人と機械設備の作業を分析するM-Mチャート
自動車レースの最高峰 (F1)では、レース中にピットインした瞬間に「タイヤの交換」「エンジンの出力調整」「サスペンションの硬さ調整」などを行っている。ピットインでの時間がレースの勝敗に影響するので、0.1秒でも速く作業を終了しなければならない。ピットインの作業のように、「2人以上の人」が連合して行う作業や「人と機械設備」の作業形態を連合作業といい、連合作業分析(M-Mチャート)により分析する。
M-Mチャート(連合作業分析)とは
連合作業分析とは、「人と機械設備」や「人と人」による一連の作業手順を、共通の時間目盛りを用いた1枚の用紙に記録し、それぞれの作業内容の時間的な順序と手待ち時間を含めた相互の関係を明確に表現した図表である。
連合作業分析の結果、ムダな作業を排除または減少させる改善により作業手順、作業分担、レイアウトなどの変更がもたらされる。

M-M チャート-事例
M-Mチャートの目的
- 人と機械の作業の流れを可視化し、無駄な時間や動作を特定する。
- 作業の効率化、時間短縮、コスト削減を図る。
- 作業者の負担を軽減し、安全性を向上させる。
- 作業手順の標準化や改善に役立てる。
M-Mチャートの構成要素
- 作業者と機械の作業内容を時系列で記録する。
- 作業時間、手待ち時間、機械の稼働状況などを明確に示す。
- 作業の開始から終了までの流れを把握できるようにする。
M-Mチャート エクセル テンプレート
M-Mチャート(Man-Machineチャート)のテンプレートを2種類ご紹介します。Excel向けの表形式です。改善活動や現場観察に役立ちます。
下記よりM-Mチャート エクセル テンプレートがダウンロードできます。
M-Mチャート(連合作業分析)の手順
駅の窓口で指定券を購入する作業は、「お客」「駅員」「端末機」の連合作業である。この例で、連合作業分析の手順を述べる。
①作業を区分し、何の作業で構成されてぃるかを確定の仕事のスタート作業を規定する。
②それぞれの順序と相互関係をつかみ、作業手順・作動順序を確定する。
③時間研究の要領で作業時間を測定し、各作業の時間値を決める。
①~③の手順をまとめたものが次である。
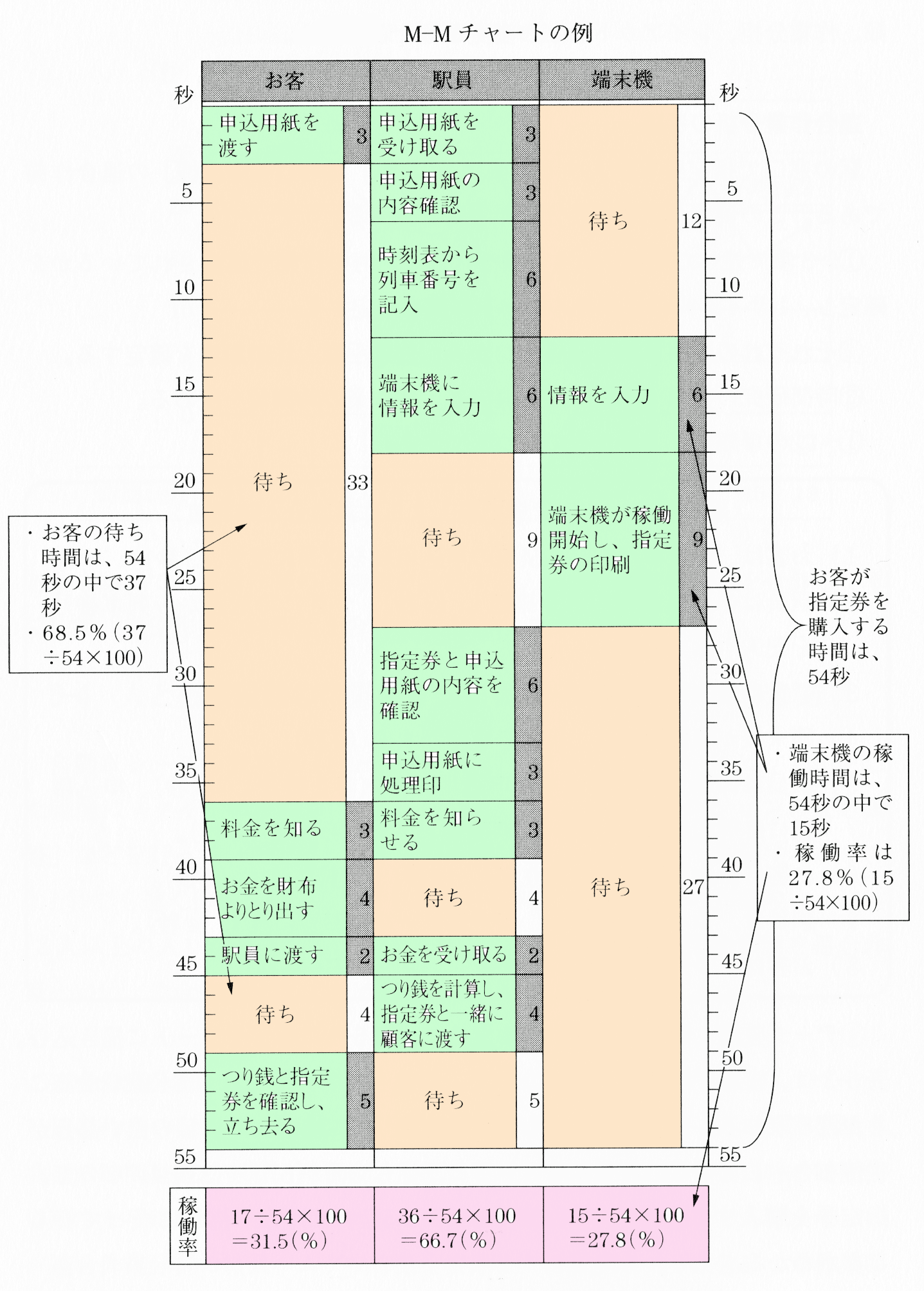
M-Mチャートの例
駅の窓口で指定席券を購入する作業区分と時間値
1)お客は、必要事項を記入済みの申込用紙を駅員に渡す(3秒)。
2)駅員は申込用紙の内容を確認し(3秒)、つぎに時刻表から列車番号を記入する(6秒)。
3)駅員は端末機に情報を人力する(6秒)。
4)端末機が稼働開始し、指定券を印刷する(9秒)。
㈲駅員は印刷された指定券と申込用紙の内容を確認し(6秒)、申込用紙に処理印を押し(3秒)、料金をお客に知らせる(3秒)。
6)お客はお金を財布より取り出し(4秒)、駅員に渡す(2秒)。
7)駅員は、つり銭を計算し、指定券と一緒にお客に渡す(4秒)。
8)お客は、つり銭と指定券を確認し、立ち去る(5秒)。
④データ整理と問題点を抽出するために、下表に示すチャートに描き込む。
下表は、縦軸が時間値(秒)なので、指定券を購入するには54秒かかることが、読み取れる。
仕事をしてぃる時間値は塗りつぶされ、時間値の白い部分が手待ちを示してぃる。お客に着目すると、待ち時間が37秒(33+4)なので、指定券を購入する54秒のうち68.5%(37÷54×100)も手待ちになっていることがわかる。
生産ラインにおけるM-Mチャートの効果
生産ラインにおける M-Mチャート(Man-Machineチャート) は、作業者(Man)と機械(Machine)の作業・稼働状況を可視化するツールで、生産性向上や無駄の排除に大きな効果を発揮します。以下にその主な効果をまとめます。
M-Mチャートの効果
作業と待ちの時間の「見える化」
作業者と機械の動作・待機時間を時間軸で示すことで、どこにムダがあるか明確になります。
例:作業者が機械の動作終了を待っている時間が長い → 改善の余地あり
稼働率・稼働バランスの把握
機械と人の稼働率を比較し、どちらがボトルネックかを特定できます。
稼働率が低い箇所は、工程の組み替えや自動化の検討ポイントになります。
作業の標準化・最適化
複数の作業者や機械を組み合わせたラインの最適化設計に活用されます。
標準作業を作る際のベースにもなります。
多能工化や作業の平準化に有効
一人の作業者が複数の機械を担当するパターン(多台持ち)を検討する際に使えます。
人と機械の最適なバランスを見つける助けになります。
改善活動の根拠資料として活用
現状分析の資料として、改善提案やカイゼン活動のスタート地点に最適です。
実際の活用例
作業者 | 機械 | 状況 |
---|---|---|
○ | ■ | 作業中 |
▭ | ▭ | 待機中 |
↑ | ↓ | 切替・準備 |
上記のように、チャートで時間の流れを視覚化することで、改善点が誰でも分かりやすくなります。
効果的な使い方のコツ
現場での実時間観測(タイムスタディ)をベースに作成
5S活動やIE(インダストリアル・エンジニアリング)手法と組み合わせる
変更前と変更後で比較し、効果を数値化する
トヨタのM-Mチャート活用事例
トヨタ自動車は、長年にわたり生産方式の改善を重ねており、M-Mチャート(マン・マシンチャート)もその中で重要な役割を果たしています。トヨタにおけるM-Mチャートの活用事例として、以下の点が挙げられます。
トヨタ生産方式(TPS)における活用
- トヨタ生産方式は、「ジャストインタイム」と「自働化」を柱としており、M-Mチャートはこれらの実現に貢献しています。
- 作業のムダを徹底的に排除し、必要なものを必要な時に必要なだけ生産するジャストインタイムの実現。
- 異常が発生した際に機械が自動的に停止し、品質不良の発生を防ぐ自働化の実現。
- M-Mチャートは、人と機械の作業の連携を詳細に分析し、ムダな時間や動作を徹底的に排除することで、生産効率の向上に貢献しています。
具体的な活用事例
- 組み立てラインの最適化:
- 自動車の組み立てラインでは、多くの作業者と機械が連携して作業を行います。
- M-Mチャートを活用することで、作業者と機械の動きを詳細に分析し、作業の重複やムダな時間を排除することで、サイクルタイムの短縮や生産性の向上に貢献しています。
- 機械加工ラインの効率化:
- 機械加工ラインでは、作業者が複数の機械を担当する「多台持ち」の作業が行われることがあります。
- M-Mチャートを活用することで、作業者の動きと機械の稼働状況を詳細に分析し、最適な作業配分を検討することで、生産効率の向上や省人化に貢献しています。
- 品質管理:
- M-Mチャートは、品質管理においても活用されています。作業工程における人や機械の動きを詳細に分析することで、品質不良が発生する可能性のある箇所を特定し、改善策を講じることで、品質の安定化に貢献しています。
トヨタにおけるM-Mチャート活用の特徴
- 継続的な改善:
- トヨタでは、M-Mチャートを活用した分析結果をもとに、継続的に作業の改善を行っています。
- 改善活動は、現場の作業者を中心に行われ、改善提案制度などを通じて、全従業員が改善活動に参加する体制が構築されています。
- 標準作業の重視:
- トヨタでは、M-Mチャートを活用して最適な作業手順を確立し、標準作業として定めています。
- 標準作業を徹底することで、作業のバラつきを抑え、品質の安定化や生産性の向上に貢献しています。
トヨタにおけるM-Mチャートの活用は、単なる作業効率の向上だけでなく、品質向上やコスト削減にも貢献しています。トヨタ生産方式の根底にある「ムダの排除」と「継続的な改善」の考え方が、M-Mチャートの効果を最大限に引き出していると言えるでしょう。
他企業における活用事例
M-Mチャートは、トヨタ自動車に限らず、様々な企業で生産性向上や効率化のために活用されています。以下に、他企業における活用事例をいくつかご紹介します。
食品業界
- 味の素、キユーピー:
- 工場内のムダ削減、歩留まり向上
- 原材料の投入から製品の包装までの一連の作業を分析し、生産ラインの最適化を図る。
- 食品加工ラインにおける作業者と機械の連携を分析し、効率的な作業手順を確立する。
物流業界
- ヤマト運輸、佐川急便:
- 仕分け工程の効率化、再配達の削減
- 物流倉庫内での作業者の動きと機械の稼働状況を分析し、最適な作業配分を検討する。
小売業界
- セブンイレブン:
- 発注のジャスト・イン・タイム化、在庫最適化
- 店舗における商品の陳列作業やレジ業務を分析し、作業効率の向上を図る。
サービス業
- コールセンターやホテル業界:
- 業務フローの標準化、対応品質の向上
- 顧客対応における作業者の動きとシステムの稼働状況を分析し、対応時間の短縮や品質向上を図る。
機械加工ライン
- 機械加工ラインでは、作業者が複数の機械を担当する「多台持ち」の作業が行われることがあります。
- M-Mチャートを活用することで、作業者の動きと機械の稼働状況を詳細に分析し、最適な作業配分を検討することで、生産効率の向上や省人化に貢献しています。
M-Mチャートの活用による改善効果
M-Mチャート(Man-Machineチャート)を活用することで得られる改善効果は、現場の「見える化」から始まり、作業効率・稼働率・コストなどに幅広く波及します。以下にその代表的な効果を具体的に紹介します。
人と機械の稼働率向上
現状:作業者が機械の完了を待つ時間が長い
改善:作業者が複数台の機械を並行して扱う(多台持ち)ことで待機時間を削減
効果:作業者の有効稼働率が向上し、1人当たりの生産性がアップ
ボトルネックの明確化と解消
可視化により、機械や作業者の待ち時間が集中している箇所(=ボトルネック)がわかる
例えば、機械Aだけ加工時間が長いなら、機械の更新や加工条件の見直しを検討できる
ラインバランスの最適化
作業者・設備の配置や作業の順序を見直し、最適な人と機械のバランスを実現
作業を均等に分担して、偏りや遊休を削減
作業の標準化と教育効率向上
一連の動作をチャートで示すことで、標準作業の構築や新人教育に役立つ
視覚的な説明で教育がしやすく、ばらつきのない作業が可能になる
無駄の発見とカイゼン活動の推進
「待ち」「ムダな移動」「空き時間」などが一目で分かる
継続的改善(KAIZEN)の根拠資料として、PDCAサイクルを回しやすくなる
コストダウン・省人化
人員配置の最適化により、同じ作業量をより少ない人員でこなせるようになる
また、自動化の導入タイミングの判断材料にも使える
活用事例(イメージ)
Before(改善前) | After(改善後) |
---|---|
作業者が1台の機械を担当し、加工終了まで待つ | 1人で3台の機械を順番に操作する多台持ち方式へ |
稼働率:人50%、機械80% | 稼働率:人85%、機械95% |
待機時間が多く、作業者が手持ち無沙汰 | スムーズな作業の流れでタイムロス減 |
M-Mチャートを用いたタイムスタディの進め方
M-Mチャート(Man-Machineチャート)は、作業者(Man)と機械(Machine)の動作を時間軸に沿って記録し、作業の効率や無駄を分析するための図表です。タイムスタディ(時間研究)においては、作業の流れや時間配分を視覚的に把握し、改善点を見つけ出すのに非常に有効です。
以下に、M-Mチャートを用いたタイムスタディの進め方をわかりやすく説明します。
目的の明確化
まずは何のためにM-Mチャートを作成するのかを明確にします。
作業の無駄を発見したいのか?
作業と機械の稼働率を把握したいのか?
作業標準時間を設定したいのか?
対象作業の選定
改善の余地がありそうな作業、あるいは代表的な作業を選びます。
作業の観察と記録
作業者と機械の動きを観察し、作業内容を細かく分解します。
作業者の動作(準備、操作、待機など)
機械の動作(加工、待機、停止など)
ストップウォッチや動画撮影を活用し、正確な時間を測定します。
M-Mチャートの作成
縦軸に作業者と機械を、横軸に時間を取り、動作の流れをブロックなどで記入していきます。
例:
時間(秒) | 作業者(Man) | 機械(Machine) |
---|---|---|
0〜5 | 材料をセット | 停止 |
5〜30 | 操作ボタン押す・待機 | 加工中 |
30〜35 | 完成品取り出し | 停止 |
35〜40 | 材料セット | 停止 |
… | … | … |
分析
チャートを見ながら、以下のような点をチェックします。
作業者や機械が「待機」している時間はないか?
作業者と機械が同時に作業している時間はどれくらいか?
機械が動いている間、作業者が遊んでいないか?
どこに改善の余地があるか?
改善案の立案
無駄な動作を削減したり、作業を並列化するなどの改善案を考えます。
⑦改善後の検証
改善後、再度M-Mチャートを作成し、改善の効果を確認します。
M-MチャートとIE(工業工学)の関係
M-Mチャート(マン・マシンチャート)とIE(工業工学)は、密接な関係にあります。IEは、生産システムの効率化や改善を目的とした学問であり、M-Mチャートはそのための有効なツールの1つです。
IEにおけるM-Mチャートの位置づけ
- 作業分析のツール:
- IEでは、作業の効率化を図るために、様々な分析手法を用います。M-Mチャートは、人と機械の連合作業を分析し、ムダを可視化するためのツールとして活用されます。
- 方法研究の応用:
- IEにおける方法研究は、作業の最適な手順や方法を追求するものです。M-Mチャートは、作業の流れや時間の分析を通じて、より効率的な作業方法を見つけるために役立ちます。
- 時間研究との連携:
- IEにおける時間研究は、作業時間を測定し、標準時間を設定するものです。M-Mチャートは、作業時間や手待ち時間を詳細に記録することで、時間研究の精度を高めることに貢献します。
- 生産性向上のための基盤:
- IEの目的は、生産性向上、コスト削減、品質向上などです。M-Mチャートは、これらの目標達成のための基盤となるデータを提供し、改善活動を支援します。
M-MチャートがIEにもたらす効果
- ムダの可視化:
- 手待ち時間、機械の停止時間、作業の重複など、ムダな時間を明確にします。
- 作業効率の向上:
- 作業の最適な組み合わせや手順を見つけ、サイクルタイムの短縮や生産性向上に貢献します。
- 作業者の負担軽減:
- 作業のバランスを調整し、作業者の負担を軽減します。
- 標準化の推進:
- 最適な作業手順を確立し、標準作業の設定に役立ちます。
IEにおけるM-Mチャートの活用例
- 生産ラインの最適化:
- 組み立てラインや加工ラインにおける作業者と機械の連携を分析し、効率的なライン構成を検討します。
- 多台持ち作業の効率化:
- 一人の作業者が複数の機械を担当する作業において、最適な作業配分を決定します。
- サービス業における業務改善:
- コールセンターや窓口業務など、人とシステムが連携する業務の効率化を図ります。
M-Mチャートは、IEの基本的な考え方に基づき、現場の改善活動を支援する有効なツールです。IEの専門家は、M-Mチャートを適切に活用することで、より効果的な生産システムを構築し、企業の競争力向上に貢献します。
現場でのM-Mチャートの効果的な活用法
現場でM-Mチャートを効果的に活用するためには、以下の点に注意する必要があります。
正確なデータ収集
- 現場観察の徹底:
- 机上ではなく、実際に現場で作業を観察し、正確なデータを収集します。
- 作業者の動き、機械の稼働状況、手待ち時間などを詳細に記録します。
- ビデオ撮影の活用:
- ビデオカメラで作業を撮影し、後で繰り返し観察できるようにします。
- ストップウォッチと併用することで、より正確な時間データを取得できます。
- 作業者への聞き取り:
- 作業者への聞き取りも重要です。
- 作業のコツや課題、改善点などをヒアリングすることで、より深い分析が可能になります。
現場主体の改善活動
- 作業者の参画:
- 改善活動は、現場の作業者を中心に行うことが重要です。
- 作業者自身が改善案を出し、実行することで、より効果的な改善に繋がります。
- チームでの分析:
- 複数のメンバーでチームを組み、M-Mチャートを分析することで、多角的な視点から改善案を検討できます。
- 改善提案制度の活用:
- 作業者からの改善提案を積極的に受け付ける仕組みを設けます。
- 提案内容を評価し、優秀な提案は表彰するなど、モチベーション向上に繋げます。
継続的な改善
- 定期的な見直し:
- M-Mチャートは、一度作成したら終わりではありません。
- 定期的に見直し、改善を続けることで、常に最適な作業状態を維持できます。
- 改善効果の測定:
- 改善策を実施した後、必ず効果測定を行い、改善効果を評価します。
- 効果が低い場合は、改善策の見直しや修正を行います。
- 標準作業の更新:
- 改善された作業手順は、標準作業として更新し、全作業者に周知します。
視覚的な工夫
- 分かりやすいチャート作成:
- M-Mチャートは、誰が見ても分かりやすいように作成します。
- 色分けや記号などを効果的に活用し、視覚的に訴えるチャートを作成します。
- 現場への掲示:
- 作成したM-Mチャートや改善結果は、現場に掲示します。
- 作業者全員が改善状況を把握できるようにすることで、改善意識を高めます。
IE(工業工学)の活用
- IE手法の活用:
- M-Mチャートだけでなく、IEの様々な手法を組み合わせることで、より効果的な改善が可能になります。
- 動作分析、時間研究、レイアウト分析などを活用し、多角的に改善を進めます。
- 専門家の活用:
- 必要に応じて、IEの専門家の協力を仰ぎます。
- 専門的な知識や経験を活用することで、より高度な改善が可能になります。
これらのポイントを踏まえ、現場に合ったM-Mチャートの活用法を検討することで、より大きな改善効果が期待できます。
人・機械稼動線図(マン・マシンチャート)事例
M-Mチャート分析を行なうことによって、作業者の監視作業や手持ちがどういう状況にあるの程度になっているのか、あるいは機械の稼働状況が作業者とどのように連動関係しているのかが理解できわかり、作業者と機械の稼動の問題点が目でわかり、課題を見つけることが可能になる。
【M-Mチャート事例1】
(数字の単位:秒)
- 第1工程でワーク脱着時間 t1=10秒、自動加工t2=60秒、歩行3秒で第2工程へ
- 第2工程でワーク脱着時間 t1=20秒、自動加工t2=90秒、歩行3秒で第3工程へ
- 第3工程でワーク脱着時間 t1=10秒、自動加工t2=30秒、歩行4秒で第1工程へ
- 第2工程の自動加工はタクトタイム120秒の時点で折り返す
120-33=87 で3秒不足、
この3秒は起点より折り返すが10秒の余裕あり
… 自動加工については問題無し - 手作業は50秒後に第1工程に戻るがタクトタイム線まで70秒有るので、これが手待ちとなる。従って更に70秒の手作業を与えることができる。
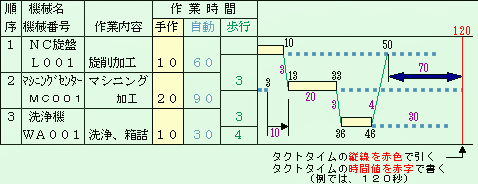
M-Mチャートの例1
【M-Mチャート事例2】
数字の単位:秒)
注)赤字1~は工程順序を示す
- 第1工程、手作業時間 t1=18秒、自動加工時間 t2=62秒、歩行時間 3秒で次工程へ
- 第2工程、手作業時間t1=22秒、自動加工時間t2=57秒、その場で手作業時間t3=32秒、手待ち時間15秒、マシンの余裕11秒有り
- タクトタイム90秒を無視すれば79秒で回れ、手待ちも4秒となる
M-Mチャートの例2
M-Mチャートのその他の活用例
- 製造ラインの作業効率改善
- 機械の稼働率向上
- 作業者の作業負担軽減
- サービス業における顧客対応時間の短縮
M-Mチャートのメリット
- 作業の現状を客観的に把握できる。
- 改善点を明確にできる。
- 改善効果を定量的に評価できる。
- 関係者間の共通認識を深めることができる。
M-Mチャートは、作業効率化のための強力なツールですが、効果的に活用するためには、以下の点に注意する必要があります。
- 正確なデータ収集
- 客観的な分析
- 関係者の協力
- 継続的な改善
M-Mチャートを活用することで、作業効率を向上させ、生産性向上、コスト削減、品質向上に繋がります。
まとめ
M-Mチャート(マン・マシンチャート)は、人と機械の連合作業を分析し、効率化を図るための強力なツールです。以下に重要なポイントをまとめます。
- 正確なデータ収集:
- M-Mチャートの精度は、データ収集の正確性に大きく左右されます。
- 現場観察、ビデオ撮影、作業者への聞き取りなどを通じて正確なデータを収集します。
- 現場主体の改善活動:
- 改善活動は、現場の作業者を中心に行うことが重要です。
- 作業者の参画、チームでの分析、改善提案制度などを活用します。
- 継続的な改善:
- M-Mチャートは、定期的な見直し、改善効果の測定、標準作業の更新など、継続的な改善活動が重要です。
- IE(工業工学)との連携:
- M-Mチャートは、IEの基本的な考え方に基づき、現場の改善活動を支援する有効なツールです。
- IEの様々な手法を組み合わせることで、より効果的な改善が可能になります。
- 効果:
- ムダの可視化。
- 作業効率の向上。
- 作業者の負担軽減。
- 標準化の推進。
M-Mチャートは、これらのポイントを踏まえ、現場に合った活用法を検討することで、より大きな改善効果が期待できます。
*工場のIE手法については下記の文献に色々な活動事例等が更に詳細に記載されています。
参考文献:
・日本のモノづくり トヨタ生産方式の基本としくみ 佃 律志 (著)
・すぐに使えるトヨタ生産方式 導入・実践ノウハウ集 (工場改善シリーズ) 竹内 鉦造 (著)
・すぐに使える現場改善 実践手法&フォーマット集 杉浦 正邦 (著)