工場レイアウト改善の重要性
工場レイアウト改善の重要性について解説します。これは製造業における効率・品質・安全性を高めるための極めて重要な施策です。
生産効率の向上
レイアウトを最適化することで、作業者の動線や物の流れがスムーズになり、無駄な移動や待ち時間を削減できます。これにより、生産スピードが向上し、リードタイムも短縮されます。
コスト削減
無駄な在庫の削減や運搬コストの低減につながります。また、レイアウト改善により設備稼働率が上がれば、生産あたりのコストも抑えられます。
安全性の確保
動線が整理されることで、衝突や転倒といった事故のリスクが減少します。作業者の安全が確保されることで、労災の防止にもつながります。
品質向上
レイアウトの改善により、作業環境や工程の管理がしやすくなり、ミスや不良の発生を抑えることができます。品質トラブルの未然防止にも効果的です。
柔軟な対応力の向上
製品の種類や生産量が変動する中でも、柔軟に対応できるようなモジュール型・セル生産方式などの導入が可能になります。
工場レイアウト改善は単なる配置換えではなく、現場全体のパフォーマンスを引き上げる戦略的な取り組みです。小さな改善でも積み重ねることで、大きな成果につながります。
運搬(マテハン)の原則とレイアウト改善
自動車で買い物に行った時、駐車場は目と鼻の先にありながら、一方通行や右折禁止で遠回りをしなければならないことがある。工場の中でも、モノを次工程に運搬するのに、機械設備の配置や固定施設に邪魔されて迂回することもある。
また、天井クレーンを利用してモノを運搬しているところでは、建屋間の運搬でクレーンを乗り継ぎごとに「玉掛け・玉はずし」があり、時間がかかることもある。これら運搬に関する問題を改善するヒントに下表に示す運搬の原則があるので以下に紹介する。
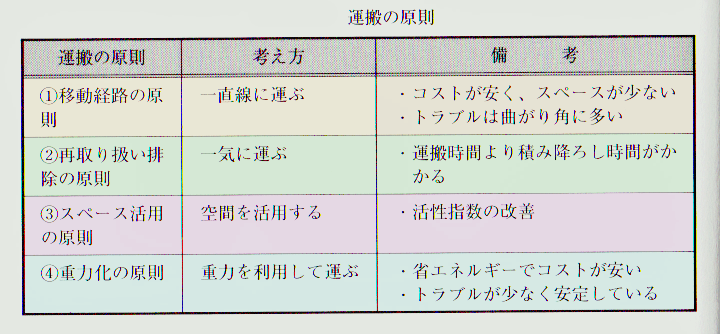
運搬の原則
移動経路の原則
運搬距離を最短にするには、一直線で運ぶことである。それには、一本道の直線で運搬できる通路を適正に配置することが重要になる。また、自動車事故も直線部分よりも曲線部分で多いように、運搬中のトラブルは曲線部にさしかかった所で発生することが多い。モノは直線で運搬することを原則としたい。
再取り扱い排除の原則
再取り扱いとは、停滞の前後に取り扱い作業がある場合のように、2度目の取り扱いをさす。モノの運搬では、運搬時間よりも台車やパレットに積み込んだり、目的地で1個ずつ降ろしたりするなどの作業に時間がかかっている。再取り扱いを排除すれば、運搬時問やムダを改善することができる。
再取り扱い排除の例として、自動車会社のラインサイド搬入がある。自動車会社では、従来窓口納入で協力会社がストックヤードに納入し、その後社内の人がラインサイドまで運搬する「再取り扱い」を行っていた。
だが、協力会社でピッキングを行っている部品を、社内で再びピッキングを行うことはムダであり、現在では社内ピッキングを排除した方法がとられている。それは、協力会社がラインサイド(またはサブ組立ライン)まで直接トラックで部品を搬入するのである。2階または地下にフロアを作成し、ライン直上または直下までトラックが入れるようにレイアウトを改善した会社もある。
スペース活用の原則
床面積や空間を活用せよという原則である。具体的には、バラ置き、ひら置きをなくし、品物の置き方を整理し、ルール化し、箱やコンテナ、パレットなどを有効に活用できる立体的な配置などを検討する。
重力化の原則
運搬改善の基本的な原則の1つでモノの運搬に重力を活用せよという原則である。重力の利用は二酸化炭素の削減など省エネルギーだけでなく、トラブルが少なく安定しているという長所がある。重力を利用した機器には、コンベア上に荷物をのせて人力で押したり、傾斜をつけて重力で滑走させたりして荷物を運ぶ重カコンベアやシュートを利用したものがある。
レイアウトの問題を把握
現場でできるレイアウト改善の最初のステップは、「改善の対象となる問題・課題の把握」である。職場内のレイアウトに関するさまざまな問題や課題を洗い出して把握し、それらの問題・課題の中からもっとも改善の優先順位が高いテーマを選定する。
「問題や課題が明確になったら解決されたようなもの」とよくいわれるが、職場のレイアウトにとって問題とは何なのかをはっきり規定する。
ここで、問題とはあるべき姿(ねらい、期待)と現状のあるがままの姿とのギャップである。あるべき姿のレイアウトとしてどうしたいか、どうなりたいかを職場のメンバー全員で明確にして、初めて問題となる。
問題と課題を見つける
人によって異なる問題のとらえ方
「問題」は、常に人が問題と認識するものが問題となる。どこかに「問題がある」のではなく、誰かが「問題にする」ことによって「問題になる」。問題はすべての人にとって問題であるとは限らない。その人にとって「問題」と思えても、ほかの人にとっては何でもないこともありえる。
くさいものに蓋をしない
人は自分の感じた問題と向き合い、何とかならないだろうかと考え始めた時、心の中には問題意識が生まれる。誰でも問題を感じるが、それに正面から挑まない限り、その問題はないのと同じである。誰も問題にしないことを問題にすることで、問題が見えるようになる。
問題と課題は違う
居酒屋で仲間と会社のことを肴にしている人たちをよく見かける。その人たちにとっては、それが問題なのかもしれないが、朝になると何を話したのか忘れていることが多いようである。
問題は、自分の意識の中にあるだけでは解決できない。自分が解決すべき問題として、具体的に考え、行動を起こし始めた時、その「問題」は、その人にとって、「課題」になる。
また、問題は発生した時、発見した時、探し出した時にメモや記録するよう心がけよう。
工場レイアウトの問題を具体的に把握する方法
現場観察(Gemba Walk)
実際に現場を歩きながら、作業者の動き・モノの流れ・滞留・ムダなどを観察します。
作業者が頻繁に往復していないか?
部品や工具を探している様子はないか?
無駄な運搬や手待ちが発生していないか?
スパゲッティチャートの作成
作業者やモノの動きを線で可視化する手法です。複雑に絡み合っていれば、レイアウトの非効率さが一目瞭然になります。
関連記事:
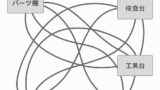
動線・物流の確認
素材の搬入から製品の出荷まで、スムーズにつながっているか?
逆流や交差が発生していないか?
作業時間の分析(タイムスタディ)
各工程の時間や、作業にかかる時間を計測します。時間のムダが多い部分は、レイアウトに問題がある可能性があります。
ヒアリング・アンケート
作業者の声から現場の問題点を拾います。実際に手を動かしている人が、一番課題に気づいていることも多いです。
レイアウト図の更新
現状の工場レイアウト図を最新に保ち、どこでどの作業が行われているかを把握します。古い図面では、正確な分析ができません。
具体的なレイアウト上の問題例
問題例 | 説明 |
---|---|
動線が長い | 作業者や部品の移動距離が長くなり、時間のロスが発生 |
工程間に在庫が滞留 | 不要な中間在庫が溜まり、スペースを圧迫 |
工場内が雑然 | 整理整頓がされておらず、探し物が多く発生 |
作業エリアが狭い/広すぎる | 作業効率や安全性に悪影響 |
設備の配置が不適切 | 設備間の連携が悪く、搬送に手間がかかる |
工場レイアウトの問題・課題を絞り込む
問題・課題を洗い出したら、その中からレイアウト改善しなければならないテーマを選定する。
限られた期間、人員、予算などの制約があるなかで、すべての問題を解決することは現実的ではない。
そこで、問題・課題に取り組む必要性、問題が解決した時の貢献度、職場の実力などの観点からテーマを絞り込む。これは、改善効果の大きい重点問題・課題に着目するという考え方で、重点指向のアプローチである。重点指向で問題・課題を絞り込むためにつぎのような項目で改善の要求度を評価する。
・重要度:問題が職場に影響している度合いはどの程度か?
・緊急性:早急に解決・達成しなければならないか?
・効 果:解決・達成した時の効果は大きいか?
・会社方針:会社の方針に沿っているか?
また、職場の改善サークルなどでレイアウト改善をテーマにする時は、下表のようなテーマ選定マトリックスを用いると便利である。
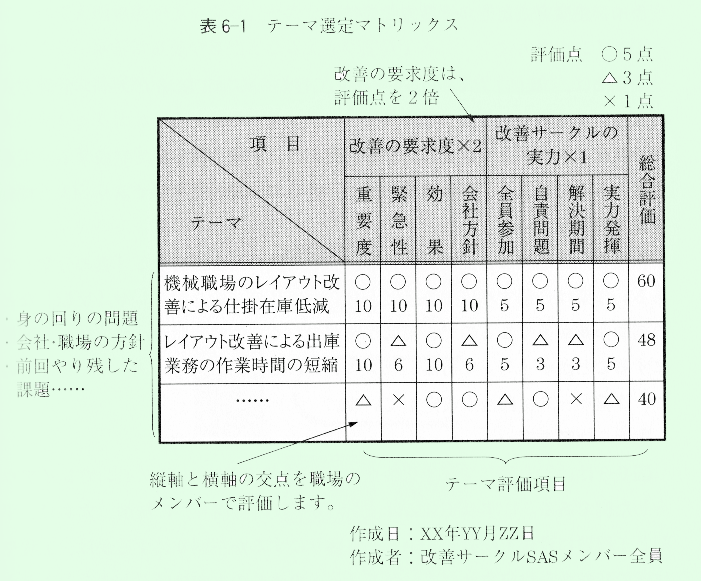
テーマ選定マトリックス
工場レイアウトの問題・課題を絞り込むSTEP
影響度 × 発生頻度で評価
それぞれの問題を、「工場全体への影響度」と「発生頻度」でマトリクス化して評価します。
影響度 \ 発生頻度 | 低い | 高い |
---|---|---|
高い | 改善候補(中) | 最優先で改善 |
低い | 後回し | 改善候補(低) |
→ **「影響が大きく、頻度が高い問題」**から着手するのが鉄則です。
ボトルネック工程の特定
全体の流れの中で、作業が滞っている工程や、他の工程のペースを制限している部分(ボトルネック)を見つけ出しましょう。
その工程の前後に仕掛かり品が溜まっていないか?
その工程だけが極端に時間がかかっていないか?
定量データの活用
現場の感覚だけでなく、数値データで判断することで、より正確な絞り込みが可能です。
移動距離(m)
作業時間(秒・分)
搬送回数/日
在庫の滞留時間(時間・日数)
→ 例えば「仕掛かり品の滞留時間が長い→工程間の距離が原因」といった形で、因果関係を見つけるヒントになります。
関係者の声を聞く
現場のリーダーや作業者に「どこが一番困っているか?」「改善したい部分はどこか?」をヒアリングすることで、絞り込みのヒントが得られます。
改善効果の見込みで選定
以下のような改善効果が高い問題を優先しましょう。
生産性が大きく上がる
安全性が劇的に向上する
作業者の負荷が大幅に減る
設備投資が不要/少額で済む
事例:絞り込みの実践
問題点 | 影響度 | 発生頻度 | 優先度 |
---|---|---|---|
組立→検査の搬送距離が長い | 高 | 高 | ◎(最優先) |
部品棚の配置が分かりにくい | 中 | 高 | ○ |
作業エリアの照明が暗い | 中 | 中 | △ |
台車の数が足りない | 低 | 高 | △ |
出荷場がやや手狭 | 中 | 低 | ×(後回し) |
絞り込みのポイント
数値で評価する
影響度と頻度でマトリクス化
現場の声を重視
すぐに効果が出るものから手を付ける
ライン生産方式とセル生産方式の特徴
PQ分析のAランクや少種多量生産に向いたライン生産方式は、素材の投入から最終工程まで、工程順に機械設備を並べてライン化し、1人または数人で仝工程を受け持つ製品別レイアウトである。
また、Bランクや中種中量生産に向いたセル生産方式も、類似グループごとに素材の投入から最終工程まで、工程順に機械設備を並べてライン化した類似製品別のレイアウトになる。ライン生産方式とセル生産方式の特徴を整理し、改善の方向性を整理する。
ライン生産方式
下図は、「旋削」「穴あけ」「平削」工程がある加工職場のライン生産方式のレイアウト例である。
材料はコンベア上を移動し、旋削、穴あけ、平削工程を経て完成する。生産要素である材料、人、機械設備中で、移動しているのは材料であり、人と機械設備は固定している。
作業の分業形態は、旋削、穴あけ、平削を別の人が担当する「質の分業」である。作業は分割すればするほど、材料や部品の「取り置き」や「反転」などの補助作業が多くなるので、補助作業が少なくて作業時間がバランスした配置にすることがポイントである。コンベアのスピードがペースメーカーになるので、作業ペースは円滑で安定している。
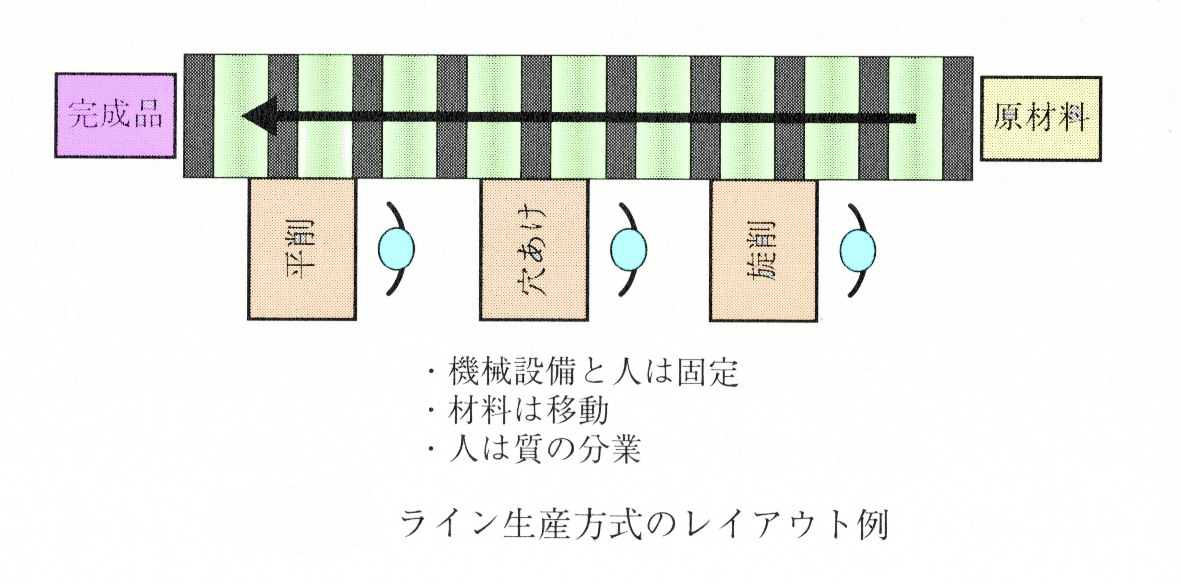
ライン生産方式 レイアウト例
メリット:
高い生産効率(大量生産に最適)
作業が単純で習熟が早い
管理がしやすい(工程が明確)
デメリット:
柔軟性が低く、多品種少量生産には不向き
作業が単調でモチベーションが下がりやすい
一部の工程が止まると全体に影響する
セル生産方式
下図は、①と同じ工程をセル生産方式の代表的なU字ラインでレイアウトした例である。U字ラインでは、左回り(反時計回り)に旋削、穴あけ、平削と工程順に設備を配置している。右回りにするか左回りにするかは、工程や作業の特性から決定すればよいがモノと人の流れの方向は同じとする。たとえば、旋削工程ではチャックが左側にある機械設備を使用するので、右回り(時計回り)にすると、勣作が不自然になるので左回りの配置にしている。
生産要素は機械設備が固定であり、材料と人が移動するのでライン生産方式に比べて人の移動が多くなる。そのため、機械設備間や機械設備の横幅は極力小さくし、歩行は直線で最短となるように配置する。
作業の分業形態は、1個の製品を1人の作業者が初工程から最終工程までを責任をもって仕上げる「量の分業」であり、多能工としての技能スキルが必要になる。ライン生産方式に比べて、作業範囲が広いのでマイペースによる生産性低下を防止する配置や仕組みにすることがポイントになる。

セル生産方式 レイアウト例
メリット:
柔軟な対応が可能(設計変更や特注品にも強い)
作業者のスキルアップ・モチベーション向上
不良の早期発見がしやすい
デメリット:
作業者に高いスキルが求められる
生産スピードはライン方式に比べて劣る場合がある
教育コストが高くなることも
ライン生産方式とセル生産方式の違い
ライン生産方式とセル生産方式は、製造業における生産方式の代表的なスタイルで、それぞれに特徴やメリット・デメリットがあります。以下に違いをわかりやすく比較してみましょう。
ライン生産方式とセル生産方式の特徴と改善の方向性をまとめたものが、下表である。それぞれの生産方式の特徴を活かし、さらなる改善点を加えてよりよいものにしていく必要がある。
ライン生産方式とセル生産方式の比較表
ライン生産方式のレイアウト改善
加工職場や組立職場で生産を流れ作業方式で行う場合、重要な要因となるのが各工程(ステーション)や機械設備に割り当てられた作業時間である。生産ラインを構成する各工程間の作業時間のバランスをラインバランスという。
ラインバランスの必要性
ラインバランスがとれていないと、仕掛品の停滞する工程や、手待ちの工程が発生し、流れ作業方式の最大の特徴である機械設備、労力の十分な活用ができなくなる。たとえ1つの工程で所要時間が少し長くなっただけでも、仝工程が、その長い時間に影響されてしまう。完全なラインバランスをとることは難しいが、極力その目標に近づけることが重要な意昧を持つ。
ラインバランスを見える化するピッチダイヤグラム
下表の左側は、コンベアで流れ生産しているラインの各工程の所要時間値を製品の流れに従ってグラフに表したピッチダイヤグラムである。第1工程はA作業を2分、第2工程はB作業を4分、第3工程はC作業を7分というように構成され、全部で7工程からなっている。作業時間が最も長いのは第3工程の7分で、いわゆるネックエ程である。
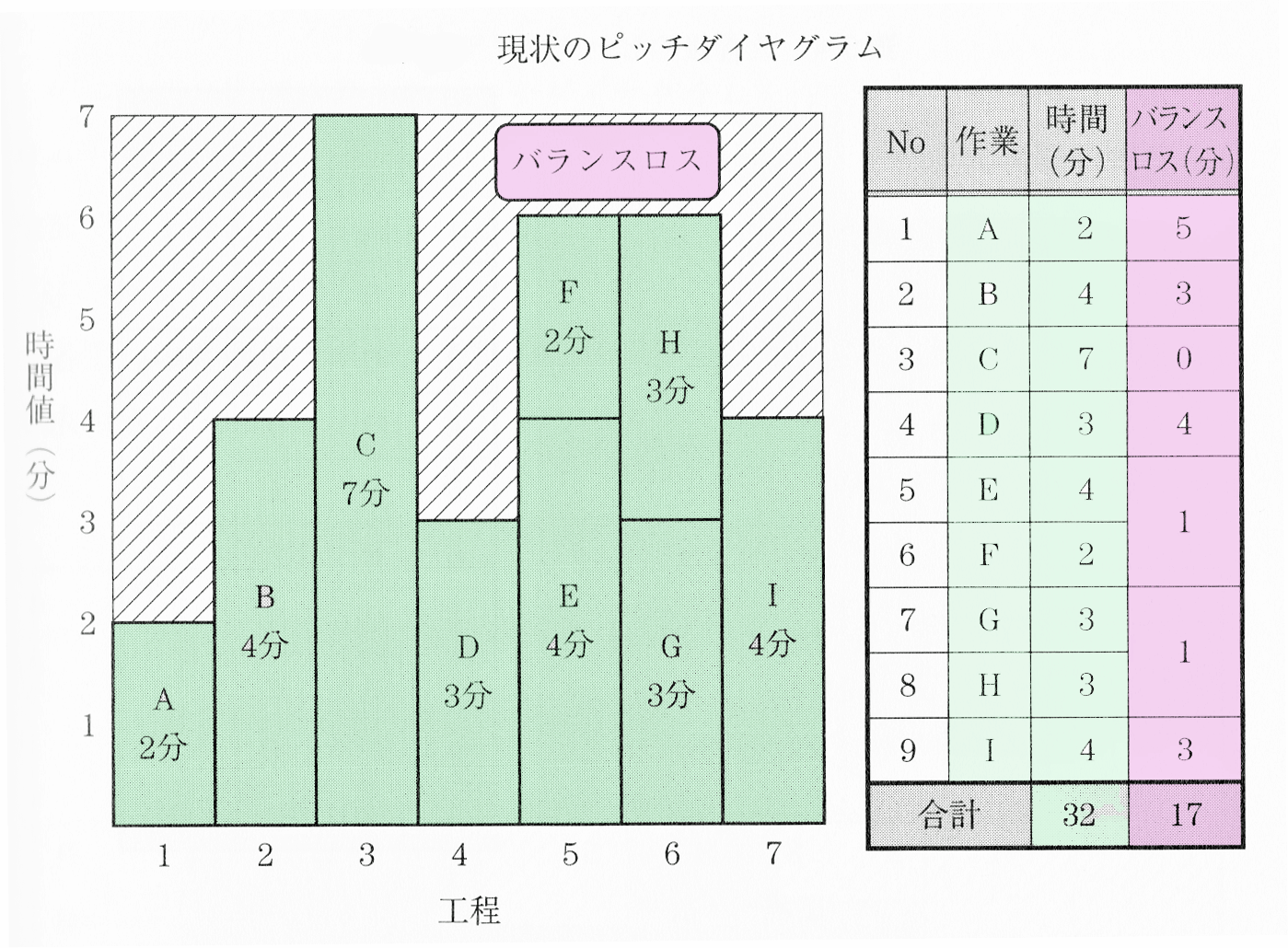
ピッチダイヤグラム
流れ作業方式で発生するバランスロス
バランスロスは、生産ラインを構成する各工程間の作業量(作業時間)のバランスがとれていないために発生するロスである。ライン作業ではネックエ程の作業量により製品の出来高が決まるため、各工程間の作業量が異なると、作業時間の小さい工程には「待ち」、すなわちバランスロスが生ずる。上表のピッチダイヤグラムでは、第1工程の作業時間は2分なのでバランスロスはネックエ程の7分から2分を引いて5分、第2工程では7分から作業時間の4分を引いて3分がバランスロスである。このようにして求めた各工程のバランスロスを合計すると、上表の右側のように17分になる。
下表の左側は、作業の人替により改善した後のピッチダイヤグラムである。
改善より工程数は7工程から5工程に2工程削減した。その構成は、第1工程はA作業とB作業で6分、第2工程はC作業で7分、第3工程はD作業とE作業で7分、第4工程はF作業とG作業で5分、第5工程はH作業とI作業で7分である。また、バランスロスは、第1工程1分と第4工程2分の計3分に低減している。
このように工程数が7工程と5工程では必要面積が異なるので、レイアウトも当然変わってくる。流れ生産の職場では、レイアウト改善とともにラインバランス改善が必要になる。
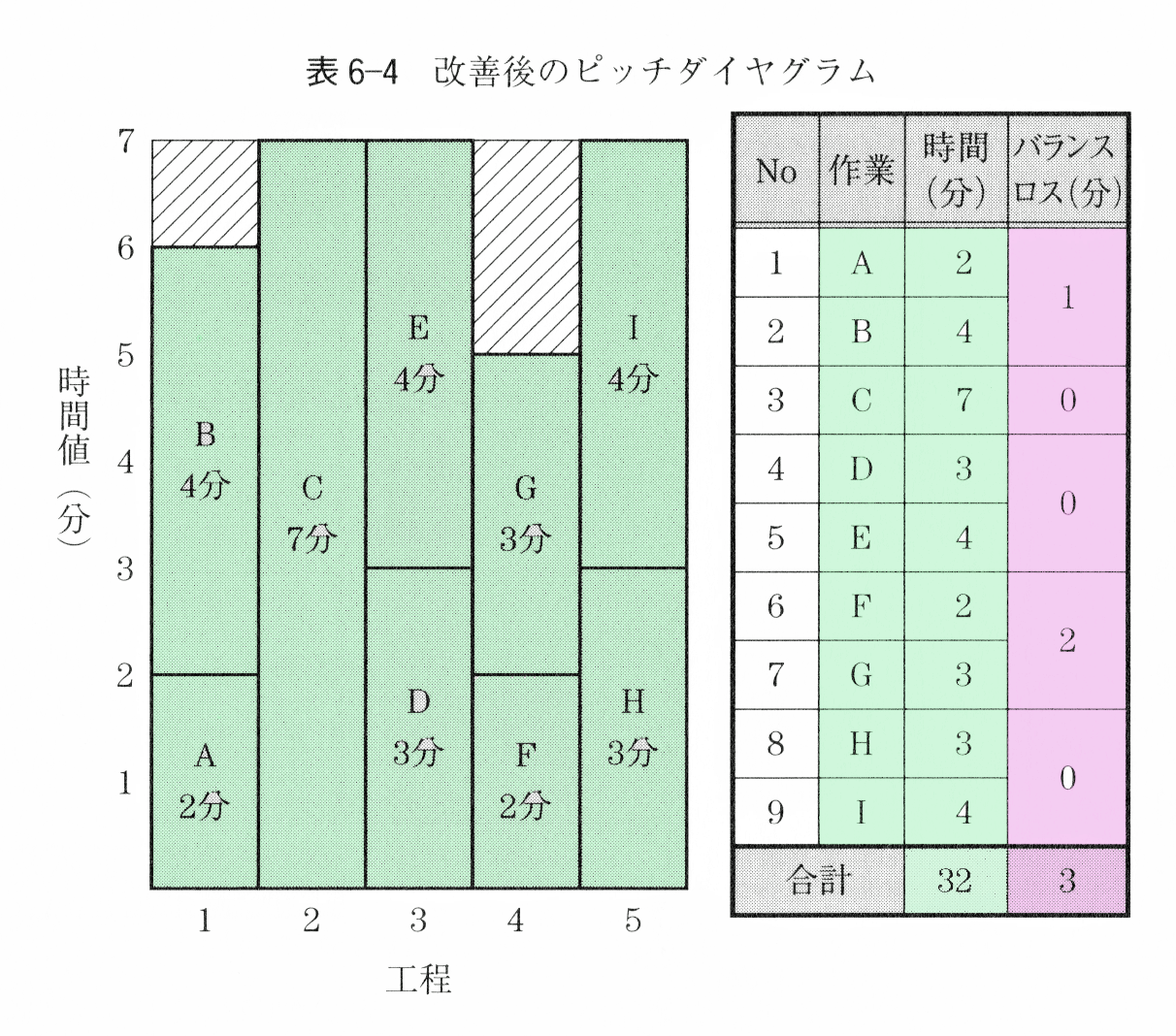
改善後のピッチタイム
バランスロスを減らすライン編成分析の進め方
ライン編成分析は、ライン作業におけるバランスロスを低減することを目的とした分析手法である。工程ごとの時間値を計り、ピッチダイヤグラムに図示し、そのバラツキを視覚的にとらえて改善のポイントを明らかにする。
ライン編成分析の手順
以下はライン編成分析の手順である。
作業を区分する
各工程(作業者)の作業を区分し、それぞれの工程が何の作業で構成されているかを確定する。
作業ごとの時間を測定する
①で区分した作業ごとに時間を測定し、1作業ずつ時間値を確定する。
ピッチダイヤグラムを作成する
作業時間の観測結果からピッチダイヤグラムを作成する。下表は、コンクリートの2次製品を製造しているラインの現状のピッチダイヤグラムである。
全部で7工程あり、ネックエ程は第2工程で、時間値は130秒である。
ラインの編成効率・バランスロス率を計算する
各工程の時間値とネックエ程の時間値により、ラインの編成効率は以下の式で求める。
編成効率(%)=各工程の時間値の合計÷(ネック工程の時間値×工程数)×100
表6-5の例で計算すると、編成効率は65.0%である。
編成効率(%)=89+129十76+97+80+55+61÷(129×7)×100=65.0%
また、100から編成効率を引くとバランスロス率になるので、計算すると35%もあることがわかる。
バランスロス率(%)=100-編成効率=100-65.0=35.0%
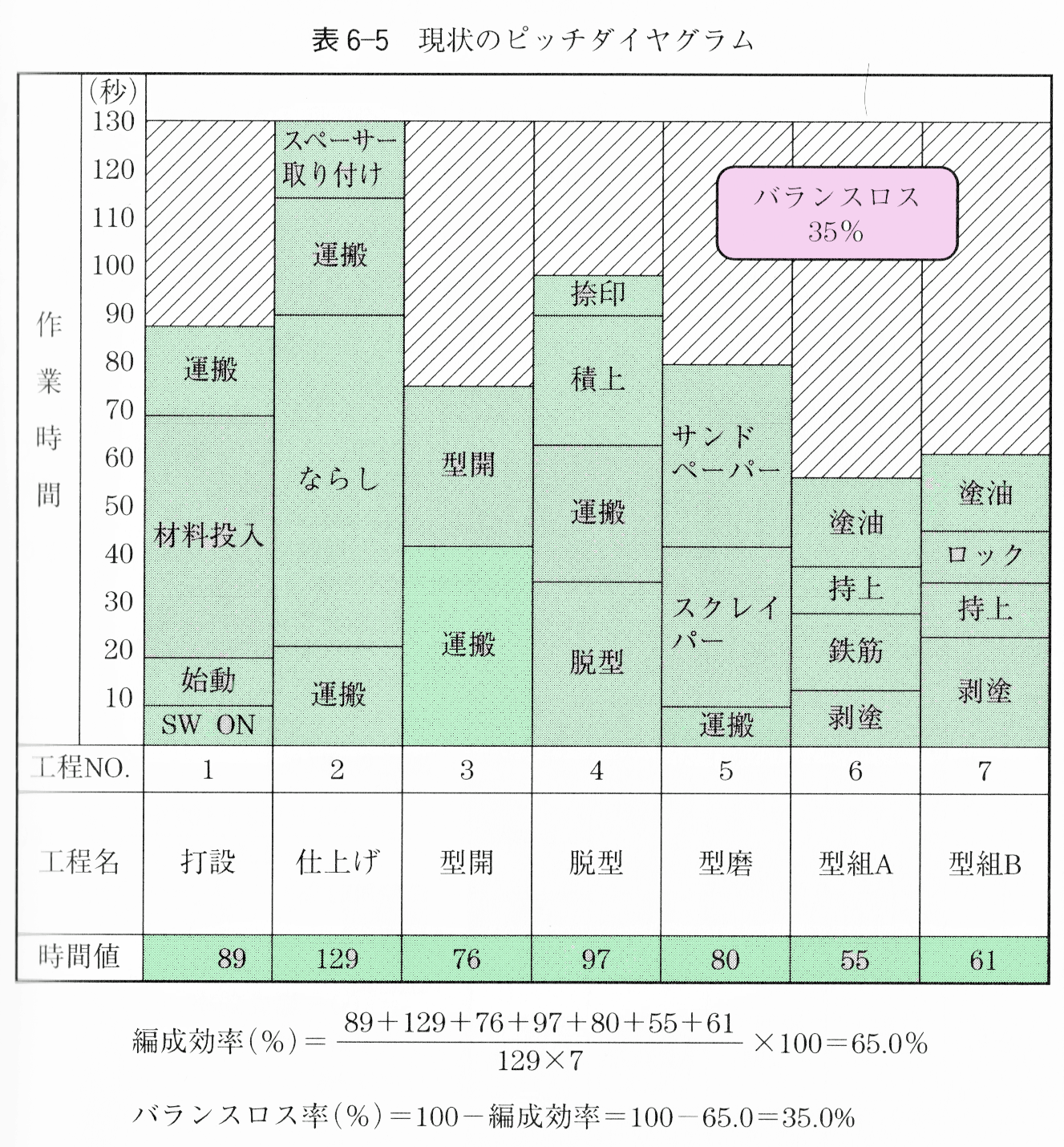
現状のピッチダイヤグラム
改善案を検討する
ネックエ程についての改善、作業の移動でバランスロスを低減する。ここで注意すべきことは、1製品を完成する時間(サイクルタイム)を意識することである。1日の生産予定数が50個ならば、1日8時間(480分)で、1個のサイクルタイムを9.6分(480分÷50個)で生産していけば、1日の生産量がまかなえる計算である。 9.6分より短い時間に改善しても、手待ちの時間が増えるだけで、改善効果は半減してしまう。
下表は、生産量を考慮して改善した結果である。運搬改善など主な改善点は表に要約したが、工程数は7工程から4工程、編成効率は65.0%から90.1%に向上している。
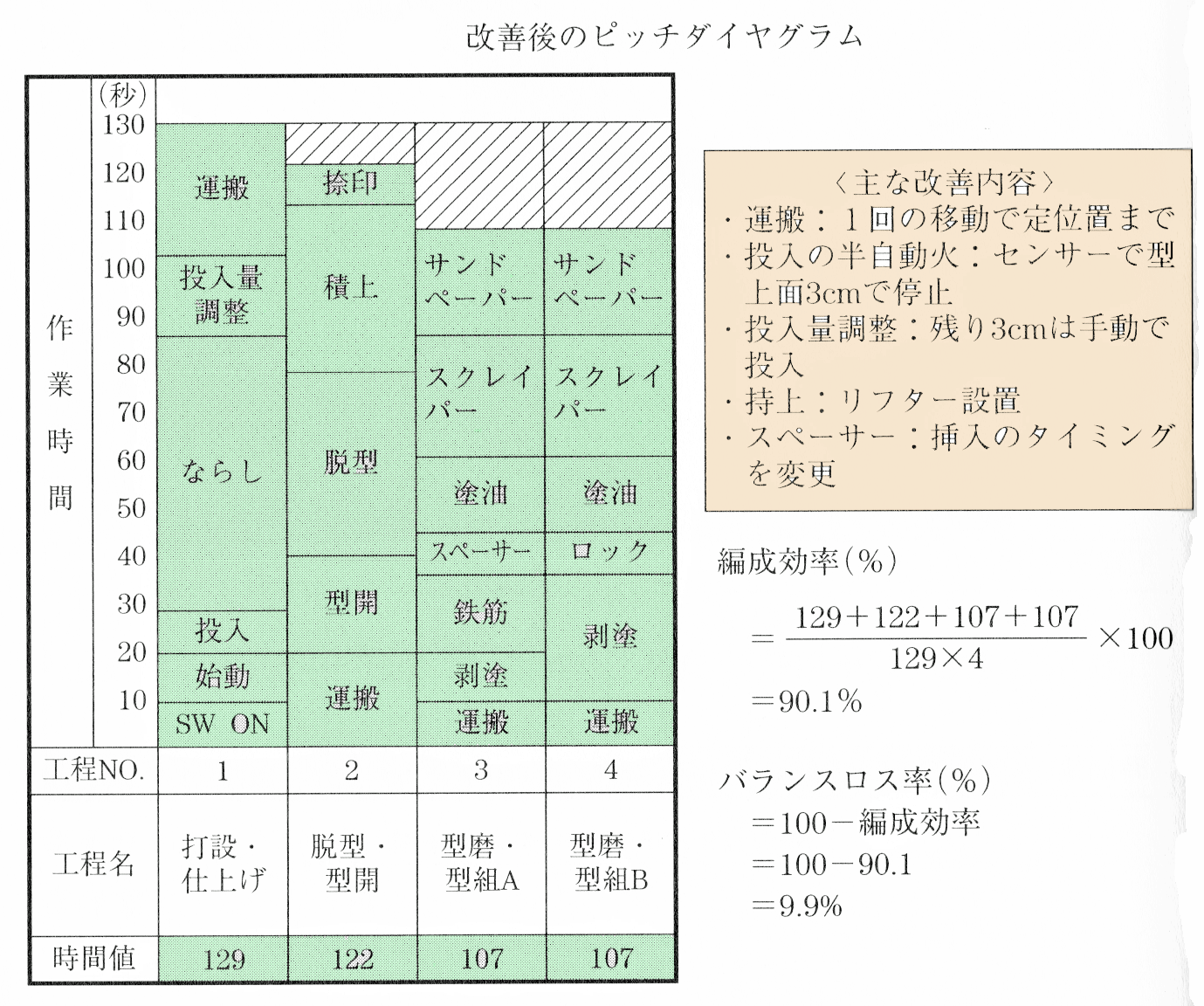
改善後のダイヤピッチタイム
U字ラインをレイアウトしよう
機械設備をU字型に配置したU字ラインは、セル生産方式の代表である。
下図のように直線に並べられたラインでは、旋削、穴あけ、平削加工が終了し、完成品を置いてつぎの材料をとりに行くのに、もと来た道を手ぶらで歩いて帰ることになりムダになる。それに対してU字ラインは、原材料と完成品入口と出口が一緒なので歩行のムダがなく、モノの流れから見ても誠に都合よくできている。

直線ラインとU字ライン
U字ラインレイアウトの基本
このレイアウトの基本は、以下の項目がポイントである。
①U字ラインの入り口は原材料置き場、出口は完成品置き場を配置する。作業者はU字ラインの内側に配置する。
②機械設備、機器、作業台を工程順に並べる。右手でモノ(ワーク)をつかんで左手で機械設備を操作(スイッチ)するためにモノは右回り(反時計回り)に流れる。
③U字ラインの幅は作業員が1人のU字ラインでは1,000mm、2人以上ではスムーズにすれ違えるために1,200 mm 程度とする。
④U字ラインでは人がモノを運搬するので、床面からのモノの取り付け高さを一定にして、水平に移動するとムダな動きが少なくなる。モノを取り外した後、次工程において取り付けの姿勢を保ち、取り付けられるかがチェックポイントである。
モノの取り付け位置を考えるうえで大切なことは、作業点がどこかということである。「モノを持ち上げたり、保持したりするには、へその位置が疲労の少ない動作である」という疲労の少ない経済の原則を参考にすると、ワークの取り付け高さは床から1,000mm程度となる。そして、モノの取り付け高さを、工場全体で標準化することも大切である。
⑤U字ラインを上から見た時、モノの取り付け点と取り外し点が直線上になるように配置すると作業者の移動距離が短くなる。
⑥モノの取り付け、加工、取り外しを自動化した機械設備は、安全面を配慮して作業者の歩行ソーンから外に配置する。
⑦モノの工程間の移動ピッチは、今後の自動化対応を考慮すると等間隔が望ましい。
⑧機械設備、機器、作業台にはキャスターを付けておくと、工程変更が容易にできる。
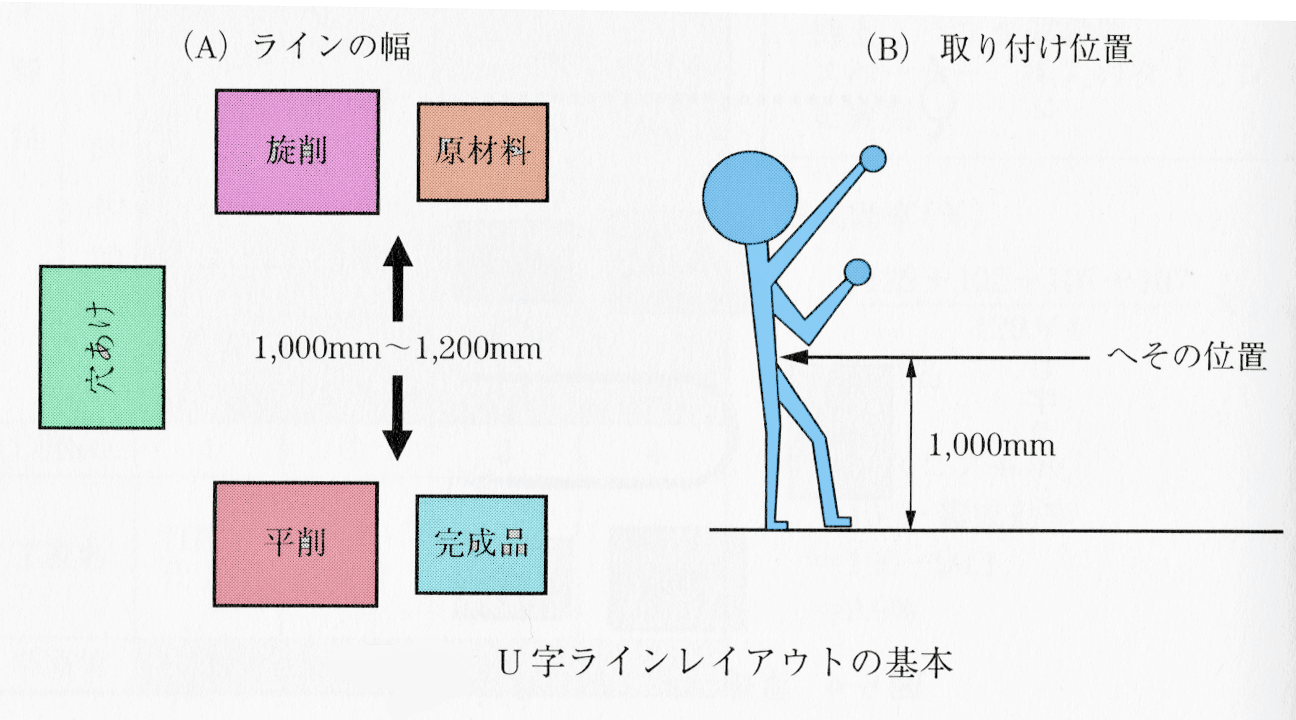
U字ラインのレイアウトの基本
セル生産方式のレイアウト改善
セル生産方式は、中種中量に適用する生産方式で、数工程を1人または数名で完結する量的分業の生産形態である。ライン生産方式に比べて、量の分業で1人の作業時間が長くなるので、「歩行距離が長くなる」「作業ペースがばらつく」などが短所となりやすい。これらの改善案を考えてみよう。
歩行距離を短縮するレイアウト
セル生産方式は、1人の作業者が数工程を受け持つために歩行距離が長くなる欠点がある。たとえば、下図の改善前のレイアウトは、2人の作業員が6台の機械設備をすべて担当しているため、歩行距離が長くなっている。一方、改片後のレイアウトは、機械設備1~機械設備3までを1人、機械設備4~機絨設備6を1人が担当しているので、作業員の歩行距離は半分以下に短縮されている。
このように歩行距離を短縮するレイアウト改善には、つぎのような方法がある。

歩行距離短縮 レイアウト
歩行を排除する
歩行は工程の分割によって発生するので、分割をやめて1工程で加工を完了させる。コンベアなどの運搬器具を活用し、歩行を排除する。
歩行距離を少なくする
立体式、対面式などのレイアウトを工夫する。
歩行回数を少なくする
同時に複数個加工することで、運搬効率を上げることで歩行回数を少なくする。
作業ペースを維持する仕組み
セル生産方式は、ライン生産方式のようにコンベアなどによる強制力がないので、作業者の能力差や作業ペースの差が生産性の差になってしまう。競争意識が芽生えて1人あたりの出来高が向上するセル生産方式では、ペースダウン作業時間のばらつきによる生産性低下を補う仕組みが大切になってくる。それには、つぎのような方法がある。
1)ペースメーカーになるライン生産方式や機械設備の間にセル生産方式をはさむ配置にする。
(2)作業員の競争意識を剌激し、作業員同士で自然に競い合えるレイアウトにする。
(3)時間ごとの出来高など目標時間管理や作業能率を管理する仕組みを導入する。
5 S を成功させるレイアウト改善
5Sとは、下図に示すSeiri(整理)、Seiton(整頓)、Seisou(清掃)、Seiketsu(清潔)、Sitsuke(躾)のSで始まる頭文字の5つをとったものであり、モノづくりの基盤である。整理と整頓の2Sが職場改善のスタートになるので、レイアウトが関連するポイントをまとめておく。
整理の進め方
整理とはいらないものを捨てることである。通常、工場内には長年にわたって回かれたものが散在している場合が多い。とくに工場の隅、機械設備の裏に誰が置いたかわからないガラクタが散在している。いるものといらないものにケジメをつけ、不要なモノを捨てることでレイアウトに必要な面積も確保できる。
整頓の進め方
整理により工場からいらないものが排除され、いるものだけが残ると、整頓が始まる。欲しいモノをいつでも取り出せる状態にしておくことが、整頓である。整頓とは「モノの置き方の標準化」であり、モノが「誰でもひと目でわかる」「誰でもすぐに使える」「誰でもすぐに戻せる」しくみをさす。
モノの置き場を決めることを定置化というが、その手順が以下である。
①近くへ置くもの、遠くへ置くもの、倉庫へ入れるものを区分する。
②近くへ置くものは、使用頻度が高く本当に必要なものだけに絞る。使用頻度の少ないものは集中管理する。
③整理整頓で決められたルールに従って、下図のように作業場や機械設備、通路、置き場所がわかるように区画線を引く。通路幅は2人が安全にすれ違うことを考えると1,200mm以上、区画線の幅は100~120mm程度である。
消火器、台車、工具、備品など定位置が決まっているものは、定位置の印を1000nm程度の区画線でつける。区画線は、直線・直角・垂直・水平にすると見た日もきれいで効率的になる。
このような、モノの置き方がひと目でわかる管理状態になると、仕事のやり方やその時の状況が「正常」なのか「異常」なのかがハッキリわかるようになる。たとえば、下図の台車置き場を見れば、すぐに置き方の異常がわかるので、改善のアクションが打たれるであろう。このように、「異常」を表に引きずり出して、改善・改革することが整頓の重要ポイントである。
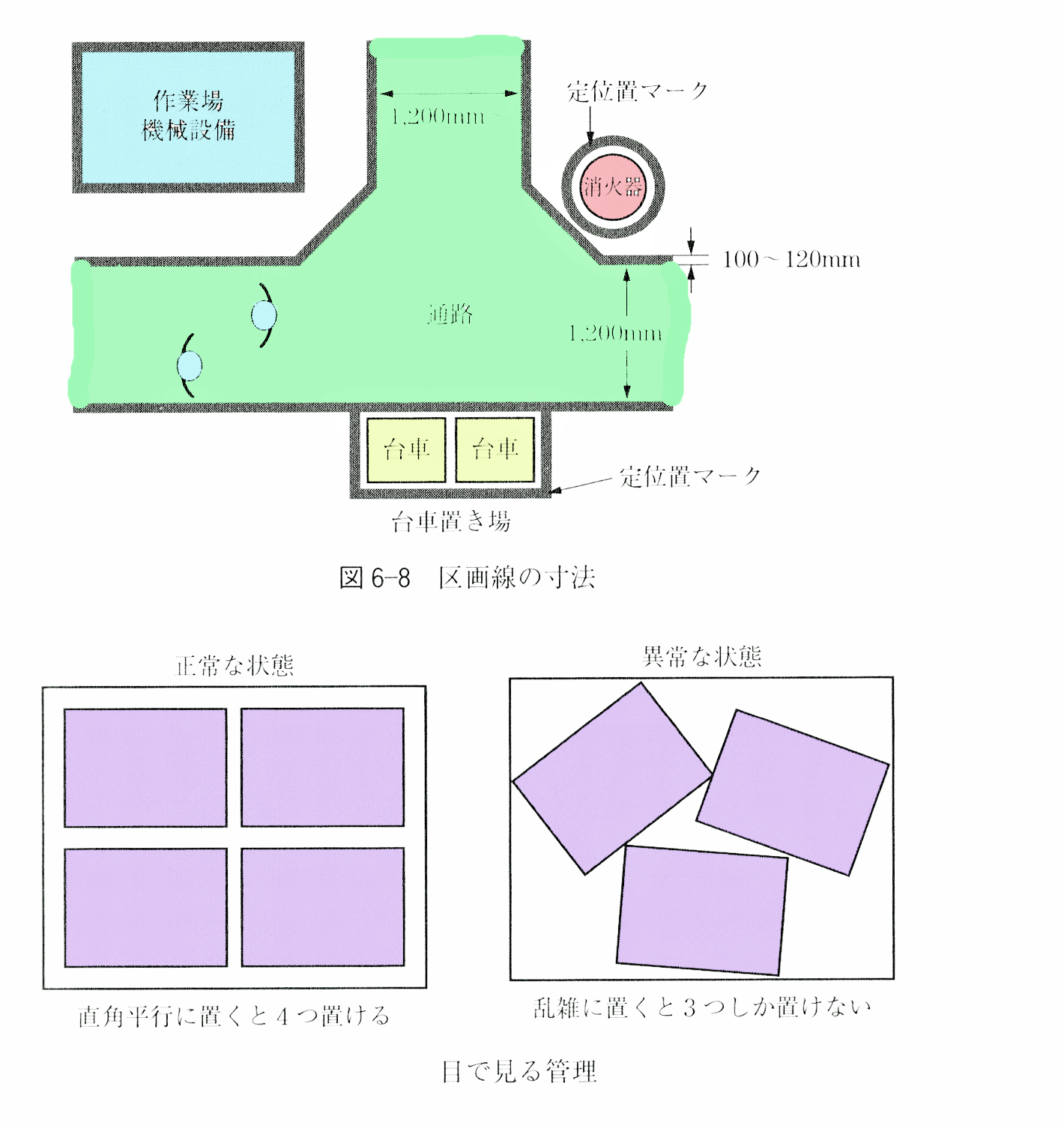
区画線の方法
関連記事:5S 活動
工場レイアウトと環境改善
「工場レイアウト改善」と「環境改善」は切り離せない関係にあります。効率だけでなく、作業者にとって快適で安全な環境づくりもレイアウト設計の重要な目的の一つです。
作業者のストレスを軽減
レイアウトが整理されていないと、作業者はムダな移動や探し物が増え、ストレスが溜まります。
環境面では以下が特に重要です:
動線が短く、分かりやすい配置
工具・部品の定位置管理(5Sの「整頓」)
騒音・振動源からの距離確保
→ より働きやすい職場環境に直結します。
安全性の向上
レイアウト改善は「危険を遠ざける」ことにもつながります。
通路の確保:フォークリフトと人の動線が分離されているか
視認性の向上:ミラーや標識で見通し良好に
避難経路の確保:緊急時の安全動線があるか
→ 環境改善と安全衛生管理はセットで考えるべきです。
快適性の向上(職場環境改善)
温度・湿度・照明・換気といった作業環境の整備も、レイアウト設計と密接に関係します。
項目 | レイアウトへの影響 |
---|---|
空調効率 | 機械の配置や遮蔽物により空気の流れが変わる |
照明 | 作業位置に対して照度が十分か |
音 | 騒音源から作業エリアを遠ざけられるか |
→ レイアウトの工夫で職場の「見えないムダ」を減らせます。
清掃性の向上(5S)
設備や通路の配置を工夫することで、清掃しやすいレイアウトが可能になります。
床にモノを置かない
設備下に隙間を空けて掃除ができるように
ゴミの発生源を分離しやすい動線
ES(従業員満足度)の向上
環境が整った職場は、モチベーションや定着率にも好影響を与えます。
作業者が自分の意見を反映できる改善活動
快適な休憩スペースの配置
パーソナルスペースを意識した作業場の設計
環境改善を意識したレイアウト改善のチェックリスト(例)
✅ 人とモノの動線が明確に分かれているか
✅ 作業場所の照度・空調は適切か
✅ 整理整頓・清掃がしやすい構造になっているか
✅ 騒音・熱源・粉塵の発生源と距離を取れているか
✅ 安全標識や避難経路が明確か
工場レイアウトの改善は、**効率化と同時に「人が快適に働ける環境づくり」**にも直結します。
単に作業のスピードを上げるのではなく、「安全・快適・清潔」な環境を作ることで、長期的な生産性や従業員の満足度を高めることができます。
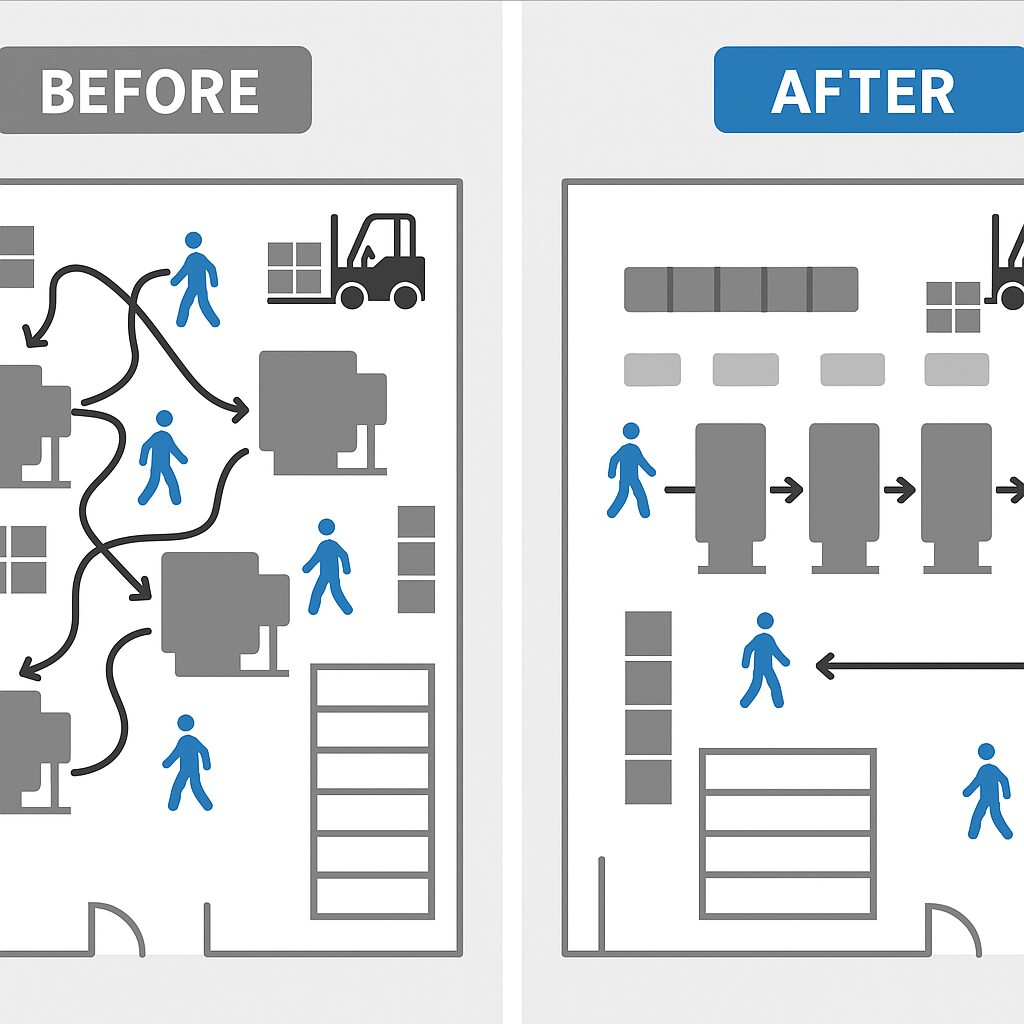
工場レイアウトと環境改善
倉庫、ストックヤードのレイアウト改善
駅前や郊外にある大型の家電量販店では、大型製品から長もの、中もの、小ものまで多種多様な製品を扱っている。その荷姿もテレビや冷蔵庫などの裸品、CD-ROMなどのケース詰、袋入れなどバラエティに富んでいる。
数万以上ある商品からお客さまが迷わず目的のものを探すために、家電量販店ではいろいろ表示がなされている。1階は携帯電話とデジタルテレビ、2階は白物家電、3階はパソコンとデジタルカメラなどの大区分、各階にはメーカー別や大きさ別の中区分などが表示されている。商品を探す時は、この表示が役に立つのである。
多品種の品目の保管と出荷をするストックヤードや倉庫でも、家電量販店と同様にどこに何を保管してあるかを「見える化」することが大切である。
ストックヤードや倉庫の課題と解決方向
ストックヤードや倉庫で抱えている課題として、つぎのような項目がある。
・出荷指図品の置場所(ロケーション)が特定の人にしかわからない。
・出庫作業の時、「歩く」「運ぷ」や「捜す」が多い。
・現品が出荷指示の品番とは違う時がある。
これらの課題を解決し、誰にでも、いつでも、モノの入出庫ができるようにするには、ストックヤードや倉庫に保管するモノに住所を付けることである。
ABC分析に基づく配置
Aランク(高頻度):出入口付近・下段に配置
Bランク(中頻度):中間エリア
Cランク(低頻度):奥または上段
→ 出庫・ピッキング効率が大幅アップ!
ゾーン別レイアウト
用途・品種・温度帯などに応じてゾーン分けし、混在を防止。
例:常温/冷蔵/危険物/工具・部品/完成品/返却品 など
動線の最適化
通路幅の基準(台車 or フォークリフトの走行幅+安全幅)
一方通行導入で事故防止&流れをスムーズに
ムダな往復動線を削減(U字・L字より「I字型」が理想)
縦空間の活用
多段ラック導入で床面積の有効活用
パレットラック+フォークリフトで高効率
IT連携の準備
レイアウトを見直すことで、以下への布石にもなります:
WMS(倉庫管理システム)の導入
バーコード・RFIDによる棚番管理
自動搬送(AGV)導入に対応した通路設計
レイアウト改善の進め方(ステップ)
現状のレイアウトと動線を可視化(図面+スパゲッティチャート)
在庫データ分析(ABC分析・保管日数)
作業者ヒアリング・安全点検
改善案の立案とシミュレーション
段階的にレイアウト変更(トライ&エラー)
倉庫やストックヤードは、単なる「モノを置く場所」ではなく、物流効率と経営成果に直結する重要拠点です。レイアウトを変えるだけで、
人の動きが減る
ピッキング精度が上がる
在庫の見える化が進む
など、大きな改善効果が見込めます。
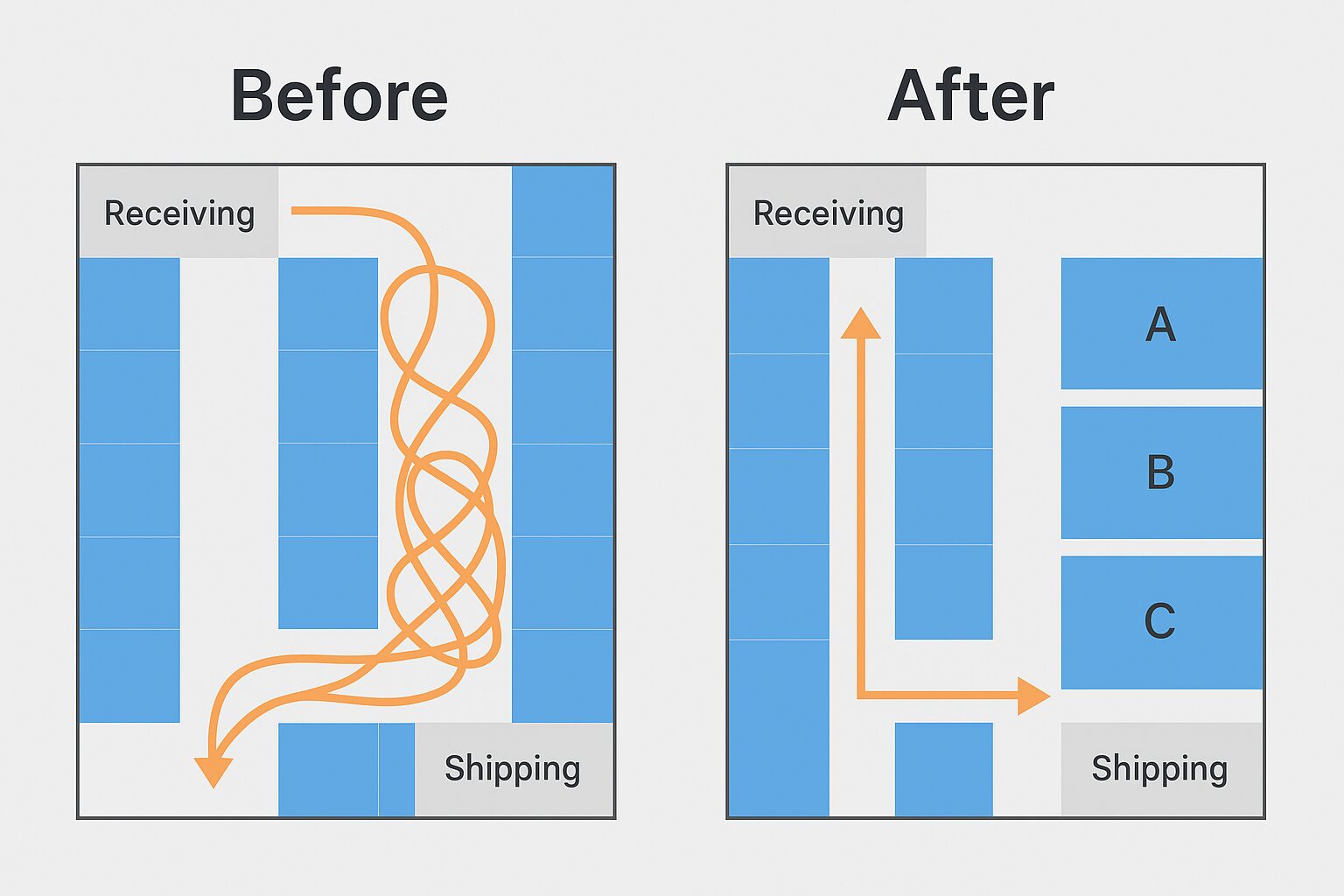
倉庫、ストックヤードのレイアウト改善
工場レイアウトの改善 欲しいモノの探し方
工場レイアウトの改善において「欲しいモノの探し方」は、効率化やムダの削減に直結する超重要テーマですね。
「欲しいモノがすぐに見つからない」ってだけで、作業効率が落ちて、ストレスも溜まる。そんな現場、意外と多いです。
ここでは、**「欲しいモノの探し方」=「探さなくてもいい仕組みづくり」**と捉えて、改善のポイントをまとめてみます。
なぜ「探す」必要があるのか?
まず現状を分析しましょう。
物の置き場所が決まっていない(5Sが未徹底)
誰かが勝手に持っていって返さない
ラベルが不明瞭、またはそもそも無い
スペースに余裕がなく、ゴチャゴチャしている
共通備品が遠くにある、動線が悪い
「探さなくていい」環境を作るための改善策
定位置管理(置き場所のルール化)
使う場所の近くに収納(「使うところに置く」が原則)
「誰でもわかる」表示:写真ラベルや輪郭表示(シャドーボード)など
棚や引き出しに「番地」を振る(例:棚A-1、棚B-2など)
5Sの徹底
整理:不要なものは捨てる
整頓:必要なものだけを、必要な場所に、必要な数だけ
清掃:きれいに保ち、異常を見つけやすく
清潔:ルールと美観の維持
しつけ:決めたことを守る風土づくり
色・形による識別の工夫
ツールの持ち手や収納箱の色をカテゴリで分ける
同じ工具でもサイズごとに色分け
視認性の高い表示材(蛍光色・ピクトグラムなど)
定量管理(数の管理)
必要数だけ常備、多すぎる備品はムダの元
数が減ったら補充される仕組み(カンバン方式など)
持ち出し記録やチェックリストの導入
貸出ボードやQRコードで使用履歴を簡単に記録
使用後は必ず元の場所へ返却する仕組みを周知
小さな改善事例(実際にあったもの)
BEFORE(改善前) | AFTER(改善後) |
---|---|
工具が毎回バラバラの場所にあって探していた | シャドーボードに固定配置+写真付きラベルで即発見 |
材料在庫がどこにあるかわからない | 棚をエリア別・品番別にゾーニング、番地で検索可能に |
部品の箱が全部同じ見た目で探すのが手間 | ラベル+色分けで直感的に取り出し可能に |
工場の現場では、「探す時間=ムダなコスト」です。
「欲しいモノを探す」のではなく、「探さなくても済む状態」を作るのが本当の改善です。
倉庫のロケーション改善
誰にでも住所があるように、またどんなところにも町名と番地があるようにストックヤードや倉庫の番地をロケーションという。モノを保管するには代表的な2種類の方法がある。1つはモノにより保管場所を固定する固定ロケーション、2つ目は保管場所を決めないフリーロケーションである。
固定ロケーション
固定ロケーションは、同じモノは常に同じ番地に保管する方法である。出庫頻度も多く、取扱量も多いモノは、取り出しやすいロケーションに、出庫頻度も出庫量も少ないモノは、奥のほうか高いところに格納する。
長所は、保管場所がいつも同じなので、作業担当者がわかりやすいことである。その反面、生産量や売上の変動が大きいと保管場所が空いてしまったり、不足したりすることが短所である。
フリーロケーション
フリーロケーションは、モノと番地の関係を固定せずに保管する方法である。
人荷したモノを、空いている番地から保管するので、スペース効率よく保管できる長所がある。しかし、これを実現するためには、コンピュータ上でモノと番地を対応させて管理する方法を構築するなどの工夫が必要になる。
保管するモノと保管場所の決定は、以下の原則に対応させて考えるとよい。
・出庫頻度が多く取扱量の多いモノの保管 →一定の固定ロケーションが原則
・出庫頻度が少なく取扱量の少ないモノの保管 →フリーロケ-ションが原則
口ケーションにより管理する目的は、担当者が、可能な限り短い時間でモノの棚入れ、ピッキングができるようにすることである。番地をなるべく探し歩かないよう、番地の振り方も下図のように工夫する。

ロケーション番号 付け方
事務所のレイアウト改善
事務所内のレイアウトも工場内と同様に安全性や機能性を配慮したものでなければならない。事務所のレイアウトを考える場合は、以下のことに注意しよう。
事務所内の標準寸法
下図の①は、人の標準的な寸法である。幅が450mm、厚みが350mmとして通路や机の幅を決定する参考資料にしよう。

標準的な寸法1
①上図の②のように通路の幅は、2人の人がスムーズにすれ違える寸法を確保しよう。また、バリアフリーの観点から車椅子が楽に通れる寸法が望ましい。車椅子が通る際の最小の通路幅は900mmなどである。これらのことを考慮したうえで通路の幅を決定すると1,200mm程度になる。
②机と机の間が通路を兼ねる図6-17の③のような事務所では、十分な間隔が必要である。この場合机間の距離は1,600~1,800mm程度必要になる。机に着席している人の動きによって実際の通路はかなり狭まってしまう。
③「最大作業域」や「正常作業域」を考えて、机の幅と奥行きを決定しよう。また、パソコンの画面との距離に配慮することも大切である。
業務内容と机の配置パターン
事務所内の机の配置については、業務内容にあわせて、いくつかの標準的なパターンが提案されている。
対向式 事務所のレイアウト
1人ひとりが個別のデスクを持つ一般的なスタイルで最もよく採用されている。スペース効率が良く部門ごとの配置がしやすく、コミユニケーションがとりやすいので、総務などの事務系部門に適した配置である。しかし、向かいの作業者と視線が交差するため思考作業には不向きである。
同向式 事務所のレイアウト
視線が交差しないため適度にプライバシーが保てる反面、コミュニケーションがとりにくくなる。また、対向式と比べてスペース効率が悪くなる。
左右対向式 事務所のレイアウト
対向式と同向式を合わせ、視線の交差少なくかっコミュニケーションをある程度とりやすくした配置である。ただし、対向式や同向式と比べてスペース効率は落ちる。
背向式 事務所のレイアウト
1人ひとりが背を向ける配置である。視線は交差せず、振り向けばお互いのコミュニケーションもとりやすいので、デザインや設計など思考作業に向いたレイアウトであるがスペース効率は悪くなる。
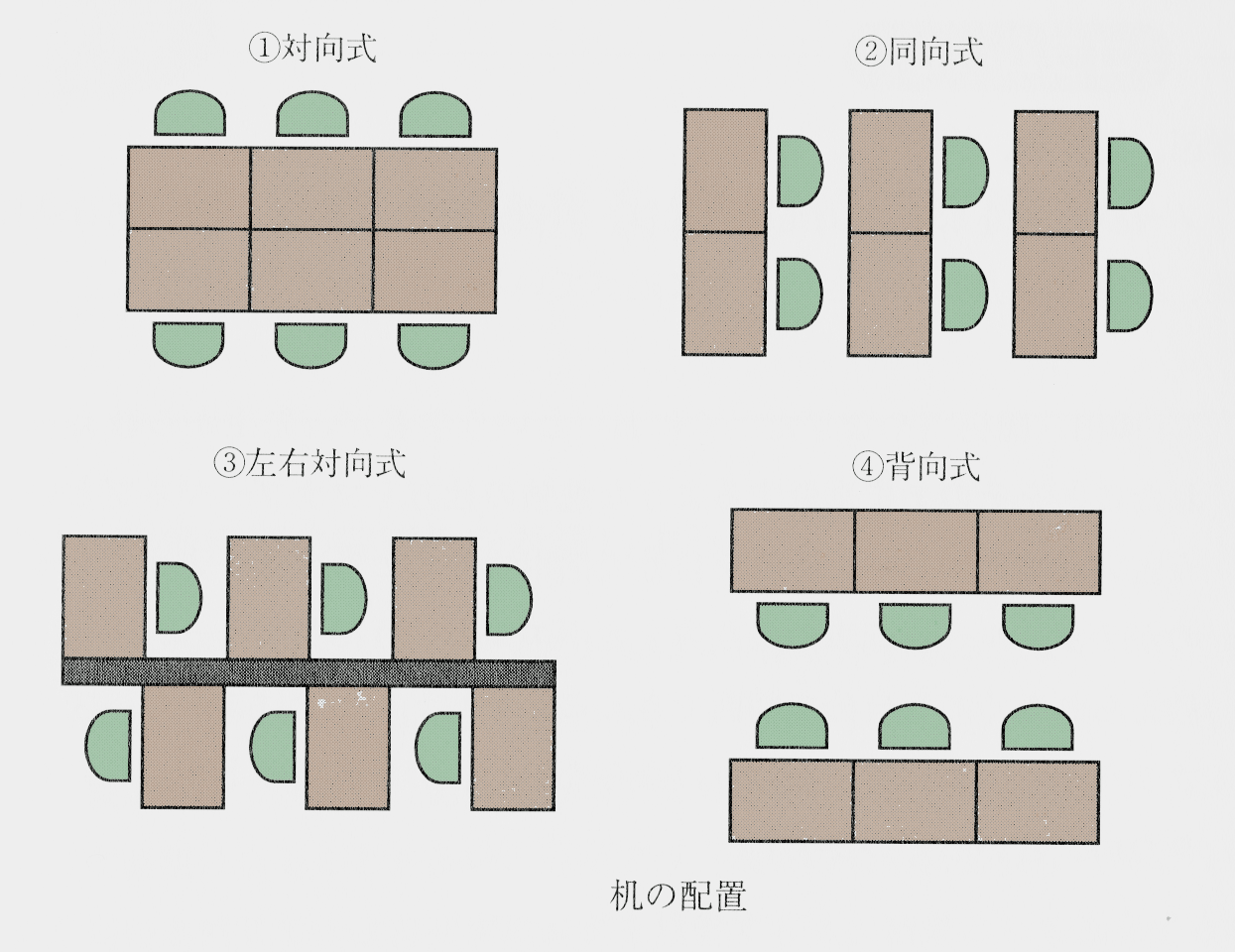
机の配置
*工場のレイアウトについては下記の文献に色々な活動事例等が更に詳細に記載されています。
参考文献:

