機械を移動して無駄を省く
改善前
改善前は三名が作業していた(下図)。手前の女性(下図では①の作業者)は左手で袋を押さえ、右手で冷凍品を数えながら入れ、入れ終わるとその横の龍の中に置いていた(これを中間仕掛という)。
仕掛品がある程度まで溜まるとシールする人(下図②)がその龍を取りに来る。
そしてバンドシーラー機でシールをかけると、一番奥の女性(下図の③)が段ボール箱に入れテープをしてパレットに積んでいた。

食品工場 改善事例1 改善前
問題点
この作業の改善着眼点として次の三点がある。
①次工程との距離を縮められないか
袋入れ作業とシール作業が離れているため運搬が発生する。
②分業が進み過ぎていないか
それぞれの作業者に手待ちがでるのは分業が進み過ぎているためと共に、作業の発生場所が離れているためでもある。
③動作の効率を上げられないか
冷凍品を数えながら袋に入れる時、片手しか使用していない。
改善後
これを改善すると下図のようになる。
①工程の連結を高める:
バンドシール機を袋人れの作業者①の籠に置き、①の作業者が袋に入れた物を自分でシールできるようにする。
②両手作業で動作効率を高める:
袋を手で押さえているのを、手を離しても袋が外れないようにストッパーをつける。これによ
り両手作業が可能になり、袋人れの効率があがる。
③バトンタッチゾーンを作る
更に成型品の数量が多くなった時は、袋入れの作業者①だけでなく、段ボール箱詰めしている
作業者②の両者がシール作業を行うようにして、二名で作業を完成させるようにする。何故なら一分間で段ボール箱を組み立て、製品を袋に十個入れ、段ボール箱をシールしてパレットに積む作業は内容的に余裕がある。

食品工場 改善後 事例1
改善後の配置図の点線部分で、どちらかの于の空いた人が手の空いていない人を助けること(または場所)をバトンタッチゾーンと言う。
このようにするだけで包装の作業が三名から二名になり、包装の生産性は五割あがる。
U字型ラインで作業発生点を減らす
改善前:
離れ小島を無くす
Lの写真は一般的に見られる包装風景である。焼売の入ったトレーを横ピローストレッチ包装機で包装し、ラベルを自動的に貼りつけていた。
改善前の作業は二名で行っていた(下図)
一人はトレーを包装機のヒンガーに置き、もう一人は包装された製品を段ボール箱に入れていた。包装が必要な数量は1分間に十個程度。
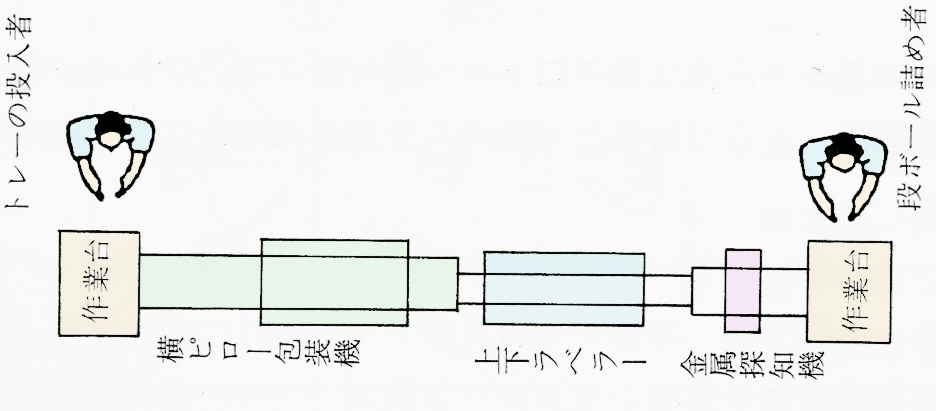
食品工場 改善事例2-改善前
問題点
この場合、作業の発生点が離れているため、二名の作業者がいて当たり前と考えられていた。この作業改善着眼点は次のようになる。
①工程の連結レベルを高められないか
投入場所と取り出し場所が離れている。
②作業発生場所を集めて減らせないか
作業者がそれぞれ離れ小島になっている。
③有効な作業なのか
段ボール箱を作る作業者が別にいて、必要に応じて運搬する。
改善後
作業発生場所が離れていると前記のような無駄が発生する。これを改善すると次のようになる(下図)

食品工場 改善事例2-改善後
①作業の発生場所を近づける
一人の作業者の所に入れたものが出てくるようにU字型ラインにする。
②手待ちをなくす
当然のことながら包装された製品は入れた数しか出てこない。例えば十個を一ケースとして段ボール箱に詰める場合、まず段ボール箱を組み立てて底をシールし、十個を流し、包装して出てきた製品を箱に入れて箱の上部をシールする
(この作業を1分間に一回繰り返す)。
必要な数だけ必要な時間内に生産すれば良いのに、直線型で二名で生産すると早く作り過ぎて手待ちが発生するか、作り過ぎによる不良在庫が発生する場合が多い。
見かけの改善より真の改善 動作経済の原則
配置を工夫するだけが改善ではない。本当の改善は指先の動作にいたるまで効率を上げることである。
「中華丼の具」のラインで、自動袋詰めシール機に具を投入する作業の改善例をあげる。
改善前
中華丼の具の小袋包装では、エビ、イカのような主要な具材がそれぞれの袋に均一に入るように個数管理しなくてはならない。また、野菜のキヌサヤは熱をかけると変色して緑色を損なってしまうため、別に入れなくてはならない。
そのため、改善前はこれらの具を三名の作業者がそれぞれ必要個数だけ投入バケットに入れ、それを機械が袋に充填していた。さらに、袋詰め機には機械のオペレーターが一人ついていた。充填包装機は1分間に三十ショットで回転していた。
ところが、折角必要数量をバケットに入れても、バケットの中に具がくっついて残ってしまったり、投入口からこぼれたりして不良品が発生していた。
その対策として具が離れ易い材質のバケットを探し、バケットそのものの改善も幾度か行ったが効果はなかった。
下図が改善前の作業配置である。

食品工場 改善事例3-改善前
問題点
この作業改善着眼点としては次の項目が採用できる。
①もっと楽に投入出来ないか
1分開に三十ショットで回転する袋の口に必要な具材を投入するのは非常に難しい
(袋がシュートロに来て、開いている時間が非常に短い)。
②個袋の中に直接入れられないか
バケットは具の最終的な行き先ではない。
③各距離が離れていないか
コンテナに入った具を機械の袋の口に入れるにはあまりにも距離が離れている。
④手待ちがないか
それぞれの作業者が2秒に一回ずつそれぞれの具を投入するのは作業量が少なく、手待ちが発生している。
改善後
これらの作業改善着眼点に基づき、次のように具体的な改善を行った。
(1)距離を縮める
袋の中に直接、エビ、イカ、キヌサヤを入れるように、部品(具材)の投入口への距離を縮める。
(2)動作の効率を上げる
動作を腕や肩の動きから手のひら、指先の動きへと、小さな動きで投入できるよう部品置場を投入口の近くに作った。また、作業者の近くに手元スイッチをつけ、袋の供給や部品の供給時には機械を止め、投入者だけで供給作業ができるように工夫し、オペレーターを排除した。

食品工場 改善事例3-改善後
団子流れを連続流しに変える
断続的な”団子流れ”を低速の連続流しに変えることで人減らしができる。
改善前:
改善前の作業(下図)では、四十から五十トレーを1分間に流すため、横ピロー包装機の周囲に、事前に蒸籠から取り出したトレーを積み上げていた。ある程度積み上げると、スイッチを入れ積み上げたトレーが無くなるまで前記のスピードで包装機を運転していた。
このような運転では段ボール箱詰めの作業が忙しく、その場でダンボール箱を立てながら詰めるためには三名の作業員が必要だった。
そのため、事前に段ボールを組み立てていた。包装室内は段ボールの山になっていた。
一方、トレーを包装機に供給する作業員は、準備したトレーを入れ終えると機械を止め、蒸籠から包装機の横にトレーを積み上げ、積み終わってから機械を運転させる断続運転を行っていた。
段ボール箱詰めの作業員は商品の流れが速いため、流れている間は非常に忙しく、取りきれずに箱詰めできない製品を横取りして置いておく。または一名がラップされたトレーを五段ずつ積み上げ横に置き、次の人がこれを段ボール箱に詰め三人目が段ボール箱のシールと段ボー
ル箱作りを行っていた。
トレーを入れる作業員は蒸籠からトーを積み上げ、準備している間に横取りした製品を包装機に流し、次の商品が流れてくるまで手待ちとなっていた。手待ちの間にせっせと段ボール箱を組み立てていた。
この作業では四名の作業員がついていた。

食品工場 改善事例4-改善前
問題点
この作業の改善着眼点として次のようなものがあげられる。
①工程連結は出来ないか
トレーの積み上げ作業は何の価値も生まない。
②作業の難度を下げられないか
本来は製品を段ボール箱に直に入れればいいものを、箱詰め作業の流れが速いため、整理や横取りのような価値を生まない作業が発生する。
③分業が進み過ぎていないか
段ボール詰め作業員が分業のため、一人一人に手渡しと手待ちがある。
④距離を縮められないか
蒸し専用のラ。クと包装機との問の距離が遠く、歩行が発生していた。
⑤手待ちをなくせないか
断続流れのため、段ボール詰め作業員に手待ちが多い。
改善後
改善着眼点に基づき、次の改善をした。
①工程を連結する
事前に積み上げていたトレーを、蒸龍の中から直接横ピロー包装機のヒンガーの中に入れる。
②作業の難度を下げる
トレーの積み上げ作業を無くすために、横ピロー包装機の運転スピードを1分間に二十個程度に落とす。
③分業をやめる
段ボール箱詰め作業員が多人数のため分業になり、それぞれ手待ちが発生していた。一名で包装作業の全てを行うために分業にある手待ちがなくなった。
④距離を縮められないか
横ピロー包装機と、蒸範のラックの位置が離れているために歩行が発生していたので、ラックを置く位置を蒸籠の横に決めた。
⑤手待ちを無くせないか
低速運転で、トレーを入れる者、段ボール箱に詰める者が各一名のため、お互いに助け合って、手待ちのない作業ができる。
改善後の作業は下図のようになる。

食品工場 改善事例4-改善後
トレーを流す作業員は蒸籠を作業者の近くに置き、包装機のスピードを1分あたり二十個程度に落とし、コンスタントな流れとする。
蒸しラックおよび蒸籠の位置は作業員の近くになるようにする。蒸籠は小さな作業台を用意してその上に置くことにより、ピロー包装機の入口との距離も出来るだけ短くする。
段ボール箱詰めの作業者は一箱ごとにテープ貼りの作業が発生するので、トレー投入者は箱詰めの作業をよく見ながら包装の所であふれないように流す。
どの工場に入っても製品の山がよく見れられる。ひどい場合には大きなテーブルを用意し、その上にまで積み上げるようなことを平気で行っている。
準備をして一斉に高速で流すといかにも早く仕事が進んでいるように見えるが、実際は断続運転であり、一方が準備をしている間に他方は手待ちになっている。しかも流れが速いため多くの人手が必要となる。
コンスタットな流れの方が人手と時間が少なくてすむのに、断続でまとめて流したほうが速いと思っている。いわゆる錯覚による開違いである。
離れ小島の解消事例
練り製品の冷却後の段ボール箱詰め作業を例に、離れ小島の解消事例を紹介する。
改善前
二段フリーザーの出口の包装作業は次のようだった。
「製品の流れ」
商品aは1分間十八個の流れで十個を一つの段ボールに詰めていた。段ボール箱の一個の
完成サイクルタイムは33秒である。商品bは段ボール箱が一杯になるのに2分20秒かかる。
「改善前の作業とレイアウト」
改善前は二人で作業していた
〈Aさんの作業〉
段ボール箱を「段ボール立て機」で組立⇒製品を両手で持ちトパック箱に入れる⇒箱に入れたら蓋をしてテーピングマシンに通す⇒三箱作ると「コロコンベア」の所に移動し、製品置場の台車に積み込む、この作業を繰り返す。
〈Bさんの作業〉
段ボール箱を手作業で組み立て、底をテーピングで固定する⇒天秤の上に段ボール箱を置き、製品シュートの蓋をあける⇒製品が一杯になるまで段ボール箱を組み立てながら待つ⇒
所定量になったら段ボール箱を替え、蓋にテープを貼り製品台車に置くにの作業を繰り返す。
問題点
「改善着眼点」
(1)手待ちの解消(AさんBさん共に手作業が多い)。
(2)作業発生点を近づける
(段ボール立て機とテーピングマシンが二人を隔離している)。
(3)無駄な作業を無くす(Aさんが段ボール箱に詰めるとき体を九〇度振ると、共に手の延ばしが大きい。Bさんの作業台が大きく、製品の運搬距離が長い)。
改善後:
「改善後の作業とレイアウト」

食品工場 改善事例5-改善後
①商品a、bを取る位置を同一の場所に変更した。即ち、段ボール箱立て機やテーピングマシンの左側から右側に移動した。
②製品aが手元に集まり、しかも段ボール箱の前にきて動作が楽になるように、点線で示したようにガイドシュートと段ボール立て機の前にコンベアを新設した。
③b製品の作業台が大き過ぎたので点線のような小型の台に変更し、作業の移動距離を減らした。
④改善後の矢印のようにタイミングを合わせて仕事を行い、二名の作業が一名に改善できた。
食品工場 改善事例 まとめ
食品製造業の生産性は、残念ながら主要製造業の中で最も低い。食品工場の生産性を向上させるために、先ず見直していただきたいのは、分業ができているか、標準化ができているか、ライン化ができているかである。
生産性の低い食品工場では、一人完結型の作業が蔓延している。一人完結型のマイペースの作業では、生産性は向上しない。作業分析を行なって作業標準を決めて、目標を定めて生産を行うことにより生産性は向上する。
製造条件によって生産リードタイムの短縮が難しい、フローショツプ型の食品工場では、メイクスパンの短縮により生産性を向上しなければならない。
この時ジョンソン法の考え方は有効であり、生産品目の少ない工場では、大きな成果を上げる
こともできる。
生産品目の多い工場では、正確なスケジュールを作る事が生産性の向上に繋がる。品目が多く、生産のパターンが常に変わる工場では、スケジュールが複雑になるので、ITの活用も必要となるであろう。
IE手法による作業の効率化も重要である。作業の流れが乱流になったり、移動距離が長かったり、手向きが悪かったり、レイアウトが悪いために生産効率が落ちている工場もある。作業のやり方が稚拙な食品工場は案外と多い。これらの改善には余りお金が掛からないものもある。
しかしこれらの問題の解決には、問題の発見能力と問題の改善能力が必要である。日ごろからIE的な発想で工場を観察することが必要である。
もちろん従業員のモラルが低ければ、これらの改善はできないので、社員のモチベーションを上げるように努力が必要であり、社員教育も重要である。作業を見直す時、ラインの整流化、同期化、一機通貫生産など、円滑にラインが稼働しているかどうか、確認の必要がある。頑張る、努力するだけでは生産性は向上しない、生産性向上に必要なものは熱意と同時にIEのような論理的思考である。
量販店などで用いられている、米国で考えられたレイバー・スケジュールに元づく、仕事量と労働量をできるだけ近づけるという考えは、製造業においても生産性を上げるために有効である。
確定した受注により生産する工場では必要労働量を正確に事前に見積もることができるはずである。
ITを活用して生産スケジュールを作成すると、必要な労働力まで算定できるようになる。しかも保存性の有る食品の生産スケジュールには、ある程度の自由度があり自由度の範囲で、生産の順番などを入れ替えることができるので、仕事量の平準化を図ることができる。
工場見える化により、仕事量の平準化をすることにより、労働力を効率良く利用することができる。多品種食品工場において、このような方法を用いて労働量換算で、20%程度の生産性が向上することが確認された。このような努力の積み重ねによって、食品製造業の生産性は向上すると信じる。
いずれにしても生産性が低いということには、原因や理由がある。従って生産性を向上させるにはその原因や理由を取り除かなければならない。次にその原因と思われるものを特性要因図にまとめてみた。

食品工場 生産低下 特性要因図
動画 食品工場 カイゼン事例
改善事例の実写映像から「改善定石」を パワーポイントをフル活用して解説!
*不良検知の自動化
*補助具活用
*食品工場のカイゼンについては下記の文献に色々な活動事例等が更に詳細に記載されています。
参考文献:
金をかけずにすぐできる!食品工場改善入門 小杉 直輝 (著)
食品工場のトヨタ生産方式 弘中 泰雅 (著)
続 食品工場改善入門 小杉 直輝 (著)