「平準化(へいじゅんか)の進め方
「平準化(へいじゅんか)」とは、業務や生産などの波をならして安定させることを指します。たとえば、忙しい日と暇な日の差をなくしたり、作業量のばらつきを減らしたりすることで、効率を上げたりミスを減らしたりするための手法です。
平準化とは
平準化(英語:Leveling)とは 限定された能力を有する生産資源に対して、一定期間における仕事の負荷の種類と量を平均化することである。
一般的には生産を平準化する”、“平準化生産を導入する”という使われ方をする。平準化生産と反対の概念を持つ用語として、“まとめ生産”が用いられる。
平準化はジャストインタイム生産の前提となる。
似た言葉として『標準化』があるがこれは平均化するのではなく効率的にムダのない生産を行うために手順、方法等をルール化することです。
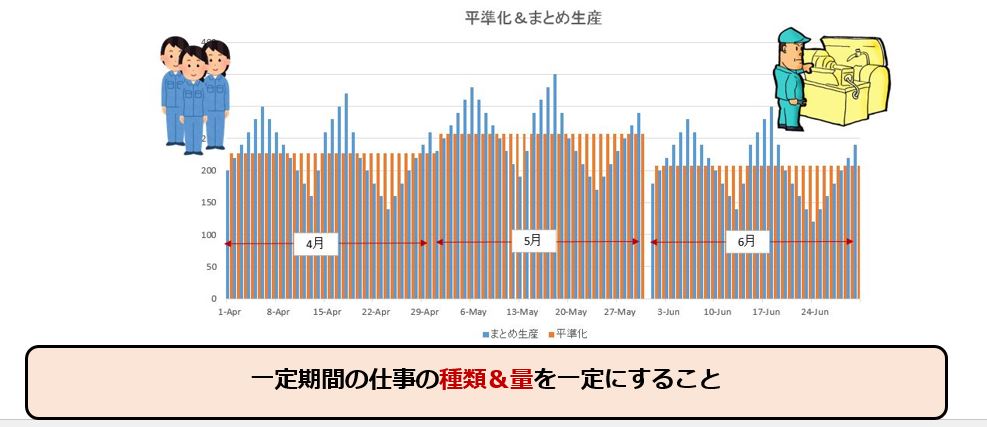
平準化とは
平準化 ポイント
1)バラツキをなくす平準化
①CとEは能力を超えてる、他の工程に負荷を移す。
②Eはボトルネック工程、ここから改善し、バラツキを圧縮する。
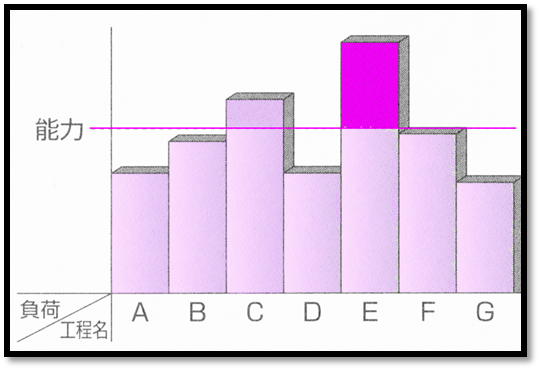
ボトルネック 平準化
2)まとめ生産と平準化生産
前工程と後工程を同期させて手待ちのムダを省く。
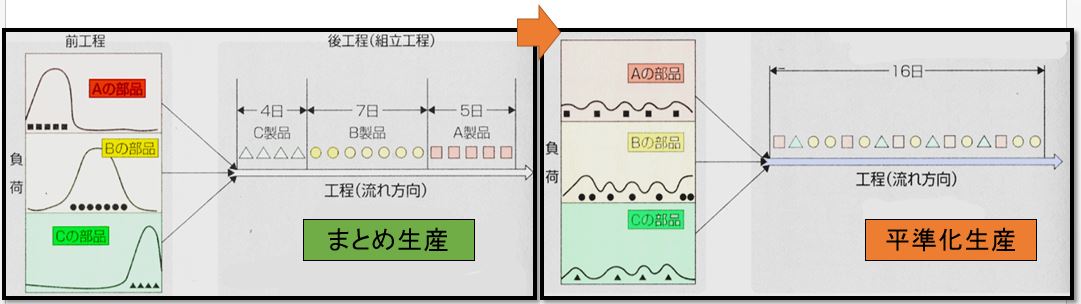
まとめ生産と平準化
平準化のメリット
過大な設備投資を避けられる
仕事の負荷に大きな変動があるとき、負荷のピークに合わせた設備を持っていないと、納期どおりに仕事を完成できない。しかし、ピーク以外の時期には設備が遊んでしまうことになり無駄である。負荷が平準化されていれば、平均負荷に見合う設備があれば需要に対応できる。
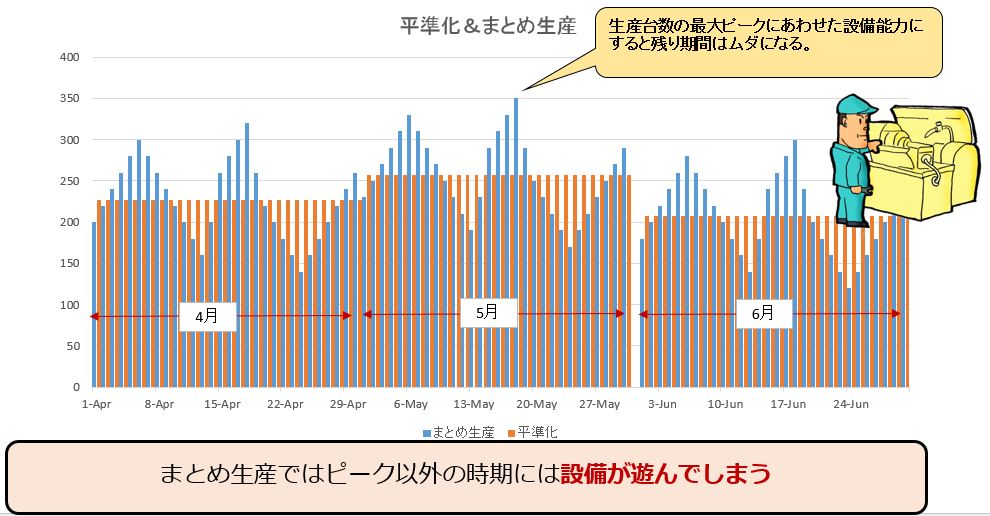
平準化と設備能力
作業者の大幅な変動を避けられる
設備同様、作業者もピーク時に合わせた人数が必要になる。しかし、短期間に作業者を雇用したり、解雇することはむずかしい。負荷が平準化していれば一定の人数で仕事をこなせる。
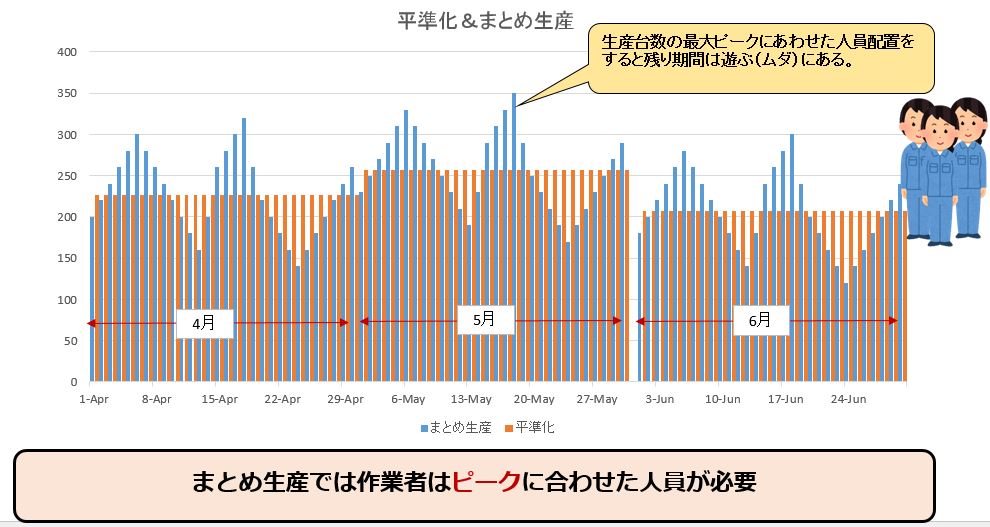
平準化と作業人員
過大な在庫を避けられる
市場(お客様の要求する商品、数量、納期)に同期した生産、出荷すれば、過大な在庫も持つ必要がなく、大きな倉庫も不要になり、在庫管理業務も削減できる。
市場が一つの後工程としてとらまえてJITの考え方である“必要なモノを、必要な時に、必要な量だけ”に対応し仕掛品を削減させる。
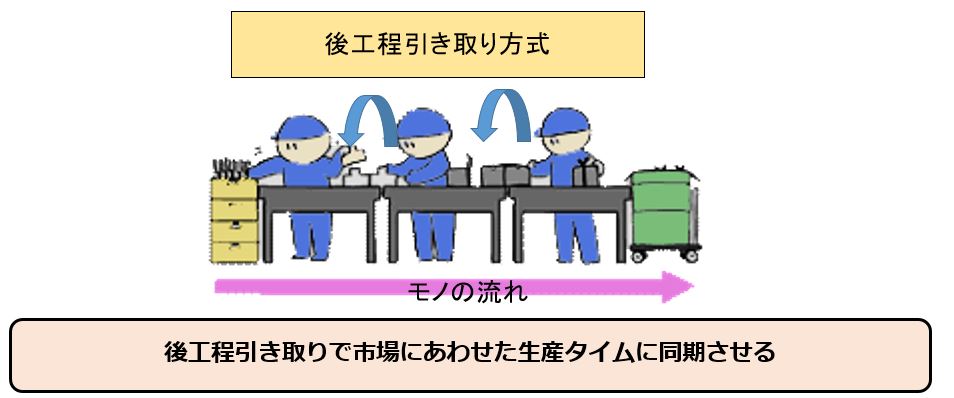
後工程引き取り方式 平準化
平準化の基礎知識
生産管理の目的は過剰な在庫を持つことなく、市場の要求する製品を、必要な時に必要な量だけ供給することである。其の為には市場で製品が売れたらすぐにその製品を売れた量だけ補充して次の需要の準備をし、JIT生産を実現しなければならない、よって平準化を実施するためには下記のような体系が整備されている必要がある。
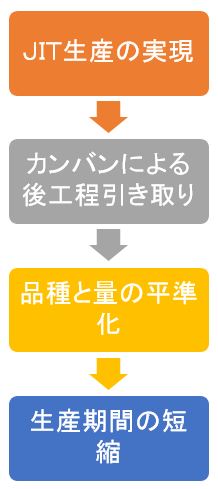
平準化の基礎知識
市場の需要情報を工場に伝えるかんばん
ジャスト・イン・タイム生産を実現している工場では、何をどれだけ補充すればよいかの情報を“引取りかんばん”と呼ばれるカードに記載してわかるようにしている。
最終製品メーカーである客先の工場で製品が売れたら、即、補充のための生産を開始する。そのために、必要な部品の引取りかんばんを仕入先の工場の製品倉庫まで運搬する。すると、仕入先工場は引き取りかんばんに記載されている部品をかんばんに記載されている量だけ客先に納入する。
このように、後工程が必要な製品や部品を前工程から引き取る方式は“後工程引取り方式”と呼ばれている。
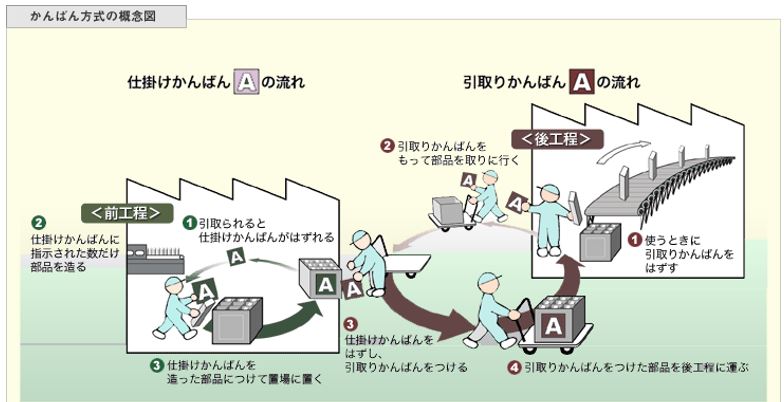
カンバン 後工程引き取り方式
円滑な引取りには生産の平準化が前提
客先の工場にとっては、カンバンを使って、仕入先から、必要な部品を即、引き取れるのは都合のよいことである。しかし、引き取り時期や引取り量が大きくばらついたらどうなるであろうか? 即納に対応しなくてはならない部品会社としては、いつ、どれだけ引き取られるかわからない状況では、すべての完成部品に対して、常に、ピーク量に匹敵する在庫を抱えておかなくてはならなくなる。
しかし、これは部品会社にとっては大変な負担である。しかし、客先工場からの需要が平準化されて、毎日、ほぼ同じ量が引き取られるのであれば、部品会社としても毎日、日産能力に見合う量をコンスタントに生産すればよいので負担はなくなる。さらに、部品会社に材料を納入する業者にとっても同様に負担が少なくなる。
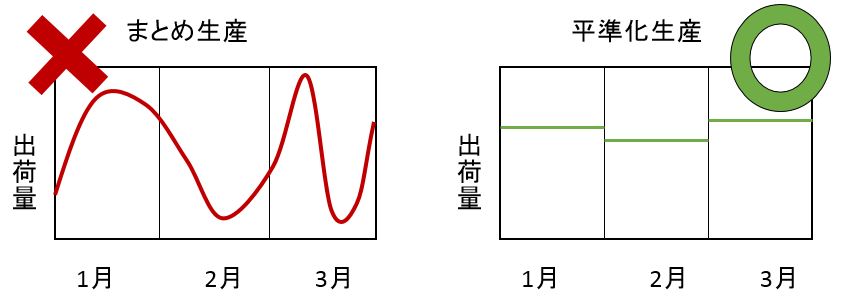
まとめ生産と平準化
生産期間の短縮が平準化の要
工程間を無駄なく同期させるためには生産期間が短い方が効率的である。
生産期間を短くする方法:工程待ち時間の短縮
生産期間とは材料が第一工程に投入されて完成品になるまでのトータル時間のことである。
生産期間の内訳を見ると最も、長い時間は加工時間ではなく、工程間の待ち時間であり、その比率は90%以上である。待ち時間が長くなる理由は、工程間の製造スピードが大きく異なっていることや、まとめ生産・まとめ運搬をするからである。したがって、工程間の待ち時間を短縮して、生産期間を短縮するためには、工程間の生産スピードの同期化、および工程間の運搬口ットを小さくして、小刻みな運搬を実現しなくてはならない。
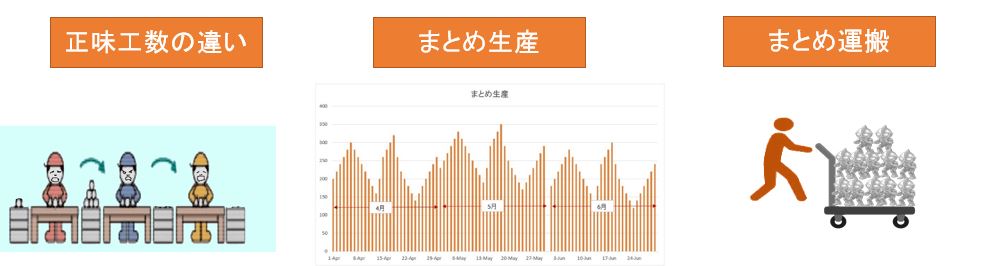
工程待ち時間の短縮
生産期間を短くする方法:運搬時間の短縮
工程間で運搬ロットを小さくして小刻みな運搬をすると運搬頻度が多くなり運搬にかかる時間が非常に長くなる恐れがある。運搬時間を短縮するためには工程間の距離を縮めることが大前提である。それに加えて、部品を積み込んだり、積み降ろす時間、すなわち、マテリアルハンドリング(マテハン)にかかる時間を短縮しなくてはならない。そのためには、専用箱や専用台車の開発が効果的である。表に運搬作業改善の着眼点を示す。
着眼点 | 内容 |
①運搬排除 | 1)レイアウトを改善し、工程間の移動を排除 2)工程の集約、統合の検討 |
②取扱い回数の削減 | 1)床への直置き、バラ置きの排除 2)積み替えの排除 3)荷姿の変更の排除 |
③運搬方式の見直し | 1)空運搬の廃止 2)バス方式(定期巡回)、タクシー方式(流し巡回)、ハイヤー方式(呼び出し)等を検討 |
④運搬距離の短縮 | 1)レイアウト検討 |
生産期間を短くする方法:作業時間の短縮
多品種生産では作業時間のうち、品種の切り替えに伴う段取り時間が相対的に大きくなる。したがって段取り時間の短縮することが生産期間の短縮のために非常に重要である。
段取り時間の短縮プロセス
下図は段取り時間短縮のプロセスを示している。

段取り時間の短縮
(1)現状の段取り作業の全体
改善前の段取り時間の中には、ムダな時間、材料や型を準備する時間、型を交換する時間、試し打ち・検査の時間、後片付けの時間などが意識的に区別されることなく混在している。
(2)段取り作業の分析
段取り改善の第一歩は、現状段取り作業の内訳の層別と分析である。作業を細かく観察し、それを大きく、内段取り作業、外段取り作業、ムダの3つに層別する。外段取り作業とは、機械を止めなくてもできる作業であり、次の製品の材料や型を、今の製品の生産中に準備することである。内段取りとは、機械を停止しなくてはできない作業であり、型や治工具の交換に伴う作業である。
ムダとはモノを探す時間、長すぎる運搬時間、ムリな作業のことである。
(3)ムダ時間の排除
作業の層別ができたら、真っ先に取り組むことは、ムダの排除である。職場の整理整頓、ムリな作業の改善等を実施する。
(4)内段取りの短縮
現在、機械を停止して行っている作業を、本当に機械を停止しなくてはできない作業かどうかを見直す必要がある。もし、機械を止めて、次の材料や型を準備しているようなら、即、前もって準備するように切り替える必要がある。
つまり、内段取り作業の外段取り化である。それに加えて、本当の内段取り作業も短縮しなくてはならない。その中でもウエートが高いのが“調整作業“である。機械と型の芯を合わせたり、刃先の出具合を調整する時間を短くすることである。目で見ながらアナログ的に調整しているような作業があれば、是非、メモリをつけるなどデジタル化すべきである。
(5)外段取りの改善
最後に、外段取り作業自体を改善する。材料や型置き場の整理整頓はもとより、外段取りを2人で並行することも効果的である。
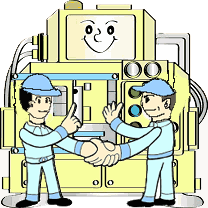
平準化 並行作業
平準化の計算式
例では組付ラインで製品A、B、Cの3種類をそれぞれ240個、160個、80個、組みつけており、一日の合計が480個だとする。すると、各製品の出現確率はそれぞれ次のようになる。
Aの出現確率=240/480=1/2
Bの出現確率=160/480=1/3
Cの出現確率= 80/480=1/6
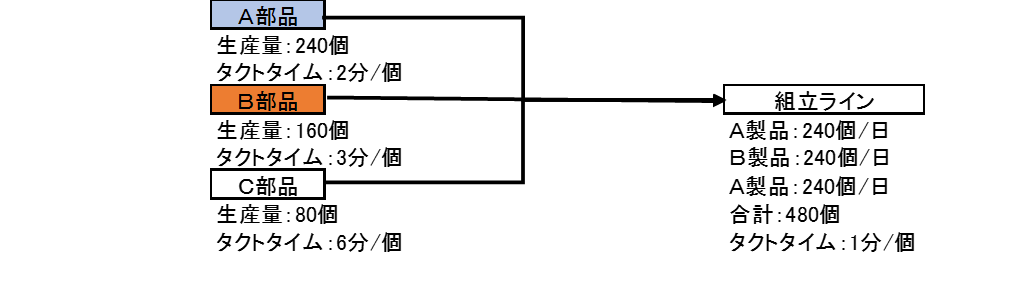
平準化 計算
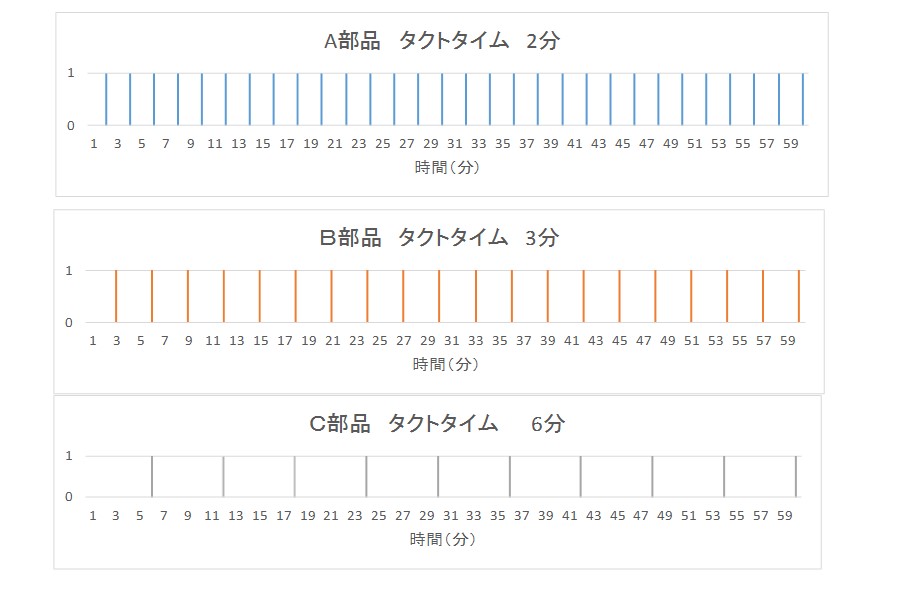
各部品のタクトタイム
この製品別の出現確率をベースに生産順序を以下のように決めてゆく。
1番目の製品の決定
・最も出現確率の大きいAに決める。
2番目の製品の決定
・Aはすでに1番目に出現しているので
2番目にAが出現する確率= 1/2×2-1=0
・2番目にBが出現する確率= 1/3×2=2/3
・2番目にCが出現する確率= 1/6×2 = 1/3
したがって、最も確率の大きいBに決める。
3番目の製品の決定
・3番目にAが出現する確率= 1/2×3-1=0.5
(Aはすでに1番目に出現している)
・3番目にBが出現する確率= 1/3×3-1=0
(Bはすでに2番目に出現している)
・3番目にCが出現する確率= 1/6×3=0.5
したがって、3番目はAまたはCになるが、Aはすでに出現しているのでCに決める(理屈の上ではどちらでもいい)。同様の順で後の順番も決定。
製品毎 出現確率計算表とグラフ
生産期間が長いと設備トラブル等で同期がとれなくなると再度、同期できるまでに長い期間を必要とする、逆に生産期間が短いと少ない時間で同期が回復できる。
例えば七夕の織姫と彦星は一年に一回しか会えないが、一度 問題が発生すると1年間は合えなくなるが期間を一か月に短縮すれば1か月間だけで済む。
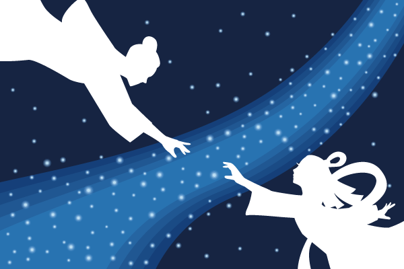
七夕 一年に一回の出会い
平準化と標準化の違い
「平準化」と「標準化」は、似たような響きですが、意味も使われる場面も異なります。それぞれ簡潔に説明しますね。
平準化(へいじゅんか)
意味:変動をなくして、ならすこと。
主な用途:
生産や業務の負荷を一定に保つこと。
需要や供給の波を小さくすること。
例:
生産平準化:忙しい時期と暇な時期の差をなくし、毎月一定量を生産する。
業務平準化:特定の人にだけ負荷が集中しないように、業務を分散する。
標準化(ひょうじゅんか)
意味:ばらつきをなくして、共通のルールや基準に合わせること。
主な用途:
作業手順や品質を一定の基準に統一すること。
製品、サービス、業務などのばらつきを減らすこと。
例:
作業標準化:誰がやっても同じ品質になるようマニュアルを整備。
製品標準化:部品サイズや規格を統一してコスト削減を図る。
■ 違いのまとめ
項目 | 平準化 | 標準化 |
---|---|---|
主な目的 | 変動をなくして「ならす」 | ばらつきをなくして「統一」 |
対象 | 時間・負荷・量の変動など | 品質・手順・規格のばらつき |
使われる場面 | 生産管理、業務スケジューリング | 品質管理、マニュアル作成など |
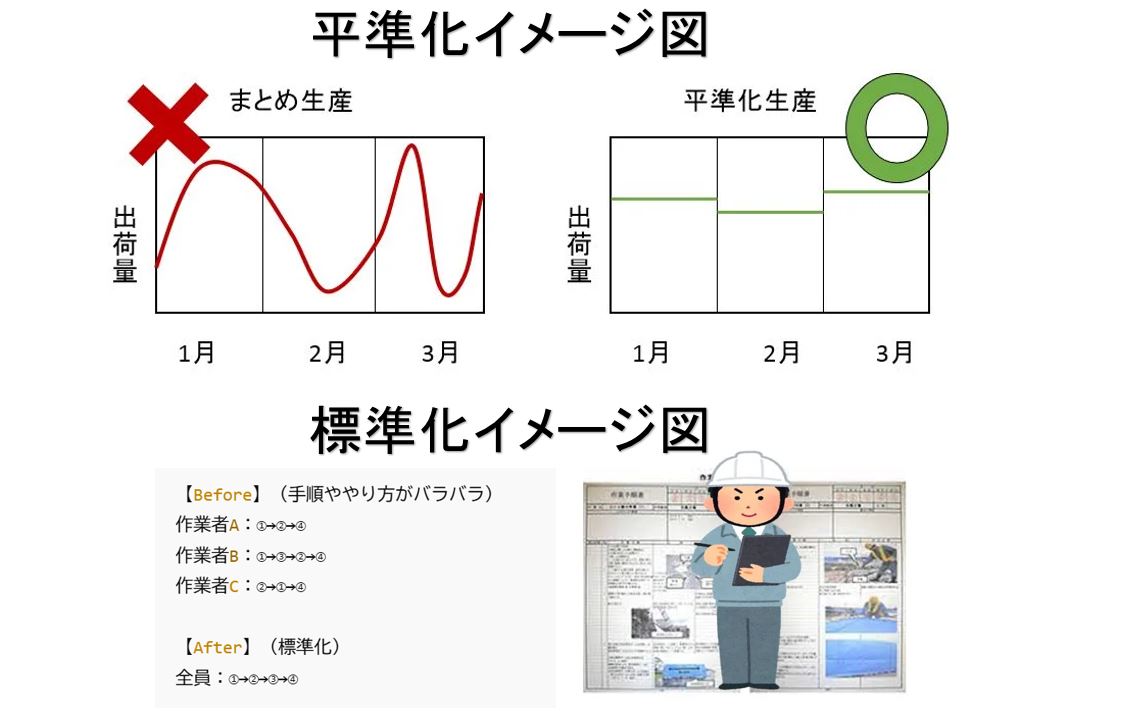
平準化と標準化の違い
平準化に関わるツールとシステム
生産・製造業向け
ツール/システム | 主な機能と役割 |
---|---|
かんばん方式(看板) | トヨタ生産方式の代表格。必要な物を必要な時に生産する。余剰在庫を抑えることで、生産を平準化。 |
生産スケジューラー | 生産計画を立てて、工程やラインの負荷を平準化。代表例:Asprovaなど。 |
MRP(資材所要量計画) | 部品や原材料の供給タイミングを平準化して在庫を最適化。 |
JIT(ジャストインタイム) | 必要な物を、必要な時に、必要な量だけ生産。ムダをなくして平準化。 |
業務・プロジェクト管理向け
ツール/システム | 主な機能と役割 |
---|---|
WBS(Work Breakdown Structure) | タスクを分割し、リソースを平準化。特定の人に負荷が集中しないように配分。 |
ガントチャートツール(例:Backlog, Redmine, Wrike) | タスクの進捗・スケジュールを可視化し、業務負荷を平準化。 |
リソースマネジメントツール(例:Kintone、Asana) | チーム内の工数・スキルに合わせて業務を平準化。 |
サービス業・コールセンター等
ツール/システム | 主な機能と役割 |
---|---|
シフト管理システム(例:KING OF TIME、ジョブカン) | スタッフの出勤・業務量のバランスを取り、ピーク時間を平準化。 |
需要予測AIツール | 顧客数や注文数の予測に基づいて、最適な人員配置を可能に。 |
平準化を進めるポイント
データの可視化:どこに負荷が偏っているかを見える化することがスタート。
ルール化との連携:平準化を進めるには、ある程度の**標準化(作業統一)**も必要。
柔軟な対応力:人や物の動きを固定せず、状況に応じて調整できる仕組みが大事。
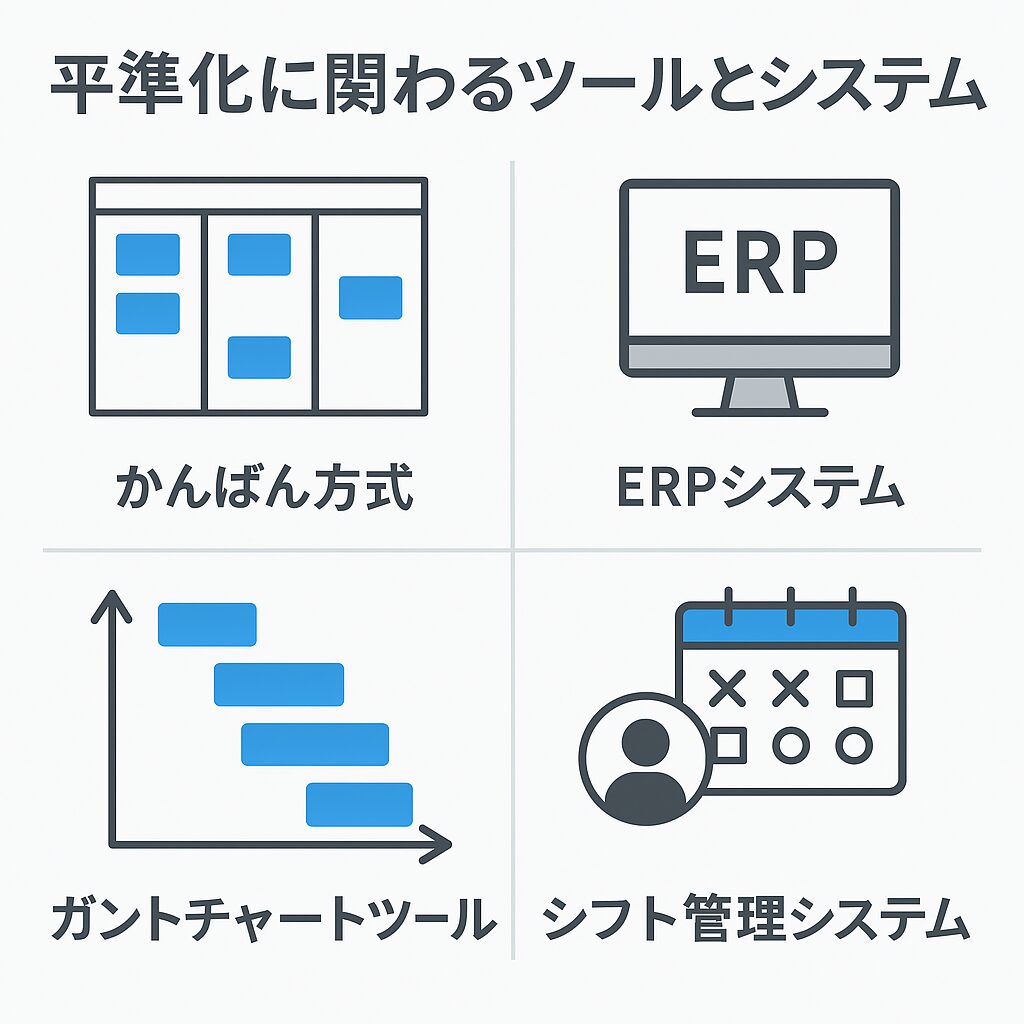
平準化に関わるツールとシステム
平準化のデメリットと対策
柔軟性の低下
内容:平準化されたスケジュールにこだわりすぎると、突発的な需要やトラブルへの対応が難しくなる。
対策:
バッファ(余裕時間や在庫)を適度に持たせる。
緊急時用のリソースや「柔軟要員」を事前に用意しておく。
初期導入の手間・コスト
内容:平準化のための業務整理やシステム導入にコストや時間がかかる。
対策:
部門単位や一部工程から段階的に導入する(スモールスタート)。
補助金やクラウド型ツールで初期コストを抑える。
従業員のモチベーション低下
内容:仕事量を均一にされることで、「忙しいときだけ頑張る」というスタイルに慣れた人がやりがいを失う場合も。
対策:
単調に感じないように、業務にバリエーションを持たせる。
成果だけでなく安定運用への貢献も評価する仕組みを導入。
季節変動や繁閑の波への対応が難しい
内容:平準化は「波をならす」考えだが、季節変動など波が避けられない業界では限界がある。
対策:
変動が激しい部分は「変動対応ゾーン」として別管理する。
予測AIや需要分析を使い、変動の見える化と準備を行う。
標準化との混同・誤用
内容:平準化と標準化を混同して、作業手順までガチガチにしようとすると逆効果になることも。
対策:
「平準化=量とタイミングのならし」と理解を徹底。
柔軟性を保ちつつ標準化とバランスを取る。
デメリット | 主な対策 |
---|---|
柔軟性が下がる | バッファや緊急対応体制を準備 |
初期導入に手間やコストがかかる | スモールスタート+安価なツール活用 |
モチベーションの低下 | バリエーション+公正な評価制度 |
季節変動への対応が難しい | AI予測・変動ゾーン管理で補完 |
標準化との混同 | 概念の正しい理解と社内共有 |
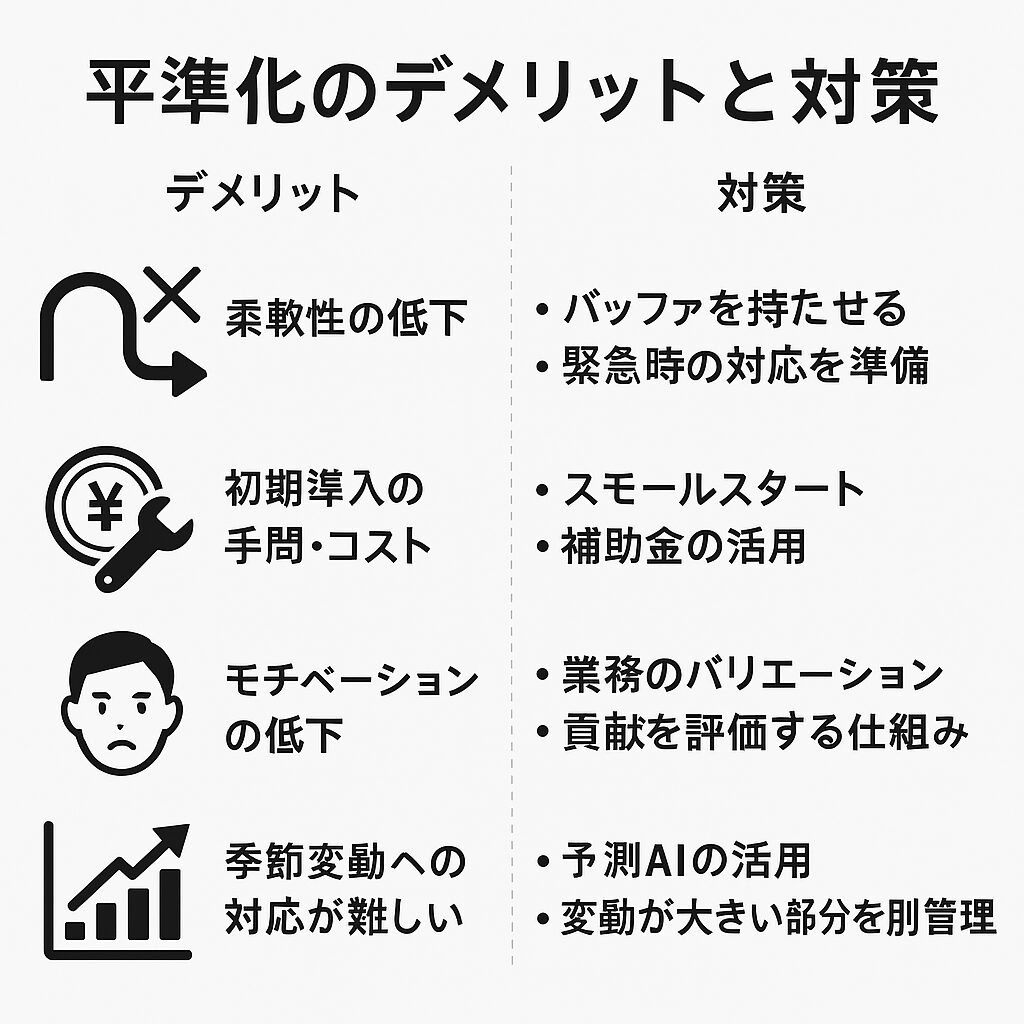
平準化のデメリットと対策
具体的な平準化のすすめ方(ステップ形式)
現状把握
日々の業務量や生産量、作業時間などを記録
繁忙・閑散のタイミングや原因を明確にする
課題の特定
どこに「ムラ(ばらつき)」があるかを分析
なぜそのムラが起きるのか、要因を洗い出す(納期、顧客要求、作業手順など)
標準化を検討
作業手順や対応方法の標準化(マニュアル化など)
誰がやっても同じような品質・スピードになるように整える
作業の平準化
作業を1日・1週間・1ヶ月単位で均等に割り振る
繁忙期の前倒し、閑散期の有効活用を検討
リソースの見直し(人員配置の最適化)
仕組みでならす
自動化ツールや管理システムの導入
生産スケジューラーやタスク管理アプリの活用
効果検証と改善
実行後にデータを再確認
平準化により、効率・品質・コストにどんな変化があったかを測定
必要に応じて再調整
平準化 シュミレーション 事例
ある工場で2種類の製品A、Bを製造しているとする。
表1のように、どの製品も一日当たりの需要数は平均50個、誤差は±20%とする(すなわち、40個から60個の間でばらつく)。ある月の需要が表のようであった場合、月単位のまとめ生産をする場合と、一日レベルで平準化生産をする場合に、製品在庫量や、売上機会損失にどのような影響の差異が発生するかを比較してみる。
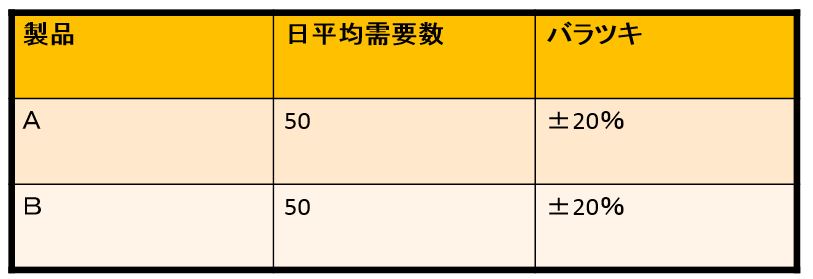
平準化シュミレーション
月間 まとめ生産計画表の事例
製品A,Bを下記のスケジュールでまとめて生産。
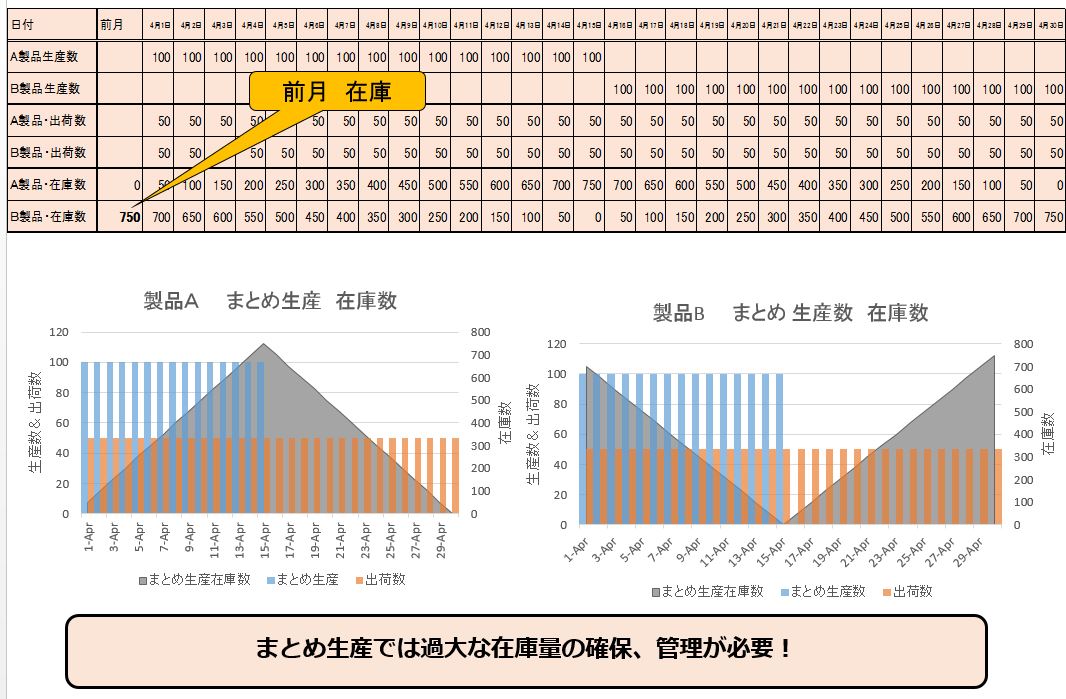
まとめ生産 事例
月間 平準化 生産計画表 事例
製品A,Bを下記のスケジュールで平準化 生産。
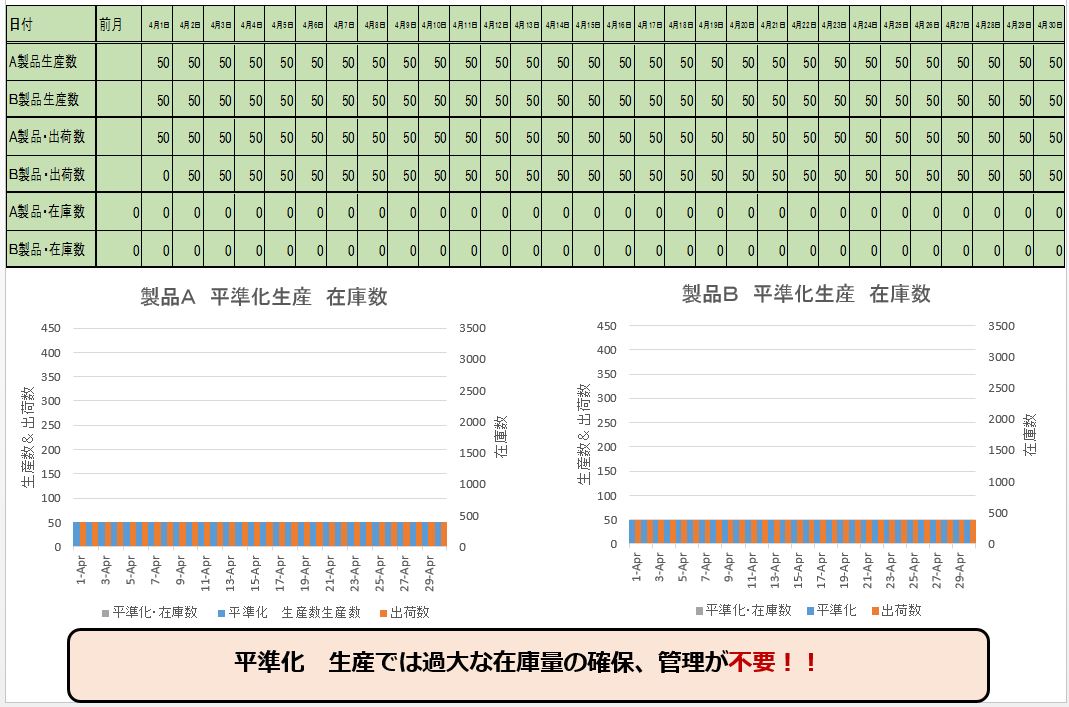
平準化 生産計画事例
平準化の未来の展望
平準化の未来は、テクノロジーの進化とともに大きく変わりつつあります。これまでの「人の経験と勘」に頼った調整から、データドリブンかつ柔軟な仕組みへと進化していくと見られています。
以下に、平準化の未来に関する展望をいくつか紹介します。
AIと需要予測による「動的平準化」
これまでの平準化は「過去の実績」ベースが多かった。
これからはAIがリアルタイムで需要を予測し、その場で最適な配分や生産計画を自動で調整。
➤ 例:天気・SNS・イベント情報なども考慮して販売量を調整。
デジタルツインによるシミュレーション平準化
仮想空間で現実の生産現場を再現し、負荷バランスや作業配分をリアルタイムで検証可能。
➤ 導入前に「もし○○が起きたら?」を試せるので、無理なくスムーズな平準化が実現。
多能工と人的資源の再配置
働き方の多様化により、1人で複数スキルを持つ人材(多能工)が重要に。
平準化された作業でも、人材配置の柔軟性があることで対応力が向上。
➤ 「人に仕事を合わせる」から「仕事に人を合わせる」へ。
サステナビリティとの両立
無駄なピーク生産や過剰在庫を抑えることで、エネルギー・資源の削減にも貢献。
➤ 平準化は「脱炭素・持続可能な運用」のカギとしても注目。
属人化からの脱却(ノウハウの形式知化)
AI・自動化によって、熟練者のノウハウを標準化・共有化。
属人化を避けながら、「平準化のコツ」そのものをシステムに取り込む動きが拡大。
未来の平準化はこう変わる
従来型平準化 | 未来型平準化 |
---|---|
人手と経験に依存 | AI・デジタル主導 |
静的なスケジュール調整 | 動的・リアルタイムな調整 |
現場ごとの属人的ノウハウ | 全社的に共有されたノウハウ |
業務効率中心 | サステナビリティと両立 |
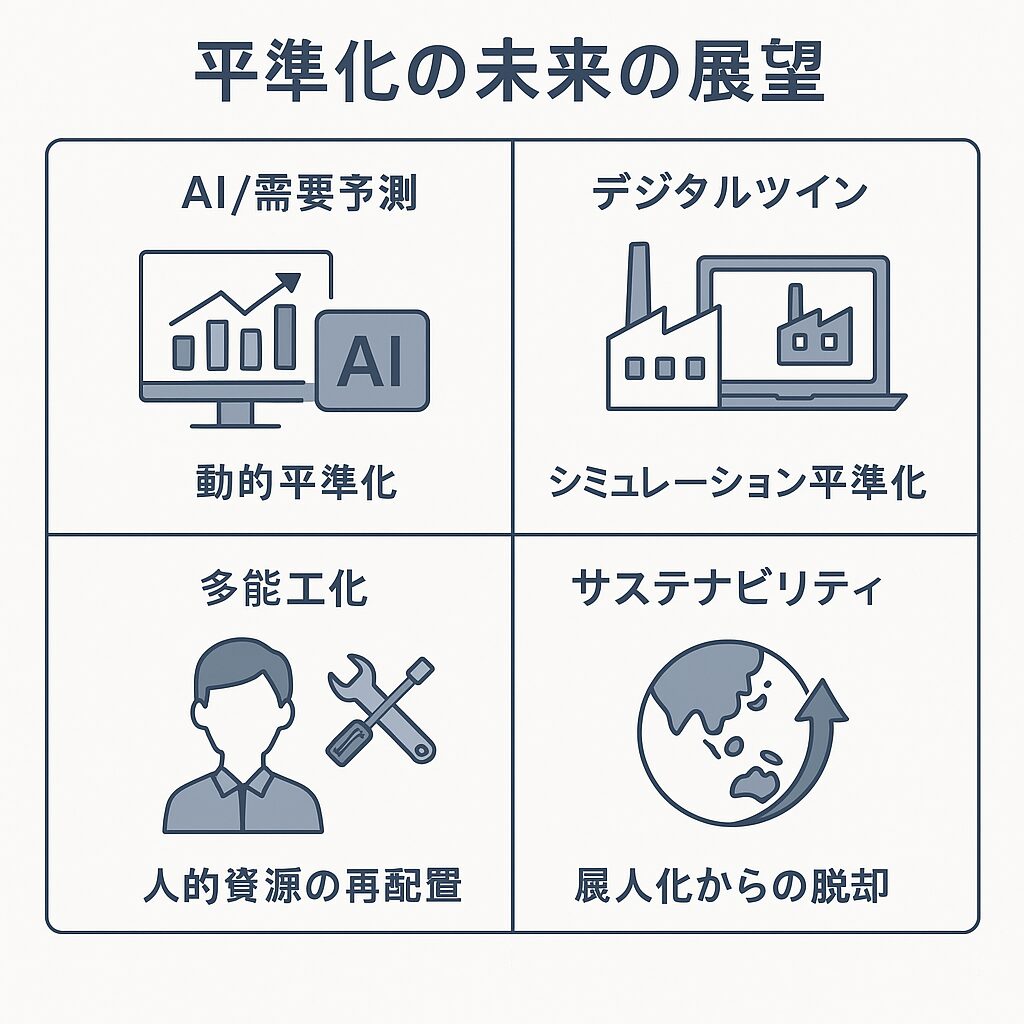
平準化の未来の展望
参考文献:
コメント