具体的レイアウト改善の進め方
工場でのレイアウト改善は、「立地計画」「基本レイアウト」「詳細レイアウト」[設置]の4つの段階に分けられる。4段階のなかで第2段階の基本レイアウトと第3段階の詳細レイアウトでは、SLP(Systematic Layout Planning)システマテック レイアウト プランニング の手順が有効である。
SLPはメイナード研究所のリチャード・ミューサーが開発した、レイアウトの進め方を体系化した手法である。この手法は、工場レイアウト方法の標準というべき手法であり、現在開発されている多くの手法の基礎となるもので、どの工場のレイアウトにも適用できる。
SLPの概略の流れ
下図にその概略の流れを示した。SLPでは、基本レイアウトを作ることと、次に基本レイアウトの詳細レイアウトを作ることが含まれている。この2つの段階は、ともに本質的には同じ手順で行われる。進め方の概略は、つぎのとおりである。
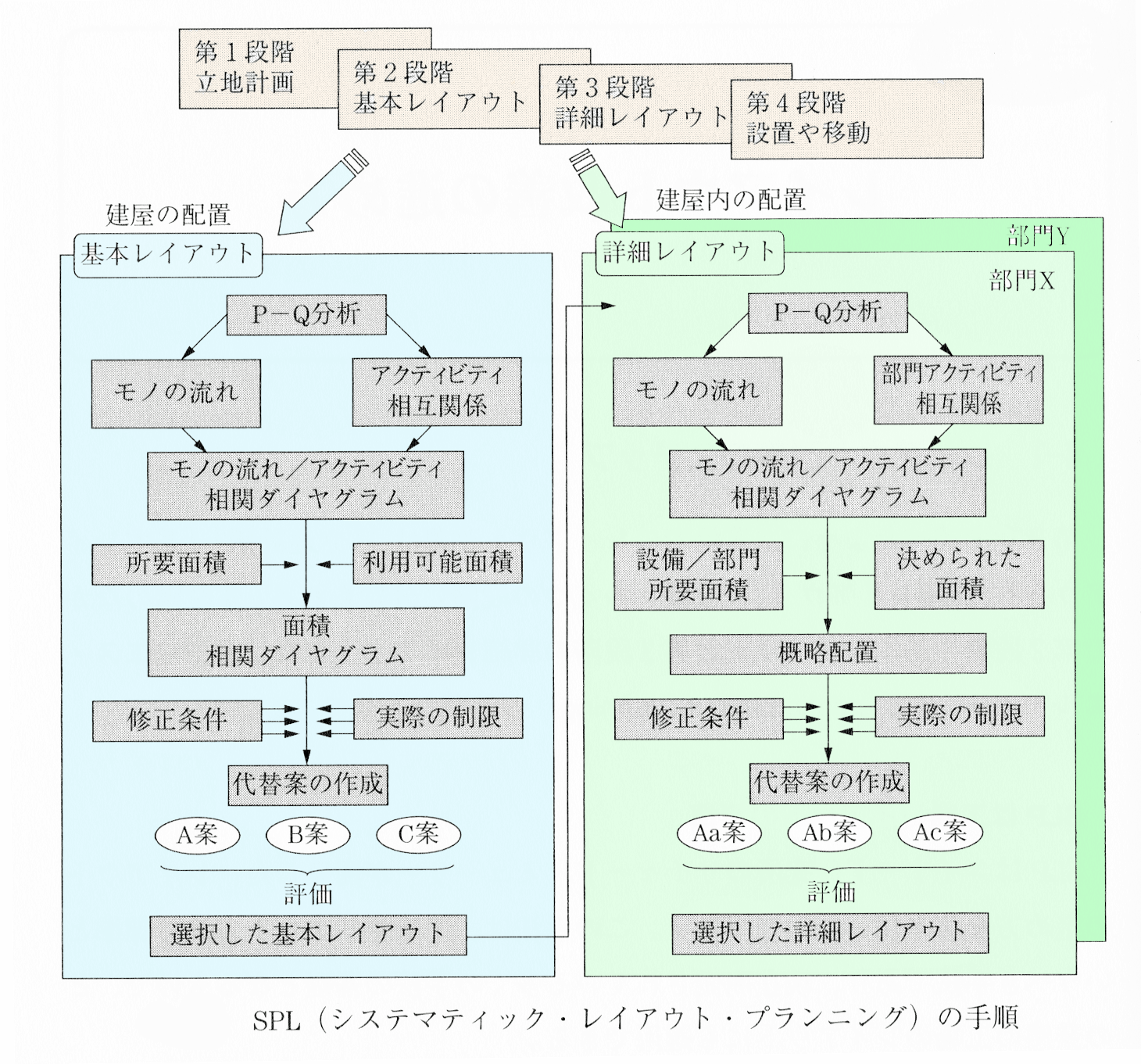
システマテック レイアウト プランニング の手順
①レイアウトの対象となる生産品目(Product)と生産数量(Quantity)関係を分析し、基本的なレイアウトの構想をかためる。
②モノの流れ分析、およびモノの流れと関連をもつアクティビティの分析を行い、各部門間の関連性を検討する。ここでアクティビティとは、レイアウト計画に関連する構成要素(部門、機械設備、倉庫など)の総称である。
③モノの流れやアクティビティの関連性を把握するために、モノの流れ/アクティビティ相関ダイヤグラムを作成し見える化する。そして、アクティビティの必要な面積は考えないで、相互の位置関係を決定する。
④つぎに所要面積である。これは、必要な所要面積と利用可能面積の調整を行い、各アクティビティの面積を決定する。そして、各アクティビティに認められた面積により面積相関ダイヤグラムを作成する。
⑤面積相関ダイヤグラムの作成により、1つの理想的なレイアウトが作成できる。しかし、建屋の特性、運搬方法、作業方法、安全などの現実的な条件や実際の制限があるので、これらの制約条件を考慮して、いくつかのレイアウト案を作成する。
⑥各レイアウト案について、生産性、安全性、コストなど、いろいろな観点より評価し、採用すべきレイアウト案を決定する。第2段階では、これが基本レイアウト(建屋の配置)であり、このレイアウト案をもとに第3段階の詳細レイアウト(建屋内の配置)を検討する。
基本レイアウトと詳細レイアウトの結びつけ
詳細レイアウトでは、基本レイアウト案をもとに各部門や建屋ごとの機械設備、通路、倉庫などの配置を計画する。
手順は基本レイアウトと同様であるが、検討範囲が絞られる。たとえば、モノの流れやアクティビティはレイアウト対象の部門や建屋内の関係である。また、所要面積は機械設備や作業場、倉庫に必要な面積であり、面積相関ダイヤゲラムでは機械設備、人、材料や製品の概略の位置決めをする。
そして、いくつかの詳細レイアウトを作成し、各案を評価して最適な詳細レイアウト案を1つ選ぶ。
PQ分析とは
見込生産の工場や受注生産の工場など工場の特性に応じて合理的なモノの流れを計画することが、レイアウトの中心である。そこで重要になるのが、つぎの力5つの要素P、Q、R、S、Tである。
1.何を作るか:生産品目 :(Product)
2. 個々の品種をどれだけ作るか:生産量(Quantity)
3. どうやって生産するか :経路(Route)
4. 生産を支えるものは何か :サービス(Service)
5. いつ生産すべきか : 時間(Time)
レイアウト計画は、5つの要素のなかの生産品目(Product)と生産量(Quantity)とを正確に把握することから始まる。それは生産品目と生産量の関係が、生産形態やモノの流れに大きな影響を与えるからである。
生産品目と生産量との関係を簡単に把握する方法として、PQ分析を用いる。
PQ分析は、パレート図(Pareto chart)をツールとして生産品目を重要な順にA、B、Cの3つのランクに分ける方法である。
PQ分析の方法
PQ分析は、つぎの手順で行う。
生産品目を分類する
レイアウトを計画する生産品目を分類して、類似品目に分ける。類似品目とは、品目のタイプ、グレード、キャパシティが同一の生産品目グループであり、今後生産する新製品も含めて類似性を分析する。
下図では、品目Aグループから品目Jグループの各々が類似品目である。
生産量を集計する
類似品目ごとに生産量を集計し、生産量の大きい順に並べる。その順に生産量を累計し、総生産量に対する累積構成比(%)を計算する。
データは、過去の傾向と未来将来の予測を加味して集計する。過去のデータは、「製品の季節変動性」「製品構成の変化」を考慮するが、原則として直近の1年間とする。未来将来は、レイアウト計画を実施する時期の生産数量のデータが必要になる。
生産品目のランクを分ける
生産量累積構成比をもとに生産品目をA、B、Cの3つのランクに区分する。
区分は生産量累計構成比の上位から、70~80%をAランク、80~90%をBランク、90~100%をCランクとすることが一般的だが、何%ごとに分けるかは品目群の特性に応じて変えてよい。
表4-1では、類似Aグループと類似Bグループで累計構成比が72.9%になるので、ここまでをAランクとした。つぎに累計構成比が89.5%になる類似Cグループと類似DグループをBランク、それ以外をCランクとした。
パレート図を作成する
横軸に生産品目の種類を、縦軸に生産量をとり、パレート図を作成する。この分析結果をもとに、生産量の多少とモノの流し方やレイアウトの形態を計画する。
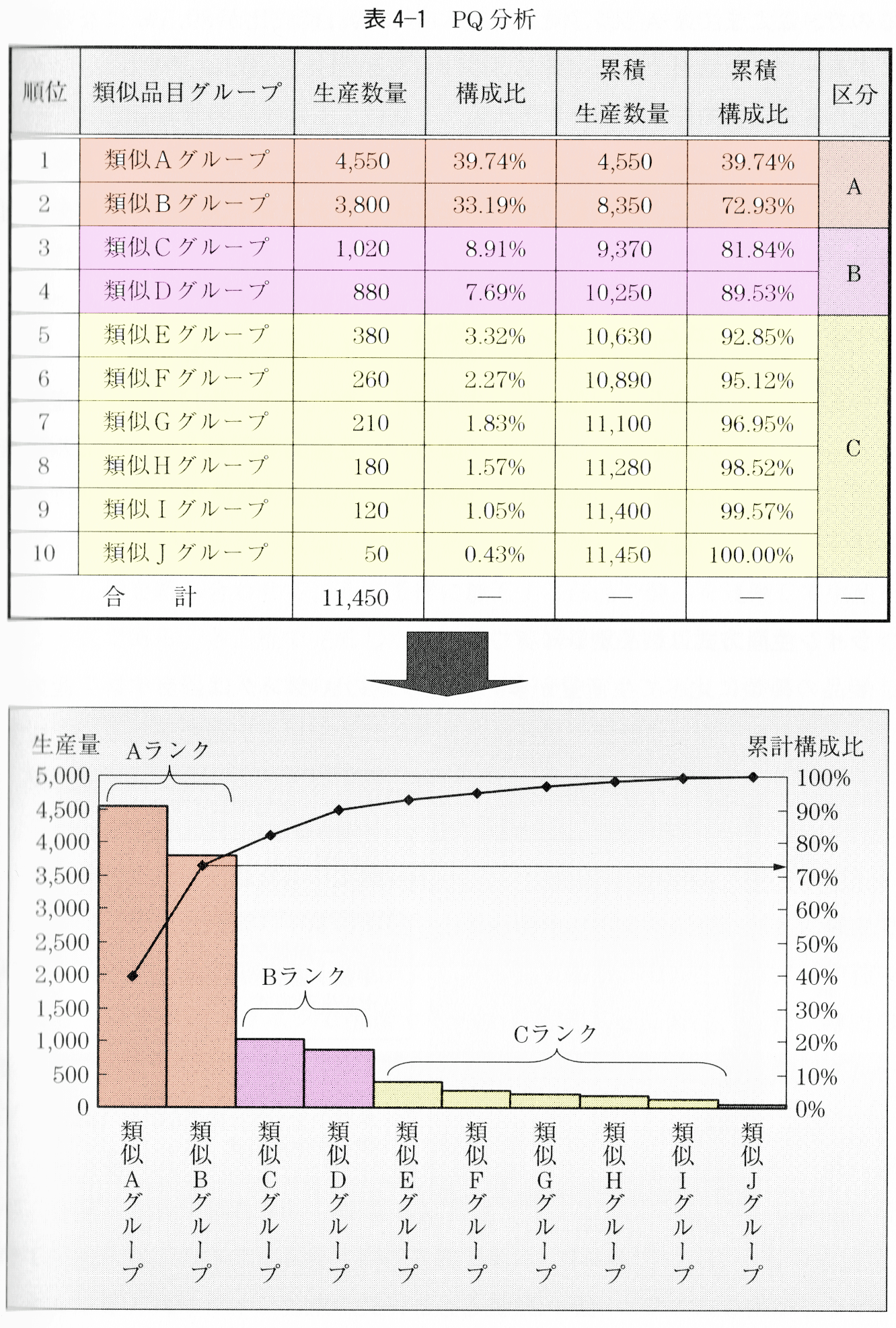
PQ分析
生産方式とレイアウトの関係
生産方式は、生産品目の量から基本的考え方が決まる。生産品目と生産数量によるPQ分析の結果から、Aランクはライン生産方式、Bランクはセル生産方式、Cランクは機能別生産方式に向いている。生産方式とレイアウトの関係を下図に整理してみた。
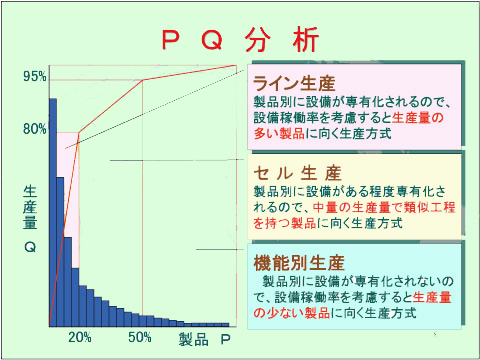
PQ分析-ランク分け
ライン生産方式は製品別レイアウト
製品の種類に比べて生産量が多い少種多量のAランクは、ライン生産方式が向いている。ライン生産方式は、ある期間に同じ部品や製品を大量に作り続けるのに向いている方法で、製造工程に沿って機械設備を配置する。

ライン生産方式2
ベルトコンベアなどにより部品や製品を移動し、流れてきた部品や製品を配置された作業員が加工や組み立てる流れ作業による生産方式である。始まりは、自動車の犬量生産で成功したフォードシステムである。
流れ作業によるライン生産方式は、仕掛が少なく、リードタイムも短い生産方式であり、多くの企業で採用されてきた。
ライン生産方式のレイアウトは、製品別レイアウトになる。
機能別生産方式は機能別レイアウト
生産量に比べて製品の種類が多い多種少量のCランクは、機能別生産が向いている。機能別生産方式は、注文ごとに仕様、納期、数量が異なる製品を、必要な工程を組み合わせて、その工程に加工する部品や製品を運搬して生産を行う方式である。
各工程で完成した仕掛品は容器単位で次工程に運搬されるので、各工程で容器に入る数の仕掛があり、リードタイムも長くかかる。しかし、空いている機械設備に仕事を入れるため機械設備の稼働率は向上する。
機能別生産方式のレイアウトは、機能別レイアウト(ジョブショップ)に適合している。
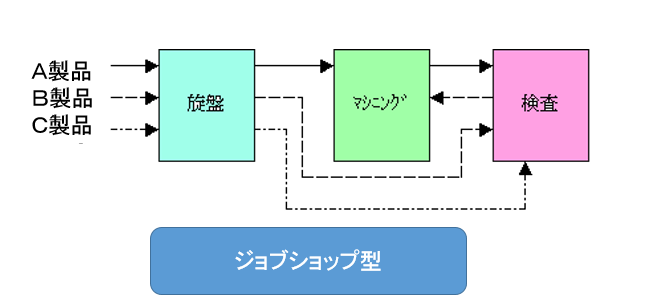
ジョブショップ型-レイアウト
セル生産方式は類似グループ別レイアウト
セル生産方式は両者の中間の形態で、機能別生産のように工程ごとに独立ではなく数工程同期の短いライン形式の生産形態である。セル生産方式は中種中量のBランクを同一ラインで生産するので、品種ごとに製品、工程、時間の変化がでる。そこで、加工工程が類似のものをグループにまとめ、類似グループ別に流れの配置をパターン化する。

セル生産方式2
セル生産方式のレイアウトは、下図のように工程順に設備をU字型に並べ、作業者が各工程を歩行して回るUの字ラインや向かい合わせで製品を分けて生産する二の字ラインなどが代表的である。
セル生産方式はライン生産の長所である仕掛、リードタイムを生かしながら、多品種生産にフレキシブルに対応できるよう設計されている。
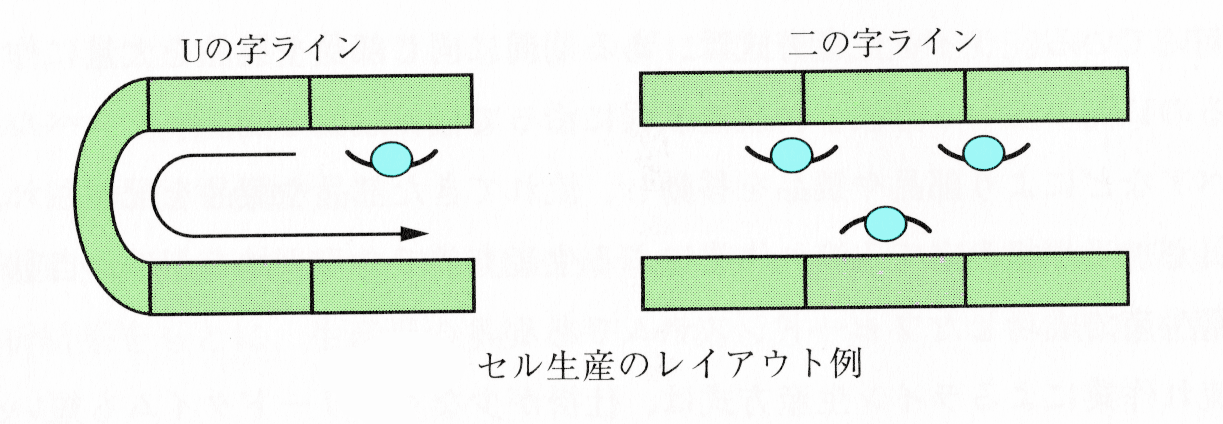
セル生産レイアウト例
モノの流れを「見える化」
P-Q分析につづいて、モノの流れを分析する。モノの流れの分析は、部品や製品を作る工程についての情報を得ることである。モノの流れは工場において建屋、職場、機械設備のレイアウトを決定する際の1つの大きな要因である。
ムダのない流れというのは、モノが工程を通じて次々と移動し、回り道や逆戻りをしないで完成に向かって進むという意味である。
P-Q分析とモノの流れ分析
モノの流れ分析にはいろいろな方法がある。どの方法を用いるかのナビゲーターとして、P-Q分析を利用する。それは、モノの流れ分析は、下図のように製品の量と種類によって異なるからである。
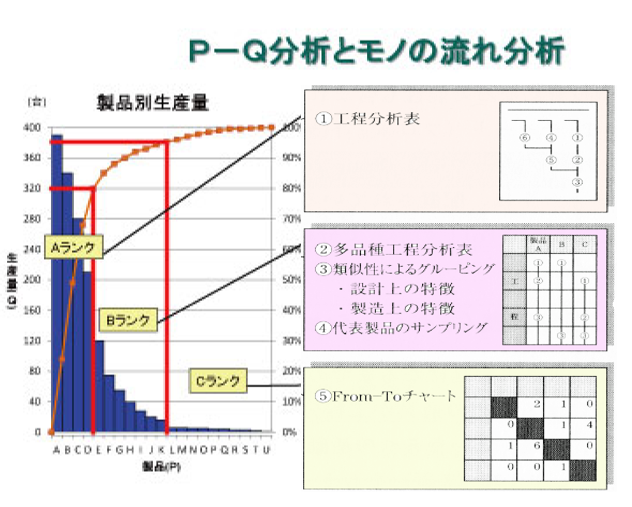
PQ分析-モノの流れ分析
工程分析表(オペレーション・プロセス・チャート)
1つまたはわずかな標準製品のモノの流れ分析には、工程分析表を使用する。
工程分析とは、仕事の過程を図式モデルとして記述し、その論理的・総合的検討を通して、最適のプロセスを求めるための手法である。
関連記事:工程分析表
多品種工程分析表(多品種用オペレーション・プロセス・チャート)
数種類の製品のモノの流れ分析には、多品種工程分析表を使用する。多品種工程分析表は、1枚の分析用紙に数種類の物の流れをまとめて分析するものである。
関連記事:多品種工程分析表
類似性によるグルーピング
数十種類の製品のモノの流れを分析するには、まず対象製品を類似グループに分ける。グループ分けにはつぎの2つの基準が用いられる。
・設計上類似している製品をグループにまとめる
・加工工程上類似している製品をグループにまとめる
代表製品のサンプリング
代表製品をサンプリングにより抽出し、工程分析表や多品種工程分析表を作成する方法も実務的である。ただ、代表製品が少ないと誤差が発生することがあるので、サンプル数は10~20製品程度選ぶのが一般的である。
また、もっとも条件の悪い製品、たとえば「もっとも重い」「もっとも長い」「もっとも弱い」「もっとも工程数が多い」などを代表に選ぶことも多い。これは、もっとも悪い条件を考慮すれば、通常の製品では問題ないという発想である、しかし過剰投資になる可能性も含まれていることを忘れてはならない。
From-Toチャート(フロム・トゥー・チャート)
PQ分析のCグループは、From-Toチャートでモノの流れを分析する。
From-Toチャートは、配置されている機械設備間の製品の流れを「どこから(From)」「どこへ(To)」の形式で分析する手法である。
関連記事:From-Toチャート
工程分析表(オペレーション・プロセス・チャート)の作り方
原材料が投入され製品になるまでのモノの流れを図式モデルとして記述し、見えるようにするための道具が工程分析である。モノの流れは、「加工、検査、運搬、停滞、貯蔵」という5つの活動に分類できる。
工程分析表(オペレーション・プロセス・チャート)とは
工程分析表とは、原材料、部品が工程に投入される点およびすべての作業と検査の流れを表現した表のことである。モノの流れ全体をひと目で把握できる特徴をもっているので、レイアウト計画以外にも、「工場全体の概要を把握したい」[現場改善の重要部分を見つけたい]などの目的にも用いられる。
工程分析では、モノの流れを下図の記号で表現する。
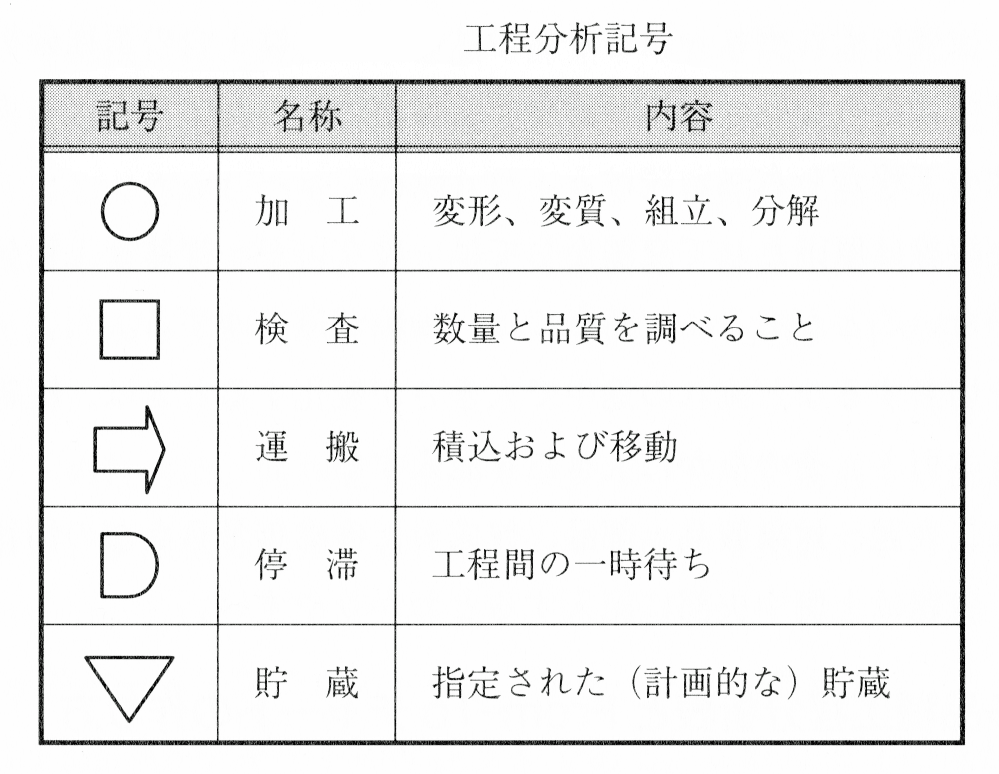
工程分析記号
工程分析表(オペレーション・プロセス・チャート)の作り方とルール
1.下表のように加工や検査などモノが流れる順序は、工程分析記号を流れの順に縦方向に並べ、縦線で結ぶ。材料や加工部品の供給は、横線を縦線に連結することにより表す。図表化にあたっては、工程数のもっとも多い部品を選定し、工程分析表の上右端から記人すると見た目がきれいになる。
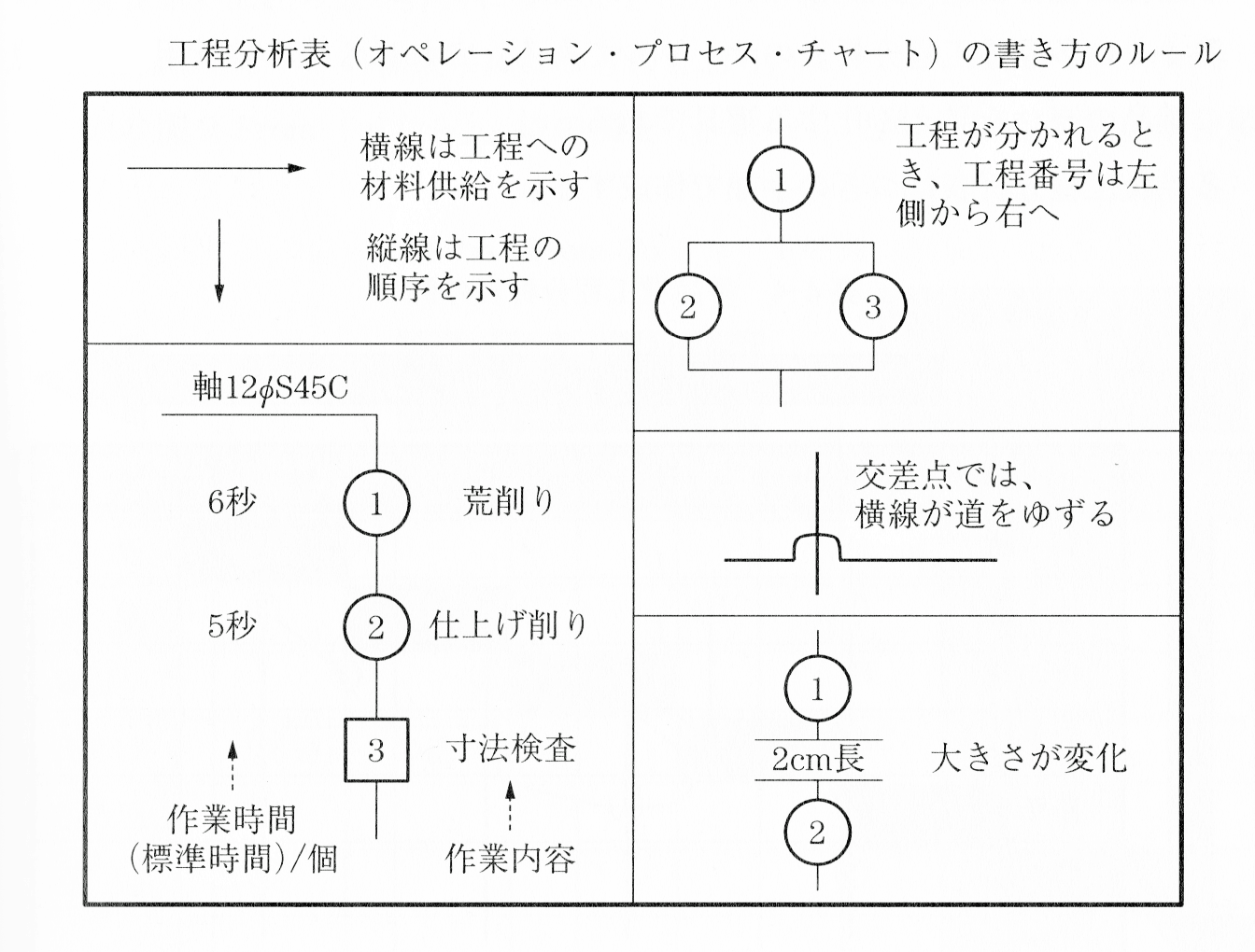
工程分析表の書き方
2.材料供給を示す横線の上に、対象部品の原材料名を記入する。
3.材料供給線の右端から垂直に縦線を引き、最初の工程記号を記入する。工程記号の右側には、作業内容を簡潔に記入する。また、左側には作業時間(標準時間)/個を記入する。
4.加工、検査にそれぞれ一連番号をつける。番号は1つの工程分析表のなかで重複させてはならない。加工の途中で工程がいくつかに分かれる場合、工程番号は左側の工程から右へと続ける。
5.横線と縦線は原則として交差をしてはいけないが、複雑な工程分析表になるとさけがたいことがある。交差点では、横線が道をゆずる。
6.棒材を切断するなど流れの途中で大きさが変化するときは、縦線の途中に水平線を2本引き、そのなかに大きさを記入する。
7.最後に、表題、対象製品・部品、作成者、作成年月日などの情報を余白に記入する。表題は上側中央部に記入するとわかりやすい。
多品種工程分析表とFrom-Toチャートの作り方
多品種工程分析表(多品種用オペレーション・プロセス・チャート)の作り方
下図は多品種工程分析表のサンプルである。これは1枚の分析用紙で数種類の製品の流れを見える化する道具である。
多品種工程分析表はつぎの手順で作成する。
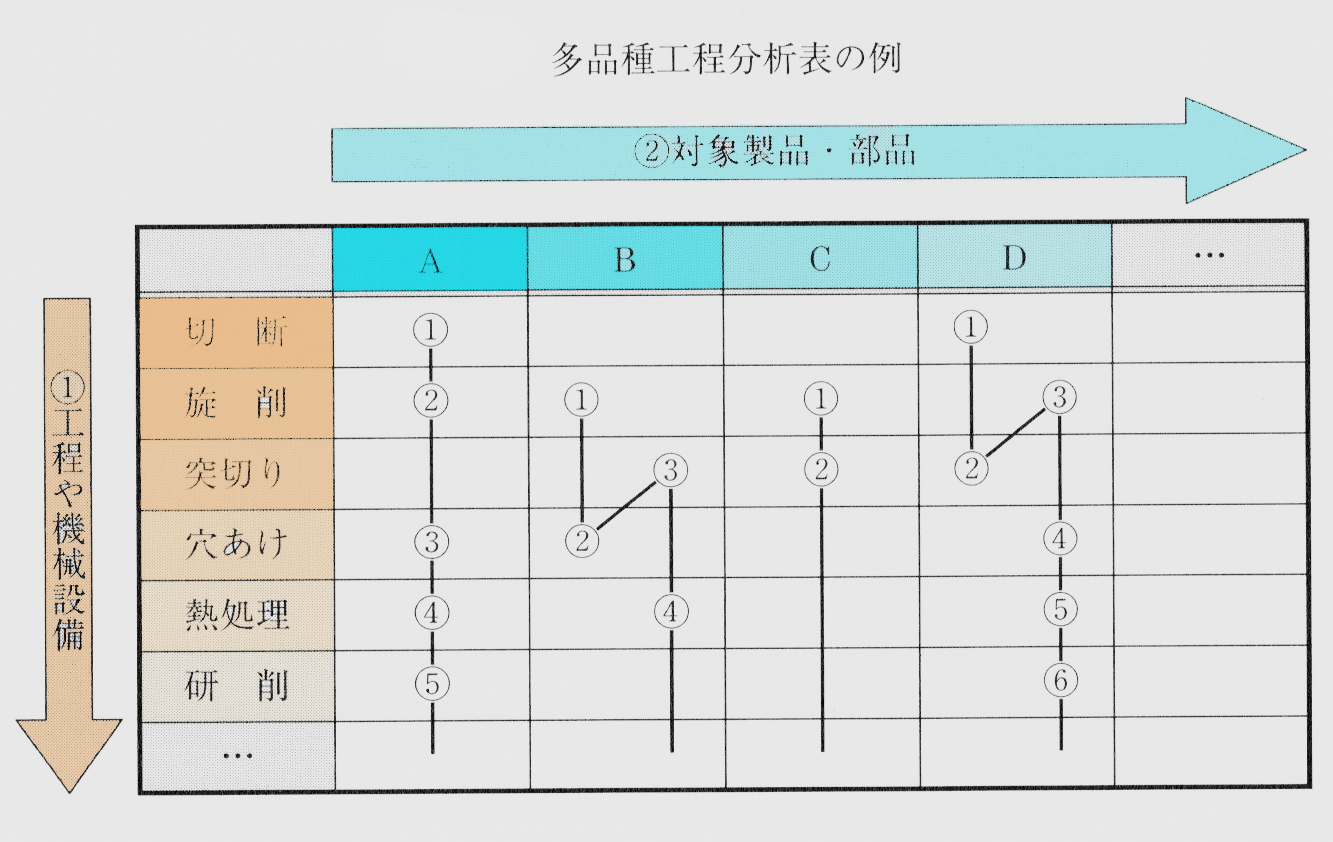
多品種工程分析表の例
①分析表の左側に分析対象の製品や部品が流れる工程や機械設備を記入する。
②分析表の上段には、分析対象製品や部品をそれぞれの欄に記入する。
③分析対象ごとに流れの順番に一連番号がついた記号(○)を記入する。
このようにして作成したモノの流れによって、製品や部品ごとにそれぞれの流れを比較することができる。
上図で対象製品・部品の流れを比較すると、Bでは「穴あけから突切りへ」、Dでは「突切りから旋削へ」の戻りが発生している。
レイアウトの目的は、回り道や逆戻りの少ないものが前進する流れを決めることであるが、多品種工程分析表によりムダな流れを把握できる。
From-Toチャート(フロム・トウー・チャート)の作り方
下図はFrom-Toチャートのサンプルである。これはモノの流れを分析する対象製品や部品の数が非常に多いときに用いる道具である。
From-Toチャートの作成手順はつぎのとおり。
①縦の欄をFrom(~から)、横の欄をTo(~へ)として製品や部品が流れる工程や機械設備を同じ順序で記入する。
②各工程や機械設備間を移動する回数を縦の欄と横の欄が交差する欄に記入する。下図は、上図「多品種工程分析表の例」の多品種工程分析表のデータを記入したものである。

From-Toチャートの例
たとえば対象製品・部品のAは、「切断から旋削」に移動するので、切断と旋削が交差する欄にAと記入する。つぎにAは、「旋削から穴あけ」に移動するので、旋削と穴あけが交差する欄に再びAと記入する。以下同じように、対象製品・部品を記入する。
③全対象製品・部品の記入が終了したら、交差する欄ごとに文字を合計して、数字を記入する。この数字が大きいほど、流れの関係が強いので近くに配置した方が効率的な配置となる。また、逆戻りの流れはFrom-Toチャートの対角線の下部に現れるので、レイアウトでは注意が必要である。
アクティビテイの相互関連を評価
工場でのレイアウト計画では、モノの流れを考慮する以外に、部門、機械設備、倉庫などアクティビティの関連性が重要な要素になる。近くに配置したほうがよいアクティビティ、離れても問題がないアクティビティなどアクティビティの関連性を評価し、レイアウトを作成する。このアクティビティ間の評価を行う道具が相互関係図表である。
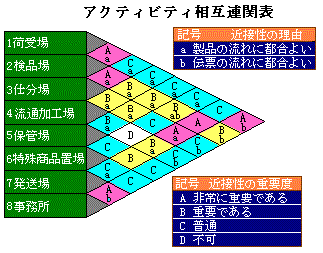
アクティビティ相互関連表
相互関係図表の作り方
相互関係図表は、下図のようなアクティビティの相互関係が記録できる交差型の図表で、つぎの手順で作成する。
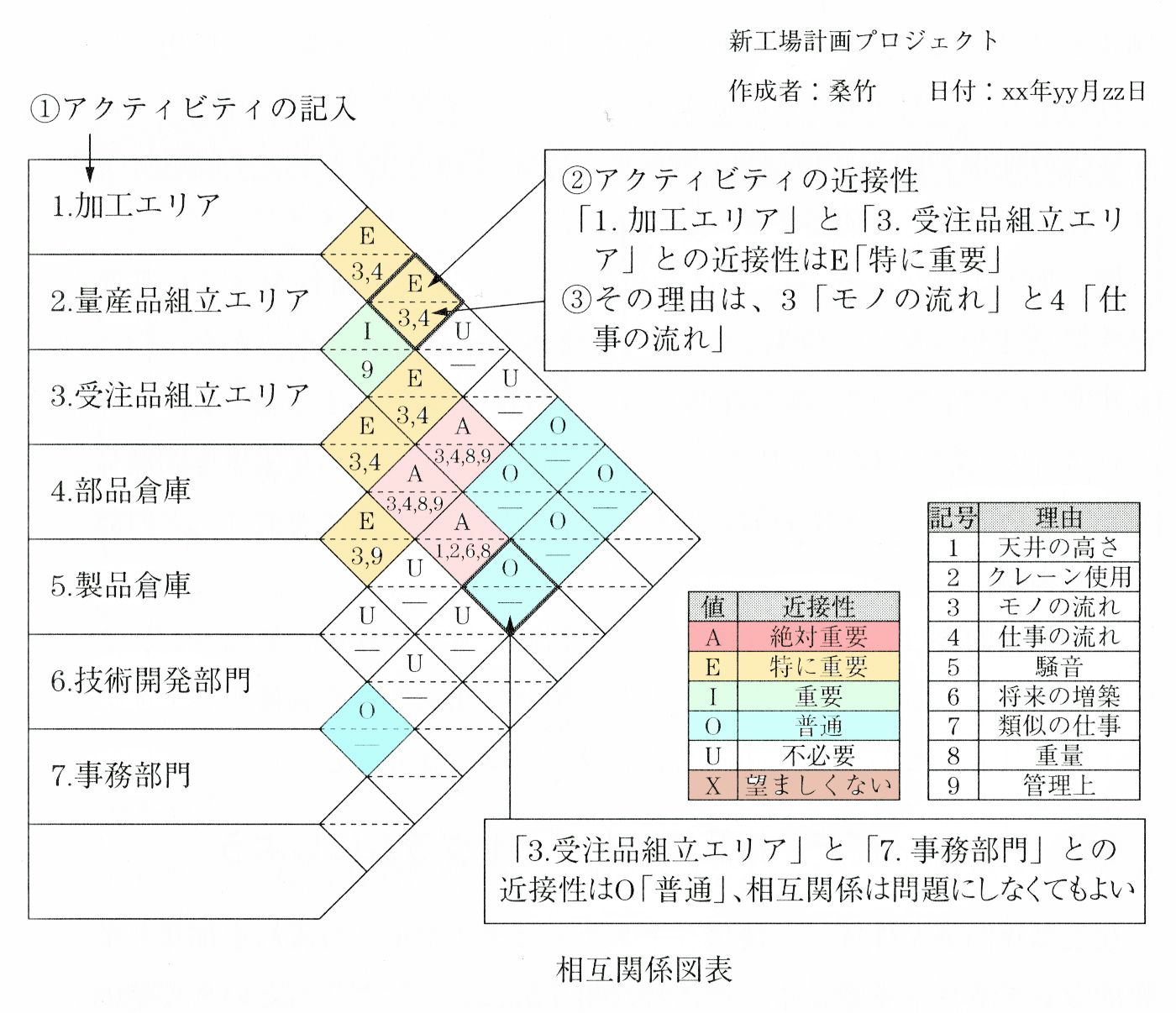
相互関係表
①レイアウトに関係するアクティビティを確認し、相互関連図表の左側に記入する。上図は、建屋の配置を検討する基本レイアウト段階で、「1.加エエリア」から「7.事務部門」まで7つのアクティビティがある。
②アクティビティどうしの近接性評価を、ひし形ブロックの上半分に記入する。たとえば、「1.加エエリア」と「3.受注品組立エリア」との関係は、1からの斜め下の線と、3からの斜め上の線の交わったブロックのなかに記入する。同じように、「3.受注品組立エリア」と「7.事務部門」との関係は、3の斜め下の線と7の斜め上の線の交わったブロックのなかに記入する。
ブロックのなかで使っている記号は、近接性の度合いをコードと色で表している。
A…Absolute(絶対必要)・‥赤 E…Especially(とくに重要)…黄
I…Important(重要)…緑 O…Ordinary(普通)…青
U…Unimportant(不必要) X…(望ましくない)…茶
「1.加エエリア」と「3.受注品組立エリア」との近接性はEなのでとくに重要、「3.受注品組立エリア」と「7.事務部門」とはOなので普通である。
③評価を行ったブロック(ひし形)の下半分にその理由をコードで記入する。
上図相互関係表では、理由コードの1が「天井の高さ」、2が[クレーン使用]で9つ
の理由がある。相互関係の評価項目としては、「連絡や事務上の流れ」「同じ機械設備の使用」「同一担当者」「混乱や干渉」「環境」などをよく使用するが、さらに多くの項目を使ってもよい。
「1.加エエリア」と「3.受注品組立エリア」との近接性をとくに重要と評価する理由は、3「モノの流れ」と4「仕事の流れ」である。また、「3.受注品組立エリア」と「7.事務部門」の下半分はダッシュ(-)になっている。
これは「3.受注品組立エリア」と「7.事務部門」との相互関係を問題にしなくてもよいことを示している。また、Uと評価したときは理由コードの記入は不要である。
相互関係図表は、なるべく多くの人の判断をもって評価するほうが、より良い結果が得られる。また、レイアウト計画では相互関係を見落としやすいので、チェックリストとして相互関係図表を役立てることもできる。
アクティビティ相互関連をダイヤグラムに
相互関係図表を作成した後は、アクティビティやモノの流れを加味して、理想的なレイアウトを考える。そこで、相互関係ダイヤグラムという理想的な配置を実現するための便利な道具を紹介。

相互関係ダイヤグラム
相互関係ダイヤグラムの作り方
相互関係ダイヤグラムは、相互関係図表に出てきた近接性評価を図式化し理想的配置に変換するものである。下表は、SLPで標準的に定めている相互関係ダイヤグラム作成のルールである。アクティビティを表す記号と色、近接性を表す線の本数と色が規定されているので、これにもとづくことが大切である。

相互関係図表-ダイヤグラム 作成ルール
相互関係ダイヤグラムは、つぎのような手順で作成する。
①最初に評価値が「絶対重要なA」の関係のアクティビティを選び、なるべく近くに配置する。下図の相互関係図表では、「2.量産品組立エリア」と「5.製品倉庫」、「3.受注品組立エリア」と「5.製品倉庫」、「3.受注品組立エリア」と「6.技術開発部門」がAの関係である。これらの関係を4本の直線で表す。
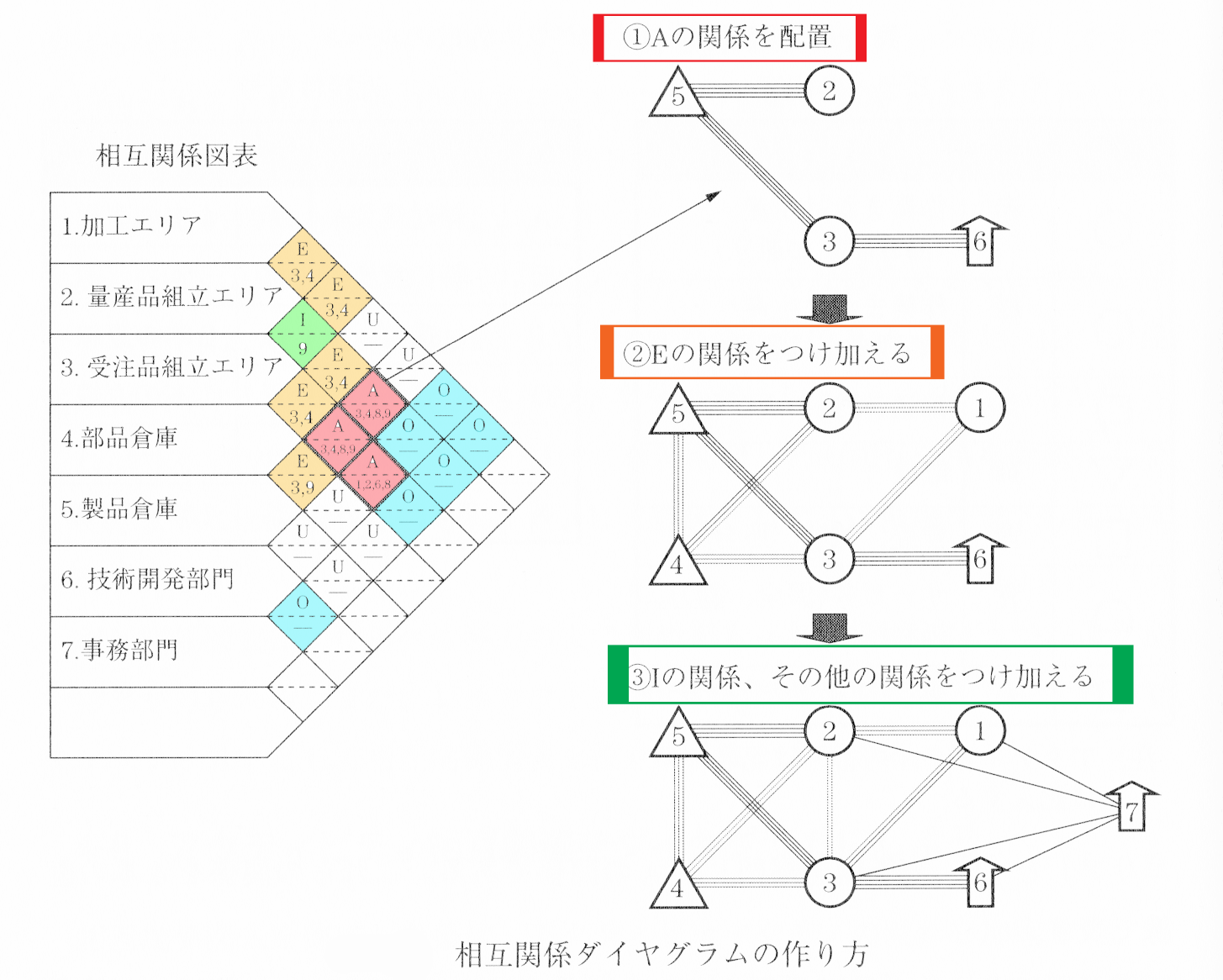
相互関係ダイヤグラムの作成
②つぎにとくに「特に重要なE」の関係のアクテイビテイを選びAの結果につけ加える。このときAの結果が位置的に修正されることがある。Eの関係にあるアクテイビテイは、「1.加エエリア」と「2.量産品組立エリア」、「1.加工エリア」と「3.受注品組立エリア」、「2.量産品組立エリア」と「4.部品倉庫」、「3.受注品組立エリア」と「4.部品倉庫」、「4.部品倉庫庫」と「5.製品倉庫」である。これらの関係を3本の直線で表す。
③A、Eの位置関係を修正しながら「重要なI」の関係があるものを付け加える。Iの関係は、「2.量産品組立エリア」と「3.受注品組立エリア」なので、これらの関係を2本の直線で表す。
④以下同じように、「普通のO」「不必要なU」「望ましくないX」の関係があるものを順次付け加えていき、線の数が多いものができるだけ近くに配置されるように試行錯誤を繰り返す。
⑤アクティビティの1つだけが非常に多くのアクティビティと関連を持つときにはアクティビティを細分化することがある。
⑥この相互関係ダイヤグラム作成の段階では現実の制約を考えてはいけない。
この段階ではあくまでも理論的に最適なアクティビティの位置関係(あるべき姿)を求め、後で制約および修正条件を考慮しながら関連線図の修正を行う。
レイアウト 必要な面積を求める
相互関係ダイヤグラムで関連する工程やアクティビティの配置関係は決定したので、つぎの段階では工程やアクティビティの面積を決定する。
面積を決定するには、量的な要素ばかりでなく質的な要素も必要になってくる。質的な要素とは、各工程やアクティビティが必要とする物理的な特性である。この物理的な特性とは、建物の構造上配慮しなければならない「梁下」「床荷重」「天井高さ」などで、これらはレイアウト計画の中に組み込まなければならない。
面積の決定には、下表に示すスペース計算シートという道具を用いる。
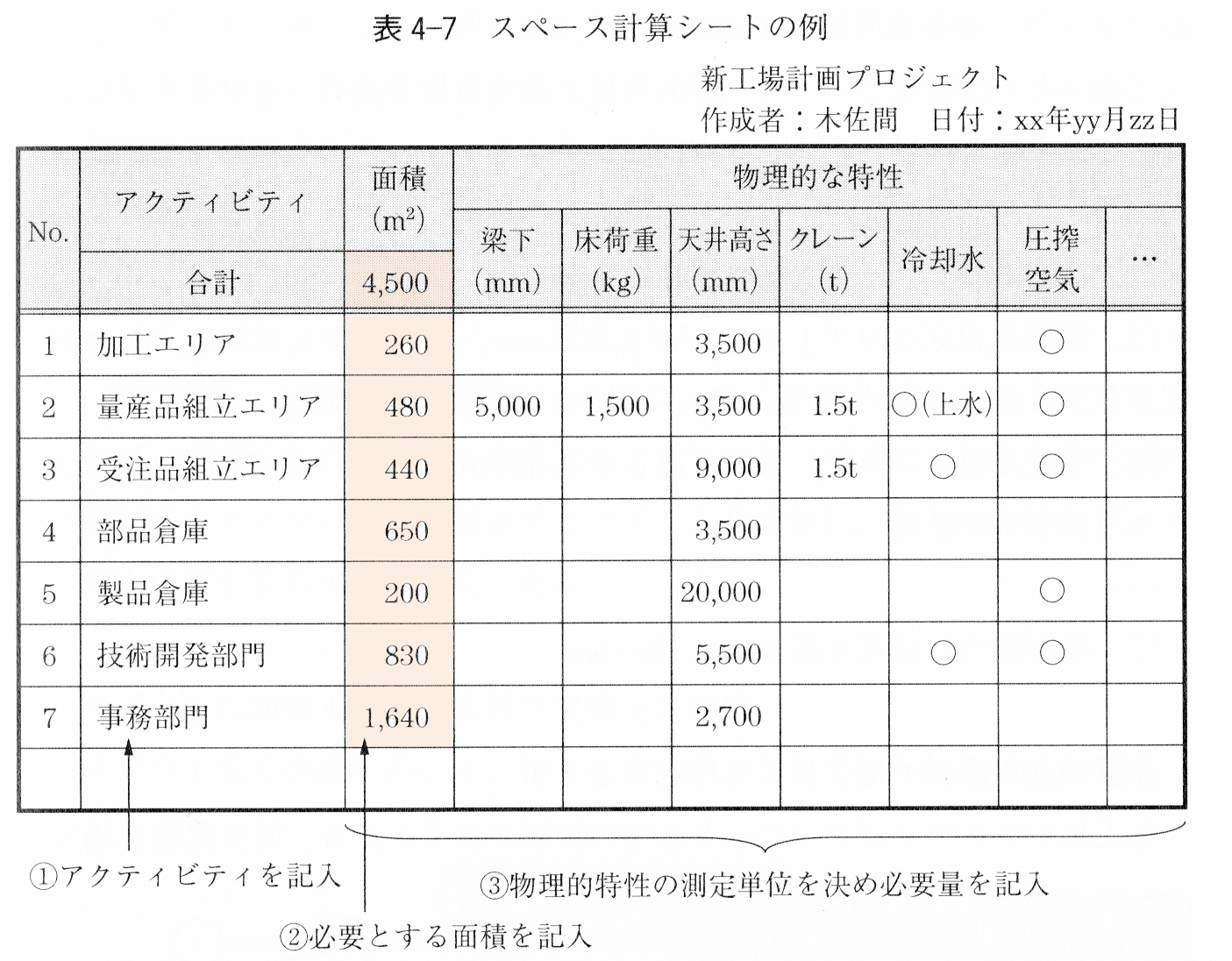
スペース計算シートの例
スペース計算シートの作り方
①スペース計算シートの左側に各アクティビティを記入する。その場合、相互関係図表と同じ順番で記入し、アクティビティ名も同じものを使うようにする。上表では、図 相互関係図と同じ「1.加エエリア」から「7.事務部門」まで7つのアクティビティを記入した。
②各アクティビティが必要とする面積を記入する。上表の各アクティビティの必要面積は、「1.加エエリア」は260 ㎡、「2.量産品組立エリア」は480 ㎡、…、[7.事務部門]は1,640 ㎡と見積もっている。
③梁下とか床荷重といった物理的特性の測定単位を決め、各アクティビティの必要量を記入する。上表では、アクティビティごとにつぎのように検討した。
・「1.加エエリア」は天井高さが3,500 mm
・「2.量産品組立エリア」は梁下が5,000mm、床荷重が1,500 kg、天井高さが3,500mm、クレーンは1.5t、冷却水と圧搾空気が必要
・「3.受注品組立エリア」は天井高さが9,000 mm、クレーンは1.5t、冷却水と圧搾空気が必要
・「7.事務部門」は天井高さが2,700mm
面積相互関係ダイヤグラムを作成する
各工程やアクティビティの必要面積の検討が終了したら、所要面積を相互関係ダイヤグラムに適用して、下図の下部の面積相互関係ダイヤグラムを作成する。作り方は「アクティビティ相互関連をダイヤグラムにしよう」と同様の進め方をする。このようにして作成した面積相互関係ダイヤグラムは、事実上のレイアウトである。
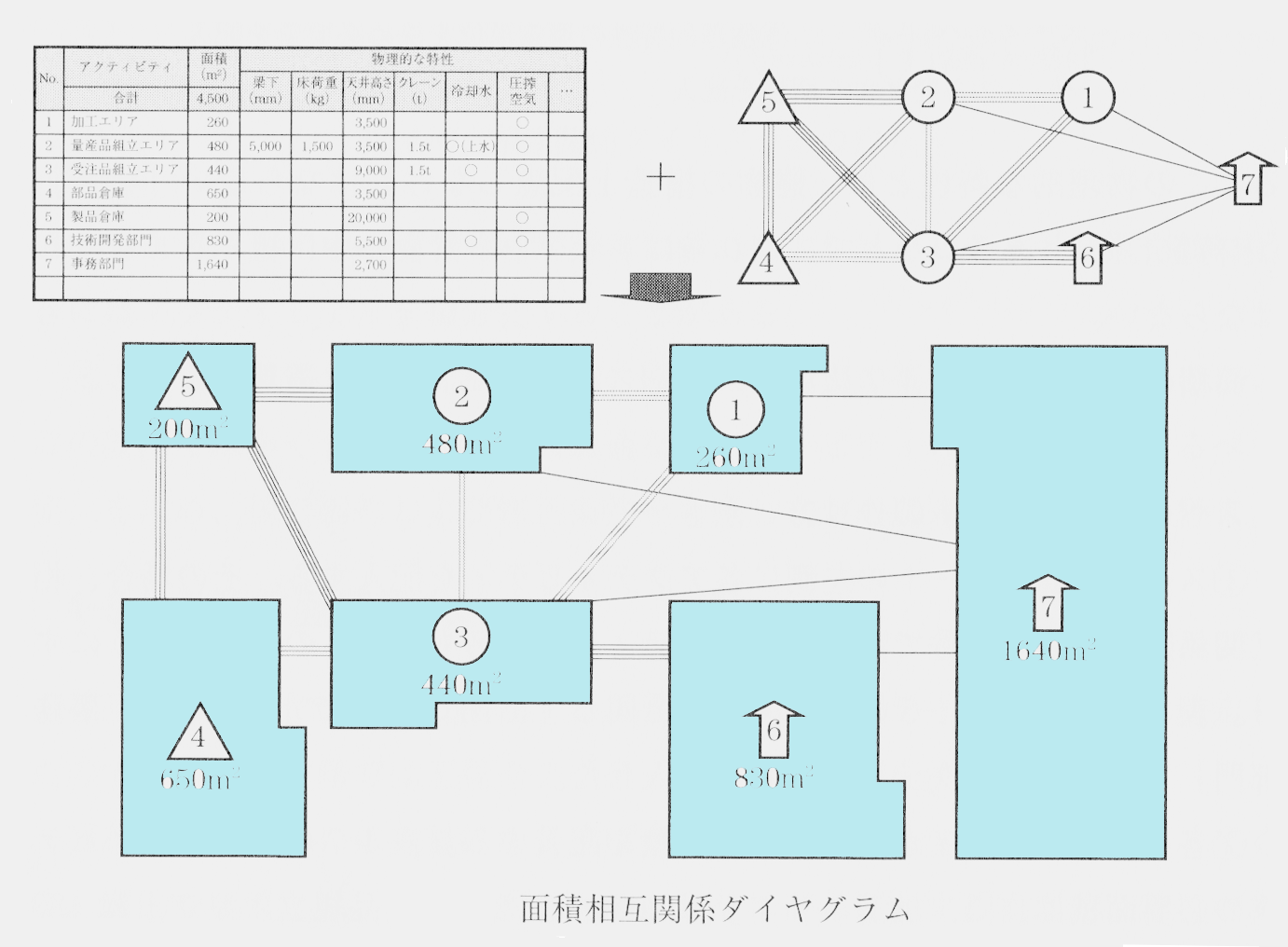
面積相互関係ダイヤグラム
レイアウト案を作成
作成した面積相互関係ダイヤグラムは、理想的なあるべき姿の配置であるが、実現するには多くの修正点を含んでいる。そこで、修正条件や制約条件を加昧してスペース相関関係ダイヤグラムを調整し、より実際的なレイアウト案を作成するのがこの段階である。
レイアウトに加味する修正条件や実際上の制約
レイアウト案を作成するには、図4-8に示すような手順と修正条件や実際上の制限について検討を加えることになる。修正条件が努力目標であるのに対して、実際上の制限は必ず満たさなければレイアウト案が実行可能とならない制約条件である。
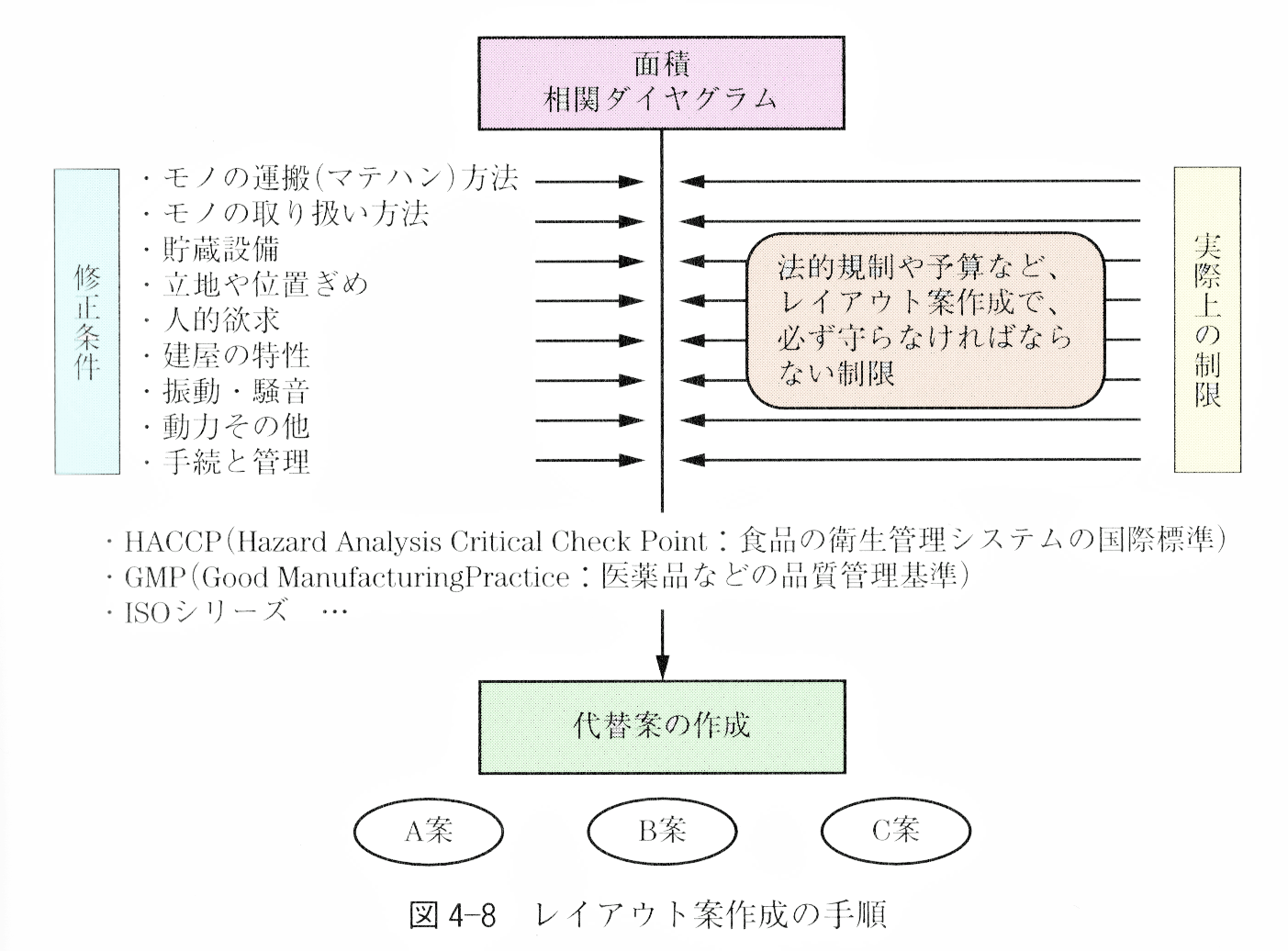
レイアウト作成の手順
上図にある修正条件は、一般的なものである。それぞれのレイアウトでは独自の修正条件があり、さらにそれらには重要度の違いがある。たとえば、ストノクヤードや倉庫のレイアウトでは、モノの運搬(マテハン)方法や貯蔵設備の選択、モノの取り扱い方法によって配置を変えることになる。しかし、事務所のレイアウトで重要な修正条件は、手続きと管理や人的欲求であり、モノの運搬(マテハン)方法や貯蔵設備などの重要度は低い。
また、業種によっては国際規格や標準的な管理手法がレイアウトの修正条件になる。たとえば、食品工場ではHACCP(Hazard Analysis and Critical Control Point)という食品工場の全工程で発生しうる危害を防止するための衛生管理手法がある。 HACCPは1960年代に米国で宇宙食の安全性を確保するために開発され、我が国では1995年に食品衛生法の一部を改正し導入された。レイアウトに影響する項目として、下図に示すような規定がある。これらの規定は、モノの流れの効率化とトレードオフの関係になることが多い。

HACCPの規定
食品工場以外でも医薬品工場のGMP(Good Manufacturing Practice :医薬品等の品質管理基準)などが考慮すべき基準の例である。
このように、会社内での修正条件や業界での条件を加味し、必ず守らなければならない実際上の制限を考慮して、下図のように面積相関関係ダイヤグラムから実行可能なレイアウト代替案を作成する。
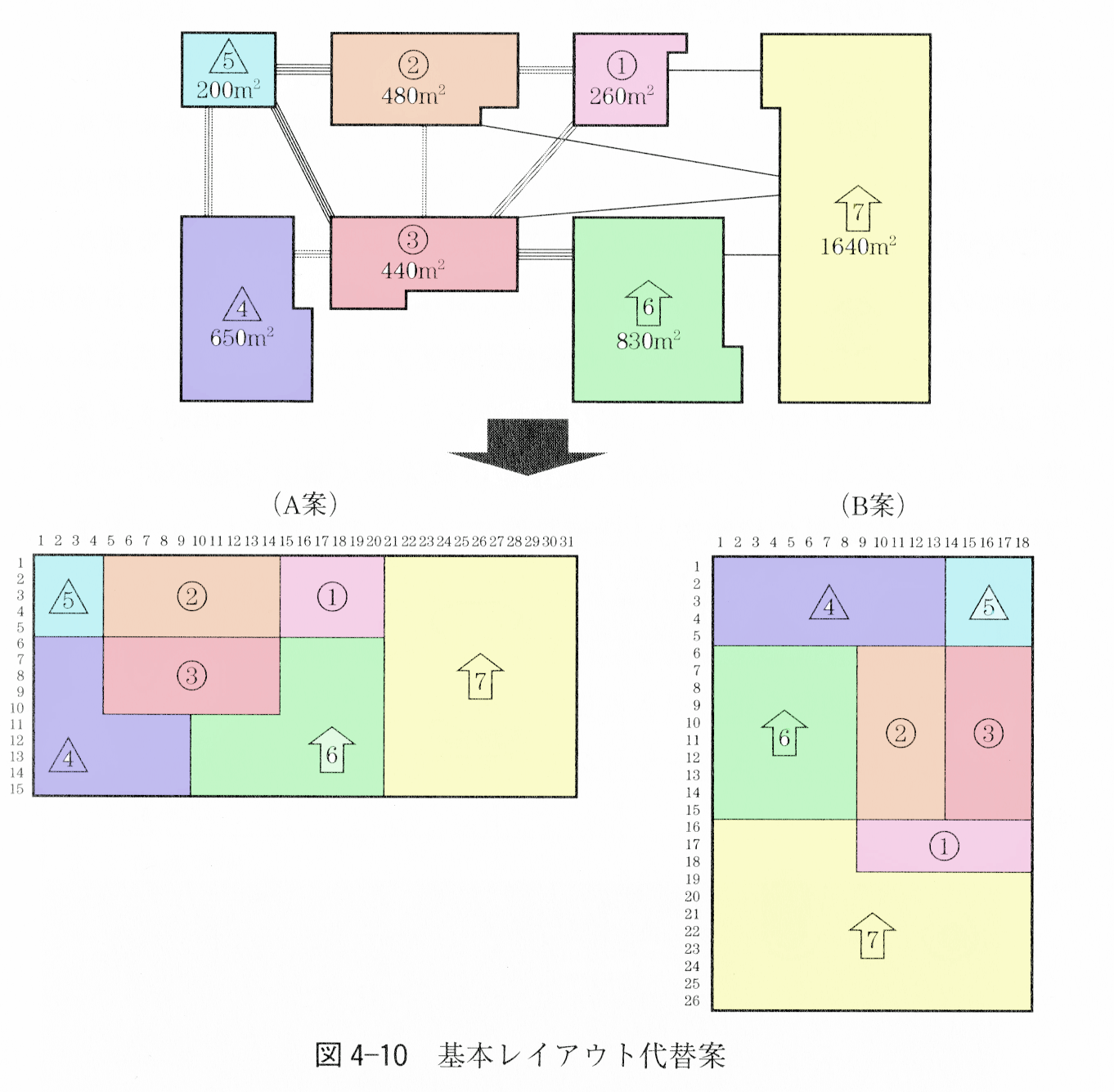
基本レイアウト代替え案
レイアウト案を評価
いくつかのレイアウト案を作成したので、つぎの段階はそれらの評価である。
代替案の中からよりよい代替案を選択するには、評価基準が必要になる。評価基準には、在庫量やリードタイムなど定量的な評価項目と満足感や容易性などの定性的な評価項目がある。
レイアウトの評価方法と評価基準
コンピュータシミユレーション法
シミユレーションソフトを利用し、コンピユータ上で仮想工場モデルを作り動かしてみる。
下図は、シミユレーションソフトウェアで仮想工場モデルを動かしている画面の例である。
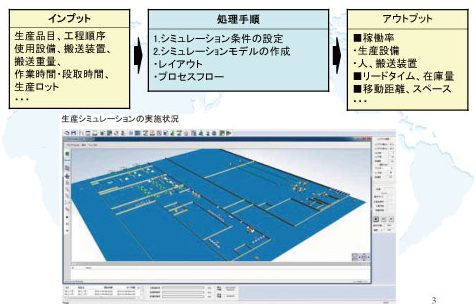
工場レイアウト ソフト
これらのソフトウェアでは、ライン生産方式による製品別レイアウト、機能別生産方式による機能別レイアウトなどで材料投人から製品が完成するまでのモノの流れ、人の動きをシミユレートして確認する機能が提供される。シミユレーションソフトウェアによっては、定量的データとして「作業員数や作業員の稼慟率」「機械設備やラインの稼働率」「リードタイムや
リードタイムのばらつき」「在庫量の推移」などの解析が可能である。レイアウト案の定量的な評価ができるだけでなく、工場を稼働させる前に今後発生する可能性のある問題を把握できる長所もある。
短所としては、シミユレーションモデルの構築にお金と時間がかかる点がある。
参考サイト:FactoryCAD
短時間で3次元の工場レイアウトを作成するツールです。
原価比較法
工場建設に要する建設費、運搬機器・設備費、据付費、機械設備費といったイニシャルコストを比較する。
運搬費比較法
ランニングコストの中で大きな比率を占める運搬費を比較する。建設費や機械設備費などのイニシャルコストは、金額は大きくても長い間使っていくものとすれば小さくなると考え、代替案ごとにつぎの計算をし、最も小さい案を採用する。
運搬費=(職場間の距離×職場間の運搬量)の総計
生産性比較法
製品1個あたりの工数、リードタイムを比較する。
面積比較法
1㎡あたりの原価や利益がどのくらいかを計算し比較する。
要素比較法
下図のような定量的と定性的な評価要素をあげ、その重要度によってウェイトをつける。そして代替案ごとに点数法(O~4の数値)などにより評価し、評価値にウェイトを掛け算した値を計算し最大のものを選ぶ。
レイアウト案を評価し基本レイアウト(建屋の配置)を決定し、ついで各部門における詳細レイアウト(建屋内の配置)を作成する。その手順は基本レイアウトで述べたものとほぼ同じである。
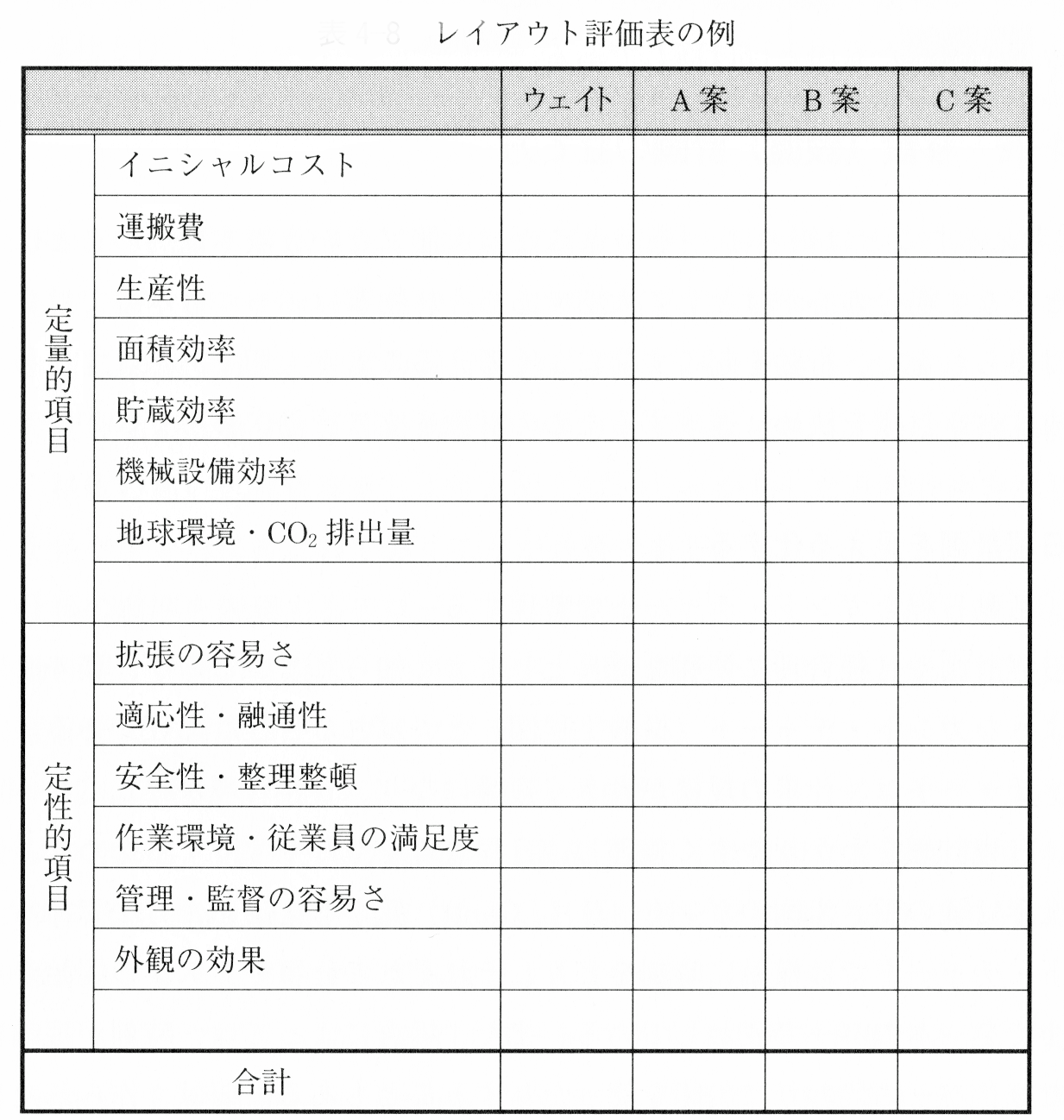
レイアウト評価表の例
移設(設置)計画の立て方
「考える」ことは細心に、「行う」ことは大胆にという坂本龍馬のことばは、ことをなす場合の心がけとして大切であろう。物事はぶっつけ本番ではよい結果は得られない。行動を起こす前によく考えることが大切である。すなわち、達成すべき目標を決め、達成するための計画を立て行動に移ろう。
日程計画を見える化する
①活動日程をガント・チャートで整理する
日程計画や日程管理に便利な道具としてよく知られているのが、下図に示すようなガント・チャート(横線工程図)とよばれる日程計画表である。ガント・チャートは、仕事の規模が大きく複雑になり、日程管理が難しくなったため、日程計画をわかりやすく整理し、日程管理をやりやすくするために、第一次世界対戦の頃、米国のガント(H.L.Gantt)氏が考え出した方法である。
ガント・チャートでは横軸に時刻をとり、それぞれの仕事やタスクの開始から終了までを一本のバーで表わしている。また、場合によっては、時刻が縦軸になったり、バーの代わりに矢印を使ったりすることもある。要は、作られた日程計画がわかりやすく表示されており、日程計画がやりやすくなっていればよいのである。ガント・チャートを使って日程管理をする場合には、ガント・チャートを壁に貼っておき、作業の進行状態によってバーを塗りつぶす。
日程管理をする場合、日程計画がはっきりしていなければ十分な管理は行えない。精度の高い日程管理をしようと思えば、しっかりした日程計画を作り、これを見やすい形にまとめておくことが必要である。
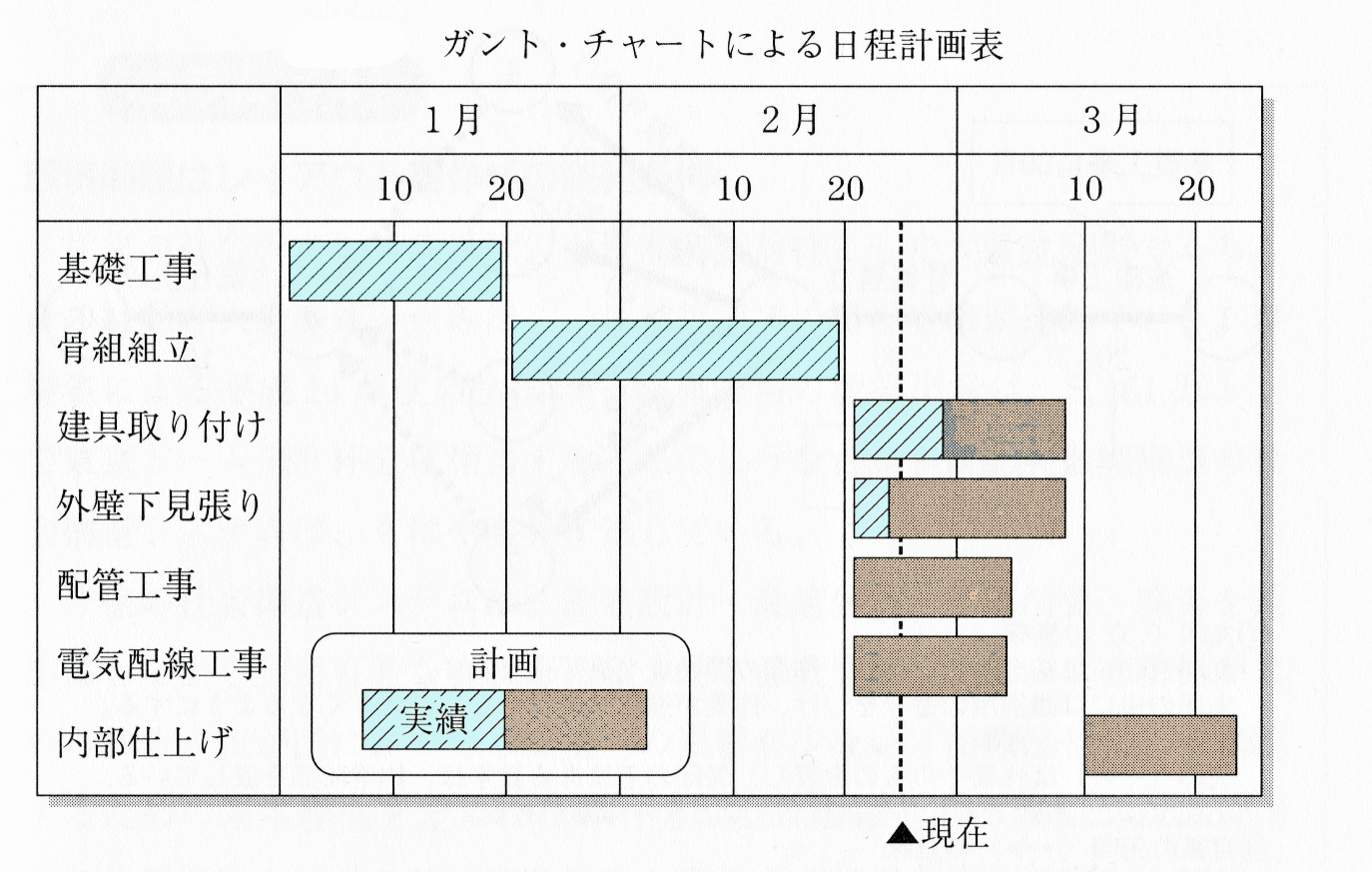
ガント・チャートによる日程計画表
仕事の順序を表現するアロー・ダイヤグラム
活動日程を計画する際に、仕事の順序、相互関係を表現するために工夫された日程計画技法がアロー・ダイヤグラム法である。
図4-12は、表4-9のガント・チャートの内容をアロー・ダイヤグラムで表したものである。図の矢印の系列は、「基礎工事」「骨組組立」「建具取り付け」などの作業で、相互関係が明確になる。日程計画を表すのに矢印を用いるため、その形からアロー・ダイヤグラム法とよんでいる。
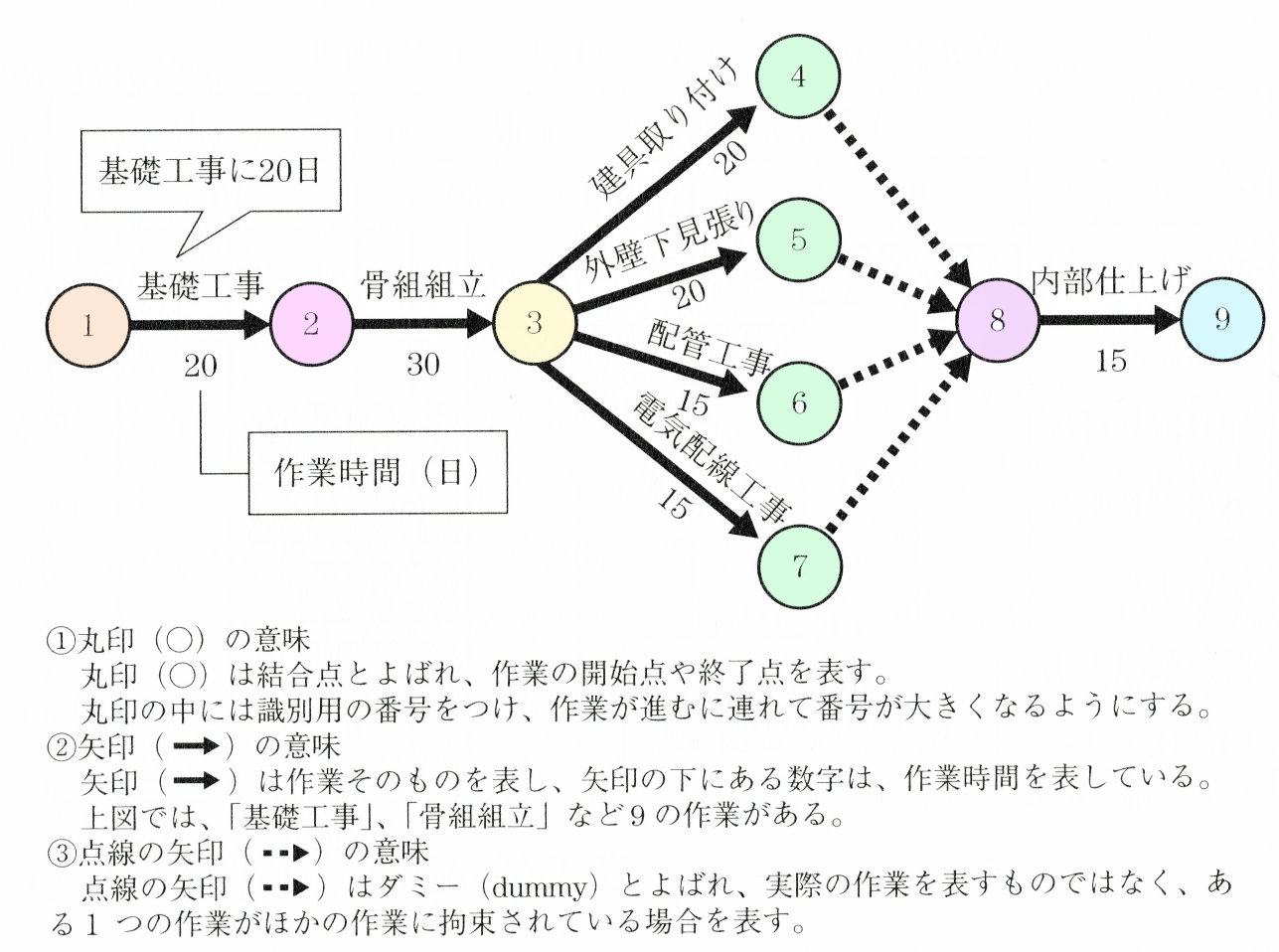
アロー・ダイヤグラム
アロー・ダイヤグラムは、PERT(パート)で用いる日程計画図である。 PERTは、Program Evaluation and Review Techniqueの略で、1958年に米国海軍のポラリス・プロジェクト(ミサイルの開発)に関連して開発された。 PERTの適用により当時ミサイルの開発期間を2年間も短縮した。
動画 工場立地とレイアウト
*工場のレイアウトについては下記の文献に色々な活動事例等が更に詳細に記載されています。
参考文献:
よくわかる「レイアウト改善」の本
小川 正樹 (著)
図解 すぐに使える 工場レイアウト改善の実務
田村孝文 (著), 小川 正樹 (著)