工場レイアウト見取り図 とは
製造工場でのレイアウトは、プラント・レイアウト、工場配置、見取り図 、施設配置(Plant layout)とも呼ばれるが、工場の材料、人、機械設備などの配置を最適化し、最も経済的な製造方式やモノの流れを確立することである。
英語および中国語で工場レイアウトは
工場レイアウトは、英語では「factory layout」または「plant layout」、中国語では「工場布局(gōngchǎng bùjú)」と訳されます。

食品工場 レイアウト
レイアウトを考える7原則
レイアウトに関する共通原則として、つぎのものがある。
生産要素統合の原則
最も経済的な製造方式やモノの流れを確立するには、生産要素の最適な組み、合わせをすることが最小コストを作り出すことになる。生産要素は人(Man)資材(Materials)、機械設備(Equipments)、エネルギー(Energy)の4つである。
工場内の各加工工程間とそれぞれの加工工程において、人、資材、機械設備、エネルギーをうまく調整し、バランスのとれたレイアウトになるようにする。
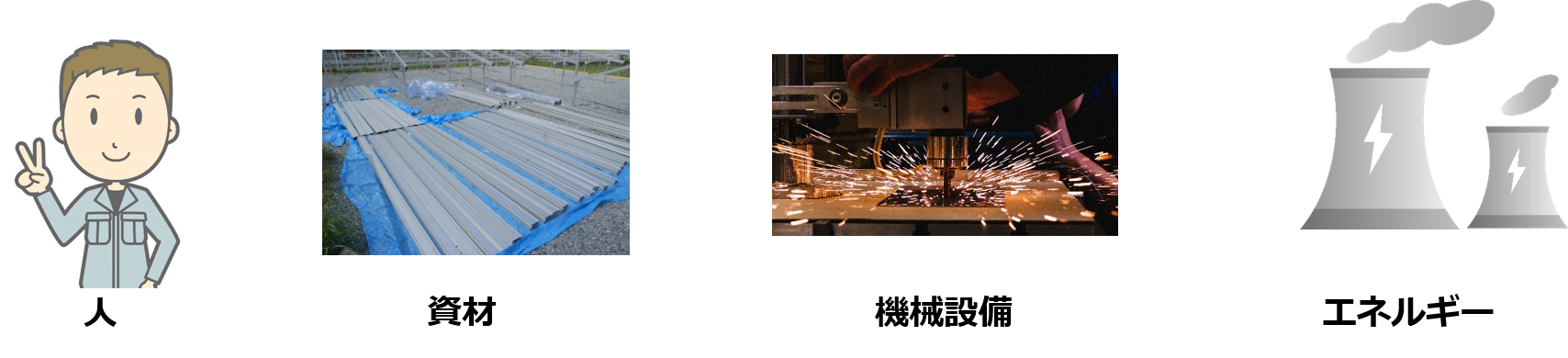
バランスのとれたレイアウト
運搬距離・時間最短の原則
資材や部品、製品の運搬を総称してマテハン(Material Handling)とよんでいる。レイアウトでは、マテハンだけでなく人も含めて移動距離や時間が最短となるよう配慮する。
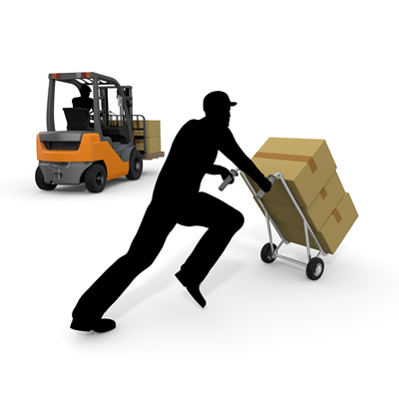
移動距離や時間が最短なレイアウト
スムーズな流れの原則
モノや人の流れは、渋滞や停滞の原因になる交差や逆行がないことが望ましい。加工工程の順序に沿ってスムーズに流れる形式がベターである。

交差 逆行のないレイアウト
3D(スリーダイー)活用の原則
3Dは「Three Dimensions」の略語で、3次元を意味する。レイアウトも、2次元の平面的効率だけでなく、3次元の立体空間の有効活用を考える。

3次元のレイアウト
人に優しい安全と満足感の原則
人間は、自らの満足度が高まることで、関心や視野を広めることができる。
従業員の満足度が高まれば、仕事に関する関心も高まり、未来思考の発想や行動が生まれてくる。従業員の安全性や満足感を高め、人に優しいレイアウトになるよう心がけることで、職場は活性化される。

人に優しいレイアウト
地球に優しい環境の原則
プラント・レイアウトにおいて考慮すべき事項として近年とくに注目されるようになってきたのが、環境への配慮の必要性である。レイアウトにより消費エネルギーや二酸化炭素の排出量を低減する可能性を検討すべきである。
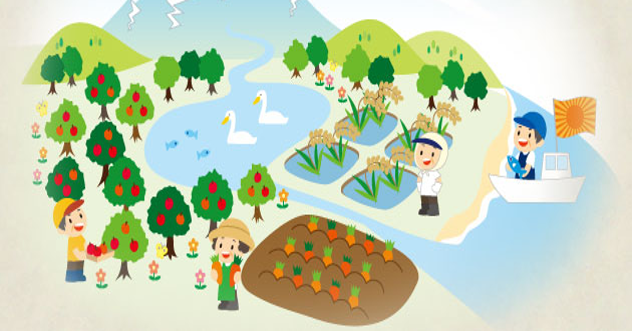
地球に優しいレイアウト
弾力性(フレキシブル)の原則
レイアウトは、生産量の変化、機械設備の更新など将来の状況変化や環境の変化を考え、フレキシブルに変えていくのが得策である。それには拡張や再配置などが最小のコストで実施できるレイアウトにする。
この原則は、レイアウトの対象が事務所、コンビニなどの小売店、病院などであっても応用し適用できる。
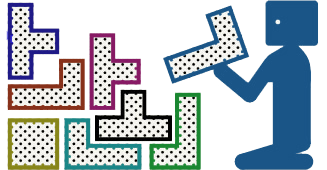
フレキシブル レイアウト

レイアウトを考える7原則
レイアウト、見取り図 改善
改善とは「かえる」ことである。辞書で「かえる」という言葉を引いてみると、変える、代える、換える、替えるなど、いろいろな「かえ方」が載っている。レイアウト改善では、何をかえるのかを製造業とサービス業の例で解説。
製造業の工場レイアウトは「モノの流れ」が中心
製造業における工場レイアウトは、生産効率に大きく影響を及ぼす重要な要因である。レイアウト改善の目的は、工場内の限られた空間やスペースのなかで、最大の効果を発揮する効率的な配置を決定することといえる。
製造業の工場は、レイアウトの観点から装置型工場と組立型工場に分けることができる。
装置型工場は、製鉄、石油精製、セメント製造などに代表されるタイプである。モノの流れで考えると、もしその一部を止めたときには、再開のためにお金や時間を必要とするので、連続した休みは正月とお盆だけという工場も多く見られる。一度配置を決定すると、再配置が難しかったり、できても投資金額が大きいので、最初の工場レイアウトで生産効率は決定してしまう。

装置型工場 イラスト
組立型は、自動車工場、家電工場、精密機械工場などである。ある工程を止めても、一部の作業者、機械設備の稼働率が低下するが、工場全体としては作業の再開も容易である。

自働車工場 イラスト
レイアウトから見た両者の違いは、「運搬の面から見た違い」「保全の立場から見た違い」「人間の面から見た違い」などが考えられるが、順調にモノを流す配置にし、生産効率を上げることは両者共通である。
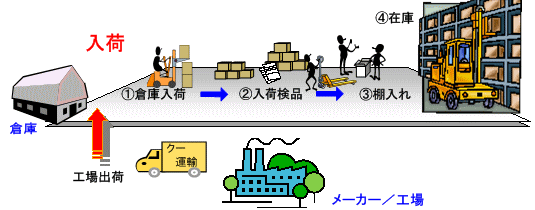
モノの流れ
サービス業のレイアウト、見取り図
サービス業のレイアウトは「人の流れ」や「情報の流れ」が中心、コンビニェンスストア、レストラン、鉄道・航空、銀行、病院などのサービス業は、お客さまに価値のあるサービスを提供するところが特徴です。サービス業の各業界では、それぞれ固有のサービスがあり、サービスを行う施設や設備もさまざまです。
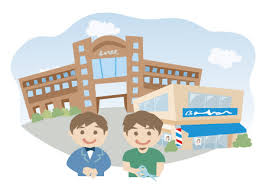
サービス業 レイアウト
サービス業のレイアウトの多くは、一般の製造業とは異なり「モノの流れ」よりも「人の流れ」や「情報の流れ」が中心になる。それは、お客さまとサービスとの出会いをコーディネートすることがサービス業の特徴となるからである。
たとえば、病院には受付、内科や外科、集中治療室、看護師センター、医者のオフィス、患者の部屋などがある。それぞれの部署は人の流れや情報の流れに沿って配置されている。
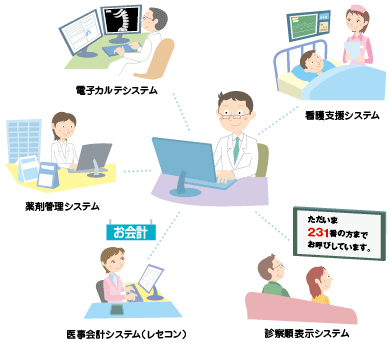
情報の流れ
多くのサービス業では、人の流れを考慮して、道路から入りやすいロケーション、人が歩く道も考慮された駐車場、バーゲンなどのラッシュ時にも対応できる出人り口、自動ドアやエスカレータなどがある。
また、情報の流れでは、ロビーやサービスカウンター、案内図、商品ディスプレイなども必要で、魅力的な装飾や照明なども当然提供されなければならない。
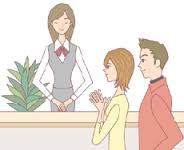
サービスカウンター
家庭内でのレイアウト、見取り図 改善
家庭内の台所が使いやすくなるか検討事例を解説。
使いやすい台所にするための改善項目
台所はかって、日光による食物の腐敗を防ぐため、北側に配置される傾向が強かった。冷蔵庫などの保存技術が発達しても、この傾向は伝統的に受け継がれていたようである。しかし、生活様式が多様化し、リビングやダイニングと一体化した対面キッチンが明るい南側に配置されることもよく見受けられる。
台所は、シンク(流し)、換気扇やコンロ、電子レンジ、冷蔵庫、食器乾燥機などの設備、食器棚、収納庫と作業スペースをから構成されている。使いやすい台所に改善するには、つぎのような項目を検討しなければならない。
・対面式にするか、クローズ式にするか
・コスト的に高価なシステムキッチンなど設備類の選択
・シンク、コンロ、冷蔵庫、電子レンジ、食器乾燥機などの主要設備の配置
・食器棚や収納庫の選定とどこに何をどのようにしまうかの工夫
・明かりの取り方
シンク、コンロ、冷蔵庫、電子レンジ、食器乾燥機などは、レイアウトによって使い勝手が変わってくるので、台所の配置について考えてみよう。
レイアウトによる分類
台所での作業は、切る、温める、まぜるなどの「調理」と食器洗いなどの「後かたづけ」、材料の「貯蔵」がある。調理、後かたづけ、貯蔵に必要な主要設備は、コンロ、シンク、冷蔵庫であり、これらの位置を何処に設置するかで下図に示す台所のおおよそのレイアウトが決まる。
I型レイアウト
I型は、シンク、コンロ、冷蔵庫を直線的に配置したレイアウトである。台所空間を小さくすることができるが、長さが伸びると移動距離が長くなるので、2.7m(一間半)~3.6m(二間)が適度である。

I型レイアウト
Ⅱ型レイアウト
Ⅱ型はシンク、コンロ、冷蔵庫を2つに分け、2列に直線配置したレイアウトである。人の動線は正三角形に近くなり、移動距離は短くなる。

Ⅱ型レイアウト
L型レイアウト
L型はシンク、コンロ、冷蔵庫をL字に配置したレイアウトである。開放的な台所が作れるが、長さが伸びると移動距離は長くなる。

L型レイアウト
U型レイアウト
U型はシンク、コンロ、冷蔵庫をU字に配置したレイアウトである。シンク、コンロ、冷蔵庫は互いに直面し、台所での作業者を中心とした配置となる。

U型レイアウト
人の動線は正三角形に近くなり、移動距離は短くなる。
どのレイアウトを採用するかは、改善の目的により異なってくる。たとえば、台所は使用頻度が多い場所なので、作業効率を優先させれば、U型レイアウトを採用するであろう。
工場でのレイアウト改善のシミュレーション、進め方
工場でのレイアウト改善は、大きく[立地計画][基本レイアウト]「詳細レイアウト」「設置」の4つの段階に分けられる。各段階の概要とポイントを整理してみよう。
下図は、レイアウト改善を進める第1段階から第4段階の関係を示している。レイアウト改善の進め方は、前の段階が完全に終わってからつぎの段階に進むというのではなく、大略決まったところでつぎに進むといった考え方である。

立地計画の流れ
第1段階は立地計画のシミュレーション
工場レイアウトの第1段階は、レイアウトすべき場所の決定である。
工場立地計画の整備
工場の立地計画は、企業の戦略に基づいたトップマネジメントの重要決定項目の1つである。立地計画をするときには、つぎのような「何をいくつ製造してどこで販売するか」という項目がすでに決まっていることが大前提である。
・何を作るか(What):生産品目
・誰のために作るか(Who):お客さまや製品市場 など
・いくつ作るか(How many):品目ごとの生産数量 など
・いくらで作るか(How much):品目ごとの目標原価、投資金額 など
・どのように作るか(How):品目ごとの材料調達方法、製造工程、機械設備、製造条件、概略延べ床面積 など
・いつまでに作るか(When):工場建設納期、回収期間
これらの前提条件が決まったら、工場の立地場所を決定する。いったん工場を設立すれば、その移転は困難であるので、最初から最適の場所を選んで工場を建設しなければならない。
工場の立地を選ぶ要因
工場の立地を選ぶには、その場所が製品を製造するのにほかの場所より有利な条件を持つからである。京浜工業地帯など大工業地帯といわれるものに共通な立地条件は、「交通の便がよく、原材料、製品の輸送に便利である」「人口密度が高く、労働力が得やすい」「情報が得やすい」などである。
工場の立地を選ぶ要因には、「自然的な要因」「経済的な要因」[社会的な要因]の3つがある。
①自然的な要因
自然的な要因には、つぎのような事項が考えられる。
・気象条件が温暖であるか
・敷地の状態(地盤、地形、勾配など)がよいか
・一連のまとまった敷地を確保できるか
・原材料、エネルギー、工業用水が手に入れやすいか
②経済的な要因
経済的な要因には、つぎのような事項が考えられる。
・上地の値段が安いか
・お客さまや製品市場に近いか
・道路が整備され輸送・交通機関が発達しているか
・質の高い人材を集めることができるか
③社会的な要因
社会的な要因には、つぎのような事項が考えられる。
・公共団体の支援やサービスが得られるか
・地域社会や住民との関係は良好であるか
・他工場の理解が得られるか
・治安は安定しているか
複数の立地場所の候補地が決定したら、要因ごとに相対評価で得点をつけ候補地を決定する。立地計画の流れを整理すると、下図のようになる。

立地候補の選択
第2段階は基本レイアウト
立地場所と敷地が決まれば、その土地の形状や特徴などを活かして、敷地内の配置を決定する。使いやすい建屋の配置は、モノや人の流れがスムーズかつ安全であることが望ましい。
敷地の特性を最大限活用して建屋の配置を検討するには、つぎの視点から敷地の特性を見直してみよう。
敷地を最大限に活用する配置
①自然環境と共存する使い方
21世紀の社会のニーズとして地球規模における環境問題がある。こうした事態のもとでは、環境保全型の工場立地政策が求められている。
②道路と敷地との関係をうまく利用する
どの方向で、何メートル幅の道路が面しているかでその敷地の配置やアクセスに影響がでてくる。敷地の一方向しか道路に面していなければ、建屋は道路から離れた場所に配置することになる。
アクセス面では、製品の出荷頻度や出荷量により必要なトラックの台数が予測できる。出荷の待ち時間も考慮するとトラック待ちや駐車スペースがどの程度必要かが把握できる。
③風・雨・雪などの気象条件に対応する
気象条件の中で風と雨は、敷地の配置に影響する。材料の搬人口や製品の出荷口を北側に配置すれば、風が吹き込み作業性も悪くなるであろう。また北国など雪の多い地域では、年間の積雪量が屋根への荷重として計算され、柱や基礎の計算に影響する。
④外観を周囲の環境とマッチさせる
工場の近くの人はもちろん、工場見学に訪れてくる方々に対して、工場の外観がその企業のイメージをよくすることが望ましい。建屋が地域に根ざしたシンボルとなるように、建物の外観を芸術家に依頼する企業も多くみられる。
外観が周囲の環境とマッチした清潔な工場は、「きちんとしたよい工場」であるとわかるものであり、宣伝効果も大きい。
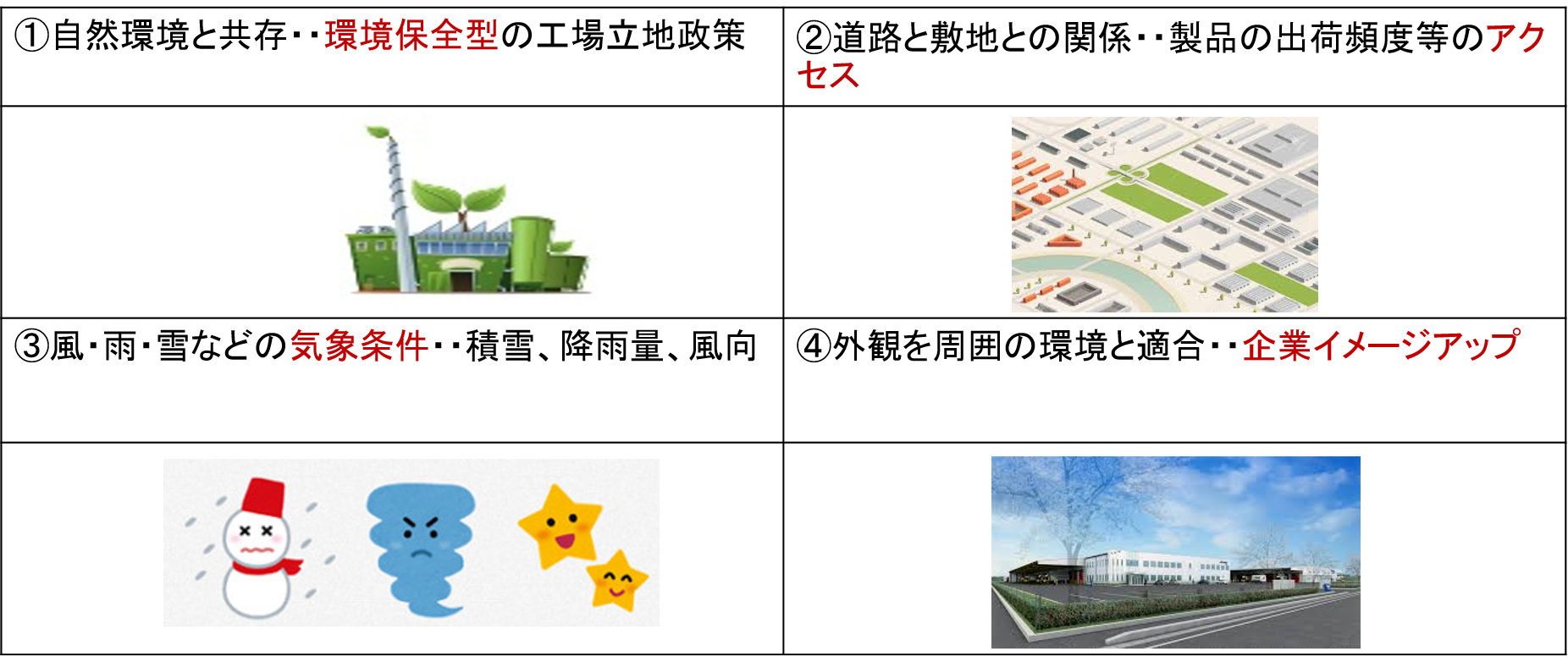
工場基本レイアウト
敷地内の配置をチェックリストで確認
敷地内の配置チェックリストを漏れがないように事前に作成し、確認し製造スペース、倉庫スペース、事務所スペース、食堂スペースなど敷地内の基本レイアウト配置を決定。
また、次章で説明するSLP(エス・エル・ピー:Systematic Layout Planning システマテック レイアウト プランニング)も併用して活用する。
敷地レイアウト チェックリスト | |
項目 | 評価 |
自然環境をうまく使っているか? | |
工場のコンセプトに合っているか? | |
敷地の出入口の数と場所は適切か? | |
モノの流れ、人の動線は最短でスムーズか? | |
建屋の間隔や道路幅は適切か? | |
風・昨雨・降雪・日照などの気象条件に対して適切か? | |
外観は周囲とマッチしているか? | |
道路から見える場所には見栄えのある建屋を配置する | |
ゴミ焼却炉や排水処理は外部から見えない場所に配置する | |
建屋の高さはなるべく揃える | |
エネルギーの配口は最短になっているか | |
将来の拡張に対して対応が収れるか | |
関連法規を満たして配置されているか |
第3段階は詳細レイアウト ~職場レイアウト改善
建屋の配置が決まったら、つぎはその中に職場をどう配置するかを検討する。
「騒音の大きな機械加工職場の隣に事務所がある」「職場間の運搬距離が長い」「機械設備の配置変更や移動に手間がかかる」などは、建屋内の職場レイアウトを見直す材料である。
建屋内の職場を配置方法としては、敷地内のレイアウトでも活用するSLP(エス・エル・ピー:Systematic Layout Planning システマテック レイアウト プランニング )が役に立つ。
SLPは、工場レイアウトの標準的な手法であり、あらゆる業種、業態の工場にも適用できる。
SLPにより複数の職場レイアウト案を作成することができる。
ライフサイクル(LCC)の評価
「より少ない投入量(インプット)により、より高い産出量(アウトプット)を得たい」という考え方が、生産性の基本的考え方である。職場配置案も同じ生産量を製造するなら、一番費用(コスト)が少なく製造できる案が一番生産性の高い案になる。
工場建設から始まる工場のライフサイクルで発生するコストについて考えてみよう。
工場のライフサイクルは、
1)工場を建設する段階
2)工場を使用し製品を製造する段階
3)工場を廃棄する3段階に大別できる。

工場のライフサイクル コスト
各段階で発生するコストをライフサイクルコスト(LCC)とよぶが、その内容についてつぎに述べる。
1つ目は、工場建設の段階である。ここでのコストは、上地取得コスト、建設コスト、機械設備取得コストなどであり、イニシャルコスト(初期費用)とよぶ。
2つ目は、製品を製造する段階である。ここでのコストは、物流コスト、職場再配置コスト、機械設備再配置コスト、空調コスト、保全コストなどであり、ランニングコストとよぶ。
最後の3つ目は、工場を廃棄するときの廃棄コストである。
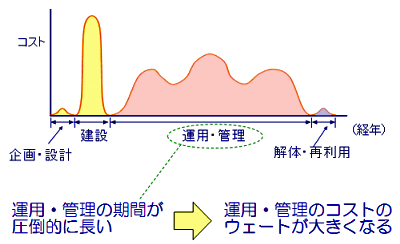
ライフサイクルコスト1
ライフサイクルコスト(LCC)で金額の大きいのは、イニシャルコストとランニングコストであり、同じ生産量を製造するなら両者の合計が最も安いレイアウト案を選択する。物流コストの最小化だけに目がいくと、ライフサイクルコストを最小化するレイアウト案を見逃してしまうので、注意したいものである。
快適な職場になっているか
従業員が疲労やストレスを感じることが少ない快適な職場配置を作ることも大切な評価項目である。たとえば、製造現場で騒音源となる機械設備については遮音材を用いたり、事務所から離れた配置にしたりするなどである。
また、作業に従事することによる疲労の回復を図るための施設として休憩室や厚生施設も職場の近くに配置したいものである。
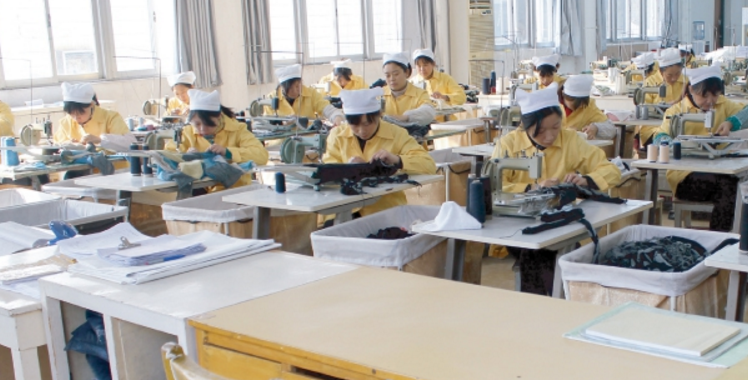
快適な職場
第4段階はレイアウト設置、移動
工場レイアウト改善の最終段階は機械設備などの移設計画の立案、移行準備、設置、移動です。
計画を立てる人の経験が不足していると移設に必要な全てのアクション項目(仕事やタスク)を移設計画に網羅できないことがあります。
移設計画(Plan)は、単なる完成予定日ではなく、必要な実施項目を全て網羅しているか確認する必要があります。また、移設途中(Do)でいくつかのチェックポイント(Check)を設置し、その時点、時点で進捗を確認し、必要であれば修正(Action)を行って、PDCAの管理サイクルを回すことが重要です。
ガント・チャートで日程管理
移設計画の日程管理に便利な道具としてよく知られているのが、下図の「ガント・チャート(横線工程図)」です。
ガント・チャートは横軸に日程(期間)を取り、「基礎工事」「骨組組立」「建具取り付け」など必要な各実施項目の開始から終了までを一本のバー(横棒)で表わし、計画項目をわかりやすく表示します。
この方式は、作成も簡単で、実施項目が分かり易いので、現在でも愛用されております。
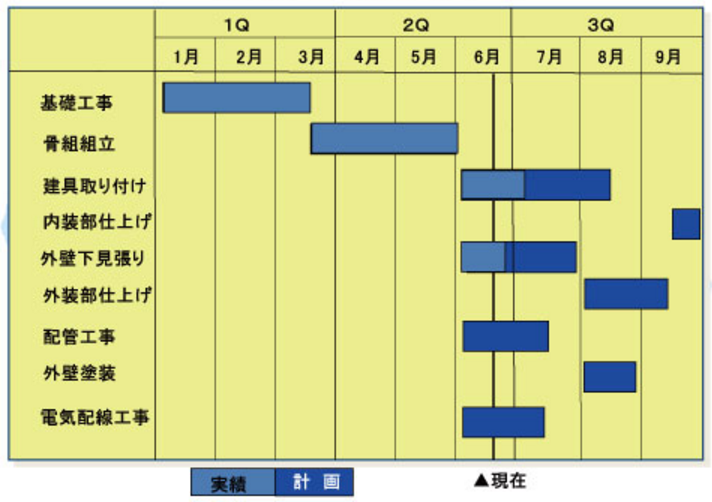
ガント・チャート
作業環境の安全性向上の為のレイアウト
作業環境の安全性を向上させるための工場レイアウトの設計は、事故の防止、生産性の向上、作業員のストレス軽減など多くの面で重要です。以下の観点からレイアウトのポイントをまとめます:
基本的な考え方
安全性は確保できているか?
事故が起きない製造現場になっているかの評価項目である。工場内の作業場、通路、在庫置き場などの区分けを明確にする、ロボットアームの移動範囲や機械設備の稼働範囲には囲いを設けるなどをレイアウトに組み込む必要がある。
下記が評価項目である。
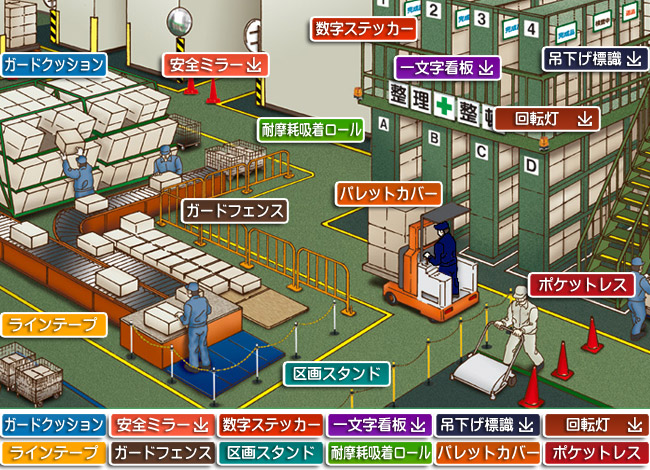
安全の確保
動線の最適化
人の動線と物の動線を分ける(交差しないようにする)
無駄な移動や混雑を防ぐ配置にする
視認性の確保
コーナーミラーの設置や死角の排除
明るい照明・危険エリアの色分け(例:床にラインを引く)
安全機器の配置
消火器・非常停止スイッチ・防護柵などを適切な場所に設置
緊急時にすぐ使えるようにする(視認性・アクセス性)
作業エリアの区分け
危険作業エリアと一般作業エリアを明確に分離
高温・高音・有害物質使用区域には立ち入り制限・換気システムを整備
余裕のあるスペース設計
通路は作業者2人がすれ違える幅(一般的に90cm以上)
機械周辺にも点検・保守作業ができるだけの空間を確保
実際の改善例
フォークリフト vs 歩行者の動線分離
→ ゾーンを色で区分け、フォークリフト用の専用通路設置作業台の高さ調整
→ 無理な姿勢による腰痛防止、長時間作業でも疲れにくい配置に視認性の悪い場所にミラーを設置
→ 工場内での接触事故防止
工場レイアウトの種類
製品別レイアウト(Product Layout)
流れ作業に向いている。生産効率は高いが柔軟性は低め。機能別レイアウト(Process Layout)
同種の機械をまとめて配置。多品種少量生産に向いている。固定位置レイアウト(Fixed Position Layout)
大型製品(船、航空機など)で、作業員や機械が移動する形式。
安全性を考慮した設計プロセスのステップ例
現状分析(ヒヤリハット報告や事故履歴の確認)
危険個所の洗い出し(リスクアセスメント)
レイアウト変更の検討(動線設計、機器配置見直し)
作業者との意見交換(現場の声を反映)
試験導入 → 検証 → 本格導入
工場レイアウト 改善後の成果と評価
工場レイアウトの改善後の成果と評価については、定量的・定性的な視点の両方からまとめると説得力があります。以下に一般的な構成例を示します。
生産性の向上
改善前: 生産ラインに無駄な動線が多く、作業者の移動時間が長かった。
改善後: 作業工程の順序に沿ったレイアウトに再構築したことで、移動距離が約30%削減され、作業効率が大幅に向上。
成果: 生産性が15%向上、1日あたりの生産量が1,000個から1,150個に増加。
作業環境の改善
改善前: 材料や仕掛品の置き場が分散しており、作業場が混雑。
改善後: スペースを有効活用した配置に変更し、通路幅の確保と整理整頓を徹底。
成果: 5S評価が向上し、安全性も改善。作業員からの満足度も上昇。
リードタイムの短縮
改善前: 材料の搬送に時間がかかり、停滞が頻発。
改善後: 必要な材料や部品を近くに集約するレイアウトに変更。
成果: 工程間の停滞時間が平均20分から8分に短縮。リードタイムが25%削減。
在庫の適正化
改善前: 過剰在庫が発生し、保管スペースも逼迫。
改善後: ラインサイド在庫の最適配置と定量管理を導入。
成果: 在庫回転率が向上し、在庫量が約20%削減。
定性的な評価
作業員のストレスが軽減され、チームワークが改善された。
品質トラブルが減少(不良率10%減)。
見学者や顧客からの評価も向上(整然とした印象、管理が行き届いていると高評価)。
倉庫・ストックヤードのレイアウト改善
原材料や供給部品、仕掛品、製品などの保管方法は、工場全体の生産性に大きな影響を与える。たとえば、倉庫に部品をとりに行った際、「保管場所がわからない」「一定の場所に置かれていない」「部品はあるが取り出せない」などの状況が発生したら、原材料や部品などの保管方法や倉庫のレイアウトを見直すチャンスである。
倉庫内の流れを最短化
倉庫内の業務には、材料・部品を受け取り、確認・分類、保管場所への運搬、人庫、保管、出庫、保管品のピッキング、梱包、出荷などがある。材料・部品の受け取りから出荷までの倉庫内の業務は、最短距離を動くような流れになっていることが理想である。業務がスムーズに流れるように、保管場所、作業台、出荷場所などの配置を設定する。

倉庫 モノの流れ
ピッキング効率を上げる保管場所の設定
品目の保管場所や棚を決める際、品目ごとや品目番号の順番で決める方法もある。しかし、ピッキング作業の効率を考えると、品番順で保管場所を決める必要はない。
入出庫の回数や品目数が多い場合は、ABC分析の結果により配置するレイアウトを検討する。 ABC分析は下図のように、縦軸に出庫金額横軸に品目を出庫金額の大きい順に並べ、A、B、Cの3ランクに分ける。
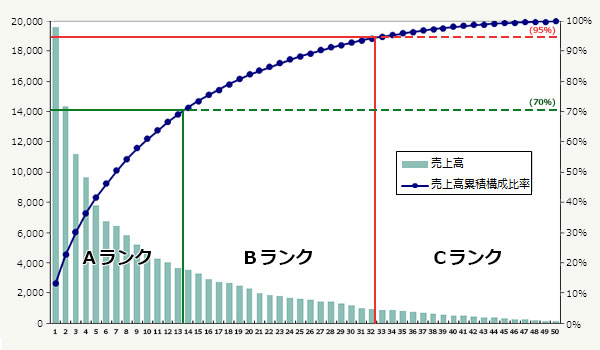
ABC分析
ランクごとの保管場所とピッキング方法の考慮点が以下である。

ABC分析-ランク分け
Aランク品 ABC分析
入出庫頻度が高いAランク品は、効率を高めるために、出荷口に近い場所に保管場所や棚を配置する。誤出荷やピッキング作業の効率のために、出荷指示書のバーコードを読み取るとピッキングする部品棚にランプがつきピッキング数量も表示するデジタルピッカーなどの機器も利用する。
Bランク品 ABC分析
Bランク品は、トータルピッキングが向いている。 トータルピッキングは、オーダーを同一部品ごとに集計し、ピッキングリストにしたがって部品ごとの総量でピッキングし、出荷先ごとに分ける方式である。保管場所はAランクについで入出庫しやすい配置である。
Cランク品 ABC分析
Cランクは、頻度が少ないし数量も限定されているので、シングルピッキッグが向いている。シングルピッキングは、オーダー単位に各商品をピッキングし、1つの出荷単位にまとめ、出荷場に揃える方法である。
レイアウト計画の注意点
レイアウト計画の注意点としては、通常時の作業だけではなく、ピーク期の作業に支障がないかどうかを考慮する必要がある。たとえば、品目や取り扱い数量が増えた場合の一時保管場所や作業スペースの確保などがある。
作業域内のレイアウト改善
作業現場で一部の機械設備が切り離されて配置されると移動距離を長くする。
機械設備と機械設備の距離を短くすることで運搬のムダ、手待ちのムダをなくすことを重要である。
人の動作の標準時間
人の動作の時間については、既定標準時間設定手法「PTS法(predetermined time standard system))が開発されている。 PTS法の中で最も代表的な手法は、MTM(methods-time measurement)法とWF(Work Factor)法で、作業を細かい動作(歩く・手を伸ばす・移動するなど)の大きさに分解し、時間値を規定している。
足の移動 MTM法
MTM法では、歩行1歩で約0.5秒の時間がかかると規定している(図2-8参照)。 10歩手ぶらで歩くと約5秒のムダが発生するのである。
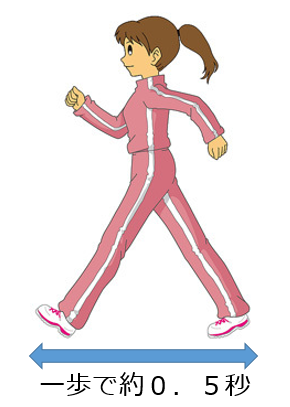
足の移動時間
手の移動 MTM法
決まった位置に30 cm 手を伸ばすと約0.34秒、20 cm では約0.28秒かかるとMTM法では規定している
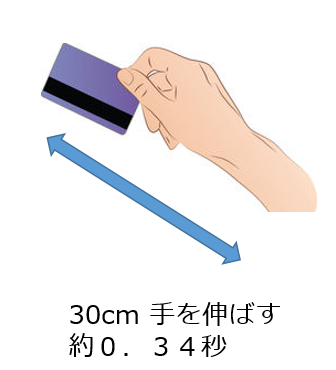
手の移動時間
レイアウト改善で移動距離を30cmから20 cm に10 cm 短縮すると作業時間は1回あたり0.06秒(0.34-0.28)低減できる。
たかが0.06秒なのでたいした改善ではないと思うのは、早合点である。 0.34秒に対する低減比率は17.6%(0.06÷0.34×100)になるので、この改善で生産性が約18%向上するのである。
作業域内でも、「部品箱を近づける」「工具の位置が高すぎないか見直す」「スィッチの位置を見直す」「操作レバーの作業距離を見直す」などのレイアウト改善を織り込むことが大切になる。
動作経済の原則
人の疲労を最も少なくして、人間のエネルギーを効率的に活用して有効な仕事量を増すための原則が動作経済に関する原則である。
この原則は大変有効なので、「配置および設備に関する原則」をつぎに紹介する。この原則をチェックリストとして活用し、レイアウト改善に役立てよう。
<配置および設備に関する動作経済の原則>
口 工具や材料は作業習慣が形成されるように定位置に置く
口 工具や材料は作業者の周辺のできるだけ前面近くに配置する
ロ モノの移動には上下移動をさけて水平移動にする
ロ モノの移動には重力を利用する
口 材料や工具は動作に最も都合のよい位置に置く
口 歩行のない作業では作業者にはできるだけ椅子を与える
口 机と椅子の高さは作業者の性質や作業者の身長に適したものとする
口 作業者の性質に適した採光や照明を与える
事務所でのレイアウト改善
工場内のレイアウト改善に比べて、事務所のレイアウト改善となるとさほどの関心も示さない人が多いようである。営業部門や管理間接部門の事務所レイアウトは、それぞれに管理者や監督者を中心に机が配置されている。
どこの机に何を配置するかは、過去の習慣や声の大きい人の意見で決められており、特別な根拠が存在しない例が多く見受けられる。
事務所のレイアウトも製造現場と同じように、書類の動きによっては事務の停滞が発生し作業能率に影響する。また、事務所のスペースを有効活用しているか、事務所で働く人が気持ちよく働けるかどうかという問題にも関連してくる。事務所でのレイアウトが原因となるさまざまな問題に気付いていないケースは意外と多いものである。
事務所のスペース拡大に役立つレイアウト
労慟安全衛生法の規定に基づく事務所衛生基準規則では、1人あたりの事務所スペースについて、「設備の占める容積及び床面から4mをこえる高さにある空間を除き、10 ㎥以上」と定めている。事務所の天井高の標準が2.6~2.7mであることから、1人あたりの床面積は4㎡以上と考えている。

事務所 レイアウト 事例
1人あたりのスペースの広さは、作業者の仕事の満足感や生産性に影響することが知られている。1人あたりのスペースを拡大することは望ましいが、コスト高になるので、多くの企業ではスペースの有効利用を図っている。たとえば、外出や出張などが多い部門で作業者ごとへの固定机の割当を廃止し、ノート型のパソコンと共用机を用意することで、1人あたりのスペースを拡大するのである。
このスペースの共用化という発想はフリーアドレスと呼ばれている。
事務所のスペース拡大に制約が多い企業にとっては、生産性の向上とコスト低減、さらには実質的な1人あたりのスペース拡大になる有効な対応策の1つである。
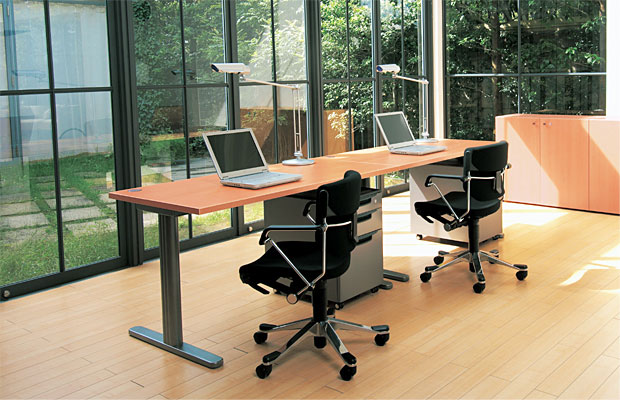
事務所 スペースの共用化
事務所レイアウトの改善ポイント
事務所のレイアウトはその主体がスペース効率の向上だけでなく、仕事をする人のための環境作りも考慮しなければならない。この点に焦点を合わせた次に述べる改善ポイントを考慮して計画してゆく。

事務所 レイアウト例
*工場のレイアウトについては下記の文献に色々な活動事例等が更に詳細に記載されています。
参考文献: