見える化とは?
「以下のコンテンツについては、『すぐに使えるトヨタ生産方式 導入・実践ノウハウ集』(著者:竹内鉦造)から抜粋したものであります」
見える化
現場で目にした状態が正しいのか、正しくないのか、説明を聞かなくても見た目でわかるようにすることである。
このままの状態で放置しておいてもよいのか?
何か問題はないのか? がわからず、現場が管理されてない状態では困るのである。
そのために、基準や標準をつくり、それを現場に表示して、基準や標準に従っているかそうでないか、わかるようにする。
たとえば、部品がシユーター上に置いてある。何の表示もされていなければ、その量で良いのか悪いのかが判断出来ない。そこで、シユーター上に部品の最小と最大を表示すれば、誰の目にも正常か異常かがわかる。
物を置く場所についてもこのことが言える。 5S活動で、物の置く場所を決め、区画をしておくと、その区問線の外やまったく異なる所に物が置いてある時に、それは異常だと、誰もが判断できるのである。
現場全体をこのように“見える化”すれば、誰でも正しいか正しくないかが判断でき、全員が正しい方法に持っていこうと努力する。
英語および中国語で見える化は
英語(English):Visual management
中国語(简体中文):目视管理(mù shì guǎn lǐ)
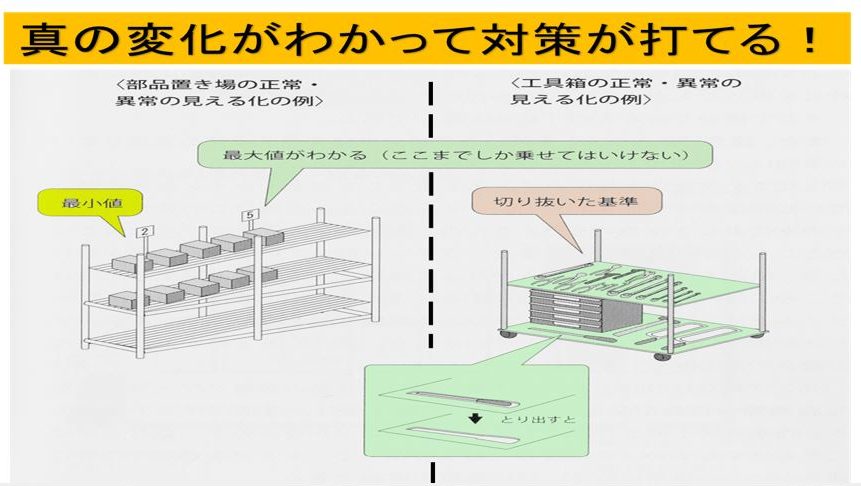
画像出典先:『すぐに使えるトヨタ生産方式 導入・実践ノウハウ集』(著者:竹内鉦造)
トヨタはさまざまな作業において、「目で見る管理」が工夫されています。目で見れば誰もが容易に状況が分かり、共通の認識ができるため、作業にムダやミスがなくなります。
ところで、トヨタでは問題が発生したら現地へ行き、問題の生じたモノを見て、問題発生状況をよく観察しなさいという思想、すなわち、三現主義が根づいています。
このことは、古くから言い伝えられている「百聞は一見にしかず」を実践のなかで企業体質として、つくりあげてきたものです。
しかし、三現主義が重要だと頭の中で分かっていても、体にしみこませるのは容易なことではあリません。現場で観察するには、現場でのモノの見方、考え方、体力、気力が必要になってきます。
実際に企業で問題が生じたとき、現場に出向き、問題発生状況を観察してもらうようなとき、問題解決の方向が見えない人は多いものです。現場でのモノの見方、考え方を話し、再度、現場観察に行つてもらおうとすると、デスクワークに逃げてしまう人も出てきます。
トヨタ生産方式の代名詞のように言われている「かんばん」も、簡単に運用できるものではあリません。
たとえば、特急品や割込み品があった場合、現在生産中のものとの関係はどうなるのか、きめの細かい対応が必要になってきます。ラインストップも問題を発見しやすくした例といえます。
下の表は、トヨタにおける目で見る管理の一例です。いずれの場合も、目的を明確にして企業体質に合つたものを導人していかないとかえって混乱を生じるので注意が必要です。
No | 項目 | 具体例と説明 |
1 | 現場主義(三現主義) | 現地、現物、現実 |
2 | かんばんのバラツキ | 進捗状況の管理、適切なかんばんの活用 |
3 | 異常警報装置 | アンドン、ブザー、呼び出し灯 |
4 | 5S | 所番地管理、通路の区画線、危険マーク、治工具形合わせ板、目に訴えるための意識づけに有効 |
5 | 進捗状況 | 現場の何を見ると進捗状況が分かるのかを認識、各工程のかんばんと現物量、手持ちの状況、生産管理板、ガントチャート(日程計画表) |
6 | 生産管理板 | 進捗状況、生産計画と実績とその差異、品種、 特急品、割り込み品への対応状況、機械設備 の稼働状況 |
7 | 生産指標 | 生産高、歩留り、生産性、稼働率、可動率、段取 り替え時間、不良率、良品率、不良件数、手直し 不良率、チョコ停 |
8 | 問題点とその対策 | カイゼン提案報告書(問題点、現状分析、原因の状況究明、カイゼン案)、現場の人たちの関心を高める、参加意識の向上に有効 |
9 | 標準作業の遅れ | 標準作業どおりに作業を進められなくなったと き、ベルトコンベヤ上に引いた線の間隔てモノ が来ないとき |
異常発生時の設備・ライン の自動停止 | ポカヨヶ、検知器、タクトタィムオーバー時の ラィン自動停止、定位置停止 | |
製品の識別 | 検査前、検査中、良品、不適合品(赤箱) | |
バラツキの吸収 | バラツキの吸収 | |
目で見る管理の代表例
「目で見る管理」とは、工程で発生した問題(異常と正常の差)を迅速に把握し、だれもが容易にカイゼンし、管理することです。主な方法を以下に説明します。
生産管理板
生産の状況が計画に対して進んでいるのか遅れているのか、目で見て分かるようにすることです。生産計画数量(生産時間帯の時間をタクトタイムで割ったもの)、生産実績との差異などで表示します。
アンドン
エ程でどのような異常が起きているかを管理・監督者に分かるよう知らせるものです。呼び出しアンドン、異常アンドン、稼動アンドン等があリます。
(下図参照)
定位置停止方式と即時停止方式
定位置停止方式とは、作業者が異常を感じたときに連絡し、ラインがいつも同じ位置で停止するようにしたものです。停止するまで時間があり、監督者の援助などで、ラインを止めなくてよい場合もあります。
即時停止方式とは、原則はできるだけ止めないようにするが、問題が発生したらすぐラインが止まるようにしたものです。
指定席と自由席
指定席とは、塗装工程などでハンガーなどに目印をつけ、ハンガーの指定箇所に製品をかけていく方法のことです。
自由席とは、生産にバラツキが発生し、バラツキを吸収するため、なにをかけてもよいようにしたものです。
現場での見える化
多くの企業で、帽子や腕章などの色で作業者を区分してわかるようにしている。管理の進んだ所は、工程毎に個人の訓練を行い、その工程の作業をして良いか否かの認定をし、実際にその工程に働く許可を取った人が入っているか否かを見える化している。
そこで働いている人の「見える化」である。
また、総合“あんどん”を使つたライン全体の見える化も見逃せない。
事例は、機械加エラインの稼働状況を示すものである。
上にライン全体を表すライン名を表示しておき、ライン全体が動いている時は青いランプが点く。ラインが止まった時はこの青が消え、その下に表示されているたくさんの工程名の中の、トラブルの起こったところが赤く点灯する。
また、ラインは動いているが、材料が切れた等、故障ではなくそこに人が行って処理をする必要が発生した時は、そこの工程の赤色ランプが点滅する。よく市販品で売っているタワーライトをマシン毎に付けて、マシンの稼働状況を表示しているが、マシンが少ない時はそのタワーでわかるが、多くなるとわかりにくいので総合“あんどん”を付ける。
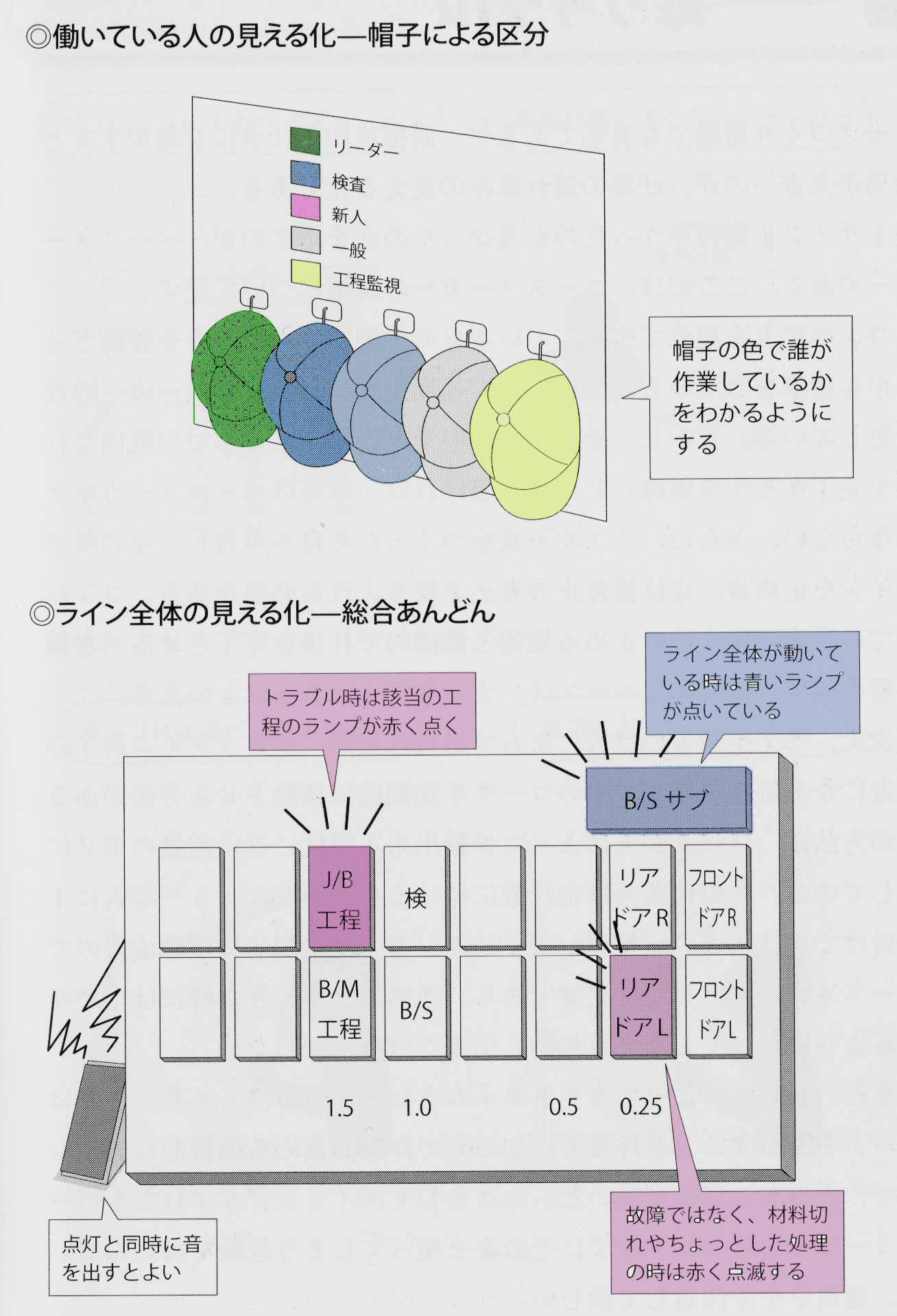
画像出典先:『すぐに使えるトヨタ生産方式 導入・実践ノウハウ集』(著者:竹内鉦造)
遅れ進みの見える化
モノづくり現場でも有効であるが、間接部門の仕事にも適用すると効果が大きいのが、仕事の遅れ進みの見える化である。
1サイクル毎に早かったのか遅かったのかを示すのが、ペースメーカーである。ここでは、ペースメーカーの詳細について記す。
コンベア上を流れて生産しているものや加工物そのものを移動させながら仕事をしている方法は、動く速度がすでにペースメーカーの役目をしている。しかし、その流れの中でどこからどこまでの範囲で仕事を完了するかを明確にしておかなければ、本来はペースメーカーとはならない。
さらに、ミスや不良をつくったら自ら申告し一定の所でラインを止める、定位置停止の考えを取り入れる必要がある。コンベアでの生産には、この止める機能と範囲内で仕事を完了させるべき線が書かれて、はじめてペースメーカーを持ったラインといえる。
次に、モノを送るのは人によって送られるが、タクトタイム終了間近になる毎に組み立て中のワークを強制的に移動させる方法がある。
この方法は、ワークが人によって移動出来る限度に近い重量のモノに適している。この仕組みは全行程に付ける必要がなく、5~6人に1つ付けておけばよい。投資が安く済み、モノを強制的に移動するのでペースメーカーとしては完璧である。当然異常が起きた時には止められるようになっており、再起動も出来なければならない。
また、光や音によってタクトタイムを知らせる方法もある。これは、ワークを動かすことを作業者に知らせて作業を進める間接的な方法なので、作業者の意識が低いと、ミスをしてタイミングがずれてもペースメーカーをリセットせずにそのまま使ってしまう危険をはらんでい
る。運用を十分注意して欲しい。
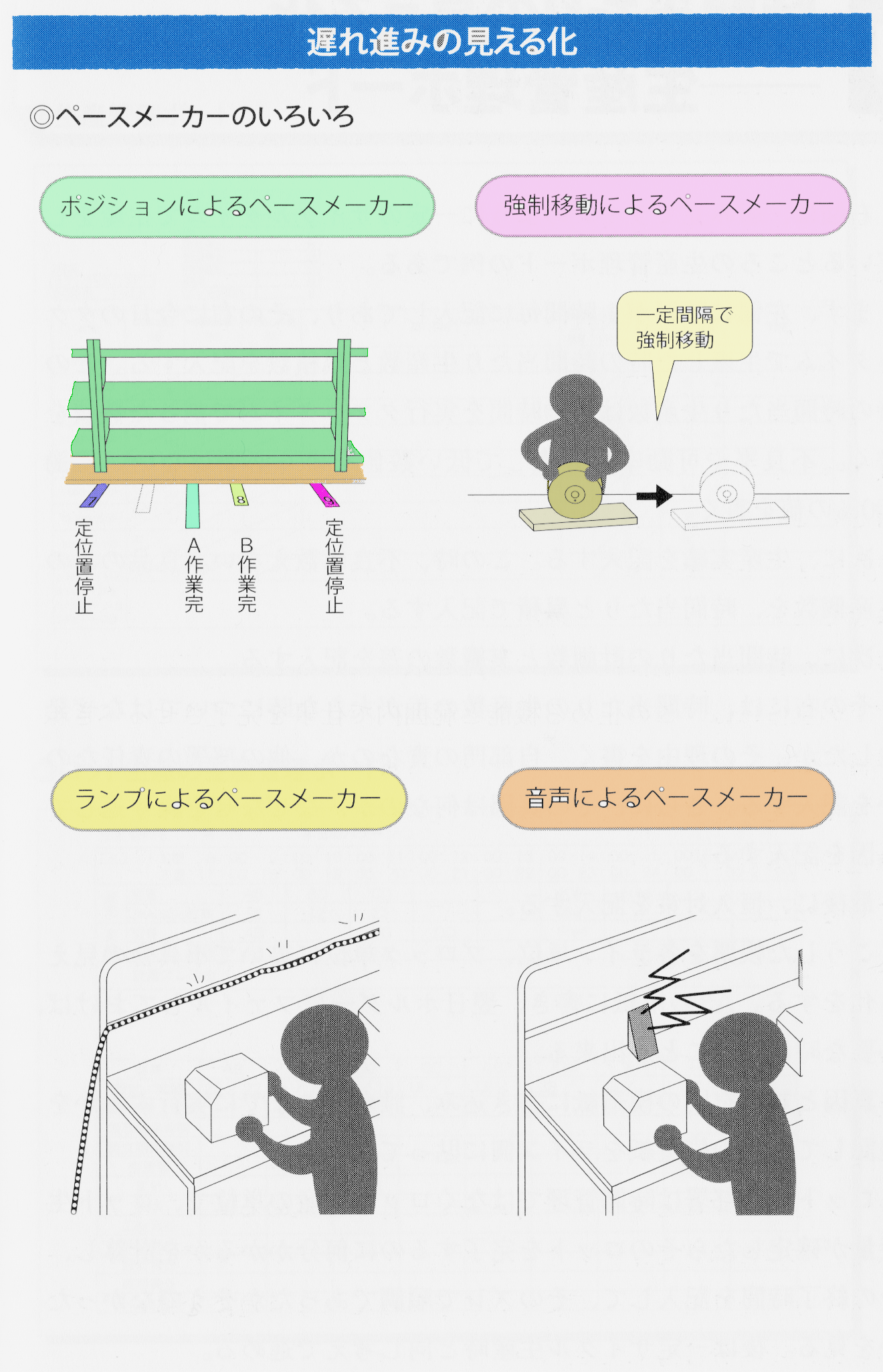
画像出典先:『すぐに使えるトヨタ生産方式 導入・実践ノウハウ集』(著者:竹内鉦造)
生産管理ボード|時間当たりの見える化
下図は、組み立てラインのように一定のサイクルタイムで生産をしているところの生産管理ボードの例である。
まず、左側に時間が1時間毎に記入してあり、その右に今日のタクトタイムで生産した時の時間当たり生産数と累積数を記人する。この時の時間当たり生産数は稼働時間を実行タクトタイムで割った数値を書く。不良率や可動率を考慮して低い数値を書く必要はない。稼働100%の値を書く。
次に、生産実績を記入する。この時、不良は数えない。良品のみの生産個数を、時間当たりと累積で記入する。
次に、時間当たりの計画数と実績数の差を記入する。
その右には、時間当たりの生産数の差が大きな時についてはなぜ発生したか、その理由を書く。自部門の責任なのか、他の部署の責任なのかを記入する。さらに、その真因は何なのか、なぜなぜを繰り返して真因を記入する。
最後に、恒久対策を記入する。
こうした帳票を各ライン単位、ブロック単位に書いて不具合の見える化をする。 A3の用紙に書き、翌日ホルダーにファイルしておけば、必要な時に見ることが出来る。
真因と対策を別の模造紙に書き込み、誰がいつまでに実行するかを追記して、その模造紙をライン側に貼っておく。
ロット生産部署は時間管理ではなくロット生産の単位で、ロット生産量が確定したらそのロットを完了するのに何分かかるかを計算し、その終了時間を記人して、そのズレで順調であったかそうでなかったかを見る。後は一定サイクル生産時と同じ考えで進める。
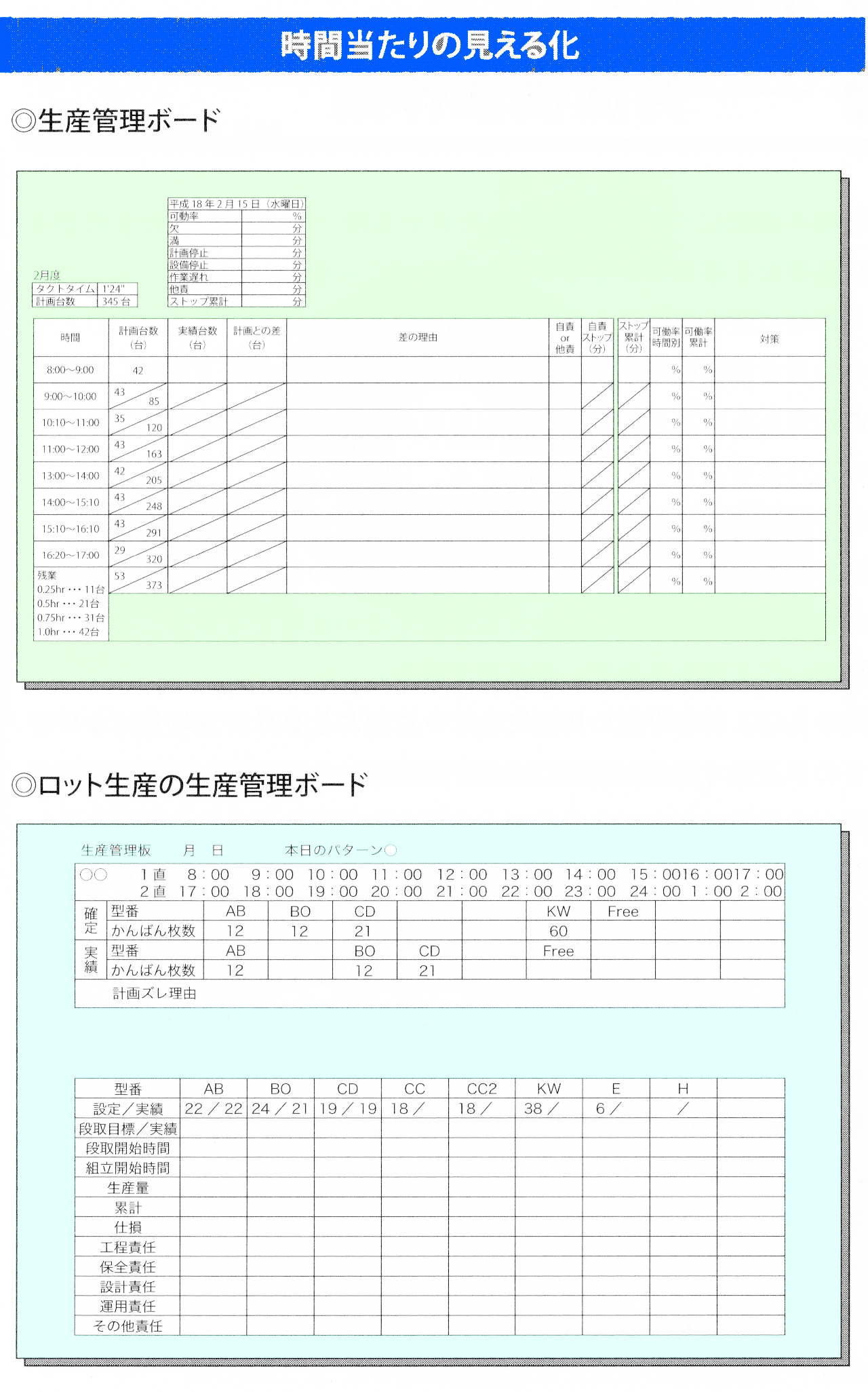
画像出典先:『すぐに使えるトヨタ生産方式 導入・実践ノウハウ集』(著者:竹内鉦造)
ムダの見える化一付加価値作業
仕事の細部についてIE的な分析をする時、その作業そのものが本当に必要な仕事なのかを分析しなくてはならない。
その時に役に立つ考えが、付加価値作業の分析である。つまり、一連の作業を要素作業単位に分解する時、その作業がモノに対して何らかの変化をもたらしているか否かを見ることにより、付加価値を与えている作業であるか否かを判断する。
こうして付加価値作業がわかれば、ムダな作業がより鮮明になり、その作業をなくすことが出来る。ただ、会社の規則やモノづくり全体での効率化を考えた時、この付加価値のない仕事でも実施しなければならないことがあるので、要注意である。
たとえば、材料を短い間隔でラインに運ぶ仕事は付加価値はないがこまめに運搬することによりライン側がすっきりすると共に作業者がラインの仕事に集中できるので、効率が上がるなどメリットがある。
ムダの見える化の次の手段は、一連の動作を繰り返し動作にすることである。繰り返し動作をしている現場と繰り返し動作をしていない現場では、ムダの発見比率は大きく違う。作業を標準化して繰り返し作業に変更することが、ムダな動作を見える化する第一歩である。
ビデオによる動作分析を実施する前に、現場に立って対象の作業が繰り返し同じ動作で作業をしているか否かを観察し、出来ていなければ、まずその原因を見つけ、改善をすることである。
そして、繰り返し作業になったら、ビデオを撮り、動作分析をして動作のムダを見つける。複雑な動きをしている時は多くのムダがあるので、注意をして見るとよい。
スムーズな動きにはムダは比較的少ない。
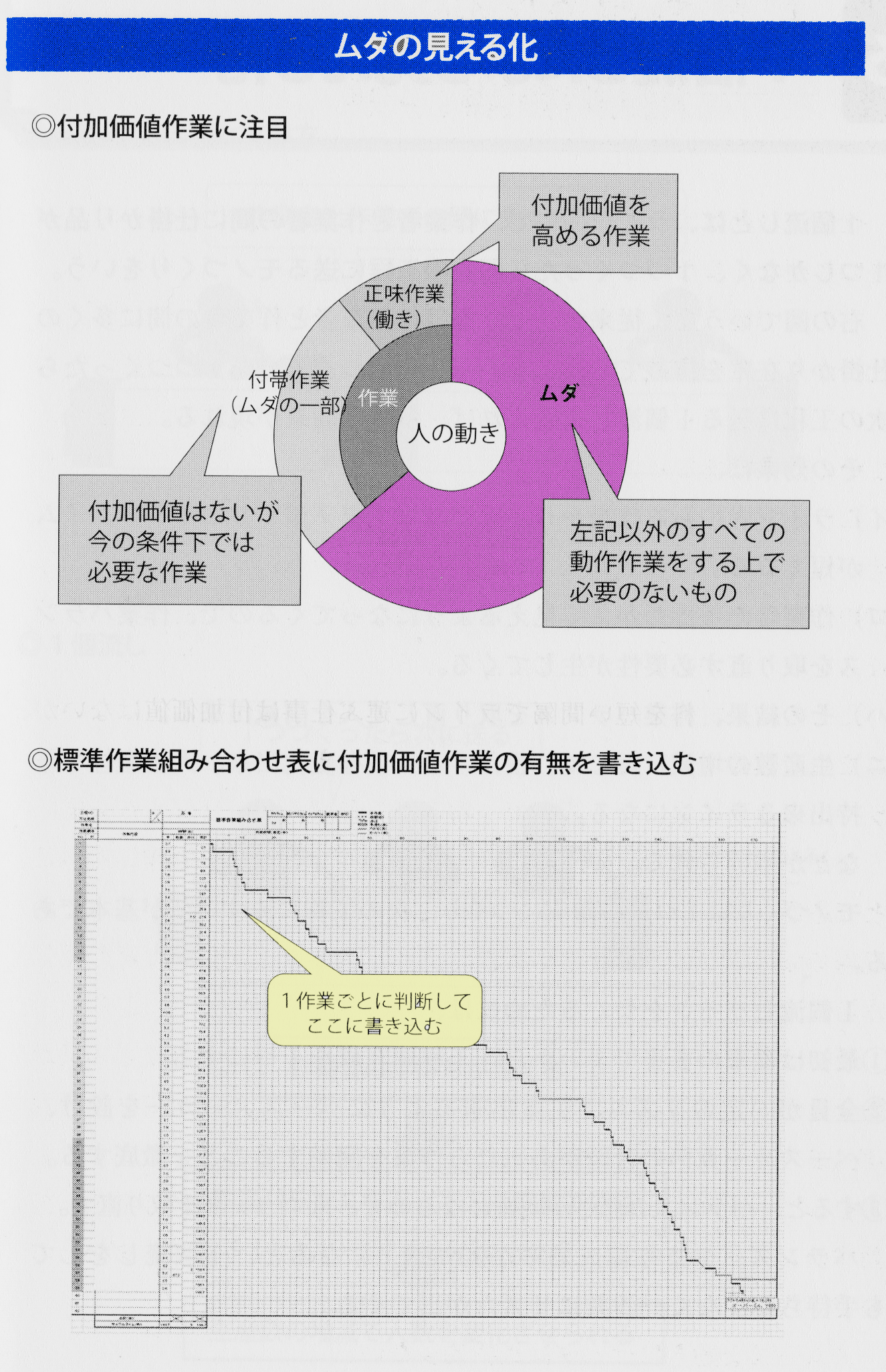
画像出典先:『すぐに使えるトヨタ生産方式 導入・実践ノウハウ集』(著者:竹内鉦造)
1個流しによる見える化
1個流しとは、ラインの中で、作業者と作業者の間に仕掛かり品が1つしかなく、1つつくったら即次の工程に送るモノづくりをいう。
下の図でいうと、従来のつくり方は、作業者と作業者の間に多くの仕掛かり在庫を持って生産していた。そのつくり方を1つつくったら次の工程に送る1個流しに変えれば、多くの効果が現れる。
その効果は、
イ)ライン内にある仕掛かり在庫が減ってモノづくりのリードタイムが短くなる。
口)作業者の手待ちがよく見えるようになってくるので、作業バランスを取り直す必要性が生じてくる。
ハ)その結果、作業バランスを取り直して人を削減出来る。
二)生産数の増減に対して、投人する人数を変化出来、生産性を維持出来るラインになる。
などが挙げられる。
モノづくりは1つずつ確実につくり、次の工程に流すことが基本である。
1個流しラインをつくるためには、
①最初は従来のままでよいから、工程間在庫を1つにする。
②全員が一定のリズムで生産出来るようにペースメーカーを設け、 ペースメーカーの合図があったら作業を開始することを徹底する。
③すると、バランスの悪さが明確になるので、即バランスを取り直す。
バランス、つまり編成効率が90%以上になると、1個流しをしても手待ちが少なく、作業にリズムが出てくる。

画像出典先:『すぐに使えるトヨタ生産方式 導入・実践ノウハウ集』(著者:竹内鉦造)
ライン在庫の見える化
組み立てラインや加エラインの中にどれだけの在庫があるかをわかりやすく表現するのに「ライン手持ち率」を用いる。
昼休み前や終了時間前の、ある時のラインの中にある在庫量を調査する。その量をX個とする。そして、ラインの中で付加価値を付けている工程数を数える。たとえばすべて人による作業であれば作業者の数になる。この値をZとする。
ライン手持ち率はY=X÷Zの式で計算される。手待ちによる工程がない限り、最小の値は1である。
無駄なく全体がリズム感を持って作業出来る範囲は、ライン手持ち率が1.3~1.5くらいの値である。
このライン手持ち率の考えは、人が主体の組み立て工程を想定して活用してきたが、マシンが主体のラインでもこの考えは適用できる。
このライン手持ち率の考えを機械加エラインや機械組み立てラインに適用すると、搬送をさせるためや向きを変更するために多くの在庫を持っていることや、チョコ停止があっても、それに影響されずにラインが動く設計をしているために工程間に多くの在庫を持っていることがわかってくる。
ライン手持ち率を少なくしてムダのないモノづくりをするためには、各マシンの信頼性を上げ、止まらないようにしなければならない。
工程間に在庫を持って止まることを前提にしたラインでは、モノづくり力は強く育っていかない。
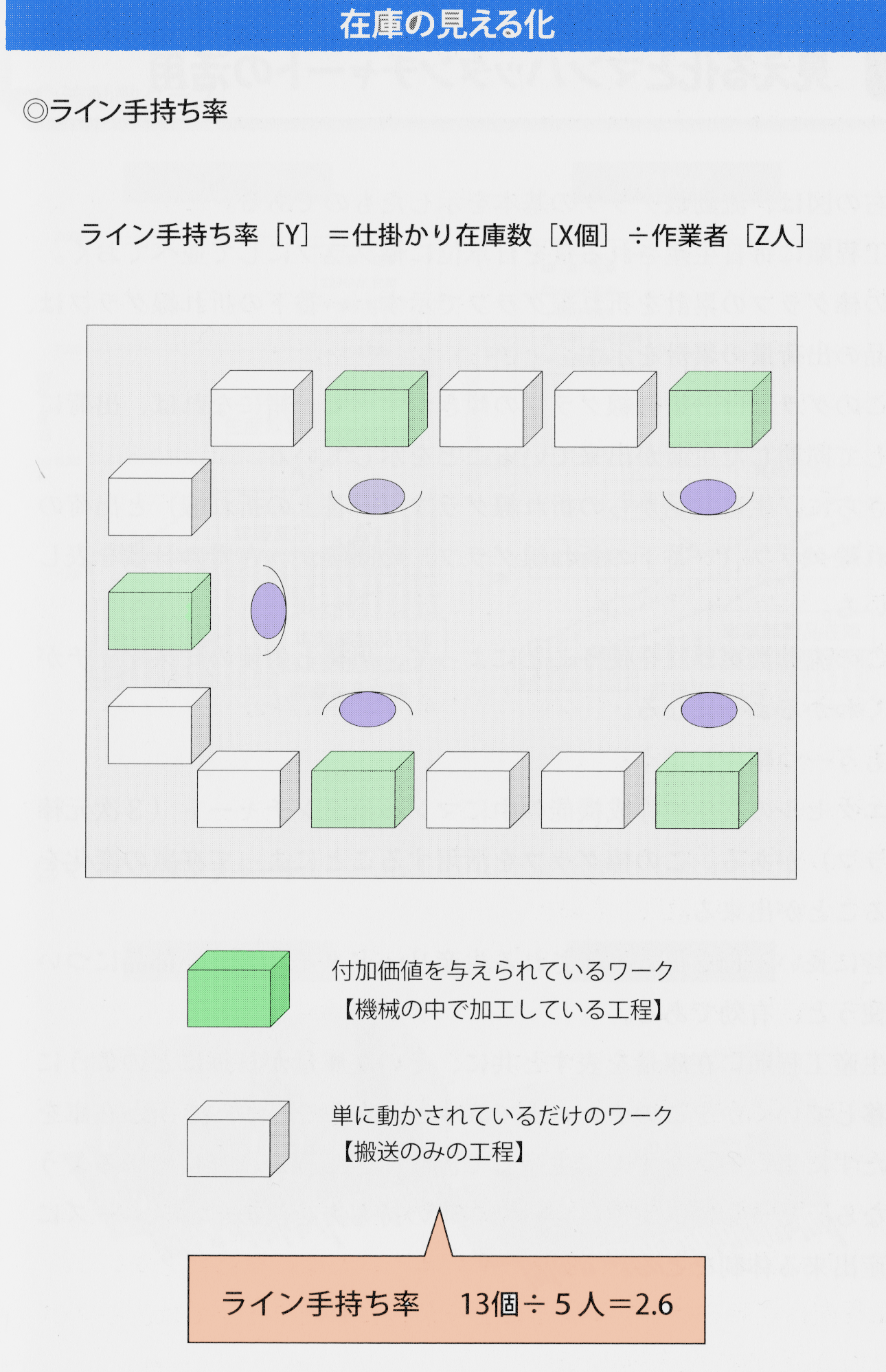
画像出典先:『すぐに使えるトヨタ生産方式 導入・実践ノウハウ集』(著者:竹内鉦造)
ミスマッチの見える化とマンハッタンチャートの活用
下の図は、流動数グラフの基本を示したものである。
工程順に毎日生産される量を日単位に棒グラフにして並べておく。
その棒グラフの累計を折れ線グラフで示す。一番下の折れ線グラフは、製品の出荷量の累計を示す。
このグラフは、折れ線グラフの傾きがすべて一緒になれば、出荷に対して同期した生産が出来ていることを示している。
さらに、生産開始からの折れ線グラフ(一番上の折れ線)と出荷の折れ線グラフ(一番下の折れ線グラフ)の間隔が、在庫の日数を表している。
この流動数グラフを使うことによって、出荷と生産のミスマッチがよくわかるようになる。
エクセルのグラフ作成機能の中にマンハッタンチャート(3次元棒グラフ)がある。この棒グラフを活用することによって在庫の変化を見ることが出来る。
特に長い工程を得て生産される生産リードタイムの長い部品について使うと、有効である。
生産工程順に在庫量を表すと共に、その在庫量が日毎にどのように推移していくかをこのチャートで表すと、在庫を持つべき所と在庫を持たずに来たモノをすぐに生産して流すべき工程が、推察出来るようになる。そうして、実態に合った在庫の持ち方を決めて、スムーズに生産出来る体制をとる。
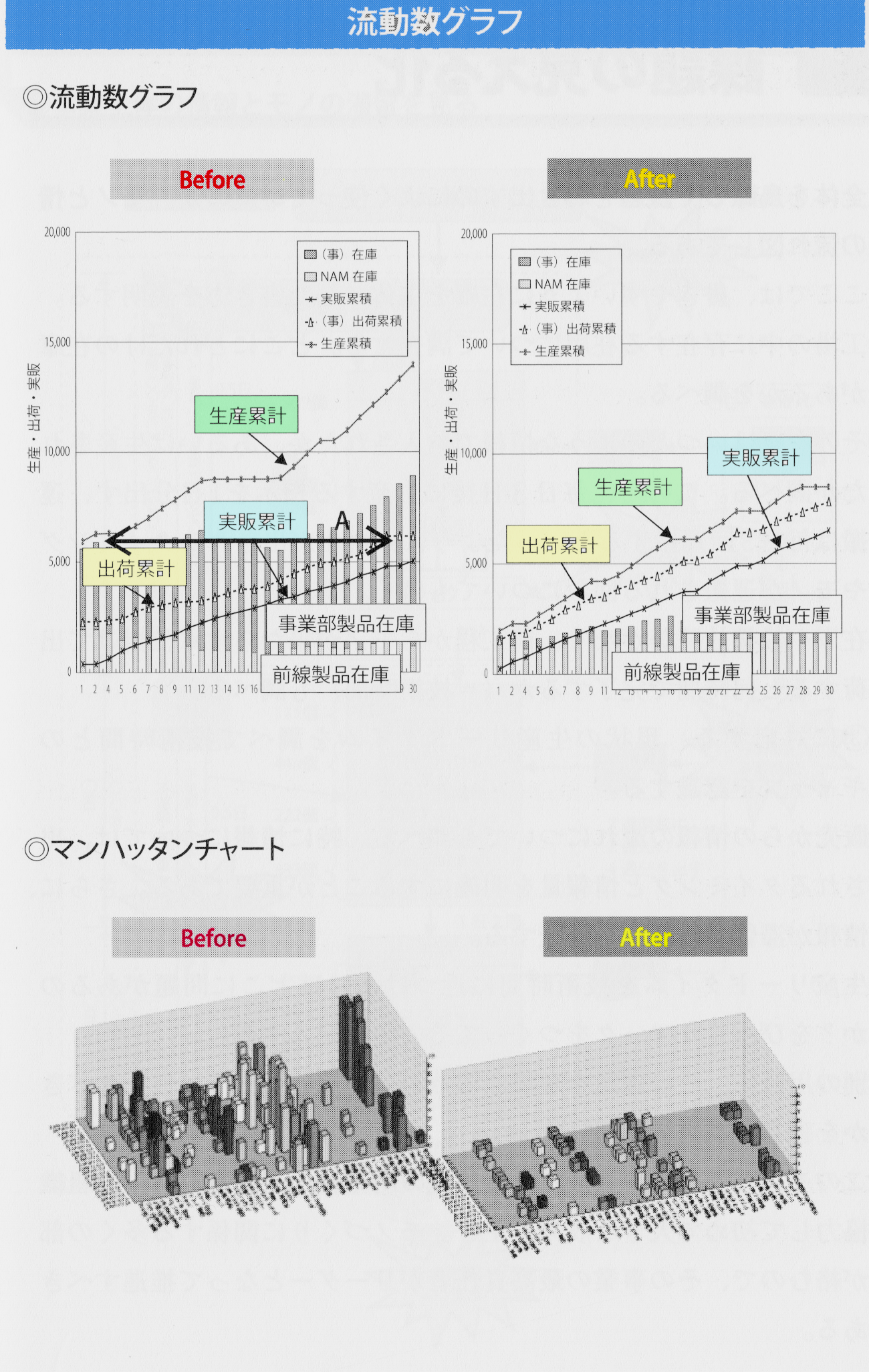
画像出典先:『すぐに使えるトヨタ生産方式 導入・実践ノウハウ集』(著者:竹内鉦造)
モノと情報の流れ図による課題の見える化
全体を鳥瞰して課題を導き出すのによく使つているのが「モノと情報の流れ図」である。
ここでは、書きやすいように在庫を主体にした書き方を説明する。
①工場の中に存在する在庫について調査する。どこにどれだけの在庫 があるかを調べる。
②その在庫はいつどのような情報で納入されたか、あるいは生産されたか調べる。この時、毎日3日後に生産する指示を1日分出す、運搬は毎日3回運搬するといったように、情報が出されるタイミング やモノが運搬される回数についても書く。
③在庫や設備故障等がなく、前工程からモノが来たらすぐ仕掛けて出荷すると何時間で完了するか(=技術時間)も調べる。
④③に対応する、現状の生産リードタイムを調べて技術時間とのギャップを認識する。
⑤販売からの情報の流れについても調べる。特に情報については、出されるタイミングと情報量を明確にすることが重要である。さらに、情報が滞留する理由も調査する。
⑥生産リードタイムを技術時間に近づけるにはどこに問題があるのか?をびっくりマークをつくってその中に記人する。
⑦別の用紙に、その課題を解決するために誰がいつまでに何をすべきかを書き、推進する。
このモノと情報の流れ図による課題の明確化と課題解決は、各組織が協力して初めて大きな成果を生む。モノづくりに関係する多くの部署が絡むので、その事業の最高責任者がリーダーとなって推進すべきである。
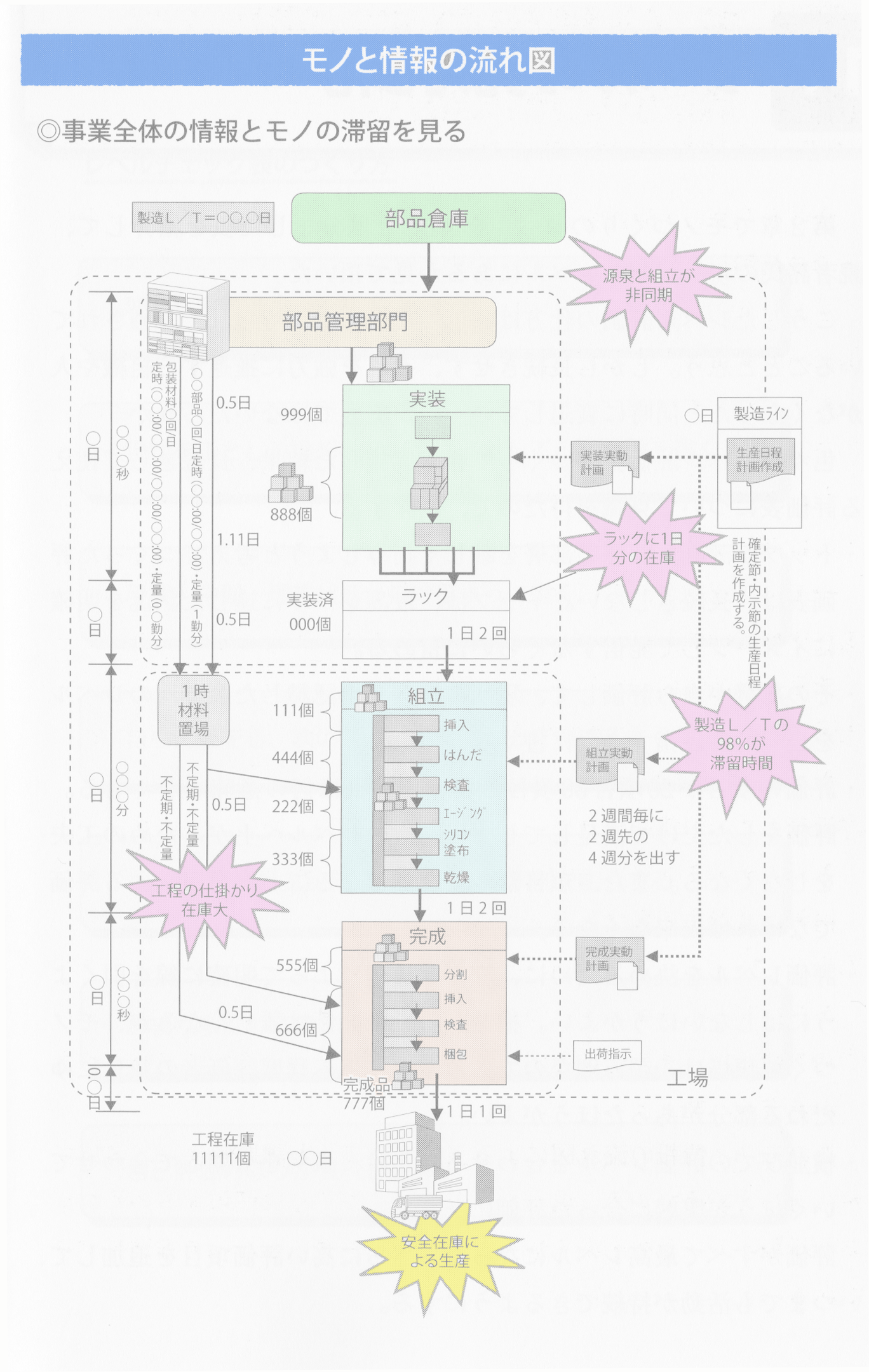
画像出典先:『すぐに使えるトヨタ生産方式 導入・実践ノウハウ集』(著者:竹内鉦造)
レベルの見える化
長続きして使える評価表について紹介する。
・トップが評価して悪い部署を厳しく指導しようと考えてつくった評価表は、長続きしない。 トップは、最高レベルに達した状況を明確にイメージして発信するくらいに留める。
・その部署が自ら評価して、現状のレベルを認識した上で次のレベルを自発的に目指すように書くべきである。
・評価の項目が20項目30項目と多い評価表は何の意昧もなくなる。
評価をしただけで満足してしまい、次のレベルヘ上がるための工夫をしなくなる。また、項目が多くなればなるほど専門家による評価でなければ出来なくなる。
・評価レベルを決めるために、細かな数値によって明確に線を引くような事はしないほうがよい。横並びの比較評価は難しくなるが、モノづくり現場は千差万別なのであるから、ある程度評価者の裁量にゆだねる部分があったほうがよい。
・横並びでの評価レベルを合わせることは、事例を公開して合わせていくほうが実態に合った評価になる。
評価がすべて最高レベルになったらさらに高い評価項目を追加して、いつまでも活動が持続できるようにする。
見える化の成果評価
見える化の成果評価のポイント
KPIの設定
見える化の目的に応じて、成果指標(KPI)を明確にすることが前提です。
生産性向上:作業時間、稼働率、不良率
品質改善:クレーム件数、ミスの発生率
コスト削減:材料ロス、在庫金額
業務スピード:リードタイム、処理件数
KPIは「見える化前」と「見える化後」で比較できるように設定します。
定量評価と定性評価
定量評価:数値での効果測定(前後比較、推移のグラフ化など)
定性評価:現場の声や業務改善の体感(アンケート、ヒアリング)
PDCAサイクルへの組み込み
見える化は導入して終わりではなく、「見える → 気づく → 対応する → 再評価する」というサイクルで運用されているかが成果を左右します。
行動変容の有無
見える化によって、社員や現場担当者の行動に変化が出たかを観察します。
自発的な改善提案が増えた
異常への反応が早くなった
情報共有が活性化した など
可視化ツールの活用度
導入したダッシュボード、帳票、モニターなどが実際に活用されているか(閲覧数、利用頻度など)
成果報告のフォーマット(例)
評価項目 | Before | After | 評価コメント |
---|---|---|---|
生産性(件/日) | 100 | 130 | 見える化によりボトルネックを解消 |
ミス発生件数 | 月10件 | 月4件 | エラー傾向が可視化され、注意喚起が強化 |
現場の声 | – | – | 「業務が分かりやすくなった」という声多数 |
工場における見える化の未来トレンド
リアルタイム × IoT・センサーの進化
機械や作業者に取り付けたIoTセンサーが、リアルタイムで稼働・異常・環境データを収集。
例:温度や振動、音から“故障の予兆”を自動検知して見える化。
AI × データ分析で“意味”を見せる
単なるグラフ表示から、AIが「傾向分析」「異常値検出」「原因推定」をしてくれる時代に。
現場に「何をどう改善すべきか」を提案するインサイト提供型の見える化が進む。
AR/VRを活用した空間見える化
工場内の工程や設備情報をAR(拡張現実)で重ねて表示。保守や教育も効率化。
VRによる遠隔監視やシミュレーションで、経験の浅い作業者の支援も可能に。
人の動きも“見える化”
作業者の動線、姿勢、作業時間などをAIカメラやウェアラブルで可視化。
無駄な動き・待ち時間の見える化→標準化・効率化へつなげる。
エッジコンピューティング × 自律判断
現場端末で高速なデータ処理を行い、その場で判断&アクションを実行。
例:異常検知→自動停止→メンテ担当へ通知、までが“人を介さず”実現。
「エッジ(端末)でデータ処理を行う仕組み」のことです。
通常のクラウド処理とは違って、センサーや機械のすぐ近く(エッジ)で情報を処理します。
クラウド vs エッジのイメージ
項目 | クラウドコンピューティング | エッジコンピューティング |
---|---|---|
データ処理場所 | クラウド(遠隔サーバ) | 現場の近く(装置やゲートウェイ) |
処理スピード | やや遅い(ネット越し通信) | 速い(リアルタイム処理) |
通信の必要性 | 常にネット接続が必要 | ネット接続なしでも動作可能 |
向いている用途 | データ蓄積・長期分析など | リアルタイム制御・即時判断が必要な場面 |
脱・現場頼みの“誰でも運用できる工場”へ
熟練者の勘や経験に頼らない、標準化・共有化された知識と判断基準を見える化で実現。
人材不足の中でも高い品質と効率を維持できる仕組みへ。
見える化 未来のキーワード
キーワード | 未来像のイメージ |
---|---|
自律型工場(スマートファクトリー) | 異常検知から改善提案までが自動/半自動で進む |
ダークファクトリー(無人工場) | 夜間や休日は人がいなくても生産・監視が可能に |
サイバーフィジカルシステム(CPS) | 工場内の動きが仮想空間にリアルタイムに再現され、最適化シミュレーションが可能 |
コックピット化 | 経営層・現場責任者が“工場全体”を1画面で把握&意思決定できるように |
これからの見える化は「課題解決型」へ
これまでは「見えるようにすること」が目的だった見える化が、 今後は「見えて=すぐに動ける/判断できる/自律的に改善できる」ことが求められてきます。
更に詳細な『見える管理の基本』『見える管理の提案事例』は下記の記事に掲載しています。
関連記事:見える管理~見える化の基本
関連記事:目に見える管理 提案事例
*工場のカイゼンについては下記の文献に色々な活動事例等が更に詳細に記載されています。
参考文献: