5S活動の ツール
赤札作戦~整理対策~
赤札作戦とは赤い札を使用して工場内の5 Sが守れていない設備、箇所等に赤い札を張り整理するやり方である。
整理は直ぐには判断しにくいので不要と思われるモノに赤札をつけて整理する候補を選ぶ。
・対象品:在庫品・・・・仕掛在庫、部品在庫、原材料在庫
・機械設備・・・台車、パレット、冶具、工具、椅子、備品
・スペース・・・床、通路、棚。
そして不要なモノと思われるモノに赤札をつけてから下記のように処理をする。
①即時、廃棄する。
②一定期間保留⇒迷い箱、遊休設備置き場に置く
③使用する⇒所定の位置に置く
会社の「アカ(「垢」)を表にする
会社では、自分の身の回りにあるものが、日々の業務活動に必要なモノかどうかの見きわめが非常に困難です。
そこで、目で見る整理の方法の1つでもある「赤札作戦」が登場します。「作戦」というからには敵が必要で、もちろんここでの敵は、自らがまいた「ムダ」とか「アカ垢)」ということになります。
しかし、会社の中でアカを見つけることは職場の社員でもむずかしいものです。どの在庫が現在の生産に必要なモノか、または不要なモノかがひと目ではわかりにくいのです。まして、職場を留守にしがちな社長や部長には、皆目見当もっきません。
まず、会社の中のアカを浮かび上がらせて、かつ社長でもどれが要るモノで、どれが要らないモノか、目で見てわかるようにすることが大切なのです。
このために、「赤札」が必要になるのです。
要・不要の判断は時間軸
不要と思われるモノに、どんどん「赤札」を貼っていきます。会社の中が真赤になるくらい徹底して貼っていきます。
なぜ赤い紙を使うのでしょうか?目立たせることと、会社の「赤信号」、それに会社の「アカ」、洋品屋さんなどで年末に行う現品処分の「赤札市」などを連想させることから赤い紙を採用しています。
また、赤札を貼るかどうかといった基準は、業種や対象物ごとに異なってきます。生産現場などでは普通、先1ヵ月の生産計画の中で使わないモノにはすべて赤札を貼ります。少し厳しい現場になると、基準を1週間単位とするなど、状況に応じて基準を決めています。
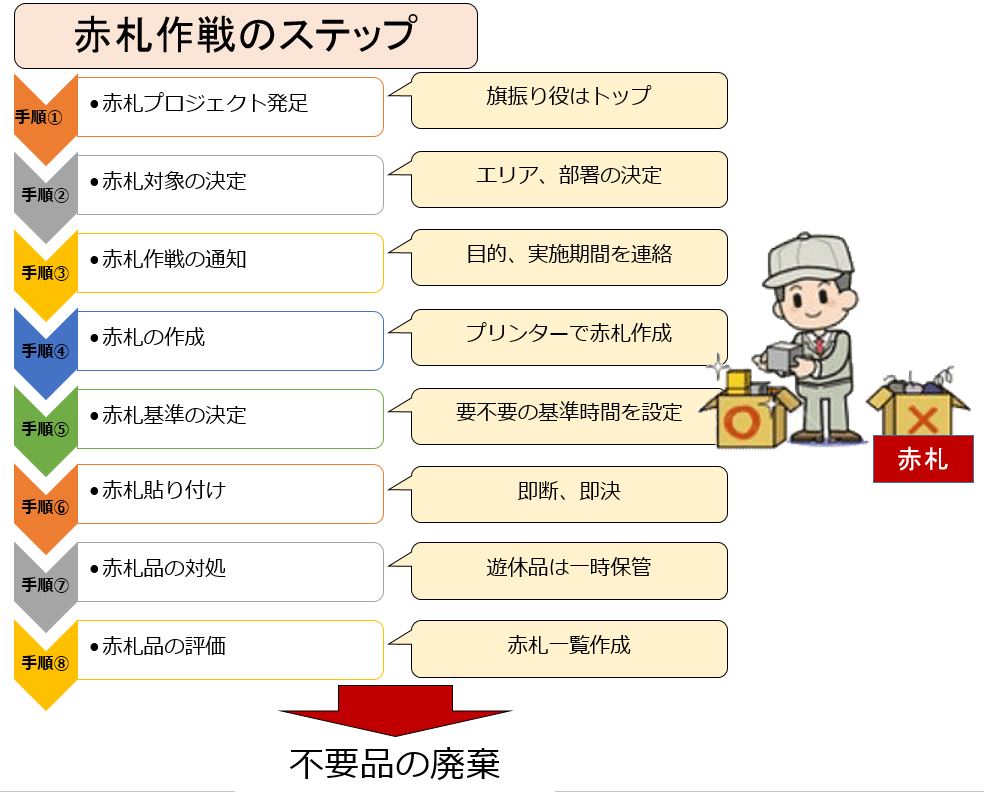
赤札作戦
『赤札作戦』の推進体制の構築
赤札作戦の最高責任者はトップがなるのがベストです、 赤札作戦は、日々コツコツと実行するのが望ましいのですが、どのような会社でも、年に少なくとも1~2回は会社総ぐるみで、赤札作戦を実施することが必要です。
会社の企業活動の期間として、半期決算、年度決算などがあります。そこで在庫などの棚卸しを行い現状を把握しますが、その前に赤札作戦を実行します。この時にただ職場まかせで行うのではなく、「赤札プロジェクト」を立ち上げます。このプロジェクトの最高責任者は、社長あるいは担当役員、事業部長などがなります。
赤札作戦の対象品の決定
赤札作戦とは「要るモノと要らないモノを、誰が見てもハッキリとわかるようにする」ことです。これは会社全体にはびこっているアカを、浮き出させることなのです。アカは年数が経てば経つほど蓄積され、思わぬ所にも濳んでいます。
はじめて「赤札作戦」を実行すると、まずは大モノなど目につくモノから始まり、続いて中モノ、小モノといった順に要らないモノが次々と出ます。
そこで、対象品を見てみると、営業や経理、総務などの事務・間接部門であれば、要らない文書資料、机、ロッカー、文房具、カタログ、名刺、見積書などが対象となります。
また、製造部門であれば、在庫、設備、治具、工具、刃具、棚、スペースなどです。在庫は、大きく倉庫在庫と仕掛り在庫とに分けられます。倉庫在庫は、原材料在庫、部品在庫、製品在庫などが対象となります。
このようにして赤札品を見つけるにあたっては、大きく2つの見方があります。1つは[モノという対象品]に対して赤札品を見ていくやり方です。もう1つは、「職場の対象範囲」を絞って端から端まで見ていくやり方です。
倉庫などは在庫などの「対象品」を分けて赤札品を洗い出す方法が多く、職場などは「職場範囲」を絞って赤札品を洗い出す方法が多く行われます。
赤札対象品 製造、物流部門
項目 | 不要品 |
在庫 | 原材料、購入部品、加工部品、仕掛品、組立品、半完成品、製品 |
設備 | 機械、設備、車両、運搬具、作業台、キャビネット |
治工具 | 治具、工具、刃具、測定具、金型 |
スペース | 床、通路、作業区、壁、棚、倉庫、部屋 |
赤札対象品 事務、間接部門
項目 | 不要品 |
資料 | 議事録、業務報告書、稟議書、見積書、契約書、覚書、社内規定、経営資料、営業資料 |
機器 | コピー機、パソコン、プリンタ、ファクシミリ、電話 |
文房具 | ボールペン、マーカー、ハサミ、定規、ホチキス |
備品 | フォルダ、バインダー、キャビネット、ロッカー |
其の他 | 名刺、伝票、カタログ、パンフレット、本 |
赤札貼り付け基準は時間軸
赤札作戦で誰もが迷うのが、どんな基準で赤札を貼るのかです。「要るモノ」と「要らないモノ」を誰が判断してもわかるように、どう切り分けるかです。
それでは、何を基準に「要るモノ」か[要らないモノ]か判断すれば良いのでしょうか。
それは誰もが同じ立場に立って判断でき、抽象的な判断にならないもので、一般的には生産計画をもとに、先1ヵ月とか先1週間といった期間で、要るモノと要らないモノを区分けします。
この判断基準をあいまいにしたり、甘く設定してしまうと、赤札作戦は失敗に終わります。予想以上に赤札品は出てきません。したがって問題もオモテに出てこなくなってしまいます。本来問題を表面化させるべき作戦なので、基準設定の際には、思い切って基準を短く設定すべきです。
当然のことですが、先1ヵ月よりも先1週間の基準の方がきびしくなります。普通の工場で先1週間の生産計画で使わないモノに赤札を貼ると、工場の中はほとんどのモノが赤くなります。業種や業態にもよりますが、先1ヵ月からスタートするのが良いです。
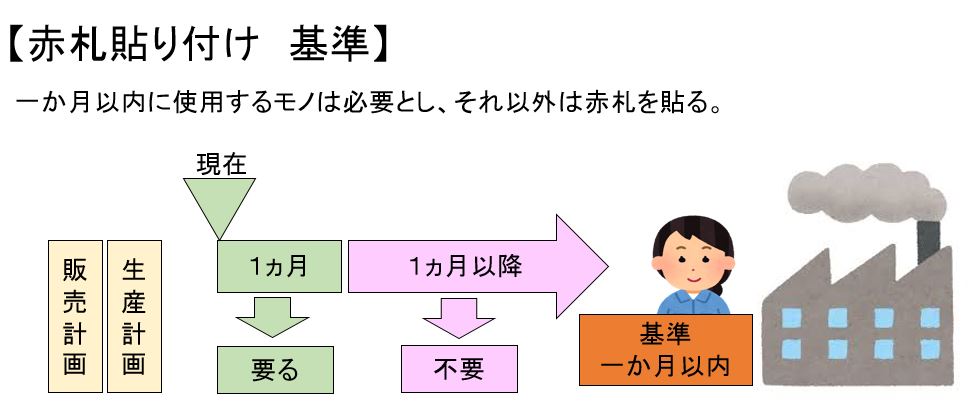
赤札貼り付け 基準
赤札 貼り付け基準 モノの量で判断
材料在庫の基準設定の際には、在庫のデータ一覧を作成し、過去の使用数とデータ上での在庫数を見比べ基準設定をあらかじめ行っておくことです。また、その際に材料の購入ロット数や納入リードタイムも合わせて調べておかなくてはいけません。
治工具、チップや予備品などは、現場まかせになってしまっている場合が多く、安心感のためか意外に多く抱えてしまっていることがあります。現場で赤札を貼りつけながら、その都度、現時点で使うか、使わないか判断し、その場で赤札品として除き、「赤札コンテナ」などを決め、回収して回る方法が有効です。
赤札の作成
実際に貼りつける「赤札」ですが、とにかく赤色で目立つものであれば、どんなものでも良いのです。赤い紙でも、赤いテープでも良いのです。赤スプレーで大きく×をつけた職場もあります。
また赤札作戦も行っているうちに、ただ赤紙を貼るのではなく、いろいろなニーズが出てきます。赤札品を集計したり、赤札置き場に移動したりする際に、最低限の情報として、通常次にあげる項目を赤札に記載しています。
①区分:赤札を貼ったモノが在庫なのか、機械なのかの区分を示します。主な区分としては、原材料、仕掛り品、製品、設備、治具、工具、金型、備品などがあります。
②品名:赤札を黏ったモノの品物名を記入します。
③品番:赤札を貼ったモノの品番を記入します。
④数量:赤札を貼った品物の数を記入します。
⑤金額:赤札を貼った品物の金額を記入します。
⑥理由:赤札を貼った理由を記入します。在庫であれば、主な理由として、不
要品、不良品、不急品のいずれか。
⑦部門:赤札を貼った品物を管理している担当部門を記入します。
⑧処置:赤札を貼った赤札品をどう対処するのか記入します。
⑨貼付日:赤札を貼った日付を記入します。
⑩処置日:赤札品をいつ処置するのか予定日を記入します。
⑩整理番号:赤札の貼付枚数を通し番号で記入します。
赤札のサンプルファイル(エクセル版)のテンプレートを下記に添付しましたのでご参考にしてください。
看板作戦~整頓対策~
住所の看板⇒「表札」
一般住居の表札も看板の一種です。
街からこれら看板が目ざわりとばかり、すべて取り去ってしまったらどうなるでしょうか。どこにどんなお店があるかわからなくなり、家を訪ねようにも迷ってしまいます。はたまた郵便物が届かなかったり、その街に長年住んだヒトにしか、街の様子がわからなくなってしまいます。
職場もまったく同じで、モノの表示がなければ、長年勤めているヒトにしかわからない職場になってしまうのです。誰でもひと目でわかる職場にするためには、あらゆるモノに、そのモノを表す何らかの表示が必要であり、このために看板が利用されるのです。
目で見る整頓
看板作戦への手順は、
①まず赤札作戦を実行して「要るモノと、要らないモノ」を明確に分ける。
②要らないモノは、日々の業務活動から外す。
この単純きわまりない、ごく当然のことが、不良をゼロにし、ムダを省くための改革の基礎となるのです。「分けることは、わかること」なのです。
そして、自分の身の回りに「要るモノ」だけが残ったら、これをもっとも効率の良い所に集め、資料については「何の資料か」、機械については「何の機械か」、在庫については「どこに、何か、いくつあるか」、ひと目でわかるようにするのです。これを「看板作戦」と呼び、「目で見る整頓」として位置づけられます。この「看板」は表示を意味し、漢字で表記します。ひらがなの「かんばん」と書くと作業指示を意味します。「かんばん方式」の「かんばん」です。漢字で書くか、ひらがなで書くか使い分けをしなければなりません。
また、看板は、いまの業務に必要なモノを中心としてつくられます。整理・整頓といわれるように、「赤札作戦」と「看板作戦」は必ず対で行わなければ、効果が半減してしまいます。
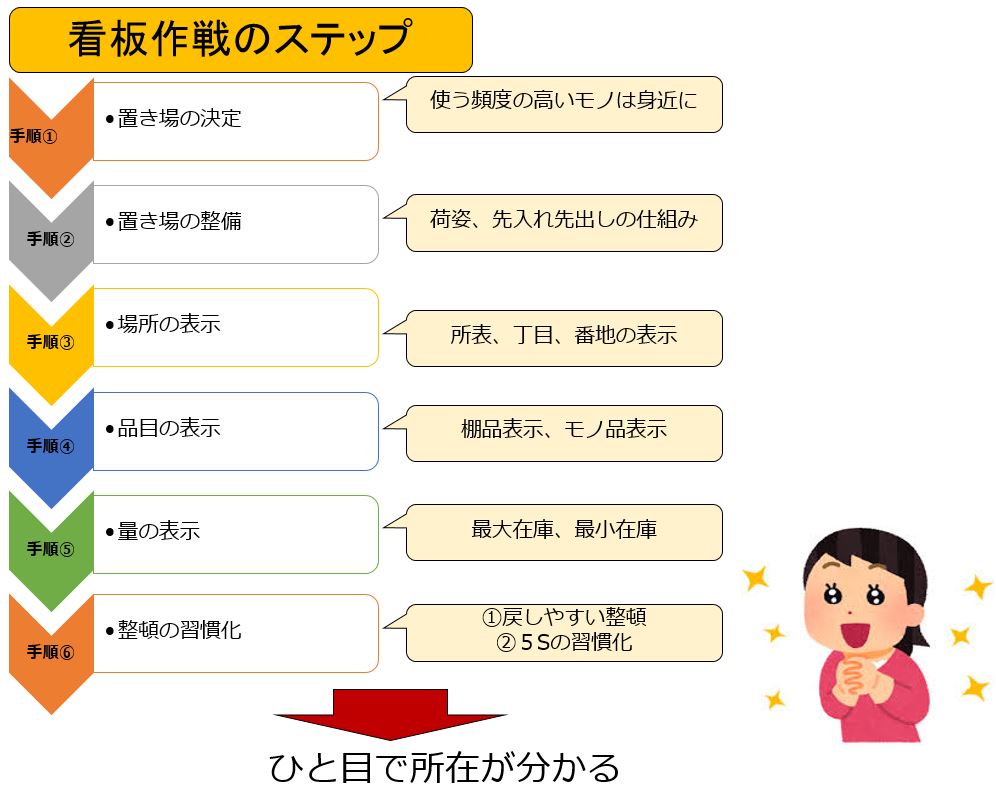
看板作戦
「3定」とは
特に在庫管理を行う際に重要なことは、どこに、何を、いくつあるか誰でもわかるようにすることです。そのためには、どこに「場所表示」、何を「品目表示」、いくつ「量表示」を表す看板が必要になります。
この場所表示を「定位」、品目表示を「定品」、量表示を「定量」といい、定位・定品一定量の3つの定で「3定」と呼んでいます。 5Sと3定は非常に重要なつながりがあり、「5S・3定」と表記することもよくあります。

定位、定品、定量
職場看板の種類
職場看板は大きな部署から小さな部署へと落とし込んでいきます。まずは全部の部署が入る会社の看板の設置です。また、事業部や場所によっては、敷地内の建屋を表す建屋看板をつけます。建屋に入ると、部や課の看板、または職場の看板があり、ライン化されている所では、ライン看板を掲示し、ラインの中の工程へは工程看板を掲示します。また、職場にある機械には機械看板を掲示し、在庫などのモノにはどこに、何を、いくっかがわかる3定の表示をし、仕掛り品には仕掛り看板を表示します。そして、人には当然名札がつけられます。
職場看板 | ロケーション看板 | 機械看板 |
会社看板 | 工場ロケーション | 設備別看板 |
建屋看板 | 巻き上げ機ロケーション | 出口看板 |
工場看板 | ||
ライン看板 |
5S 場所表示
モノをどこに置くかといった時の、「どこに」の表示が「場所表示」です。
「所番地表示」ともいわれています。
この場所表示の方法は、住所でいう所番地と同じようにつければ良いのです。私たちが普段利用している郵便物や宅配便は、住所の所番地をたよりに日本全国、または世界各国に配達されます。日本の中で所番地のついていない所はありません。それくらい徹底されているのです。
たとえば「東京都千代田区麹町1丁目3番地11号」であれば全体が所番地です。所番地をよく見ると、それは「所」と[丁目]と「番地」とに分けられます。 所は「東京都千代田区麹町」であり、丁目は「1丁目」、番地は「3番地11号」です。
所は全国でただ1つの名前になっています。これに対し、1丁目3番地11号という丁目と番地は、全国のいたる所に存在し、東京都千代田区麹町といった所の中を区分けしたものです。
これとまったく同じことが、モノの置き場の場所表示にも適用されます。
下図で場所表示を示している、Aが所表示であり、これは建屋の中でただ1つの名前となります。
丁目、番地表示
これに対して、1、2、3の横の数字は丁目を表し、縦の数字は番地を表します。このように、所番地をハッキリ明示した工場では、新しく入ってきたパートの作業者に「A-2-2の棚」と指定するだけで、目的の棚へ行くことができるのです。このように、誰でも、目で見てわかるようにすることが大切です。
表示の仕方
また、所表示の看板については通路に対して直角に表示をします。これは小学校のクラス表示の看板と同じです。これが通路に並行に表示されていたらどうでしょうか。その看板の前まで行かないとクラスの確認ができないのです。これでは看板の機能が半減してしまいます。
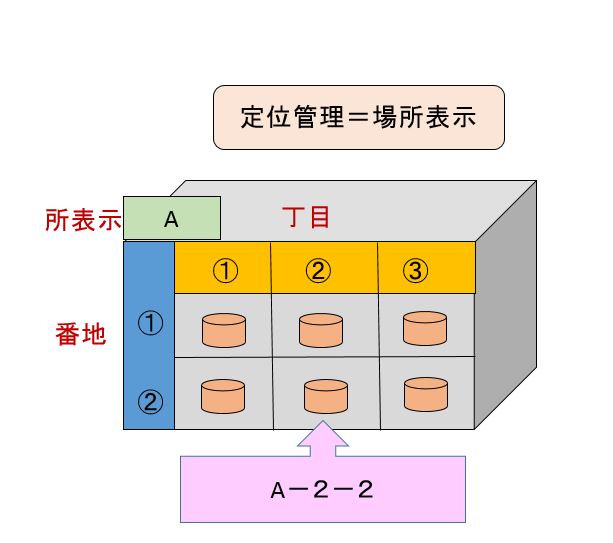
定位管理
『モノ品目表示』と『棚品目表示』
棚の所番地がハッキリ決まったら、次はそこに何を置くのか明示します。これが「品目表示」です。
「品目表示」する場合は「モノ品目表示」と「棚品目表示」を表示する必要があります。
モノ品目表示は、「置くモノ自体が何であるか」を示し、置かれているモノが入っている容器に表示したり、置かれているモノ自体に品名が入っている場合は、誰が見てもわかるように品名を表に向けて棚に置いたりします。
棚品目表示は、モノを「どこに置いたらよいか」を示す名札であり、家であれば表札なのです。また、この棚品目表示をつける場所ですが、モノが置かれている棚板に表示します。
よく見かけるのは一番下の棚板では見えにくいと、モノが置かれている上の棚板に表示されている場合です。これではモノと品目表示が離れ、目線が遠くなります。このような場合は、棚からの取り出しやすさをも考慮して、膝下の棚は使用禁止にします。
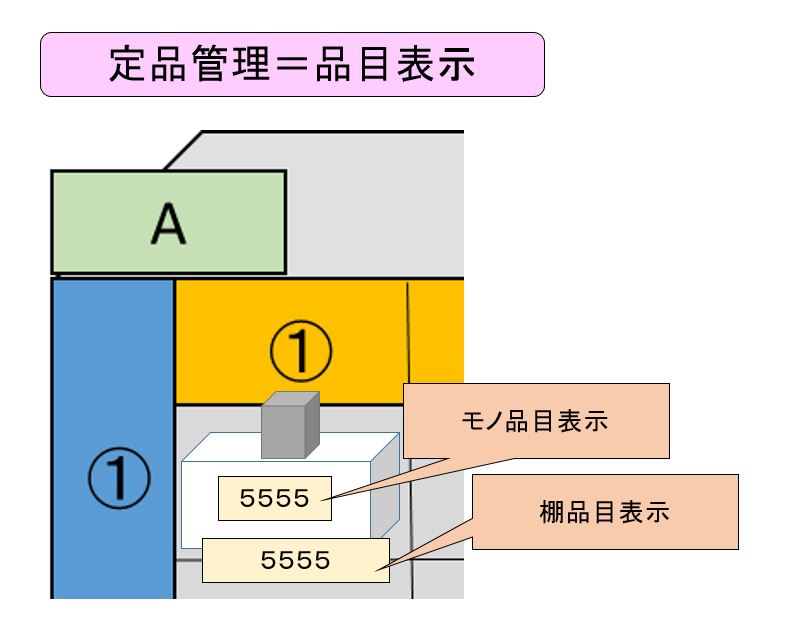
定品管理
「最小量」と「最大量」の表示
赤札作戦でせっかく不要な在庫を撤去しても、規制しないとドンドン増えてしまいます。しかし、その量が赤札作戦を行った時に設定した「必要とされる量」なのかどうかは表示がなければわかりません。
たしかに、コンピュータ上では在庫数や仕入れの数、出庫の数など計算はされていますが、実情にともなわないことが多々あります。今までも、コンピュータを使い、在庫を管理していたにもかかわらず、赤札作戦で多くの不要在庫が出てくるのは、やはりモノの管理の仕方や、入庫時や出庫時に出される指示が、作業者にうまく伝わらない場合があるためです。
そこで、置かれているモノが設定した在庫量なのかどうか、量の表示をします。その際、
①日々の使用量や1ヵ月の使用量を調べます。
②発注費用と在庫維持費用を考慮して1回の発注量を決めます。
③対象としているモノの納入リードタイム(調達期間)を調べておきます。
④発注してから納入されるまでの使用量の変動や納期のバラツキ、品切れ損失などを考慮して安全在庫を決めます。
⑤こうして求めた安全在庫量に、納入リードタイム期間内の使用量を加えて割り出し発注点とします。
そして、この安全在庫量を「最小量」、発注点の際の在庫量と発注数を足した数量を「最大量」とします。
異常がひと目でわかる表示をしよう量表示のもっとも良いやり方は、置き場や棚の大きさを制限してしまうことです。
また、これができない場合は、最大在庫量は赤色、最小在庫量は黄色などと決めて、色を使い異常納入があれば、誰が見てもひと目で判断できようにします。まず、現場で異常や問題、ムダがひと目で識別できるようにします。
う。
また、パレット積みなどの仕掛り品は、抜き差し可能なポールを立てて、そのポールに最大量を赤テープや赤塗料でマーキングするのも良い方法です。
この量表示で発注点が決まってくると、重要になるのが先入れ先出しの仕組みです。どこから使うか、そして納入はとこから入れるか、作業者が迷わない仕組みで置き場を設定しなければいけません。
3定の定位・定品・定量でもっとも重要なものが、この「定量決め」です。
こうして、赤札作戦で出た不要物を二度と出さない仕組みの基礎をつくります。
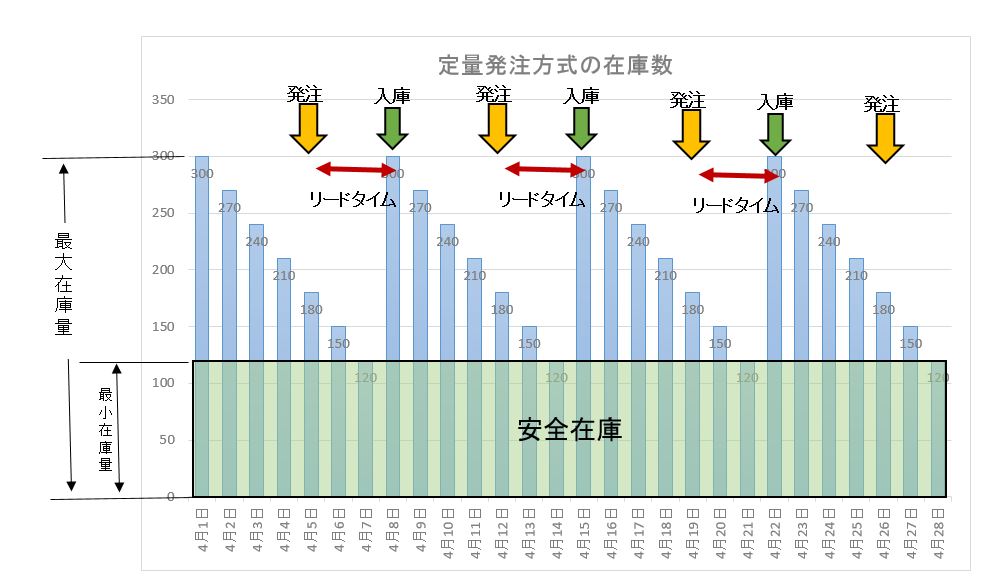
定量発注方式の在庫数
ロケーションの優先順位
治工具などの置き場を決める際に基本となるのが「動作経済の原則」です。
これはヒトの動きをもっとも効率的に、楽にするために考え出された原則です。基本的条件として採用し、職場などに掲示して、これにそって整頓を行います。動作経済の原則は、「身体の使用の原則」、「作業場の配置の原則」、それに[治工具・機械に関する原則]の3つに大別できます。
こうして、必要なモノを作業者が使いやすい所にどのように置くかを決め、職場内で目線が通る高さも確保します。
そこで、1つの基準としてモノを置く高さ範囲を決めると良いでしょう。その基準は、モノの取出しやすさや、職場の視界の高さから決めていきます。これを置き場の[ABCゾーン]といい、軽労化指数=重さ×姿勢で優先順位を決めます。
Aゾーン:肩から腰まで
Bゾーン:目線から肩まで
Bゾーン:腰からヒザまで
Cゾーン:手の届く位置から目線まで
Cゾーン:ヒザから床まで
Dゾーン:手の届かない位置
Dゾーン:無管理
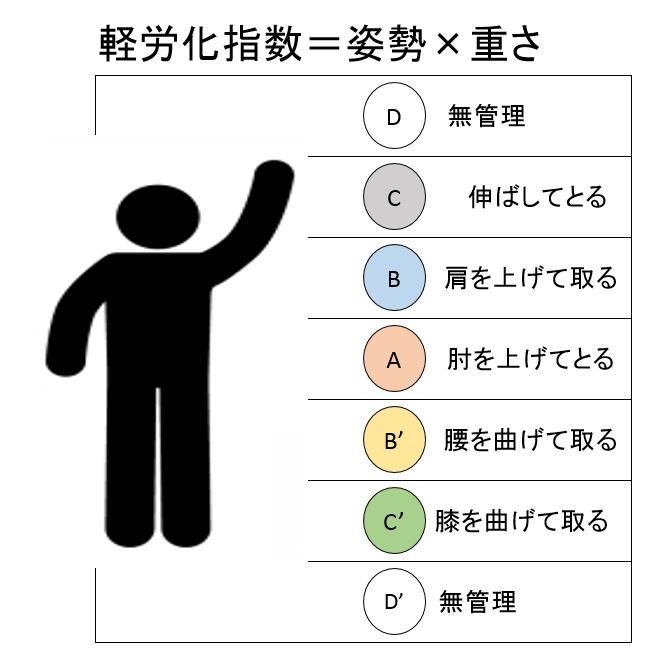
棚 置き場の優先順位
ペンキ作戦~整頓対策~
職場エリアを明確に区分
5Sは一般に目で見る整理「赤札作戦」から始めます。まず日々の業務に不必要なモノを現場から追い出し、本当に必要なモノだけを現場に残します。そして、不要なモノが取り除かれた職場は、空き地が生まれます。
この段階でモノの流れや作業性を重視し、職場のレイアウトを見直し、集中的に現場を改革・改善し、本来あるべき職場の理想像に近づけます。
そして、必要なモノを使いやすい形で配置し、モノの表示をハッキリさせるために目で見る整頓の1つである「看板作戦」を行います。
ほぼこの看板作戦と同時期に、作業者の安全を確保するための通路や、作業エリア、モノの搬送通路など誰が見てもわかるよう、床には作業区と通路を分ける区画線、置き場の範囲を示す置き場線など、ペンキやテープなどの色を利用した「ペンキ作戦」が開始されます。
「赤札作戦」により不要なモノを取り除いたすっきりした職場に、区画線や色でメリハリをつけるのです。
区画線で安全確保
街の中にある道路や歩道がハッキリと分かれているように、職場内にも区画線を引いて、作業者の安全を確保して歩ける通路を設けます。
つまり、車が決められた通りに通行するのと同じく、フォークリフトや搬送車が工場内、職場内をルール通り運行できるような区画線や、そこからはみ出したり、入り込んだら危険だということがハッキリわかるような区画線を確保し、右側通行か、左側通行かルールがわかるように、矢印による通行線を引いておくのです。
また、モノの置き場の表示とともにどの範囲にモノを置くのか、どの位置にそのモノを置くのか、誰が見ても判断できるように、範囲や位置を決める区画線も引きましょう。
ペンキ作戦の第1歩は、区画線で職場内にメリハリをつけることから始めます。区画線とは作業区と通路、車道と通路を分ける線のことで、作業者が通る通路の確保とその明確化を行い、工場内の安全を確保します。
一般には実線で、白や黄色を用いています。幅は10cm以上が良いとされています。ただし、建屋の外や重工業関係の工場では、フォークリフトなどが往来する場所では15cm以上は欲しいものです。
区画する場所によって線の幅や色を決めておくと良いでしょう。そして、一度引かれた区画線は[踏むな、またぐな、モノ置くな]を絶対に守らせなくてはいけません。
そのためには、作業区の出入口を明確に定めることです。出入口は破線にします。また車道を横切り、通路から通路へ横断する箇所には、街中の道路と同じように、横断歩道を設け安全確保にあたります。
そして、横断箇所には「右ヨシ!左ヨシ!前方ヨシ凵の指差し呼称を促す表記もしましょう。また、通路では右側通行か左側通行かを決め、矢印で定めた方向線を所々に引き、社内での交通ルールを明確にします。
職場の中で床に置かれているモノには置き場線で、その置き場を明確にしておきます。看板作戦で仕掛り置き場の看板を掲示しましたが、掲示された置き場の床には、パレットであれば1パレットごとに台車であれば台車ごとに、区画を線で引きます。
職場内にある作業台には、作業台の4本の脚にカギ型のコーナーラインを引きます。そうすることで作業台の位置を明確にし、置き場かすれていると誰でも判断できるようになります。
また、不良置き場として設定しているコンテナは赤で塗るとともに、置き場も赤い線で区画し、良品か不良品か誰でもすぐにわかるようにします。
消火器や消火栓、灰皿など火を連想するモノの置き場も赤で区画します。特に消火栓前にはモノが置かれないように通路からすぐに取り出せ、対処できるようなスペースを確保し、赤線で区画します。
置き場線においても、対象品目ごとに線の幅や線の種類、色などを決めておきます。
工場内 区画線の種類
区分 | 区分2 | カラー | 幅 | 備考 |
線 | 区画線 | イエロー | 10cm | |
出入り口 | イエロー | 10cm | ||
扉開閉線 | イエロー | 10cm | ||
方向線 | イエロー | |||
置き場線(仕掛) | ホワイト | 5cm | ||
置き場線(不良) | レッド | 5cm | ||
床面の色分け
作業者や、作業者が手で押す台車が通る通路と、フォークリフトや搬送車などの車両が通行する通路を色分けしたり、付加価値の生まれない置き場と、付加価値を生む作業区の床の色を分けてみましょう。また、作業者がゆっくりと休める休憩所の色も分けると良いでしょう。色と線の種類により意味合いを分けて線引きます。
通路の色分け
工場での床を大きく分けると、通路、作業区、倉庫、休憩所などになります。
まず通路は、なるべく周りが暗くても目立つような色合いを使います。蛍光色的なオレンジ色など、明るい色を使うことで少しの照度でもハッキリわかるようになります。
反対に暗い色を使うと、通路に落ちたゴミや、たまたま落としてしまったボルトやナットなど、障害物となってしまうモノがハッキリわからなくなるケースもあり、転倒などの危険災害につながります。まして、夜勤の場合など、節電のため薄暗くなっていることもあり、そんな薄暗い中でも通路にある異常がハッキリわかるような色が良いでしょう。
作業区と倉庫の色分け
作業区は明るめの緑が多いようです。深緑だと先はどの通路の例のように暗くなり、異常が発見しにくくなります。
倉庫は付加価値のつかない在庫置き場です。ここの色は作業区と分けることで、付加価値のつかない置き場にどれだけスペースをとっているか、ハッキリと自覚できるようにもなります。
また、塗料の種類もメーカや業者に相談して決めましょう。安易に塗ってしまうと、梅雨時期にやけに床面に湿気が溜まったり、やたらに滑ったりします。床の材質に合わない塗料では、すぐに剥離してしまう場合もあります。また、塗り直す場合は、床の傷んでいる箇所や、床面のレベルが保たれていなかった箇所を同時に補修してしまうと効率的です。
休憩スペース
最後は休憩スペースです。作業スペースと休憩スペースを床の色をハッキリ分けてあげることで、作業者の心の気分転換にもなります。ずっと同じ色合いの所にいると、休憩をしていても、気分的にはあまり休まらないものです。
区分1 | 区分2 | カラー | 幅 | 備考 |
床 | 作業区 | グリーン | ||
通路 | オレンジ | 蛍光色 | ||
休憩所 | ブルー |
迷い箱、遊休設備置き場
赤札をつけたが、即捨てる決断がつかないモノを迷い箱(大きいモノは遊休設備置き場)に置く。一定期間(例えば1ヶ月間)過ぎても使用しなければ、その場で捨てる。
赤札をつけても、すぐに捨てる決断ができない場合は、そのまま放置されるか、あるいは所定の位置に置かれる。それを防ぐために迷い箱(遊休設備置き場)を利用する。
迷い箱置き場は、明確に表示し、しかも目立つ所に設置する。執行猶予期間(保留期間)を明確にして、迷い箱に表示する。月ごとに識別ラベル(色を活用)を貼ると一目で期日がわかる。執行猶予期間が過ぎたら、迷うことなくすぐに捨てる。ただし執行猶予期間中に使用したモノ、今後も使用する可能性の高いモノに関しては、所定の位置に移す。
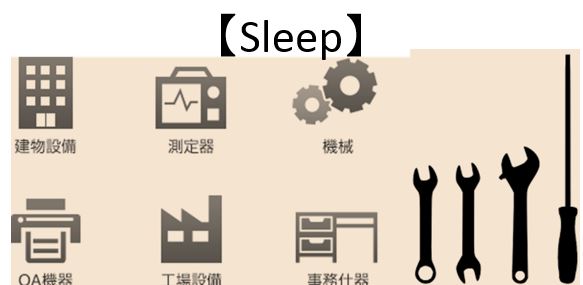
遊休設備
廃棄基準
モノを捨てる基準は大きく分けて使用期間と保管数量に分けられる。
使用期間がないモノは直ぐに捨てる対象になるが、使用頻度が高くても多くの在庫がある場合は適正な数量を決めてそれ以外は廃棄の対象となる。
モノが多くあることは保管スペースおよび管理費用がかかり、また必要とするのモノが探しにくくなる。よって適正な在庫だけを置くようにする。
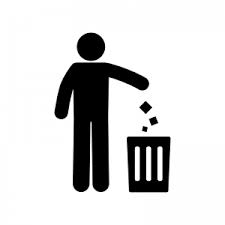
捨てる基準
定点撮影
同じ位置から同じ高さで同じ方向で同じ対象物を定期的に撮影してその改善状態を確認する方法である。
目で見る管理:(定位置管理)
工場や事務所では、モノの流し方、情報の流し方、作業のやり方、管理の方法など、あらゆることが誰でも、ひと目でわかるようになっていなければなりません。これは「目で見る管理」と呼ばれ、正常な姿と異常な状態が、誰が見てもひと目でわかり、すぐに対処できるようにすることを意味しています。
5Sとて例外ではありません。整理、整頓、清掃の状況が良いか悪いか誰が見ても、ひと目でわかるようになっていることが要求されます。
これを「目で見る5S」といい、整理や整頓では赤札や看板、区画線や線引き、形跡整頓や色別整頓などがこれに当ります。
清掃や清潔は個人ごとにその判断レベルが異なります。同じ現状を見てもあるヒトはキレイと考え、あるヒトは汚いと考えるのです。客観的な判断ができるように、[清掃点検チェック表]や「清潔度5点チェックリスト、「5S・3定チェックシート」などにより、5Sレベルや清潔度合いなどを数値化します。
このような目で見る職場は、5Sにかぎったことではありません。生産を行ううえで作業にも一定の標準が存在し、異常をいち早く発見し、これを管理するにも、職場の現状がひと目でわからなければならないのです。ヒトには「標準作業」、モノには「かんばん」、設備には「アンドン」で目で見る管理をします。
目で見てわかる5S
No | 項目 | 内容 |
1 | 整理整頓 目で見る管理 | 赤札 |
2 | 看板 | |
3 | 区画線 | |
4 | 色分け | |
5 | 清掃、清潔 目で見る管理 | 清掃点検チェック表 |
6 | 5S 3定チェック表 |
たとえば工具などの外形をボードに描いておきその位置に外形に相当する工具を掛ける方式の工具掛けボードは工具の紛失を防止することができる
【例:工具掛けボード】
又、表示する時は何処から見てもすぐに分かるように工夫してください、下は看板を直角に表示して何処からも見えるように改善した事例です。
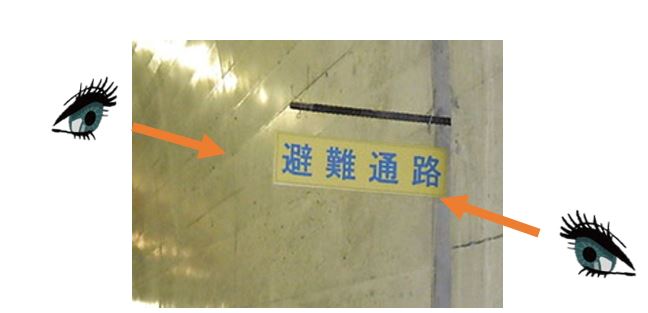
看板 見える化
清掃マップ
清掃区域のマップを作成する
清掃対象が決まったら、清掃区域、清掃担当責任者、清掃時間の3項目を決めておきます。まずはじめに、工場レイアウト図を基に対象スペースを区分けします。さらにモノの置き場で分けていきます。そして、詳細の設備関係も書き込み、全体マップをつくります。
全体マップを職場対象単位に分け、清掃区域がわかるように色分けし、各職場へ掲示できるようにしておきます。
清掃担当責任者を決める
清掃区域が決まったら、次はその区域を誰が担当し、責任者は誰かハッキリ割り当てます。また、注意して決めなければならないのは、共同で使用する場所で、会議室、休憩所、トイレ、資料室、通路などです。これについては、よく当番制がとられています。担当が決まっていないと無管理状態となり、「誰かがやるからいい」と誰もが思い、結局誰もやらないままとなるのです。かといって、共同で使用する場所について、担当者を1人に決めてしまうと、汚した所を直接本人が掃除しないため、汚したという自覚がなく、いつまで経っても汚すことに注意を払わなくなります。
共同使用場所では使用するヒトを洗い出し、まずは担当責任者を決めます。
そして、清掃作業の中身を洗い出し、手順化し、日々の担当者を割り当てます。これを基にスケジュール表を作成し、掲示するのです。また、当番札を作成し、担当者問で回していきます。
清掃時間を決める
こうして、清掃区域、清掃担当責任者が決まったら、清掃時間を決めます。
清掃時間は、清掃をいつ実施するのかという「清掃時刻」とどの程度の時間をかけて清掃するのかという「清掃時間」の2つがあります。清掃時刻は仕事が始まる前の時間帯と、仕事の合間の時間帯、そして仕事が終わったあとの時間帯に分けられます。また、清掃時間は清掃区域、対象によって異なるので実際に清掃を行い、どの位時間がかかるか一度計測します。
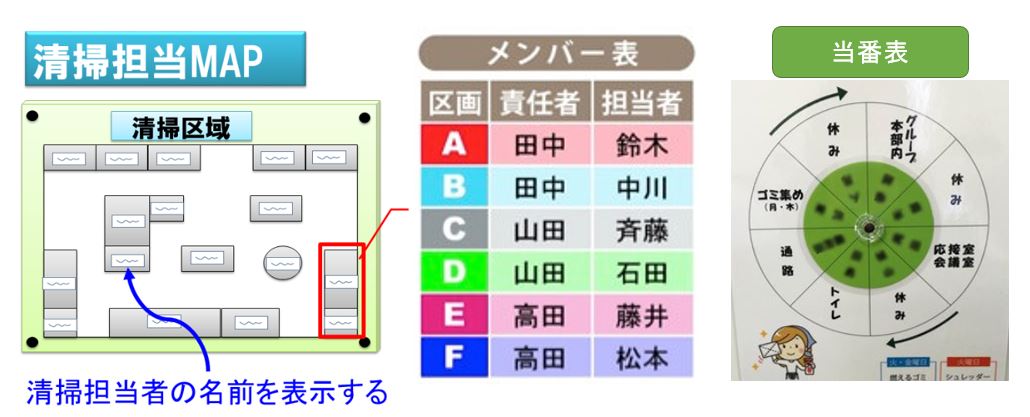
清掃担当マップ
清掃手順&清掃用具
清掃手順を決める
ただむやみに清掃を行ってしまうと、同じ箇所を2回も3回も掃いたり、拭いたりしてしまいます。また、あるヒトは左から右に、またあるヒトは上から下へとヒトそれぞれ、やりたい方から掃いたり拭いたりしていきます。これでは同じ清掃でも清掃後の状態にバラツキが起こり、掃除し忘れや見落としが発生してしまいます。それぞれの清掃区域や対象を何の清掃用具で、どこを、どのような手順で、どの清掃状態まで清掃し、仕上げるのか決めておきます。
清掃用具を対象区域ごとに洗い出す
清掃対象を決めると続いて、手順とともに使用する清掃用具を洗い出します。切りくずや粉が床に散らかる職場では、まずホウキを使って床を掃き、モップなどで床の拭き掃除をします。作業台、事務机、機械類は原則として雑巾を使い、ホコリやゴミの多い場合は濡れ雑巾を用います。磨きをかける場合や油とりは乾いた雑巾やウエスを用います。また、洗剤や消毒のアルコールなどを使用する場合もあります。
「清掃点検マップ」作成
現象面、機構面のそれぞれ清掃ポイントを洗い出したら、対象設備について三角法などで絵や図を描き、そこに印をつけていきます。
そして、日々点検する箇所、週に1度点検する箇所、1ヵ月に1度点検する箇所を色分けし、一筆書きになるように順番を決めてNO.を表示し「清掃点検マップ」を作成します。
【現象面からの清掃ポイント】
現象 | ポイント | 処置 | |
1 | ゴミ汚れ | ホコリ、ゴミ、サビ、くず | 清掃 |
2 | 油 | 油漏れ、油汚れ、油切れ、油不足、油間違い | 給油手順 |
3 | 温度、圧力 | 温度オーバー、温度不足、圧力オーバー、圧力不足 | 復元修理 |
4 | 緩み、タルミ | ボルトの緩み、外れ ナット緩み、外れ | 増締め、復元修理 |
5 | 破損 | ホース、メーター、スイッチ破損 | 復元修理 |
【機構面からの清掃ポイント】
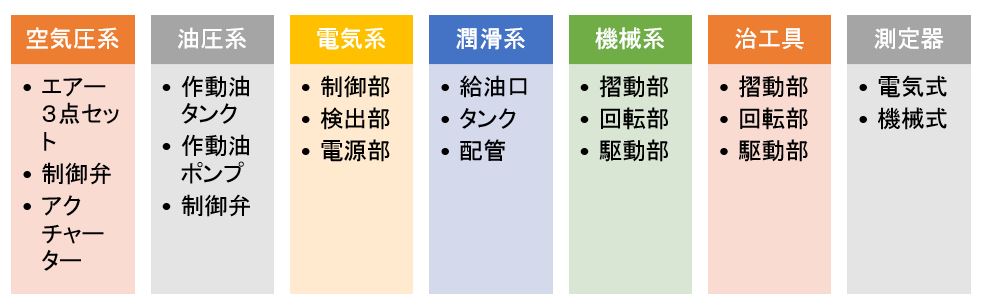
機構面 清掃点検ポイント
清掃保全
清掃は作業の効率や品質、安全面、衛生面などで大変に重要な役割りをもっており、人間の向上心とも大変に深いつながりがあります。
清掃とは、まずホウキをもつこと、次に雑巾を握ることです。これが清掃のもっとも根底にある基本であり、まさに読んで字のごとく、清掃とは掃き清める”ことなのです。
この基本を土台にして、清掃は次の3つのステップを踏みます。
ステップ1:日常清掃
ステップ1では、床や通路それに機械、設備を徹底して磨き上げて「キレイにする清掃」です。これは[ピカピカ作戦]などと呼ばれ、ホウキで掃き、雑巾で拭くことを基本として日々行われます。また、年に2回から4回ほど、全社をあげて一斉に大掃除として「集中清掃」を行い、清掃を業務の中に浸み込ませ、「日常清掃」として認知し、かつ習慣化していきます。
ステップ2:清掃点検
ステップ2では、単に「キレイにする清掃」をもう一歩深めて、キレイにした職場に、何らかの不具合点を感知できるような仕組みを組み込んでいきます。これは[感知する清掃]であり、機械設備では欠陥部分をいち早く感知、発見し、故障を未然に防ぐような保全活動へとつなげていきます。このような日々の点検を清掃業務の中に浸み込ませ、「清掃点検」としての業務を確立、習慣化していくのです。
TPMでは初期清掃と呼ばれ、機械設備を磨く、部品の間に溜まったカスを取る、操作板の汚れを取って文字が鮮明に見えるようにするなどの清掃を行いながら機械、設備の異常を早期に検出する清掃の事です。
清掃保全
最後に、ステップ3では、「清掃点検」によって感知、発見した不具合点や欠陥を復元または改革・改善します。この時、作業者がその場ですぐにできる復元や改革・改善は「即時改革」とします。また、これが困難なものは、保全部門へ依頼をして復元・改革・改善を行います。このように清掃点検業務に復元や改革・改善といった保全業務を浸み込ませて「清掃保全」とし、これを習慣化していきます。このようにステップ1からステップ3までを通して見ると、そのポイントの流れはまさに、清掃とは「点検」であることがわかります。
例としては発生源対策としてごみ、汚れの発生源を改善し飛散防止用のカバーを取り付ける等の改善です。
又、清掃点検に発見した不具合による設備劣化を防ぐ為に清掃、給油を確実にできるように基準書を作成することも清掃保全のひとつです。
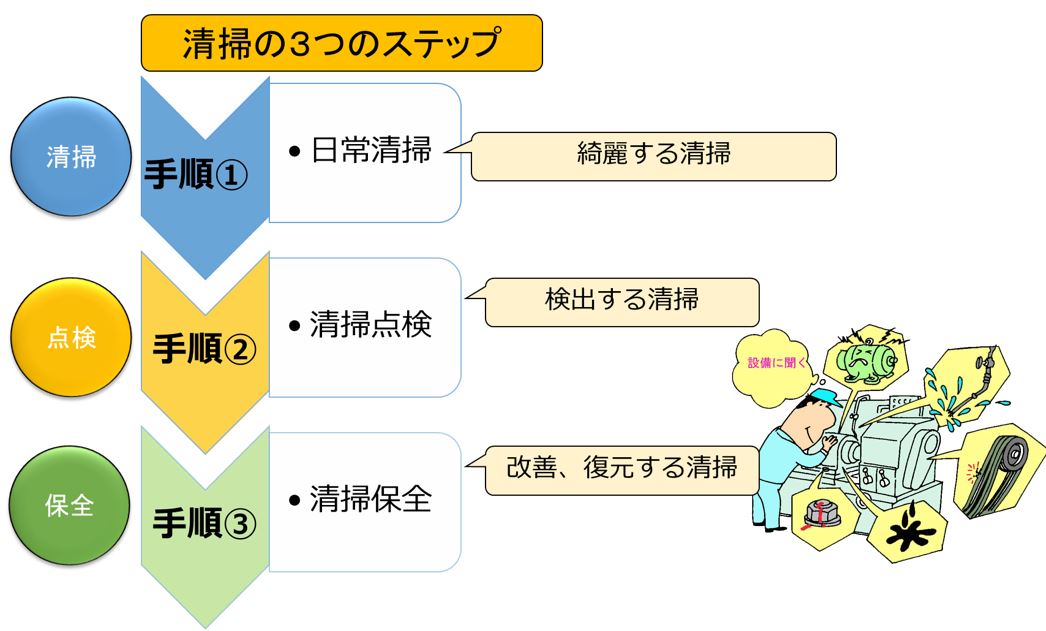
清掃の種類
5S活動における社内の共有と教育
5S活動における社内の共有と教育は、活動を成功させる上で非常に重要な要素です。以下に、具体的な方法とポイントをまとめました。
5S活動の目的と重要性の共有
- 目的の明確化:
- 5S活動が単なる清掃活動ではなく、業務効率化、品質向上、安全確保など、企業の目標達成に繋がる重要な活動であることを理解してもらう。
- 各部門や従業員にとっての具体的なメリット(例:作業時間の短縮、ミスの削減、快適な職場環境)を示す。
- 重要性の共有:
- 5S活動が企業の競争力強化に繋がることを、具体的な事例やデータを交えて説明する。
- 経営層からのメッセージや、成功事例の共有を通じて、全社的な意識を高める。
効果的な教育方法
- 研修・ワークショップ:
- 5Sの各要素(整理、整頓、清掃、清潔、躾)の具体的な進め方や注意点を、実例を交えて解説する。
- 現場での実践を想定したワークショップを行い、参加者自身が改善案を考え、実行する力を養う。
- ツール・資料の活用:
- 5S活動のチェックリストや手順書、写真やイラストを用いた分かりやすい資料を作成し、配布する。
- 動画やeラーニング教材を活用し、時間や場所にとらわれずに学習できる環境を提供する。
- OJT・現場指導:
- 経験豊富な従業員が、現場で具体的な指導を行う。
- 定期的なパトロールやチェックを通じて、改善状況の確認とフィードバックを行う。
情報共有とコミュニケーション
- 定期的な会議・報告会:
- 各部門の5S活動の進捗状況や課題、改善事例などを共有する。
- 成功事例を表彰するなど、モチベーション向上に繋がる取り組みを行う。
- 掲示板・社内報:
- 5S活動の成果や改善事例、関連情報を定期的に発信する。
- 従業員からの意見やアイデアを募集し、活動に反映させる。
- デジタルツールの活用:
- 社内SNSやグループウェアを活用し、情報共有や意見交換を活発化させる。
- 写真や動画を共有し、視覚的に分かりやすく情報を伝える。
活動の継続と定着
- 定期的な見直しと改善:
- 定期的に5S活動の成果を評価し、改善点を見つける。
- 従業員からの意見やアイデアを積極的に取り入れ、活動内容を柔軟に改善する。
- 評価制度への組み込み:
- 5S活動への貢献度を人事評価の項目に組み込むなど、従業員のモチベーションを高める仕組みを作る。
- トップの積極的な関与:
- 経営層が率先して5S活動に参加し、その重要性を発信する。
- トップの関与は、従業員の意識改革と活動の定着に大きく貢献する。
5S活動における教育のポイント
- 5S活動は、従業員の意識改革から始まることを理解する。
- 5S活動は、継続することが大切であることを理解する。
- 5S活動は、従業員全員で取り組むことが大切であることを理解する。
これらの方法を参考に、自社の状況に合わせた効果的な共有と教育を行い、5S活動の定着と継続を目指しましょう。
5S活動 全社員参加の意義
5S活動への全社員参加は、単に職場をきれいにするだけでなく、組織全体の意識改革や企業文化の醸成に繋がる重要な意義を持ちます。以下に、その具体的な意義をまとめました。
組織全体の意識改革と一体感の醸成
- 全員参加による共通認識の形成:
- 5S活動を通じて、整理、整頓、清掃、清潔、躾の重要性を全社員が共通認識として持つことで、組織全体の一体感が生まれます。
- 部署や役職に関係なく、全員が同じ目標に向かって取り組むことで、連帯感が強化されます。
- 意識改革と改善文化の定着:
- 全員参加は、個々の意識改革を促し、改善意識を組織全体に浸透させます。
- 日々の業務の中で、常に改善点を見つけ、実行する文化が定着します。
業務効率化と品質向上
- 無駄の排除と効率化:
- 全員参加による徹底的な整理整頓は、無駄な時間やスペースを排除し、業務効率を向上させます。
- 必要なものがすぐに取り出せる環境は、作業時間の短縮やミスの削減に繋がります。
- 品質向上と顧客満足度向上:
- 清潔な職場環境は、製品やサービスの品質向上に繋がり、顧客満足度を高めます。
- 全員が品質意識を持つことで、不良品の発生を防ぎ、品質管理体制を強化します。
安全性の向上とリスク軽減
- 事故防止と安全確保:
- 整理整頓された職場は、転倒や衝突などの事故を防止し、安全性を高めます。
- 全員が安全意識を持つことで、危険な箇所を早期に発見し、リスクを軽減します。
- 快適な職場環境の実現:
- 清潔で快適な職場環境は、従業員のストレスを軽減し、モチベーション向上に繋がります。
- 全員が協力して職場環境を維持することで、働きやすい環境が実現します。
人材育成と企業文化の醸成
- 人材育成と能力向上:
- 5S活動を通じて、問題解決能力や改善能力など、様々な能力を向上させることができます。
- 全員参加は、リーダーシップやチームワークなど、組織で働く上で重要なスキルを育成します。
- 企業文化の醸成:
- 5S活動は、規律や責任感、協力など、企業が大切にする価値観を浸透させ、企業文化を醸成します。
- 全員参加は、企業文化を共有し、組織全体の方向性を一致させる効果があります。
全員参加を成功させるためのポイント
- 経営層の積極的な関与とリーダーシップ
- 明確な目標設定と計画的な推進
- 継続的な教育と意識啓蒙
- 成果の評価とフィードバック
- 従業員の意見を積極的に取り入れる
5S活動への全員参加は、組織全体の力を結集し、持続的な成長と発展に繋がる重要な取り組みです。
5S教育プログラムの実践
5S教育プログラムの実践は、5S活動を組織に定着させ、効果を最大化するために不可欠です。以下に、効果的な5S教育プログラムの実践方法をまとめました。
教育プログラムの目的と目標設定
- 目的の明確化:
- 5S活動の目的(業務効率化、品質向上、安全確保など)を明確にし、教育プログラムの目標と連動させる。
- 参加者に、5S活動が自分たちの業務にどのように役立つかを理解してもらう。
- 具体的な目標設定:
- 教育プログラムを通じて、参加者にどのような知識やスキルを習得してほしいかを具体的に設定する。
- 例:5Sの各要素の定義を理解する、整理・整頓の具体的な方法を実践できる、など。
教育プログラムの内容
- 5Sの基礎知識:
- 5S(整理、整頓、清掃、清潔、躾)の各要素の定義と重要性を分かりやすく解説する。
- 5S活動の歴史や背景、企業の成功事例などを紹介し、参加者の興味を引き付ける。
- 具体的な実践方法:
- 整理・整頓の進め方、清掃・点検のポイント、清潔を維持するためのルールなどを、具体的な事例や写真を用いて解説する。
- 現場での実践を想定したワークショップやシミュレーションを行い、参加者が実際に手を動かして学ぶ機会を提供する。
- 維持・改善の仕組み:
- 5S活動を継続するためのチェックリストや評価方法、改善提案の仕組みなどを説明する。
- 参加者が、日常業務の中で5S活動を実践し、改善を続けるための意識を高める。
教育プログラムの実施方法
- 対象者別プログラム:
- 新入社員、一般社員、管理職など、対象者別にプログラムを設計する。
- 役職や業務内容に応じて、必要な知識やスキルに焦点を当てる。
- 多様な教育手法:
- 講義、ワークショップ、グループディスカッション、現場見学、eラーニングなど、多様な教育手法を組み合わせる。
- 参加者の興味や理解度に合わせて、効果的な手法を選択する。
- 継続的な教育:
- 一度の研修で終わらせず、定期的なフォローアップや継続的な教育を行う。
- 5S活動の進捗状況に合わせて、必要な情報やスキルを提供する。
教育プログラムの効果測定と改善
- 効果測定:
- 教育プログラムの前後で、参加者の知識や意識の変化、現場の改善状況などを測定する。
- アンケートやインタビュー、現場観察など、多様な方法で効果を測定する。
- プログラムの改善:
- 効果測定の結果を踏まえ、教育プログラムの内容や方法を改善する。
- 参加者からのフィードバックを積極的に取り入れ、より効果的なプログラムを目指す。
5S教育プログラム実践のポイント
- 経営層の積極的な関与と支援
- 参加者の主体性を引き出す工夫
- 現場での実践を重視したプログラム
- 継続的な改善とフォローアップ
これらのポイントを踏まえ、組織全体の5S意識を高め、効果的な5S活動を推進しましょう。
5S成功事例を用いた社内研修
5S活動の成功事例を用いた社内研修は、参加者のモチベーションを高め、実践的な学びを促進する効果的な手法です。以下に、研修の設計と実施における重要なポイントをまとめました。
研修の目的と目標
- 目的の明確化:
- 5S活動の重要性を再認識し、職場環境改善への意識を高める。
- 成功事例を通して、具体的な改善手法や効果を学ぶ。
- 自部門や自社の課題解決に繋がるアイデアを得る。
- 具体的な目標設定:
- 参加者が成功事例から具体的な改善策を3つ以上挙げられる。
- 自部門の5S活動における課題を特定し、改善計画を作成できる。
- 5S活動への積極的な参加意欲を高める。
研修内容の設計
- 成功事例の選定:
- 自社の業種や規模に近い事例、または参考になる事例を選ぶ。
- 具体的な改善前後の写真やデータを用いて、効果を視覚的に伝える。
- 改善のプロセスや苦労した点など、ストーリー性のある事例を選ぶ。
- 事例分析とディスカッション:
- 成功事例の分析を通して、改善のポイントや成功要因を抽出する。
- グループディスカッションやワークショップを通して、参加者自身のアイデアを出し合う。
- 自部門の課題との共通点や相違点を議論し、具体的な改善策を検討する。
- 実践的なワークショップ:
- 実際の職場を想定したシミュレーションやロールプレイングを行う。
- 整理・整頓の具体的な方法を実践し、改善の効果を体感する。
- チェックリストや改善提案書の作成など、実践に役立つツールを提供する。
研修の実施方法
- 参加者の主体性を引き出す:
- 一方的な講義形式ではなく、参加者同士の意見交換や議論を重視する。
- グループワークや発表など、参加者が主体的に参加できる機会を設ける。
- 参加者の意見やアイデアを積極的に取り入れ、研修内容に反映させる。
- 視覚的に分かりやすい資料:
- 写真やイラスト、グラフなどを効果的に活用し、視覚的に分かりやすい資料を作成する。
- 成功事例の具体的なデータや改善前後の比較などを提示し、説得力を高める。
- 動画や事例紹介ビデオなど、多様なメディアを活用する。
- 継続的なフォローアップ:
- 研修後も、定期的な進捗確認や情報共有の場を設ける。
- 改善活動の成果を評価し、フィードバックを行う。
- 継続的な改善活動を支援するための相談窓口やサポート体制を整える。
研修効果の測定
- 研修前後のアンケート:
- 参加者の意識変化や知識習得度を測定する。
- 研修内容や進行方法に対する評価を収集し、改善に繋げる。
- 現場改善状況の評価:
- 研修で学んだ内容が現場で実践されているか、定期的に評価する。
- 改善活動の成果を数値化し、効果を具体的に示す。
- 参加者からのフィードバック:
- 研修後の感想や意見を収集し、今後の研修内容に反映させる。
- 改善提案やアイデアなど、現場からの声を積極的に取り入れる。
5S活動成功事例を用いた社内研修は、組織全体の5S意識を高め、継続的な改善活動を促進する効果的な手段です。
トヨタの5S活動から学ぶ
トヨタの5S活動は、単なる整理整頓にとどまらず、生産性向上、品質向上、安全確保、人材育成など、多岐にわたる効果をもたらす重要な活動です。トヨタの5S活動から学ぶべき点は数多くありますが、特に重要なポイントを以下にまとめました。
徹底した整理・整頓
- トヨタでは、「必要なものだけを、必要な時に、必要な量だけ」使えるように、徹底的に整理・整頓を行います。
- 工具や部品の置き場所を明確にし、誰でもすぐに取り出せるように工夫されています。
- 無駄な在庫や不要なものを排除することで、スペースの有効活用、作業効率の向上、コスト削減を実現しています。
清掃と点検の徹底
- 清掃は単に汚れを落とすだけでなく、設備や機械の異常を早期に発見するための重要な点検作業と位置づけられています。
- 日常的な清掃を通じて、設備や機械のメンテナンスを行い、故障やトラブルを未然に防ぎます。
- 清潔な職場環境は、従業員のモチベーション向上や品質向上にも繋がります。
ルールと標準化の徹底
- 5S活動を維持・継続するために、ルールや標準を明確に定め、全員がそれを遵守します。
- 定期的なチェックや監査を行い、ルールや標準が守られているか確認します。
- ルールや標準は、常に改善の余地があるものとして、定期的に見直しが行われます。
全員参加の文化
- 5S活動は、一部の担当者だけでなく、全従業員が参加する活動です。
- 従業員一人ひとりが、自分の持ち場を責任を持って管理し、改善提案を積極的に行います。
- 全員参加の文化は、組織全体の意識改革や改善意識の向上に繋がります。
継続的な改善(カイゼン)
- トヨタでは、5S活動を「カイゼン」の土台と位置づけ、常に改善を追求します。
- 小さな改善を積み重ねることで、大きな成果を生み出すことを重視しています。
- 改善活動を通じて、従業員の能力向上や組織全体の成長を促します。
トヨタの5S活動から得られる教訓
- 5S活動は、単なる清掃活動ではなく、組織全体の生産性や品質を向上させるための重要な活動である。
- 徹底した整理・整頓、清掃・点検、ルール・標準化、全員参加、継続的な改善が、5S活動を成功させるための鍵となる。
- 5S活動は、組織文化として根付かせることで、持続的な成果を生み出すことができる。
トヨタの5S活動は、多くの企業にとって模範となるものです。これらの教訓を参考に、自社の5S活動を見直し、改善に繋げていくことが重要です。
病院における5S活動の導入
病院における5S活動の導入は、医療安全の向上、業務効率化、患者満足度の向上など、多くのメリットをもたらします。以下に、病院における5S活動の導入について詳しく解説します。
病院内の5S活用事例
病院における5S活動は、医療安全の向上、業務効率化、患者満足度の向上に大きく貢献します。ここでは、病院内での具体的な5S活用事例をいくつか紹介します。
医療器具・薬品の管理
- 整理:
- 使用頻度の低い医療器具や期限切れの薬品を処分し、必要なものだけを保管。
- 在庫管理システムを導入し、過剰在庫や不足を防ぐ。
- 整頓:
- 医療器具や薬品の置き場所を明確にし、ラベリングや色分けで識別しやすくする。
- 使用頻度の高いものを手の届きやすい場所に配置し、動線を最適化。
- 清掃:
- 医療器具や薬品の保管場所を定期的に清掃し、清潔な状態を維持。
- 清掃チェックリストを作成し、担当者と清掃頻度を明確にする。
診察室・処置室の環境整備
- 整理:
- 不要な書類や備品を処分し、診察に必要なものだけを置く。
- 患者の個人情報保護のため、書類や記録の整理を徹底する。
- 整頓:
- 診察に必要な器具や備品を、使いやすい場所に配置する。
- 患者が安全に移動できるよう、床に物を置かない。
- 清掃:
- 診察台や処置台を患者ごとに消毒し、清潔な状態を保つ。
- 空気清浄機を設置し、院内の空気環境を改善する。
院内全体の環境整備
- 整理:
- 共有スペースや倉庫の不要品を処分し、スペースを有効活用する。
- 書類や記録の電子化を進め、保管スペースを削減する。
- 整頓:
- 院内の案内表示を分かりやすくし、患者や訪問者の移動をスムーズにする。
- 待合室の椅子や雑誌を整理し、快適な空間を提供する。
- 清掃:
- 院内の床や壁を定期的に清掃し、清潔な状態を維持する。
- トイレや洗面所を常に清潔に保ち、患者の不快感を軽減する。
5S活動の定着化
- 清潔:
- 整理・整頓・清掃の状態を維持するためのルールや基準を設ける。
- 定期的なチェックや監査を行い、清潔な状態を維持する。
- 躾:
- 5S活動の重要性を理解し、全員が主体的に取り組む文化を醸成する。
- 継続的な教育や研修を行い、5S活動の意識を高める。
これらの事例は、病院における5S活動のほんの一例です。各病院の状況や課題に合わせて、5S活動を柔軟に活用することで、より安全で快適な医療環境を実現できます。
患者安全への効果
病院における5S活動は、患者安全に多大な効果をもたらします。以下に、具体的な効果をまとめました。
医療ミスの防止
- 整理整頓による誤使用防止:
- 医療器具や薬品の置き場所が明確になることで、必要なものを迅速かつ正確に取り出すことができ、誤使用のリスクを低減します。
- 特に、緊急時における医療器具の取り違えや薬品の誤投与などを防ぎます。
- 清潔な環境による感染症対策:
- 徹底した清掃と消毒は、院内感染のリスクを大幅に低減し、患者を感染症から守ります。
- 医療器具の適切な滅菌や消毒は、患者への感染を防ぎます。
医療事故の防止
- 動線の確保による転倒防止:
- 整理整頓された環境は、患者や医療従事者の動線を確保し、転倒や衝突などの事故を防ぎます。
- 特に、高齢者や体の不自由な患者にとって、安全な移動環境は非常に重要です。
- 設備・機器の安全管理:
- 定期的な点検とメンテナンスは、医療機器の故障や不具合を早期に発見し、医療事故を防ぎます。
- 清潔な環境は、医療機器の性能を維持し、安全な医療を提供します。
患者の安心感向上
- 清潔で快適な環境:
- 清潔で整理整頓された環境は、患者に安心感を与え、医療に対する信頼感を高めます。
- 快適な待合室や診察室は、患者の不安やストレスを軽減します。
- スムーズな医療サービスの提供:
- 整理整頓された環境は、医療従事者の作業効率を向上させ、患者への対応時間を短縮します。
- 迅速かつ正確な医療サービスの提供は、患者満足度を高めます。
5S活動が患者安全に貢献する具体的な例
- 手術室:
- 医療器具の配置を最適化し、手術中の器具の受け渡しをスムーズにする。
- 手術室内の清掃と消毒を徹底し、感染症のリスクを最小限に抑える。
- 救急外来:
- 必要な医療器具をすぐに取り出せるように整理整頓し、救急患者への対応時間を短縮する。
- 救急カート内の物品配置を見直し、緊急時に必要なものがすぐに取り出せるようにする。
- 病棟:
- 患者の転倒リスクを減らすために、病室や廊下の整理整頓を徹底する。
- 医療器具や薬品の管理を徹底し、誤使用を防ぐ。
このように、5S活動は医療現場における様々なリスクを低減し、患者安全に大きく貢献します。
5S活動の具体的な効果測定
5S活動の具体的な効果測定は、活動の成果を可視化し、継続的な改善を促すために重要です。以下に、効果測定の具体的な方法と指標をまとめました。
定量的な効果測定
- 時間短縮:
- 作業時間、探し物時間、移動時間などを測定し、5S活動前後の変化を比較します。
- 例:医療器具の準備時間、書類の検索時間、患者の待ち時間など。
- コスト削減:
- 在庫削減、廃棄物削減、設備故障削減などによるコスト削減額を算出します。
- 例:期限切れ薬品の廃棄量、医療機器の修理費用、消耗品の購入量など。
- 品質向上:
- 不良品発生率、クレーム件数、感染症発生率などを測定し、5S活動前後の変化を比較します。
- 例:医療ミスの発生件数、院内感染の発生率、患者からのクレーム件数など。
- 安全性の向上:
- 労働災害発生件数、転倒事故件数などを測定し、5S活動前後の変化を比較します。
- 例:医療従事者の労働災害発生件数、患者の転倒事故件数など。
- スペース効率:
- 保管スペースの削減率、通路の確保率などを測定し、5S活動前後の変化を比較します。
- 例:病室のスペース効率、倉庫の保管効率など。
定性的な効果測定
- アンケート調査:
- 従業員や患者にアンケートを実施し、満足度、意識の変化、改善提案などを収集します。
- 例:職場環境に対する満足度、5S活動に対する意識、改善提案の件数など。
- インタビュー:
- 従業員や患者にインタビューを実施し、具体的な意見や感想を収集します。
- 例:5S活動による業務の変化、患者の心理的な変化など。
- 現場観察:
- 5S活動の実施状況や効果を、現場で直接観察し評価します。
- 例:整理整頓の状況、清掃状況、安全対策の実施状況など。
- チェックリスト:
- 5S活動の実施状況を定期的にチェックし、改善状況を評価します。
- 例:5Sチェックリストによる評価、改善提案の実施状況など。
効果測定のポイント
- 測定項目の明確化:
- 5S活動の目標に合わせて、効果測定の項目を具体的に設定します。
- 測定基準の設定:
- 効果測定の基準となる数値や評価方法を明確にします。
- 定期的な測定と評価:
- 定期的に効果測定を行い、改善状況を継続的に評価します。
- 結果のフィードバック:
- 効果測定の結果を従業員や関係者にフィードバックし、改善に繋げます。
病院における効果測定の具体例
- 医療器具の準備時間短縮:
- 5S活動前後の医療器具の準備時間を測定し、短縮効果を評価します。
- 院内感染の発生率低下:
- 5S活動前後の院内感染の発生率を比較し、感染症対策の効果を評価します。
- 患者満足度の向上:
- 5S活動前後の患者アンケート結果を比較し、患者満足度の変化を評価します。
- 医療ミスの減少:
- 医療ミスの件数を計測し5S活動による減少率を評価します。
これらの効果測定方法を組み合わせることで、5S活動の具体的な効果を把握し、より効果的な活動に繋げることができます。
5S活動の維持と継続的改善
5S活動を組織に定着させ、継続的な改善を促すことは、その効果を最大限に引き出すために不可欠です。以下に、5S活動の維持と継続的改善のための具体的な方法とポイントをまとめました。
5S活動の維持
- ルールと標準化の徹底:
- 5S活動のルールや手順を明確にし、文書化して全員に周知します。
- 定期的なチェックや監査を行い、ルールや手順が守られているか確認します。
- ルールや手順は、現状に合わせて定期的に見直し、改善します。
- 定期的なパトロールとチェック:
- 定期的なパトロールやチェックを行い、5S活動の実施状況を確認します。
- チェックリストを活用し、改善が必要な箇所を特定します。
- パトロールやチェックの結果を共有し、改善策を検討します。
- 評価とフィードバック:
- 5S活動の成果を定期的に評価し、従業員にフィードバックします。
- 良い取り組みは表彰するなど、モチベーション向上に繋がる仕組みを作ります。
- 改善が必要な箇所は、具体的な改善策を提示します。
- 教育と訓練の継続:
- 5S活動に関する教育や訓練を継続的に行い、意識の維持とスキル向上を図ります。
- 成功事例や改善事例を共有し、水平展開を図ります。
- 5S活動に関する情報を定期的に発信し、意識を高めます。
5S活動の継続的改善
- 改善提案制度の導入:
- 従業員からの改善提案を積極的に受け付ける制度を導入します。
- 改善提案は評価し、積極的に採用します。
- 改善提案の実施状況を共有し、改善意識を高めます。
- 定期的な見直しと改善:
- 5S活動の実施状況や効果を定期的に見直し、改善点を見つけます。
- 改善サイクル(PDCAサイクル)を回し、継続的な改善を図ります。
- 外部の専門家や他の企業の事例を参考に、改善のヒントを得ます。
- デジタルツールの活用:
- 5S活動の進捗管理や情報共有にデジタルツールを活用します。
- 写真や動画を共有し、改善前後の比較や改善事例を分かりやすく伝えます。
- データ分析を活用し、改善効果を可視化します。
- 全員参加の文化:
- 5S活動は、一部の担当者だけでなく、全従業員が参加する活動であることを再認識します。
- 従業員一人ひとりが、自分の持ち場を責任を持って管理し、改善提案を積極的に行います。
- 全員参加の文化は、組織全体の意識改革や改善意識の向上に繋がります。
5S活動継続のポイント
- 経営層の積極的な関与とリーダーシップ:
- 経営層が率先して5S活動に参加し、その重要性を発信します。
- 経営層の関与は、従業員の意識改革と活動の定着に大きく貢献します。
- 目標設定と計画的な推進:
- 5S活動の目標を明確にし、具体的な計画を立てて推進します。
- 目標達成度を定期的に評価し、計画の見直しを行います。
- モチベーション維持:
- 5S活動の成果を共有し、従業員のモチベーションを高めます。
- 表彰制度やインセンティブ制度を導入し、活動への参加を促進します。
5S活動の維持と継続的改善は、組織全体の意識改革と改善文化の醸成に繋がります。
5S活動を持続させるための体制づくり
5S活動を持続させるための体制づくりは、組織全体の意識改革と継続的な改善を促し、その効果を最大限に引き出すために不可欠です。以下に、5S活動を持続させるための体制づくりの具体的な方法とポイントをまとめました。
推進体制の構築
- 推進責任者の任命:
- 5S活動の推進責任者を任命し、活動全体を統括する。
- 推進責任者は、経営層と現場の橋渡し役となり、活動を推進する。
- 推進委員会の設置:
- 各部門の代表者からなる推進委員会を設置し、活動計画の策定や進捗管理を行う。
- 推進委員会は、定期的に会議を開催し、情報共有や課題解決を行う。
- 現場リーダーの育成:
- 各現場に5Sリーダーを配置し、現場での活動を推進する。
- 5Sリーダーは、現場の従業員を指導し、改善活動を支援する。
目標設定と計画的な推進
- 具体的な目標設定:
- 5S活動の目標を、数値や具体的な行動目標で設定する。
- 目標は、組織全体の目標と連動させ、達成度を評価できるようにする。
- 計画的な推進:
- 5S活動の計画を策定し、スケジュールや役割分担を明確にする。
- 計画は、現場の意見を取り入れ、現実的なものにする。
- 進捗管理と評価:
- 5S活動の進捗状況を定期的に確認し、評価する。
- 評価結果を共有し、改善に繋げる。
教育と意識啓蒙
- 継続的な教育:
- 5S活動に関する教育や研修を継続的に行い、意識の維持とスキル向上を図る。
- 成功事例や改善事例を共有し、水平展開を図る。
- 意識啓蒙活動:
- 5S活動の重要性を、ポスターや社内報などで周知する。
- 5S活動に関するイベントやコンテストを開催し、参加意識を高める。
評価とフィードバック
- 定期的な評価:
- 5S活動の成果を定期的に評価し、従業員にフィードバックする。
- 評価は、数値データだけでなく、現場の意見や感想も取り入れる。
- 表彰制度の導入:
- 5S活動に貢献した従業員や部門を表彰し、モチベーションを高める。
- 表彰制度は、公平性を保ち、全員が目標にできるようにする。
- 改善提案制度の導入:
- 従業員からの改善提案を積極的に受け付ける制度を導入する。
- 改善提案は評価し、積極的に採用する。
継続的な改善
- 改善サイクルの確立:
- PDCAサイクル(計画、実行、評価、改善)を回し、継続的な改善を図る。
- 改善活動は、小さな改善を積み重ねることを重視する。
- デジタルツールの活用:
- 5S活動の進捗管理や情報共有にデジタルツールを活用する。
- データ分析を活用し、改善効果を可視化する。
- 外部との連携:
- 外部の専門家や他の企業の事例を参考に、改善のヒントを得る。
- 5S活動に関するセミナーや研修に参加し、知識やスキルを向上させる。
トップのコミットメント
- 経営層の積極的な関与:
- 経営層が率先して5S活動に参加し、その重要性を発信する。
- 経営層のコミットメントは、従業員の意識改革と活動の定着に大きく貢献する。
これらの体制づくりを総合的に行うことで、5S活動を持続させ、組織全体の改善に繋げることができます。
図解で具体的な5S活動『改善事例』を紹介
清掃区分と清掃担当者の割付
5H1Wに従って工場内を職場別に分割してクリーン化の担当グループ、担当者を決める
改善前:担当者、不明
清掃道具の備え付け
まず始めに清掃道具の管理から始める
清掃しやすいレイアウトに変更
床配管、床配線及び設備のレイアウト
床配管、床配線及び設備のレイアウトを検討して安全で清掃しやすいレイアウトに変更する
改善前:
スライドシェアー ダウンロード資料
5S活動の資料が無料でダウンロードできます。
*工場の5Sについては下記の文献に色々な活動事例等が更に詳細に記載されています。
参考文献:
1) 5S (実践現場の管理と改善講座 )名古屋QS研究会 (編集)
3) 図解入門ビジネス最新5Sの基本と実践がよ~くわかる本 石川 秀人 (著)
4)会社がみるみる良くなる「5S」の基本 平野 裕之 (著), 古谷 誠 (著)