レイアウト改善で何が変わる?
運搬、停滞、貯蔵時間を排除できる
材料から製品への流れを表す工程の中で、付加価値を上げている活動は「加工」だけである。
残りの「検査」「運搬」「停滞」「貯蔵」は、付加価値の向上にはつながらず、労務費や経費などの原価のみを増大させている。原価低減や生産性向上は企業の永遠のテーマであるが、付加価値を生まない検査、運搬、停滞、貯蔵は、排除する方向で改善を考える必要がある。
製造工場のなかでも、「材料置き場と機械設備」「機械設備と機械設備」「機械設備と製品置き場」などが離れていれば、運搬距離が長くなり、運搬時間が増大し、運搬による原価増が発生する。
さらに、材料や部品の流れが渋滞し、「加工待ち」「検査待ち」「運搬待ち」などの停滞が発生すれば、製造リードタイムが長期化したり、仕掛在庫が増大したりする。このように工場内のレイアウトがうまく整備されていないと、運搬、停滞、貯蔵が数多く発生し、原価を増大させてしまう。
運搬、停滞、貯蔵を排除するには、レイアウトの改善が必携である。

運搬 貯蔵の排除
製造リードタイムが短縮できる
ある作業を始めてから終了するまでの時間がリードタイムである。個別受注生産の製造業では「受注→設計→調達→製造→納品」までの時間、見込生産では「受注→在庫引当→出荷→納品」までの時間になる。

リードタイム 事例
お客さまの立場で考えれば、欲しいものが欲しい時に欲しいだけ手に入れば、利便性が高まり、購入する可能性が高まる。したがって、作り手はリードタイムを短縮することで、市場の変化に柔軟に対応できライバルや競合他社に対して優位に立つことができる。たとえば、お客さまが要求するリードタイムが2週間、受注から出荷までのリードタイムが1週間であれば、個別受注生産を行うことが可能になる。
製造リードタイムの4つの構成要素
下図のように、リードタイムには「開発リードタイム」「調達リードタイム」「部品加エリードタイム」「納入リードタイム」などがある。
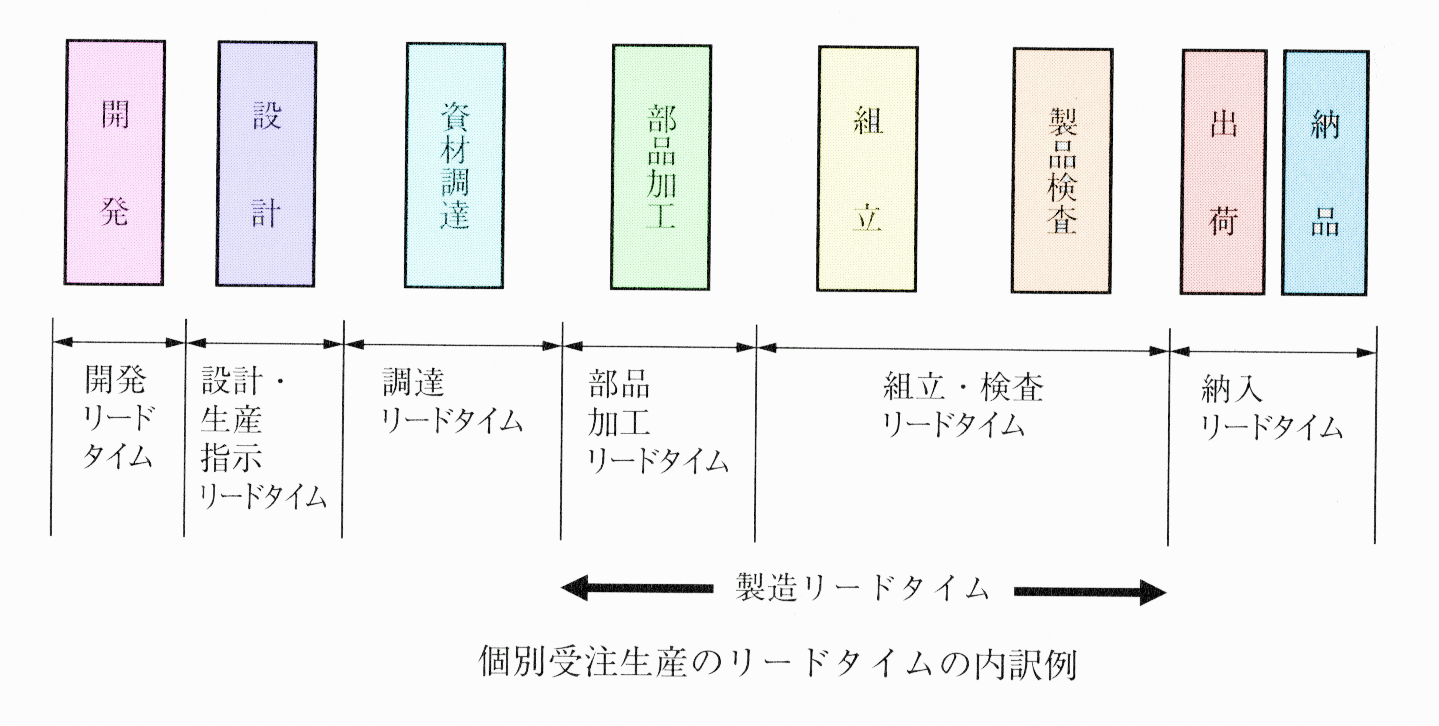
リードタイム
この中の製造リードタイムの中身は、①加工時間、②検査時間、③運搬時間、④停滞時間の4つの要素から構成される。
一般に、停滞時間と運搬時間の改善余地が大きい。
下図は、一般的な機械加工業の製造リードタイムの内訳を示したものであるが、製造リードタイムの中で停滞時間と運搬時間が95%を占めている。

製造リードタイム 内訳
また、加工の内訳を見ると、本来の加工(製品の変形・変質を伴う作業)である基本機能と補助機能(基本機能を補助する取り置きなどの作業)の比率は、基本機能が30%で補助機能が70%である。
付加価値を付けている基本機能は製造リードタイムとの比率で考えると、わずか1.5%をしめるにすぎないので、製造リードタイム短縮のねらいどころは停滞と運搬の改善にあることは、必至である。
製造リードタイムを短縮する 同期化レイアウト
お客さまの必要とするモノ(製品)を素早く作るには、必要なモノ(部品)を、必要な時に、必要なだけ、必要な順に供給する同期化が必要である。そのモノ(製品)を効率的に作るには、加工工程と組立工程が同期化するレイアウトにすることである。
必要なモノを、必要な時に、必要なだけ、必要な順に供給できれば、モノは順調に流れ、停滞やムダな運搬は発生しない。同期化をすることによって製造リードタイムは加工時間だけになる。

一個流し生産 後工程引き取り
運搬のムダが低減できる
製造工場では原料や材料が倉庫に入ってから製品として出ていくまで、付加価値を生まない運搬が行われ、原価を押し上げていることが多い。「材料倉庫から原料をリフトで運ぶ」「棚にある部品を作業場に運ぶ」「製品を製品會庫に運ぶ」などモノを動かす時間と労力は、1円の金も生まないと考えるべきだ。

運搬のムダ
運搬のムダ潰し
「運搬のムダ」とは、文字どおり運ぶこと自体のムダであり、下図に示すつぎのような例がある。
・材料倉庫と機械設備間、機械設備と機械設備間などの距離が長すぎる運搬
・通路が曲がりくねっているために距離が長くなる運搬
・途中に障害物があるために迂回して距離が長くなる運搬
・パレットや容器が空に近い積載効率の悪い運搬
・必要な量を運搬できないために発生する頻度が多すぎる運搬
・目的地まで運搬せずに途中でとりあえずの仮置をする運搬
・仮置きすることなどで発生する余分な積み上げ降ろし作業
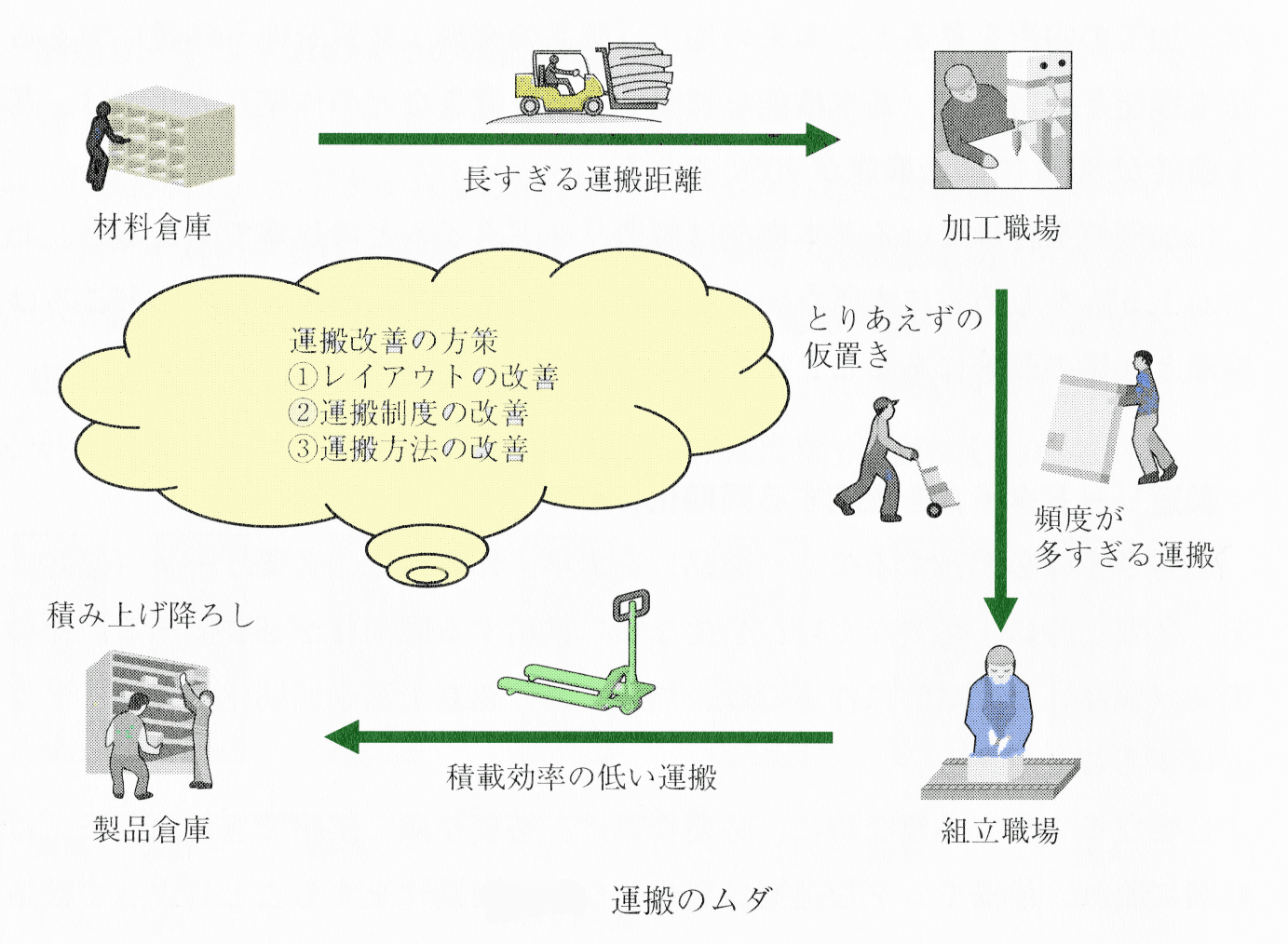
運搬のムダ
これらの運搬のムダを低減する運搬改善には、つぎのような方策がある。
レイアウトの改善
材料倉庫内の原材料や購入部品置き場、工場内の機械設備配置、製品倉庫内の製品置き場などのレイアウトを改善し、運搬距離を最小化する。
運搬制度の改善
効率的な運搬には、運搬制度の改善が必要である。運搬時間は、「運搬距離×回数」で決まるので、一回の積載量、運搬頻度などの標準を設定し、運搬の作業標準を制度化する。
運搬方法の改善
人による手作業を機械化、自動化して運搬作業そのものを楽にしたり、載せ替えしたり、再取り扱いなどの手間を最小化する。
このように運搬のムダは、とどのつまりレイアウトの問題であり、工場のレイアウト改善は、工場内の運搬費を低減する切り札である。また、資材や部品、製品の運搬を総称してマテハン(Material Handling)とよんでいる。
工場改善のコンサルトである新郷重夫(しんごう しげお、1909年-1990年)氏は、著書『工場改善の原点的志向』(日刊工業新聞社 昭和57年1月)の中で、レイアウトについてつぎのように述べられている。
”レイアウト(Lay out)とは、運搬をレイ(零)にして、アウト(Out)にする。
すなわちO -Out にすることである。”
待ち時間のムダや仕掛在庫スペースが削減できる
ファミリーレストランや居酒屋で料理を注文してから出てくるまでの待ち時間、電車の乗り継ぎでの待ち時間、駐車場が満車で駐車するまでの待ち時間など、私たちの日常生活ではいろいろな待ち時間に遭遇する。
待ち時間が長くなるほどストレスを感じるのは、待ち時間に価値を認めていないからであろう。
製造工場では、製品、部品、材料などが、つぎの加工、検査、運搬を行うために一時待ちしている状態を停滞といったが、待ち時間が発生する状況を考えてみよう。
現場で発生する待ち時間
工程待ち
下図のように、ロット生産の工場であるロットが、前ロットの加工、検査、運搬のため、ロット全体で停滞している状態を工程待ちという。
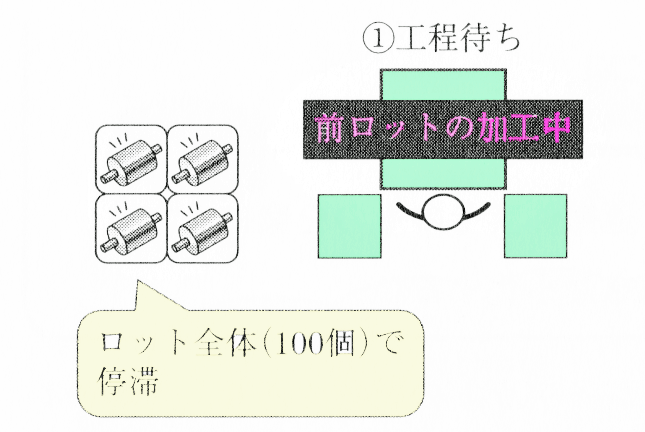
工程待ち
ロット待ち
下図のように、ロット内のほかの製品が加工されているときに生じる停滞の状態がロット待ちである。たとえば、1回のロットを100個で加工している場合、1個目が加工されているときは99個が待ち、2個目が加工されているときは98個が待っている。
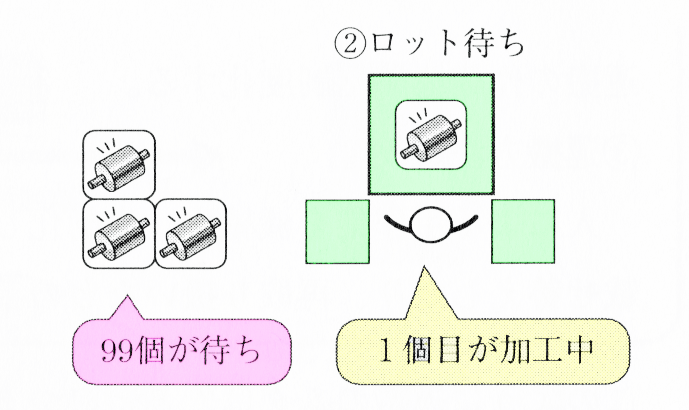
ロット待ち
工程待ちやロット待ちの状態は、組立ラインでも発生している。たとえば、下図のように、組立ラインが数本あり、次工程の機能検査を1台の機能検査器で確認している場合である。組立ラインと機能検査器が同期化していなければ、組立ラインと機能検査器の間にはロット待ちが発生している。
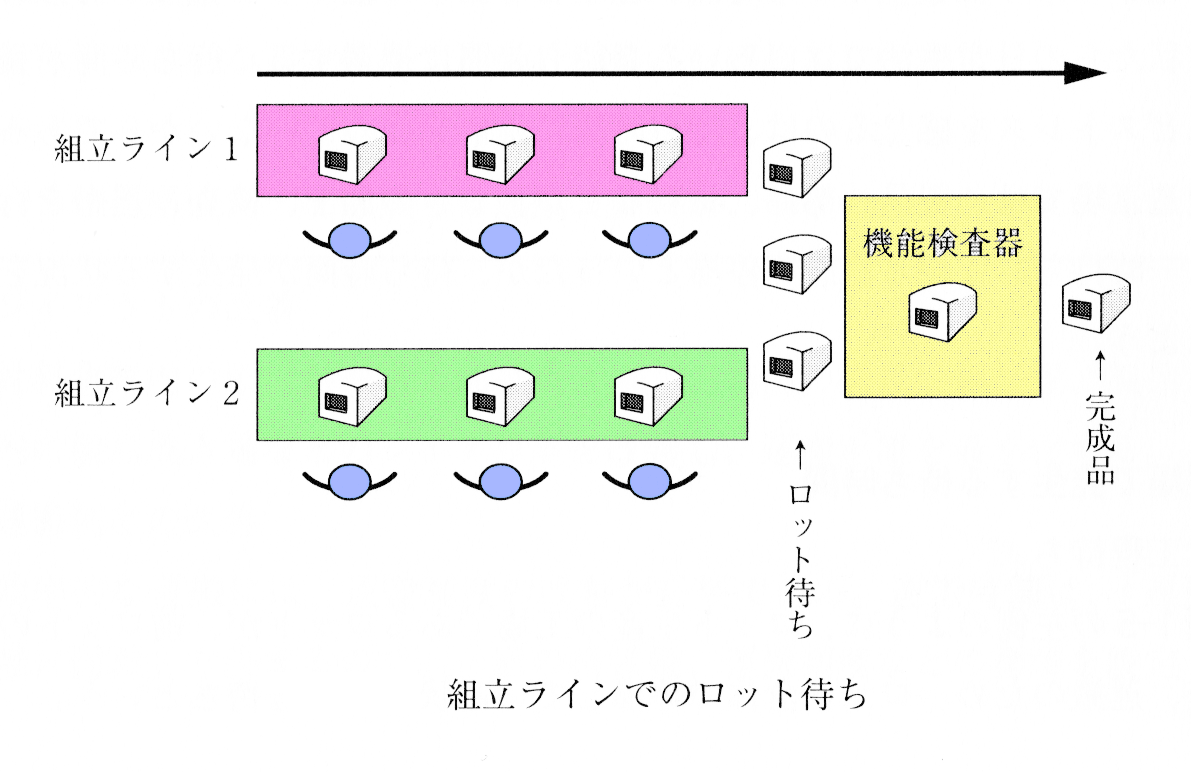
組立ラインてのロット待ち
工程待ち・ロット待ちの悪影響と改善策
工程待ちやロット待ちが発生している職場では下図の上部のように、後工程の機械設備が別の職場や離れた場所に設置されていることが多い。材料や部品をつぎの工程や機械設備に1個ずつ運搬したのでは効率が悪いので、ロット単位でまとめて運搬する。すると工程間の仕掛り在庫が増え、いたずらにモノの取り扱いや保管スペースが増え、製造リードタイムも長くなってしまう。
改善策としては、下図の下部のように、最終工程または一部の工程を連結することである。このようなレイアウト改善により、運搬時間の削減、仕掛在庫の低減によるスペース効率の向上、製造リードタイムの短縮などが実現できる。
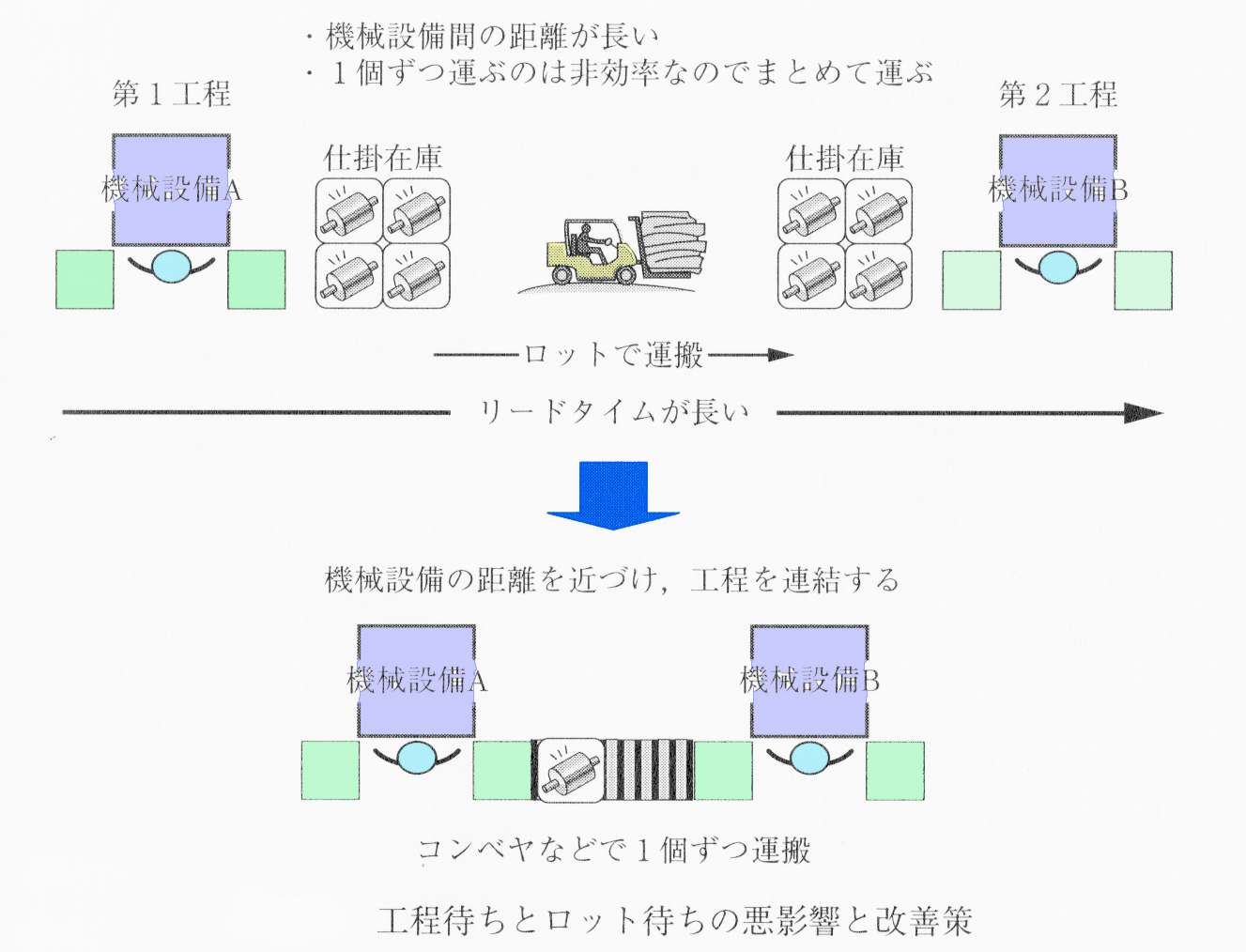
工程待ちとロット待ち 改善事例
加工時間中の手待ち時間が削減できる
工程待ち、ロット待ち以外にも、加工時間中に発生する待ち時間がある。たとえば、下図左側のような1人の作業者が1台の機械設備を使用して加工する工程では、つぎのような状況をよく製造現場で目にする。
・機械設備が自動的に加工している時、作業者は設備を見ているだけ手待ちになっている。
・作業者が仕事をしたくても機械設備が稼動していて手が出せない。
人と機械設備の干渉による手待ち時間
加工時間中の手待ちを見える化するには、下図の下側にある人と機械設備の関係を表わしたM-M(マン・マシン)チャートを利用すると便利である。
黒くぬられた部分が稼慟を表している。
現状のM-Mチャートを見ると、人がA部品を5秒でセットすると、機械設備Aが10秒で加工し、加工終了後5秒でA部品をリセットしている。ここで人の動きに着目すると、黒くぬられた部分(A部品のセット、A部品のリセット)が稼慟を示し、白い部分が機械設備の規制によって発生している手待ち時間を意味している。このような人と機械設備からなる作業で、お互いが干渉し合うことによって発生する手待ちロス時問を干渉ロス、加工時間における干渉ロスの比率を干渉ロス率という。
現状の作業では、A製品1個の加工時間は20秒、干渉時間が10秒なので、干渉ロス率は50%(10秒÷20秒×100)である。
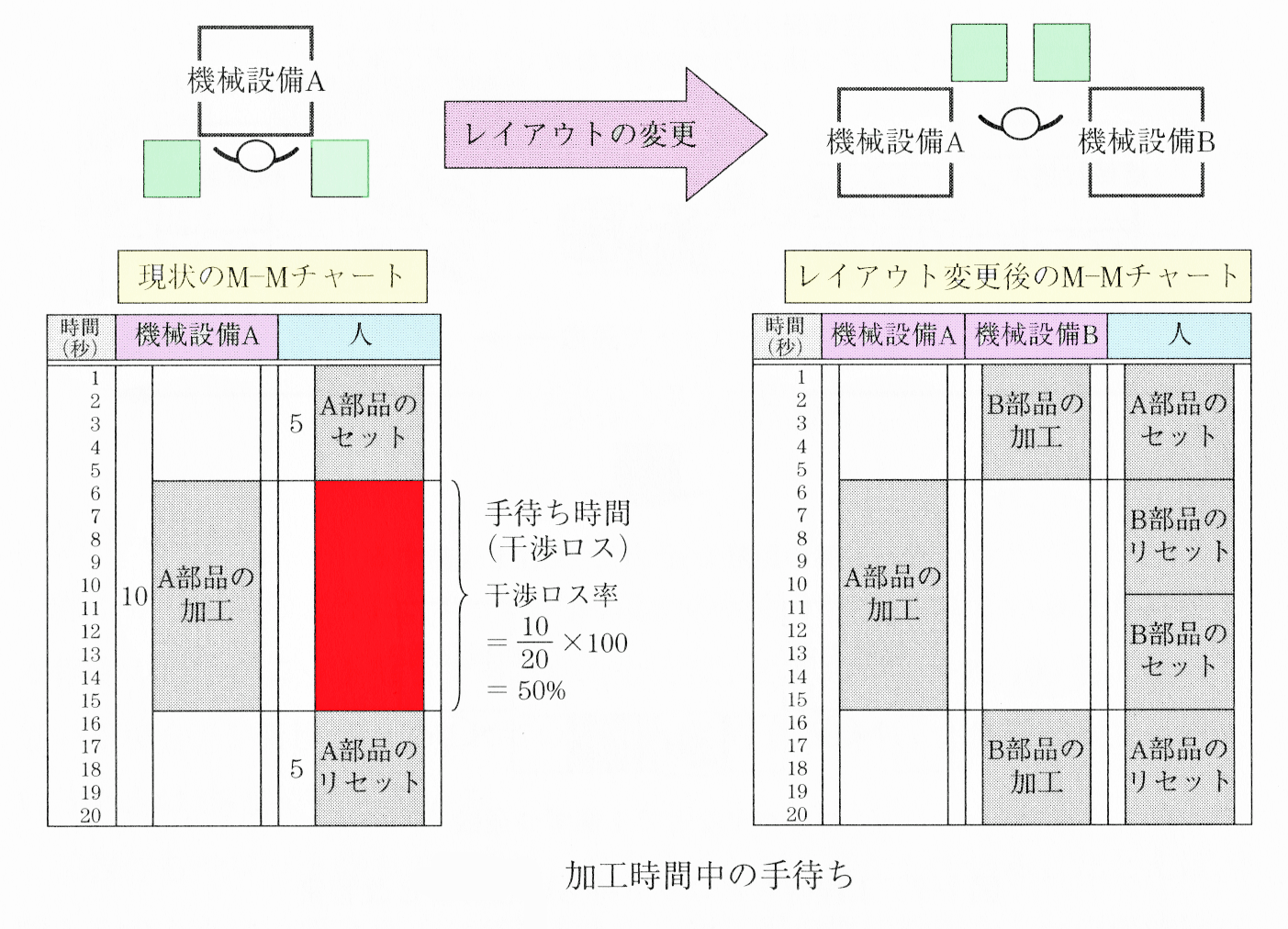
図 加工時間中の手待ち
干渉ロスの低減策
干渉ロスを低減するには、2つの方策が考えられる。
1つ目は、機械設備の作業改善により加工時間を小さくし、干渉時間を少なく改善する方策である。現状10秒かかっている加工時間が5秒になれば、製品1個の加工時間は15秒、干渉時間が5秒なので、干渉ロス率は33%(5秒÷15秒×100)に改善できる。
2つ目は、作業の入れ替えやレイアウトを変えることで、干渉時間を作業に変えてしまう。たとえば、上図の右側のように、1人の作業者が2台の機械設備を受け持つようにレイアウトを変更し、干渉時問に別の作業をする。レイアウト変更後のM-Mチャートを見ると、A部品の加工時間中にB部品をセット・リセットするので、干渉時間がゼロになっている。この改善により、20秒の作業時間でA部品とB部品の加工が完了するので、A・B部品ともに加工時間は10秒(20秒÷2)になり、生産性は倍増している。
動画 工場立地とレイアウト
*工場のレイアウトについては下記の文献に色々な活動事例等が更に詳細に記載されています。
参考文献:
よくわかる「レイアウト改善」の本
小川 正樹 (著)
図解 すぐに使える 工場レイアウト改善の実務
田村孝文 (著), 小川 正樹 (著)