- 物流改善の基本とは?~物流センターを効率化する具体策
- 物流改善とは何か?〜現場力を高めるカギは「流れ」にあり〜
- 物流とは?その役割をもう一度見直す
- なぜ物流改善が重要なのか?
- 改善は「現場の見える化」から始まる
- よく使われる改善手法
- 成果を「数値」で見える化しよう
- 物流改善は「全体最適の視点」で
- 倉庫での改善手法 現場力を高める10のアプローチ
- 1. レイアウト改善:動線を整え、無駄な移動をなくす
- 2. 5S活動:整理・整頓・清掃・清潔・しつけ
- 3. ピッキング改善:探す時間と歩行距離を削減
- 4. 在庫管理の見直し:過不足のムダを防ぐ
- 5. 入出庫の標準化:作業のバラつきをなくす
- 6. マテハン機器の導入:作業の自動化・省力化
- 7. ミス防止のポカヨケ:人間は間違える前提で仕組みを作る
- 8. IT・デジタル化の活用:リアルタイム管理へ
- 9. 作業者の教育と動機づけ
- 10. KPI管理と定期レビュー:成果の見える化
- 小さな改善の積み重ねが大きな変化に
- AI・ChatGPTによる物流改善とは?
- ChatGPTが物流現場でできること
- 物流業務別:ChatGPTの具体的な活用例
- ChatGPT × 他システムとの連携
- ChatGPT導入で得られるメリット
- 導入時の注意点とコツ
- まとめ
- スライドシェア 無料パワポ資料 ダウンロード
物流改善の基本とは?~物流センターを効率化する具体策
物流改善を成功させるには、物流センターや工場倉庫での基本的なポイントを押さえることが重要です。本記事では、物流改善の基本から、マテハン(マテリアルハンドリング)の改善方法まで具体的に解説します。
関連記事:マテハン分析の進め方
お金をかけずにできる物流改善アイデア【現場の知恵】
億単位の資金を投資してで物流改革を進めることで、コスト削減や効率化の実現をする前にやるべきことがあります、現場の知恵を活かすことです。大規模な物流関連機器を導入したり、情報システムの刷新を図ったりするのではな<、まずは現場で創意工夫を凝らして物流改善を行うことです。
具体的には物流倉庫、物流センターのレイアウトを変えたり、梱包をシンプルにしたりすることで物流コストも物流効率も大き<変わってきます。
そこで「お金をかけずにすぐできる物流現場改善」のポイント、知恵を使って解決する物流現場改善の基礎を解説します。
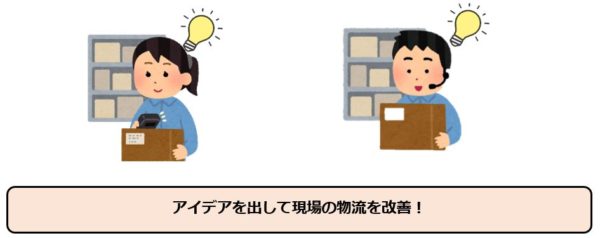
知恵を出して現場の物流を改善
YouTube動画 物流現場の改善事例
【賢者の選択】物流の現場に革命を起こす画期的な「台車」とは】
キャタピラー台車、アシスト台車及び免許が不要なフォークリフトの紹介
キャタピラ・クローラー付きの台車
階段を登れるタイプのキャタピラ・クローラー付きの台車。
電動アシスト台車
重い荷物を載せても、電動のアシスト力で安定して楽に運ぶことができる台車です。 電動アシストがついた台車により、重量物運搬作業による体への負担軽減。
トラスコ α電動台車オートランナー 900×600 OR501
電動昇降台車 高層ピッキングマシーン
フォークリフトとは違い、高層ピッキングマシーン(ハイピックランナー)『Hypick Runner』は通路幅が最小1.1~1.4mのみで運用可能なため、限られた倉庫内により多くの収納ラックが設置できます。倉庫内の上部空間に留まらず、大型店舗の製品補充、空港でのピッキング作業など幅広い場面で活躍できます。
免許不要で操作も簡単。使用前に安全教育、操作講習のみでどなたでも乗車ができます。パレットごと上げ下げをしないで必要なものだけを人の手で取りにいけるため作業効率がUP。作業性が大幅に上がるため人手不足解消にも効果を発揮します。
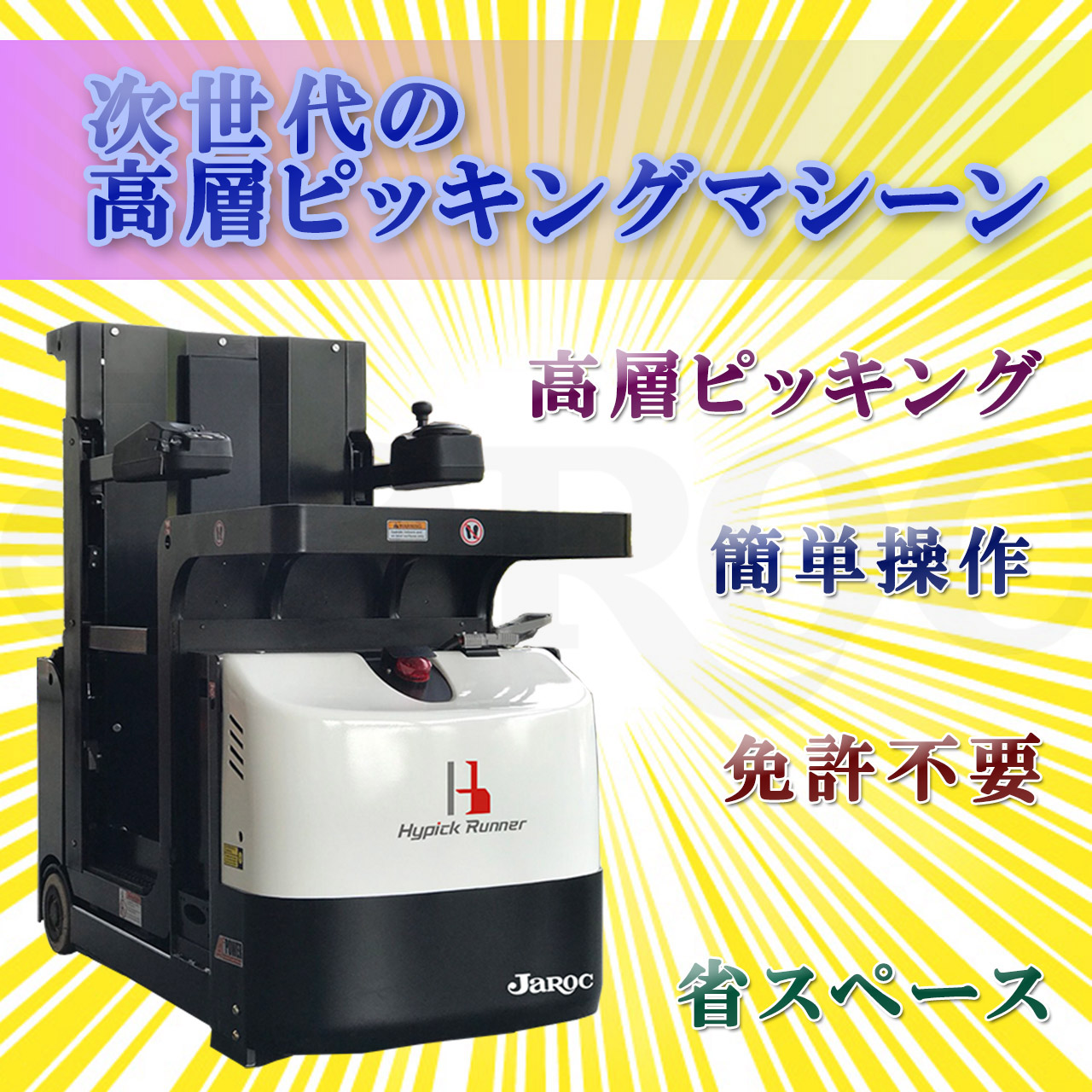
高層ピッキングマシーン(ハイピックランナー)
物流改善とは何か?〜現場力を高めるカギは「流れ」にあり〜
私たちの身の回りにあるほとんどのモノは、作られて終わりではありません。工場で生産された商品が、倉庫に保管され、輸送され、店頭に並び、消費者のもとへと届く――そのすべてを支えているのが「物流」です。
そして、そんな物流にひそむ「ムダ」や「ムリ」をなくし、効率よく、安定して流れるようにする取り組みが、物流改善です。
物流とは?その役割をもう一度見直す
物流とは単に“運ぶ”ことではありません。企業活動における物流は、以下の5大機能から成り立っています。
項目 | 概要 |
---|---|
輸送 | モノを必要な場所へ届けること(トラック、船など) |
保管 | 必要な時期まで安全に保管すること |
荷役 | 荷物の積み下ろしや移動、仕分け作業 |
包装 | 壊れやすい商品やバラ物を適切に梱包すること |
流通加工 | 商品に値札を貼る、セットを組むなどの加工工程 |
これらを適切に設計し、改善していくことが「物流改善」の本質です。
なぜ物流改善が重要なのか?
現代の市場では、「納期の短縮」「品揃えの多様化」「人手不足」など、あらゆるプレッシャーが物流現場にのしかかっています。その中で、物流の非効率=企業の競争力低下と直結する時代です。
物流改善の目的は、大きく以下のように分類されます。
- コストの削減(人件費、在庫費、輸送費)
- 納期の短縮(リードタイムの圧縮)
- 品質向上(誤出荷や破損防止)
- 働きやすい環境づくり(作業負担の軽減)
- 在庫の適正化(欠品や過剰在庫の抑制)
たとえば、部品倉庫の配置を変えただけでピッキング時間が30%短縮された例や、在庫管理システムを導入して月100万円の在庫削減に成功した事例もあります。
改善は「現場の見える化」から始まる
物流改善の第一歩は、「現場の見える化」です。たとえば以下のような分析が有効です。
- 動線分析(ヒートマップ):作業者がどの経路を通っているか
- 時間観測:作業ごとにかかっている秒数
- 作業分析:「歩く・探す・待つ」などのムダ動作の有無
こうして現場を“見える化”することで、「改善のタネ」が明確になります。
よく使われる改善手法
物流改善でよく活用される代表的な施策は以下の通りです。
改善項目 | 内容例 |
---|---|
倉庫レイアウト | ピッキング頻度に応じたゾーニング、通路幅の最適化 |
作業手順の標準化 | 作業マニュアルの整備、動画による教育 |
在庫管理 | ABC分析、先入先出、定点補充 |
マテハン導入 | ハンドリフト、AGV(自動搬送車)、棚搬送ロボット |
ITシステム活用 | WMS(倉庫管理)、TMS(輸配送管理)導入 |
特に最近では、AIを活用した需要予測や物流シミュレーションも注目されています。ムダな在庫を抱えず、必要な商品だけを効率的に供給するという理想に近づきつつあります。
成果を「数値」で見える化しよう
改善の成果を評価するには、定量的な指標(KPI)が欠かせません。たとえば:
- ピッキング1件あたりの作業時間(秒)
- 1人1時間あたりの処理件数
- 誤出荷率(%)
- 在庫回転率
- 輸送費用/商品1個あたり
これらのデータを月次で追い、**PDCA(計画・実行・評価・改善)**を繰り返すことが改善の定着につながります。
物流改善は「全体最適の視点」で
物流改善でありがちな落とし穴は「部分最適」です。たとえば、「輸送コストを削減するためにまとめ出荷を増やしたら、倉庫がパンクした」というようなケースです。
物流は全体の流れをどうスムーズにするかが命です。「倉庫・輸送・在庫・受注処理・現場作業」が有機的につながることで、はじめて「改善」が成果として表れます。
今すぐできる改善アクション
- 倉庫の「歩行距離」を測ってみる
- よく出る商品に「赤札」を貼る
- ピッキング動作を動画で撮ってみる
- 出荷前チェックリストを導入する
- 在庫棚に「先入先出」のラベルをつける
たった1つのアクションでも、物流の流れが変わることは少なくありません。小さな改善の積み重ねが、大きな効果を生み出す――それが物流改善の本質です。
倉庫での改善手法 現場力を高める10のアプローチ
倉庫は物流の中枢を担う重要な拠点です。受け入れ、保管、出庫、梱包、出荷――すべてのプロセスがスムーズに流れて初めて、お客様への迅速な対応や在庫管理の正確性が実現できます。
しかし現場では、「探す時間が多い」「棚の前で渋滞する」「ミスが多い」など、さまざまな課題が顕在化しています。
そこで今回は、倉庫での改善手法を10のカテゴリに分けて、わかりやすく解説します。
1. レイアウト改善:動線を整え、無駄な移動をなくす
倉庫内での無駄な移動距離は、作業時間や疲労の大きな原因です。改善ポイントは以下の通りです。
- ABC分析による棚割り:出荷頻度が高い商品(Aランク)は出入口近くに配置
- ゾーニング:商品カテゴリごとにエリア分け
- ワンウェイ動線:一筆書きのように、戻らない流れを設計
👉 例:1人あたりのピッキング距離が1日2000m → 1200mに短縮、歩行時間を30%削減
物流現場の動線分析
物流現場の改善を考える場合に「作業動線を変えれば効率化が図れるのではないか」という考え方は役に立ちます。
庫内レイアウトを工夫することで物流効率が向上し、コスト削減が実現できます、庫内レイアウトはOne Wayが基本になります。
入荷から出荷までの作業動線が一筆書きで表せるようになっていることが望ましく、庫内全体の流れとしては、入荷、検品、保管、ビッキング、仕分け、積込み、出荷の各エリアを一方通行型に並べます。
作業動線が重複したり、後戻りしたりすることがないようにします。
なかでも重要なのがピッキングエリアです。「物流コストの3割が人件費」とよくいわれますが、そのうちの7割はピッキング作業者の人件費となっています。
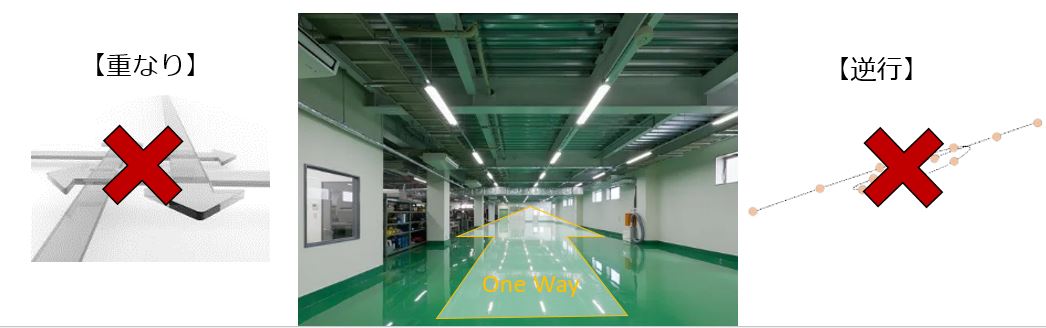
逆行、重なり NG
又、通路の片面だけではなく、棚の両面からピッキングできるようにもします。さらにいえば、動線はたんにOneWayにするだけではなく、歩行距離が可能な限り短くなるようにします。
在庫量が多い場合、出荷量が少ない物品は保管エリアとピッキングエリアを分けて、ピッキングの歩行距離を短くするという方法が有効です。作業者の動線を短くすることによってピッキング作業が効率化し、人員や残業の削減が可能になります。
また、保管エリアに中二階(メザニン)、移動ラック、自動倉庫などを導入し、ピッキングエリアを必要最小限にすることでスペース効率も高まります。この場合、ピッキングエリアではケース単位、あるいはバラ単位で保管し、必要に応じてパレット単位、あるいはケース単位で保管されている保管エリアから物品を補充します。
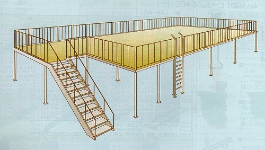
中二階(メザニン)
トータル在庫量が少なく出荷量が多い場合には、保管エリアとピッキングエリアを統合するレイアウトも考えられます。もちろんピッキングエリアに限らず、物流センターやトラック運送営業所のレイアウトや動線を工夫することで作業効率が格段に向上することが少なくありません。
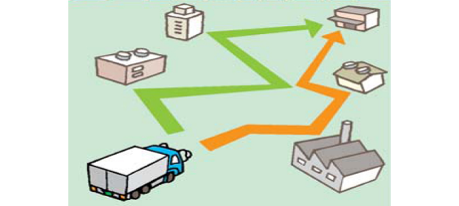
物流センター 動線
ピッキング作業から検品、梱包、出荷にいたる流れをスムーズにするための工夫も重要です。ピッキング作業に時間がかかってしまい、出荷に影響が及ぶということがあります。したがって出荷エリアまでムダのない動線が必要になってきます。
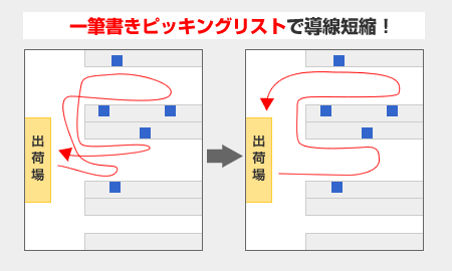
ピッキング作業 動線分析
YouTube動画 物流現場の動線改善事例
<富士ロジテック> 作業動線の改善(該当動画:2分から)
YouTube動画 移動ラック、レール式移動棚
2. 5S活動:整理・整頓・清掃・清潔・しつけ
5Sは倉庫改善の基本中の基本です。
活動 | 内容例 |
---|---|
整理 | 不要な棚・工具・資材の廃棄 |
整頓 | 定位置・定品・定量で管理 |
清掃 | 日々の掃き掃除と床のチェック |
清潔 | 汚れの原因を根絶 |
しつけ | ルール・マナーの徹底 |
棚に「定位置ラベル」や「定量ライン」を引くだけで、探す時間や間違いを激減できます。
3. ピッキング改善:探す時間と歩行距離を削減
ピッキングミスや時間のばらつきは、物流品質に直結します。
- デジタルピッキング(ライト・音声)
- ピッキングカート導入(段ボールセット済)
- バッチピッキング(複数伝票のまとめ処理)
- ピッキングリストの写真付き化
👉 例:1伝票平均ピッキング時間が4分 → 2分半に短縮し、作業者2人分を削減
ABC分析のよるピッキングしやすいレイアウト
出荷頻度の高い物品のピッキング作業などについての庫内移動距離は可能な限り短くしたいところです。そこでたとえばピッキングェリア内では、出荷頻度の高い物品を入出荷囗に近い場所に集中させます。
ABC分析をふまえて出荷頻度別に物品の配置を決めるのです。
出荷頻度の高いA品目の物品は入出荷バースにもっとも近いところに置きます。
~ABC分析とは~
ABC分析は下図のように、縦軸に出庫金額、横軸に品目を出庫金額の大きい順に並べ、A、B、Cの3ランクに分ける。
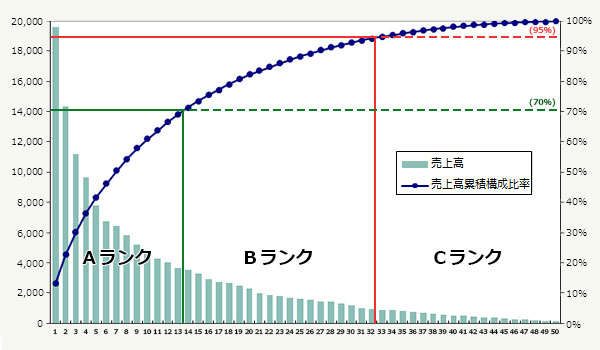
物流改善 ABC分析
頻繁に出荷する物品が出荷バースに近ければ、作業時間や歩行距離の大幅な短縮が可能になります。
次いでB品目、C品目の順に出荷バースに近いところから配置します。比較的出荷頻度の低い物品は出荷バースから離れていても、作業の進捗に大きな影響を及ばさないと考えられるからです。
季節波動、曜日波動などに応じてピッキングエリアのレイアウトを適時、変更することも効果的です、季節や曜日などの状況に応じてA品目の物品が変化することがあるからです。また出荷頻度の大きかった物品がモデルチェンジなどの影響で頻度が下がることもあります。出荷量、出荷頻度は適時、チェックします。
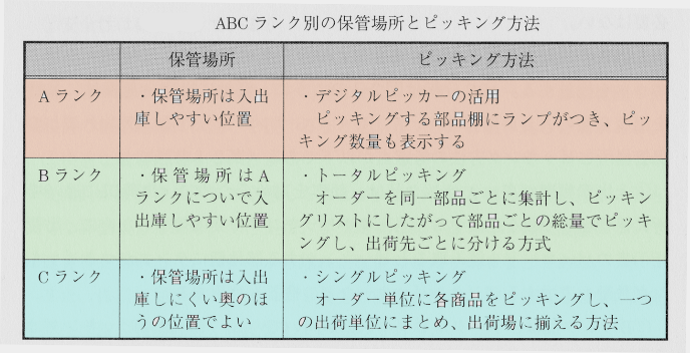
ABC分析による保管場所
YouTube動画 アマゾン 出品サービス 物流改善事例
Amazonフルフィルメントセンター動画ツアー(該当動画 2:55から)
4. 在庫管理の見直し:過不足のムダを防ぐ
在庫が多すぎると倉庫が圧迫され、少なすぎると欠品が発生します。
- ABC分析で管理強化
- 先入先出のルール化(棚に日付表示)
- ロケーション管理の導入
- 定期棚卸をサイクルカウント化(毎日1列だけなど)
👉 例:在庫精度が90% → 98%に向上。誤出荷も激減。
5. 入出庫の標準化:作業のバラつきをなくす
誰がやっても同じ品質になるよう、「標準化」は非常に重要です。
- 作業手順書(イラスト入り)
- 動画マニュアル
- 新人用チェックリスト
- 異常時ルールの掲示
👉 ベテラン頼みだった出庫作業が新人でもできるようになり、教育時間が1/2に短縮
6. マテハン機器の導入:作業の自動化・省力化
機器名 | 効果 |
---|---|
ハンドリフト | 重量物移動の負荷軽減 |
パレットラック | 空間効率向上、保管容量アップ |
AGV | ピッキング後の自動搬送 |
自動棚 | 高さのある空間も有効活用 |
特に重たい荷物の多い倉庫では、腰痛・けが防止にも直結します。
7. ミス防止のポカヨケ:人間は間違える前提で仕組みを作る
- 2重チェックリスト(ピッキング→梱包)
- スキャンチェックによる照合
- 重量センサーで入れ忘れを検出
- 出荷前に音声読み上げシステムで確認
👉 出荷ミス率が月10件 → 月2件以下に減少した実例あり
8. IT・デジタル化の活用:リアルタイム管理へ
- WMS(倉庫管理システム)
- ハンディ端末(バーコード・QR)
- クラウドでの在庫連携
- AIによる需要予測と自動発注
👉 在庫データの“見える化”により、担当者が現場にいなくても状況がわかるように
9. 作業者の教育と動機づけ
作業の効率や品質は「人」に大きく依存します。
- 多能工化(複数作業を覚えてもらう)
- 改善提案制度
- 月間MVP制度でやる気向上
- スキルマップによる人材育成
現場の声から改善が生まれる風土をつくることが、持続的改善のカギです。
10. KPI管理と定期レビュー:成果の見える化
改善活動の効果を数字で追いましょう。
指標 | 意味 |
---|---|
ピッキング1件時間 | 作業の効率を数値で確認 |
作業者1人あたり処理件数 | 労働生産性を把握 |
在庫精度 | 実数とシステム在庫の一致度 |
誤出荷率 | 品質管理の最重要指標 |
週報や月報で数字を共有することで、チームの意識も高まります。
小さな改善の積み重ねが大きな変化に
倉庫改善において重要なのは、「いきなり大がかりな投資をしなくても、できることはある」という視点です。たとえば、現場に1本のテープを貼って動線を整理するだけでも作業効率は向上します。
また、改善は「1回やって終わり」ではなく、継続的に見直し・挑戦・学びを繰り返す文化がある現場こそが、長期的に強くなっていきます。
横持ちゼロ~仮置きの削減
部品倉庫や物流センター内などの動線を考えた場合、「横持ちを極力減らす」ということはきわめて重要です。「横持ちゼ囗」が物流改善のーつの大きな目標となります、横持ち輸送は、お金を生まない物流であるため、その回数を減らすことが求められます。
横持ちとは同一地域、拠点内で諸事情から行われる搬送、輸送作業のことです。同じ工場内、総庫内での搬送や、工場や物流センターへの近隣の外部倉庫などからの輸送のことです。目的が明確でないにもかかわらず物品の移動が最短距離を経由せずに行われることを指します。
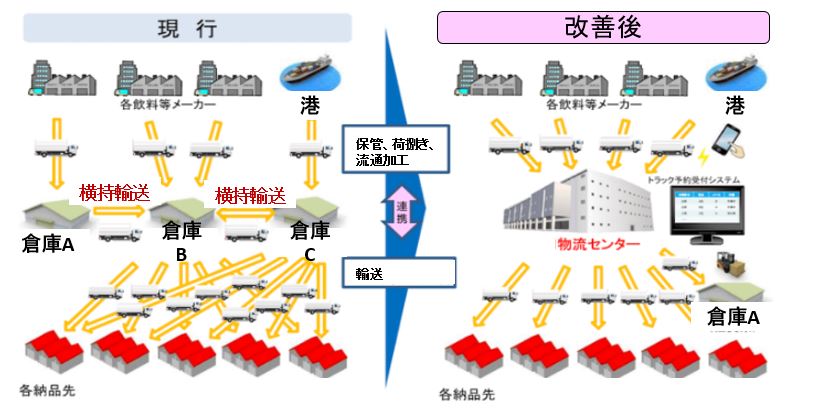
横持ち 改善
横持ちが多いのは作業にムダが多く、必要以上に仮置き場や外部倉庫などを構えているからと考えられます、 したがって横持ちがないように最短距離での物品の移動を推進することが物流改善につながります。
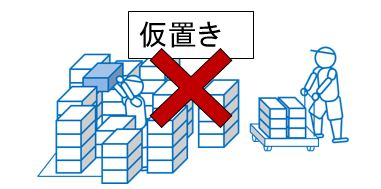
仮置き場
たとえば頻繁に出荷される製品が入出荷バースから離れた場所に保管されていれば、保管エリアから入出荷バースヘの頻繁な搬送が必要になります。その結果、作業プロセスに余分な手間が入り込んでくることになります。
(バース:荷物の積み下ろしのために船、トラックがある場所)
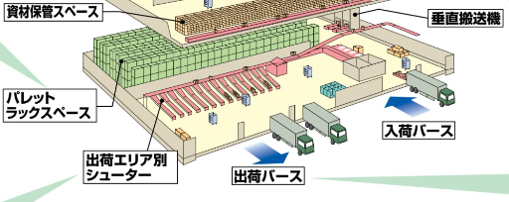
入出荷バース
また、工場の近隣の外部倉庫に保管されている場合、横持ちが頻繁に行われるようならば、そのための搬入の手間や輸送コストは無視できません。出荷量の多い製品などを外部倉庫に保管するのは得策とはいえないのです。
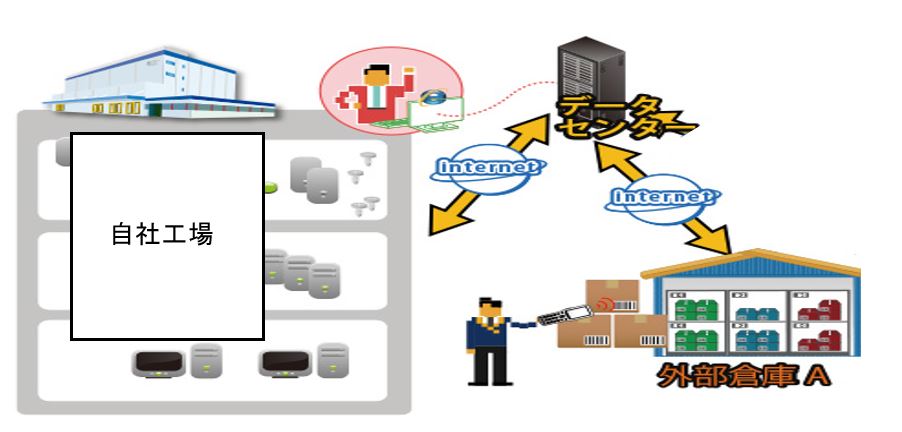
外部倉庫 自社倉庫
物流の基本は生産、配送リードタイムの短縮です、そして場内、庫内の横持ちを解消するためにはリードタイムの短い商品と長い商品を一緒に保管しないようにします。
そしてリードタイムの短い商品は回転ラックなどには格納せずにパレットなどに平置きして入出荷バースのそばに置くようにします。外部倉庫などにもできるだけリードタイムが長い物品は保管しないようにします。
さらにいえば大きさ、形状、重量などの物理的に類似した物品や類似品一関連製品はまとめておくと、トラックへの積込みがスムーズになります。
YouTube動画 リードタイムの短縮 物流改善事例
納期改善->滞留の見える化による
レイアウト改善で保管効率アップ
アイテム数、数量などが増えてくると、「このままでは現在の倉庫では保管スペースが足りなくなる」という問題が必ず浮上します。工場などの自社倉庫の在庫が膨らんだ場合、付近に外部倉庫を賃貸する必要が出てくるというわけです。しかし、外部倉庫を借りるとなると、その賃料は相当の額に上がります。
できれば現在の保管スペースの効率アップを図り、保管コストを抑えたいところです。
初めに倉庫内を保管スペース、作業スペース、仮置きスペース、その他(通路など)に分類します。
次に保管効率を向上させるために仮置き場に着目します、仮置き場は一見、作業効率を効率的に行うために必要なスペースに思えます。けれども多くの場合は逆に作業効率を落としムダなスペースです。
仮置き場を少なくするためには、入荷、入庫、格納、保管、出庫、出荷という庫内の一連の作業の流れをできる限り統合することです。
たとえば「大量に入荷した物品をいったん保管エリアに仮置きして、それから順次、棚入れ、格納していく」ことを禁止します、入荷と棚入れ・格納のプロセスを統合すれば仮置き場を省くことができるわけです、又「検品作業が忙しいので梱包しなければならない物品はとりあえず仮置きしておく」といったことも好ましくありません。
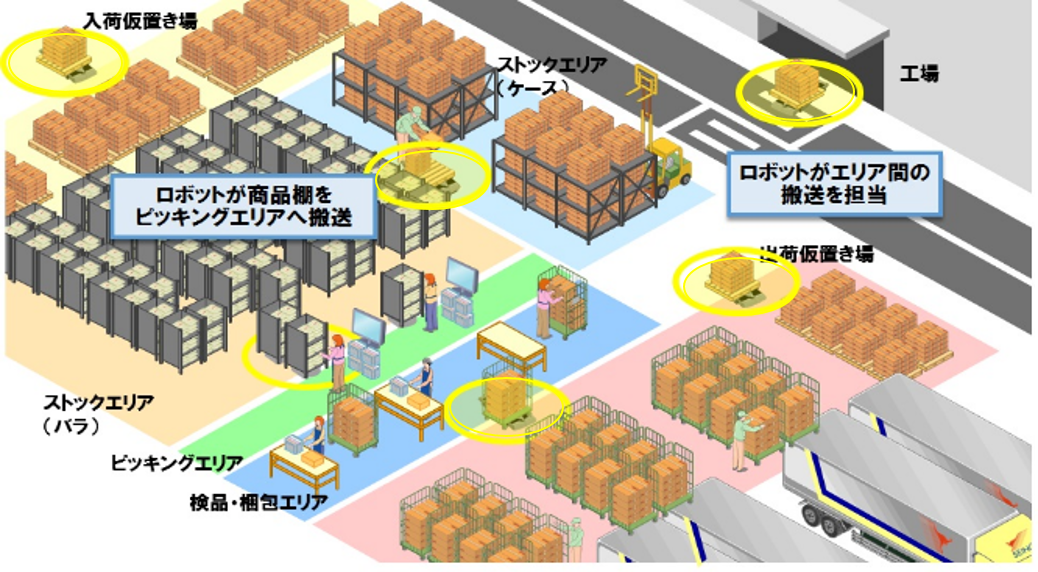
仮置き 調査
YouTube動画 倉庫 レイアウト改善事例
トヨタ生産方式:工場の流れの見える化改善で生産力を高めよう
物流現場の見える化
物流現場の「見える化」を図ることで作業効率が大きく向上することも少なくありません。なかでも物流センター内の見える化においてロケーション管理をしっかり行うことはきわめて重要です。
たとえば、入庫、棚入れ作業において工場、部品センター、物流センターなどでは、材料・資材、部品などが入荷されると、その都度、保管スペースを定められることがあります。しかしこれでは「どこにどの物品があるのか」ということがわからなくなる危険があります。
また入庫、棚入れについても時間がかかってしまうかもしれません。つまり場内、庫内が荷繰りや荷探しを誘発しやすい環境になってしまうのです。無論、それは荷役コストにも大きく影響します。
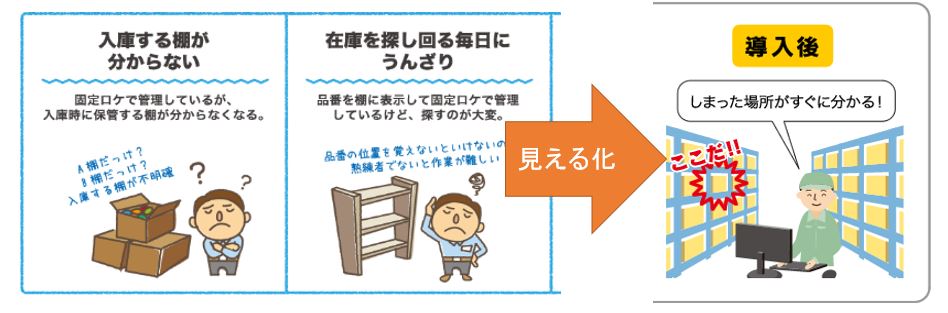
物流現場の見える化
又、固定ロケーションでは商品別に格納エリア、保管エリアに所番地をきちんと設けて、しっかり管理します。これに対してフリーロケーションは空所となっている任意の所番地に商品を順次格納していく方式です。
固定ロケーションかフリーロケーションか、どちらを用いるかは取扱品目や入出荷量、在庫量、物流システムの特徴などを総合的に考慮して決定しますが、重要なことはどの物品がどこに格納・保管されているのかをしっかりと把握し、それを作業者に対して、見える化をしておくということです。
ロケーション管理に限らず、庫内のさまざまな物品の収納・保管に際して看板表示を採用したり、色別管理を行ったりすることで、すぐ見てわかるような作業環境を提供することで効率化を図るのです。
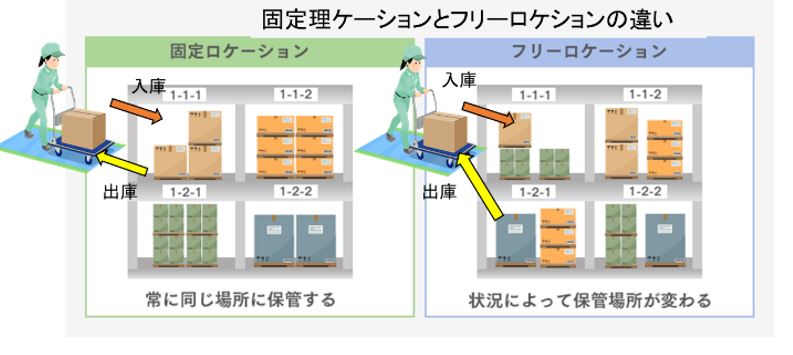
固定ロケーション&フリーロケーション
YouTube動画 物流 倉庫 見える化 改善事例
物流現場の見える化と作業品質向上を実現!物流現場IoTソリューション
物流 8ないの徹底
良い物流センターは作業者が「8ない」となるようになっている、といわれています。「8ない」とは、
(1)歩かせない (2)持たせない (3)待たせない (4)探させない
(5)考えさせない(6)書かせない(7)屈ませない(8)拭かせない
理想の物流センターは動線のムダをなくし、効率的にしますので作業者が待たず、そして必要以上に歩きません。
また必要以上に物品や工具、マテハン機器を持っていることもありません。
「次にどんな作業をすればいいんだろう」と作業者が考え込むこともありませんし、
又、「どこに何があるのだろうか」と探し回ることもありません。
更にどこに何があるのかを他の作業者に聞かなければわからないといったこともありません。作業手順などをメモ書きして覚えたり、必要事項を書き込んだりといった手間が作業中に発生することもあってはならないのです。
すなわち、庫内は見える化された環境で、作業者は最短の動線と効率的なレイアウトのもとで、「次にはこうするんだな」という手順が庫内の適所に示されているというのが理想となるわけです。
そして「屈ませない」はピッキングや格納、梱包作業でスタッフが前のめりになるか、膝を曲げ、腰を下げながら作業をする動作で作業者の腰に負担になるような動作、「屈ませない」ことも重要です。
最後に「拭かせない」はタオルで汗を拭かせない、空調設備の必要性を意味しています。夏場の倉庫の温度は高くなりやすく、高温下での作業は疲労が生じやすく、また安全事故も発生しやすくなります。
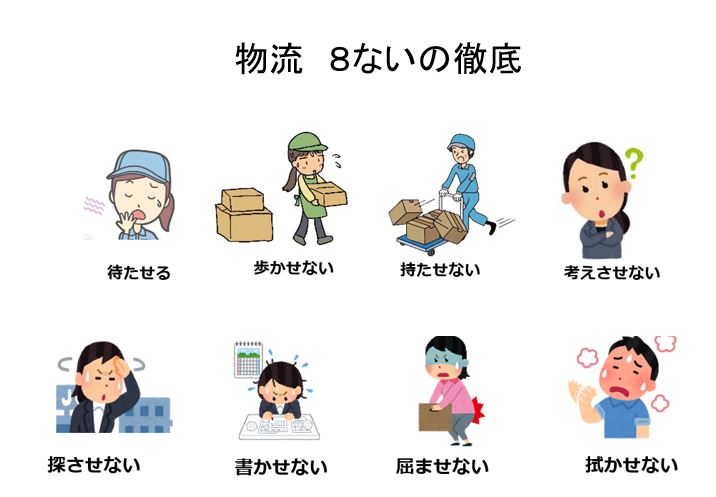
物流 8ない
YouTube動画 物流改善事例
トヨタL&F物流ソリューション導入事例(株式会社アステム様)
物流 7つのムダ
トヨタ生産方式の製造ラインの改善のツールとして「7つのムダ取り」があります。
このツールは『物流 8ない』と関連しますが物流改善に活かせます。
発注すぎのムダ
現在、必要な量以上のモノを発注することは余剰在庫の増加に繋がります。
例えば4個だけで良い商品を発注するときに10個も発注すれば、6個は現在は不要な在庫になり、管理費、固定費が掛かります。
手待ちのムダ
運搬作業で、品物が来るのをボーッと待っている運搬者がいないか?その時間が1分だったとしても、その後の運搬者も停滞待ちになりので非常にムダになります。
運搬のムダ
トラックから品物が運び込まれたときに、その品物を倉庫の空いている場所に置きます。トラックからその空き地までの距離を、もっと短くすることができたら、作業速度も速くなります。
在庫のムダ
在庫している商品のムダには3種類あります。1つ目は、在庫したまま流通しない商品があるかどうかです。2つ目は、過剰に在庫していないかどうか。3つ目は、在庫しているものが消費期限切れになったり、不良品だったりしていないです。
探すムダ
普段使う道具は、置く場所を決めて、それを共有できているか、例えばハサミが見当たらなくて探す場合、その時間はムダです。
探すムダ
庫内は見える化された環境で、作業者は最短の動線と効率的なレイアウトのもとで、「次にはこうするんだな」という手順が庫内の適所に示されており、書かせる、覚える、考えるムダがなく、円滑に運搬、移動が可能な状態が理想です。
配送ミスのムダ
配送ミスはあるものですが、そのミスを場当たり的に対処するのではなく、そもそもの原因を追求して改善し、再発防止を行う。
定位、定品、定量を極める
定位・定品・定量をあわせて「3定」といいます。
3定を行うのはまず、どこに何をいくつ置くかということをしっかりと決めます。そのうえでラック(棚)を活用したり、白線を引いたり、ファイリングを行ったりといった置き場所の整理を行います。
ラック(棚)などについては所番地を行い、ロケーション管理をし、次に置かれている物品の棚板には品目表示をするように、あわせて在庫が一目でわかるように最大量と最小量、最適量などを明示します。
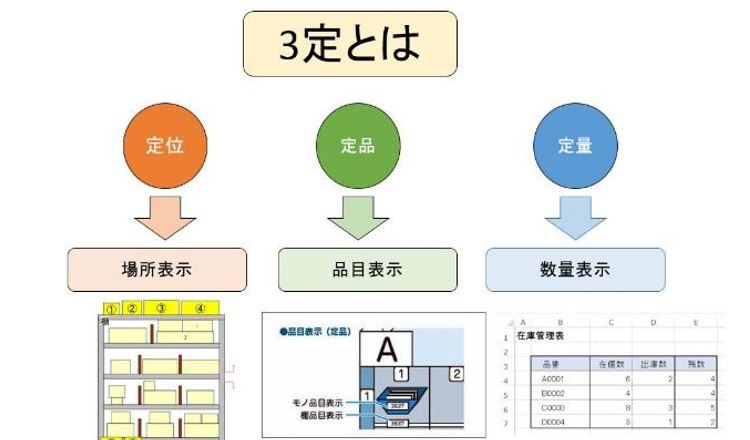
定位・定品・定量をあわせて「3定」
定位とは?
定位とはモノの場所表示することです、モノをどこに置くかといった時の「どこに」の表示が「場所表示」です、「所番地表示」ともいわれています。
下図で場所表示を示している、Aが所表示であり、これは建屋の中でただ1つの名前となります、次に丁目、番地を表示します。
これは①、②、③の横の数字は丁目を表し、縦の数字は番地を表します。このように、所番地をハッキリ明示した工場では、新しく入ってきたパートの作業者に「A-2-2の棚」と指定するだけで、目的の棚へ行くことができるのです。このように、誰でも、目で見てわかるようにすることが大切です。
定品とは?
定品とは「品目表示」の事です。
「品目表示」する場合は「モノ品目表示」と「棚品目表示」を表示します。
モノ品目表示は、「置くモノ自体が何であるか」を示し、置かれているモノが入っている容器に表示したり、置かれているモノ自体に品名が入っている場合は、誰が見てもわかるように品名を表に向けて棚に置いたりします。
棚品目表示は、モノを「どこに置いたらよいか」を示す名札であり、モノが置かれている棚板に表示します。
定量とは?
定量とは「数量表示」の事です。
置かれているモノが適切な在庫量なのかどうか、量の表示をします。
具体的には在庫管理表を現場に掲示しますが誰が見てもひと目で在庫量が判断できように看板および大型液晶モニターで在庫量を表示するのがベターです。
3定をきちんとすることで荷繰りや荷探しが減少します、荷繰りとは保管品を取り出す際にその保管位置の手前などにある物品を一時的に別の場所に移動させることなどを指します。意味のない仮置きのことです。
例えば倉庫の中、トラックの荷台の上などで、荷物を並べることです。あるいは探し出して、運ぶことです。
また、荷探しとはその名の通り。「荷物を探す手間」のことです。「どこに保管物があるのかわからない」という状態では入出庫処理やピッキング作業が円滑に進みません。「どこに何が保管されているかが瞬時にわかり、それをスムーズに出し入れできる」というのが最善の保管状態です。
又、段ボールで保管物を段積みしておくと、最初に定めた保管場所以外の通路などに一時的に別の保管物を置かなければならなくなります。そうなれば通常の保管品を取り出す場合には手前の通路の物品を一度、移動させる必要が出てきます。しかしこれでは通路の物品にかかる移動時間が相当なものになってしまいます。
また、通路が死角になって「保管物がきちんとそこにあるか」ということがわからなくなります。
AI・ChatGPTによる物流改善とは?
~人とAIが協力する新時代の現場改革~
近年、物流業界は人手不足、配送遅延、誤出荷、在庫過多など、数多くの課題に直面しています。そんな中で注目されているのが、AI、特に生成AI(ChatGPTなど)を活用した物流改善です。
AIはもはや「未来の技術」ではなく、「現場ですぐに使える改善ツール」として急速に広がっています。では、ChatGPTのような対話型AIをどのように物流現場で活用できるのでしょうか?
ChatGPTが物流現場でできること
ChatGPTは、単なるチャットボットではなく、知識の提案者・文書作成者・意思決定支援ツールとして機能します。物流改善で活用できる主な領域は以下の通りです。
1. 改善案のブレインストーミング
- 「誤出荷が多いがどう改善すればよいか?」
- 「倉庫の動線を短縮するレイアウトアイデアは?」
といった問いに対し、ChatGPTは現場知識+改善手法を組み合わせて多角的な提案をしてくれます。
2. 作業標準書・マニュアルの作成支援
作業手順書、5Sマニュアル、フォークリフト安全指導資料など、現場文書の作成を自動化できます。
例:
「新人向けのピッキング作業マニュアルを作って」と指示すると、見出し、注意点、ステップが自動生成されます。
3. KPIデータの解釈と改善提案
倉庫のKPI(出荷ミス率、在庫回転率、作業時間など)を入力すると、「なぜ数値が悪化したか?」「どこを改善すべきか?」といった分析まで行えます。
例:
在庫精度:92% → ChatGPT:「ABC分析を導入し、Aランク商品から棚卸頻度を高めましょう」
物流業務別:ChatGPTの具体的な活用例
業務領域 | 活用例 |
---|---|
倉庫内作業 | 作業指示書の作成、ピッキング動線の改善案、5Sチェックリスト作成 |
輸送管理 | 積載効率アップの提案、ドライバー教育文書、配送ルートの最適化案 |
在庫管理 | 在庫過多の原因分析、棚卸方法の提案、先入先出ルールの見直し |
現場教育 | クイズ形式の教育資料、音声読み上げ対応、質問対応チャット |
ChatGPTは、あくまで人間の「考える力」「判断力」を補助する存在です。人とAIの協働が、物流改善のスピードと精度を一段階引き上げます。
ChatGPT × 他システムとの連携
ChatGPTは単体でも便利ですが、以下のように既存の業務システムと組み合わせることで、より実践的になります。
- WMS(倉庫管理システム):エラー履歴をChatGPTで解析し、傾向と対策を提案
- ExcelやGoogleスプレッドシート:作業実績データからAIに要因分析させる
- スマートフォンやタブレット:音声入力で作業日報をChatGPTが自動整形
ChatGPT導入で得られるメリット
効果 | 内容 |
---|---|
属人化の解消 | 誰でも同じ手順や説明をAIから得られる |
作業時間の短縮 | 文書作成・分析業務を大幅に削減 |
教育コストの削減 | 新人教育をAIが一部代替できる |
改善文化の定着 | 「いつでも相談できるAI」が現場改善を後押し |
実際、ある中小企業では、ChatGPTによってマニュアル作成時間が1/5に短縮された事例もあります。
導入時の注意点とコツ
- AIにすべてを任せすぎない:AIはあくまで補助。判断は人が行う。
- 指示の仕方が重要:「どんな現場か?」「何に困っているか?」を具体的に伝える
- 小さく始めて効果を実感:まずはピッキング作業マニュアルの改善など、部分導入から始めると成功しやすい
まとめ
ChatGPTのような生成AIは、ホワイトカラー業務だけでなく、現場の改善活動にも確実に役立ちます。最初は「AIって難しそう…」と思っても、一度使ってみると「これ、もっと早く使えばよかった!」という声が多いのが実情です。
特に、以下のような悩みを持つ現場には強くおすすめします。
- 「作業ミスが多くて困っている」
- 「教育資料を毎回作るのが大変」
- 「改善したいがアイデアが出ない」
AIは「やる気のある現場の右腕」になります。今こそ、人とAIが協力する物流改善を始めてみませんか?
スライドシェア 無料パワポ資料 ダウンロード
物流改善の進め方【図解】のパワポ資料が無料でダウンロードできます。
自己学習、講座開催時にお役に立ててください。
おすすめ BOOK
鈴木 邦成 (著) 図解入門ビジネス 物流センターの改善の進め方がよ~くわかる本
コメント