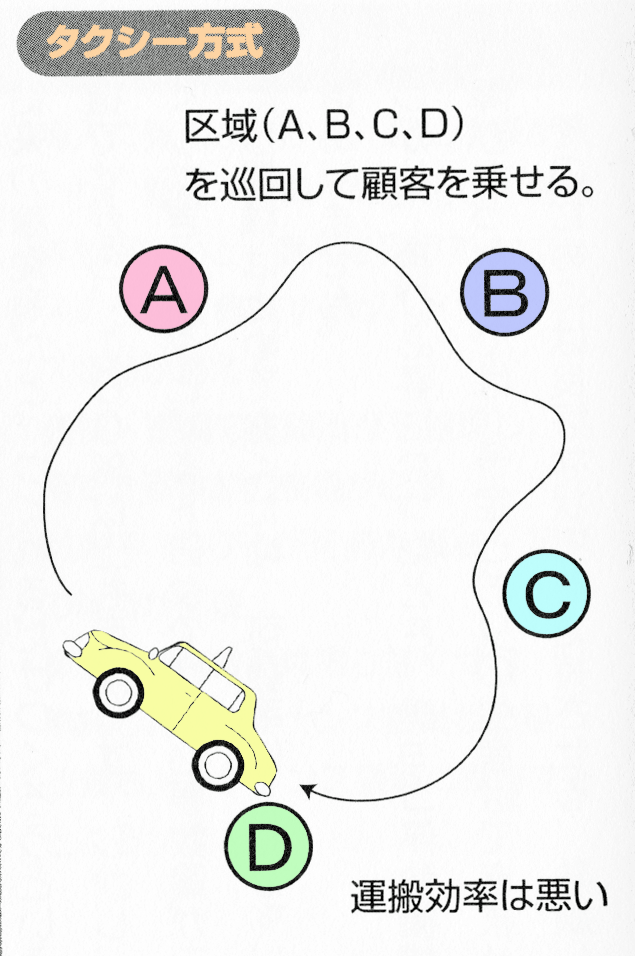
タクシー方式
乗り継ぎ運搬方式
トラックの荷物の運搬を運転手が行う場合、荷の積み降ろし中、トラックは非稼働状態になります。
乗り継ぎ運搬方式とは、運搬と積み降ろし荷の作業を切り離し、トラックが目的地へ着いたら、運転手はすでに積み降ろしを終了しているトラックに乗り換え、次の運搬を行うことです。運転技術を最大に活かす方法で、トラックの有効活用につながります。
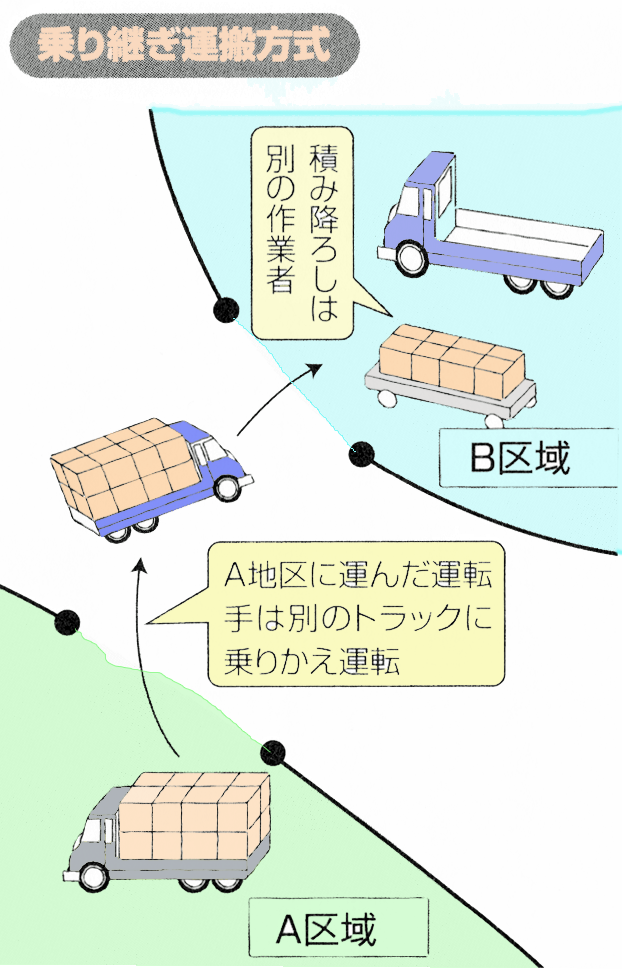
乗り継ぎ運搬方式
加工のムダと稼働率
ムダは極言すると、良品をつくリ出しているとき以外はすべてムダということができます。
加工作業のムダとして、バリ取り、修正加工等かおりますが、これを何の疑問も持たず漫然と実施している状況に遭遇します。バリ取りは1回当たりの時間は少なくても、トータルすると多大なムダとして累積します。
これ以外にも、工夫しないで使っている治工具類、問題は既に解決しているのに、従来からの慣習として取り続けている記録など、見直し改善すれば、多くのムダが低減できることが現場には多くあります。
ところで、機械化、自動化をやみくもに進める企業があります。機械・設備けだしかに便利なものですが、作用がかかり、十分使いこなさないと、かえって費用高になります。そうならないために、トヨタは機械と人との仕事の役割を、よく研究しています。機械・設備を必要なときに、いつでも良好な状態で動かせるように、「可動率」という言葉を使い、能力を100%出させるための体制をつくリ上げています。
従来の稼働率だと、つくれるだけつくろうという指標ですから、100%以上も可能です。しかし、つくりすぎをムダとするトヨタでは、必要数量ができたら機械は止めておくため、可動率に100%以上はありません。
しかし、再び必要になったとき、チョコ停や機械故障があっだのでは、予定どおりの生産はできません。そのためには良好な状態を維持させる、熟練しかメンテナンス要員が必要となってきます。
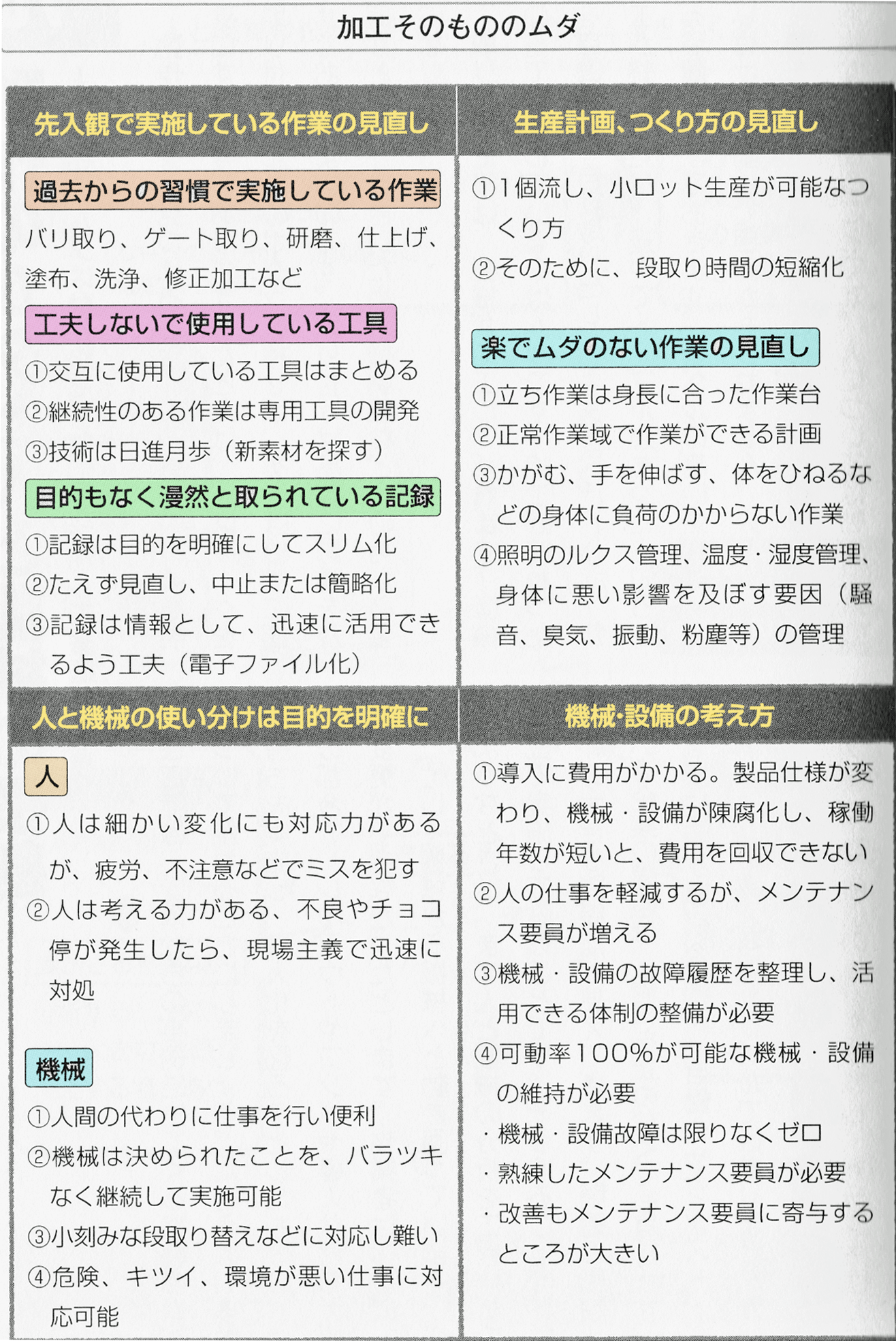
加工ムダの排除
動作のムダを見つけるとき、人と機械の役割を明確にする必要があります。たとえば、人はワークを取り付け、起動のボタンを押せば、あとは機械に任せておけばよいのです。取り付けは品質に影響を及ばすところが大きいため、微調整など人の力が必要になります。
取り付けた後は、機械が加工してくれます。機械の前で監視しているのはムダです。加工が終わったら自働停止、自動取り出しができるようにします。加工が終了したり、途中でトラブルがあったら知らせる装置を付けておきます。レベルの高い企業は、取り付けも自動化できるかもしれません。人と機械の役割を明確にするということは、人と機械を有効に活用するということです。人については動作経済の、徹底して動作のムダを省きます。
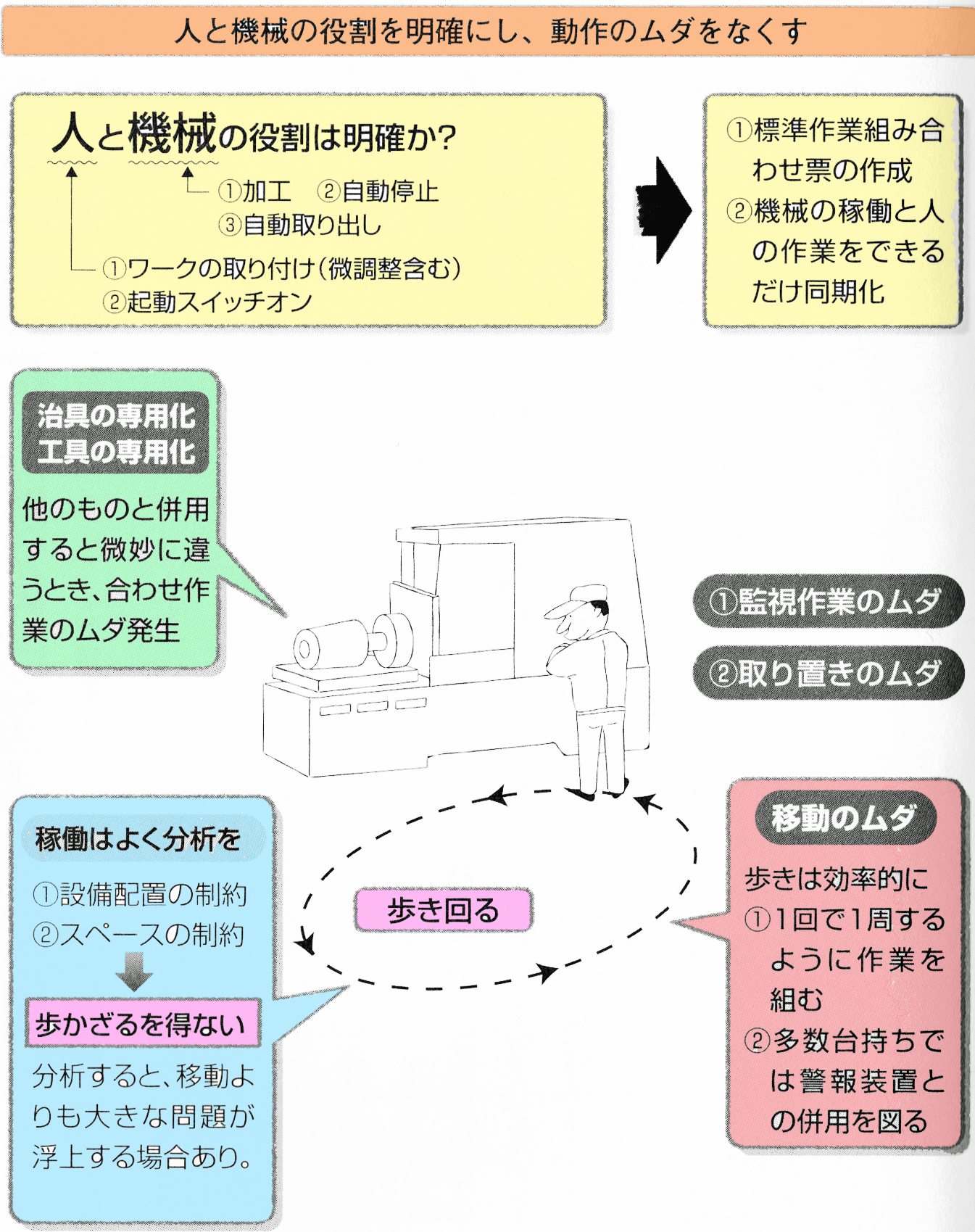
動作のムダをなくす
手待ちのムダの排除
1個30秒でできる、5人からなるラインの組立作業があったとしましょう。作業者は忙しく手を動かしており、1秒でも大切にする改善の強い意欲がないと、どこにムダがあるかを発見することはできません。
繰り返し作業ですから、仮に2秒改善できれば、下図のように、年間では1人当たり、18.6日多くの仕事が可能になります。このように、改善では秒単位の細かいモノの見方が必要になってきます。
人が機械を使って作業しているとき、モノは機械の中で加工されているのに、その前でじっと待っている作業者がいます。作業者が見ていなくても、機械は動いているわけですから、監視作業は手待ちのムダになるのです。
この場合、異常事態が発生したとき、初めて作業者が必要になるわけですから、センサー等で異常を知らせるしくみをつくれば、作業者は不要となります。
一方、チョコ停や資材の欠品が生じた場合、ラインストップとなります。作業者は手待ちとなり、じっとしていることができなくなり、余分な作業をすることになります。トヨタ生産方式でつくりすぎのムダなどにつながり、よくないとしています。
とくに、手待ちは他の作業や見かけの作業をすることで、顕在化した問題が見えなくなり、改善を遅らせてしまいます。「すべての道はローマに通ず」という言葉があるように、「すべてのムダは手待ちのムダに通ず」と言えるでしょう。ムダが見えないときは、手待ちのムダに置き換えてみるのもよいでしょう。
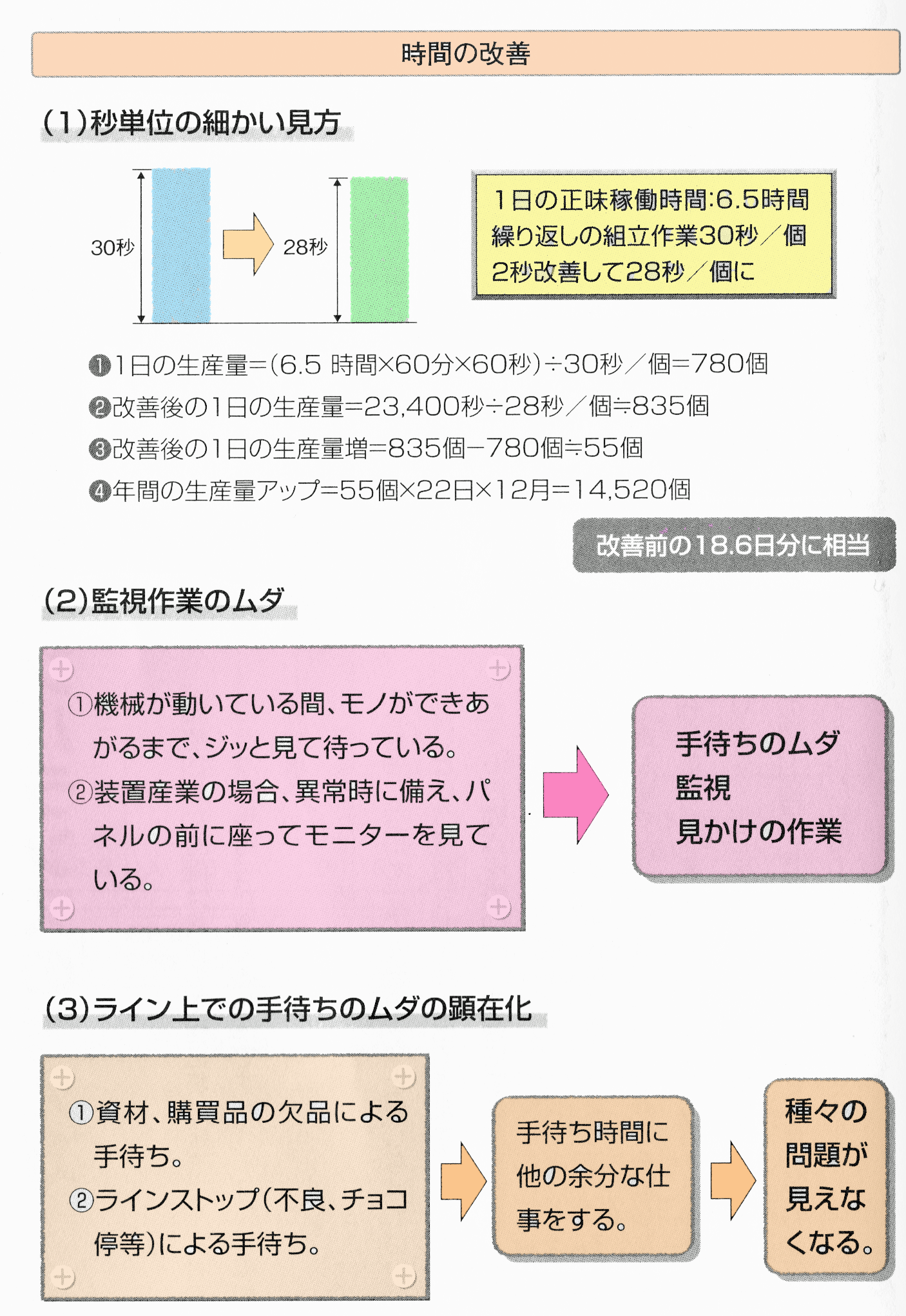
時間の改善
動画 5Sと3ム(ムリ・ムダ・ムラ)
*工場のムダの排除については下記の文献に色々な活動事例等が更に詳細に記載されています。
参考文献:
・日本のモノづくり トヨタ生産方式の基本としくみ 佃 律志 (著)
・すぐに使えるトヨタ生産方式 導入・実践ノウハウ集 (工場改善シリーズ) 竹内 鉦造 (著)
・すぐに使える現場改善 実践手法&フォーマット集 杉浦 正邦 (著)