かんばん方式(カンバン方式)とは
ジャスト・インータイム生産のために、後工程引取り方式(プル方式ともいう)を実施しますが、このとき使用される管理の道具が「かんばん」です。
「かんばん方式」とは、「かんばん」を使用し、生産情報を伝える伝達方式です。モノのつくリ方、流し方を体系化したトヨタ生産方式の代表的な生産管理の手法です。
従来の押し込み方式では、情報の流れが先行し、前工程でつくられたモノがどんどん後工程に押し込まれていきます。後工程引取リ方式では、かんばんとモノがほぼ同時に動きます。
顧客に売れただけ組立工程が組み立て、組立が使用した分の部品を部品工程が加工するというように、順次前工程へ展開していきます。
この方式だと、モノの需要が発生してから、情報時間差なく流れるため、生産計画の変更にフレキシブルに対応でき、ムダを生じなくてすみます。
「かんばん」の目的とするところは、品質の向上、作業改善、在庫の低減です。
「かんばん」を見て、顕在化した問題点を追いかけることで、目で見る管理が可能になります。
ところで、「かんばん」が多いということは、多くの生産指示が出ていることになり、在庫増につながっていく可能性があります。したがって、「かんばん」を減らす努力をすることで在庫の低減が可能になり、つくりすぎのムダをおさえることができるのです。
トヨタ生産方式は別名、「かんばん方式」ともよばれている。これは、よいクルマをより安く、はやくお客様にお届けするために、あらゆるムダを徹底的になくすことをめざしている方法です。
具体的な方法としてはいつ、どこで、何が、どれだけ使われたかが書いてあるカード⇒「かんばん」というものを使っています。
部品箱1つ1つに「かんばん」がついていて、部品を1つ使うと「かんばん」をはずします。組み立て工場では定期的にこのはずされた「かんばん」を回収して部品工場へ届けます。
部品工場の人は、「かんばん」に書かれた数の部品をつくります。こうすることにより、部品工場はつくり過ぎのムダがなくなり、組み立て工場は使わない部品を置くスペースのムダがなくなります。
かんばん生産方式
カンバン 運用を可能にする条件
「かんばん」は、モノのつくり方、流し方の生産情報を伝える便利な道具です。しかし道具は使い方次第で、有益にも害にもなることに注意が必要です。
そこで、かんばん方式は、生産現場で種々の改善がなされ、ある程度の生産レベル、体質ができたときに可能になる方式と理解されたほうがよいでしょう。
生産の平準化(種類と生産量の平準化)のなされていない企業で導入すると、従業員はてんてこ舞いになることもあるからです。
生産管理の究極の目的
どんな業種であれ、売れるモノを売れる時に売れるだけ作る
「ジャスト・イン・タイム生産」が究極の理想です。
お客様の要望が先です、したがって、原点に戻って、どのような考え方をすればよいか、また、どのような制約条件を取り除けばよいかについて考えてみる。理想を追うことが大切です。
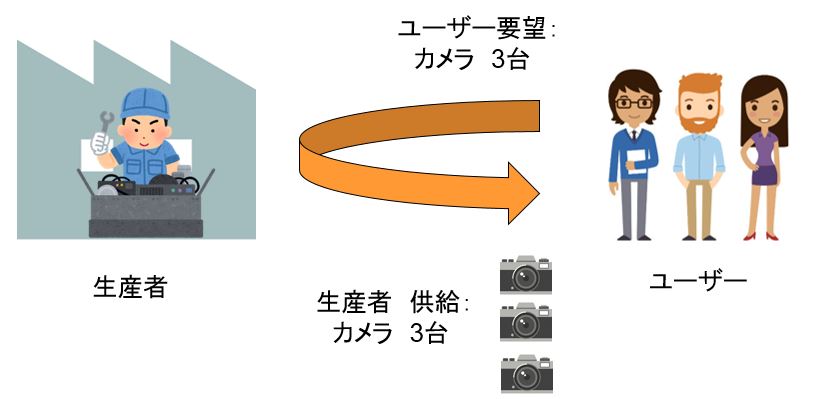
ジャストインタイム生産方式
(2)かんばん方式の歴史
かんばん方式の原点は、アメリカのスーパーマーケットの商品仕入れだといわれている。すなわち売れた商品を売れただけ仕入れるということです。
製造業では、売れた数だけ補充生産するということである。そのために、最終製品の保管場所にある製品一つひとつにかんばんを付けておき、製品が売れたら、売れた分のかんばんを外す。
次に、かんばんが外れた分だけ、製品を補充生産する。この時、製品を作るために使用する部品にもかんばんを付けておき、外れたかんばんの量だけの部品を、前工程に引き取りにいく。
後工程は、かんばんの数だけの部品を即納し、その後、再び引き取られた分を補充生産する。このように、最終製品から部品まですべてが、市場の需要とリンクしてジャスト・イン・タイムに生産されていく。
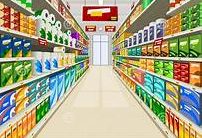
スパーマーケット方式
(3)後工程引き取りを支える平準化
部品を引き取る側にとっては後工程引き取り方式で必要な時にいくつでも引き取れれば、都合のいいことはが前工程にどうだろう?
今日は10個、明日は100個、次はなし、というふうに品目や量が突然大きく変動し、それを即納しなくてはならないとすると、前工程としては、常にすべての品目において、最大引取量に見合うだけの在庫を保有していなくはならず、在庫の山ができ、莫大な資金が埋もれることになる。もし、前工程が中小の外注企業だと、資金がショートして倒産しかねない。
そこで、後工程が前工程から毎日、引き取る品目や量を一定の変動幅以内で平均化、つまり平準化しなければならない。
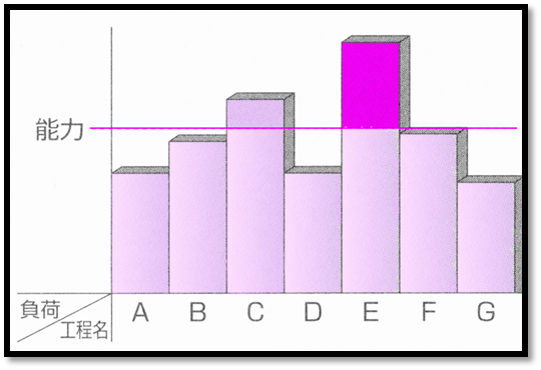
平準化
(4)生産リードタイムの短縮
平準化によって、後工程は、毎日さまざまな品目を一定量ずつ引き取りに来るようになる。ということは、前工程は、毎日、いろいろな品目を短期間でコンスタントに生産できなくてはならない。したがって、前工程の課題として完成部品を引き取られてから次に引き取られるまでに完成部品在庫を補充できるように生産期間(生産リードタイム)を短縮しなくてはならない。
純粋に人や機械が部品を加工している時間は、停滞時間と比べると1 : 100~1:100000ほどの比率で無視できるくらい小さい。したがって、この停滞時間を短縮することが最重要課題である。
停滞する理由は工程間の製造スピードが大きく異なっていることや、まとめ生産、まとめ運搬などの要因がある。
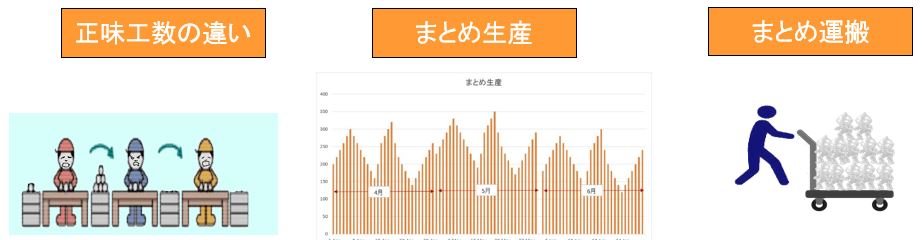
生産リードタイムの短縮
(5)停滞時間の短縮方法① 運搬ロットの最小化
では、なぜ、それほど停滞時間が長いのだろうか。
それは、部品を大きな口ットで生産するからだ。たとえば、一ロット1000個の部品を加工する場合、一個目の部品を加工した後、その部品は、残りの999個の加工が完了するまで 工程に停滞していることになる。そこで、この停滞時間をなくすためには、加工が済んだ部品は即、次の工程へ運搬する必要がある。 100個単位で運搬すれば停滞時間は1/10に、10個単位だと、1/100、1個流しだと、1/1000に短縮。
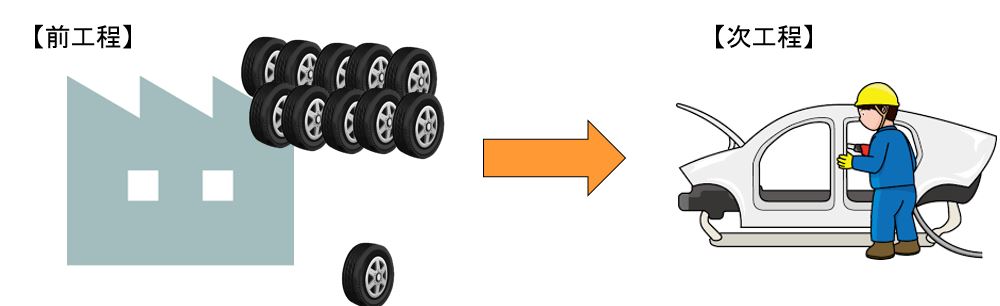
運搬ロットの最小化
(6)停滞時間の短縮方法②工程の同期化
部品の停滞時間を短縮するためには、運搬ロットの最小化のほかに、工程間の同期化を図る必要がある。いくら、即、次工程に運搬できたとしても、次工程の加工速度が、前工程と比べて遅ければ、次第に次工程の前に、仕掛在庫がたまっていく。したがって、部品を待たせずに加工するためには、前後工程の生産速度が等しく、つまり同期化していなくてはならない。
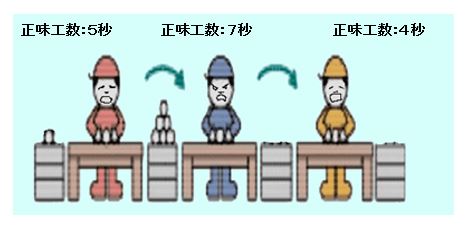
工程の同期化
(7)停滞時間の短縮③方法運搬時間の短縮
待ち時間を短縮するには、小さな単位で運搬することが効果的であると述べたが、運搬ロットを小さくしたその分、運搬回数は増える。もし、運搬距離が長かったり、運搬するための荷積み・荷降ろしに長い時間がかかっては、運搬時間が長くなる、したがって運搬時間を短縮するための課題として、運搬距離の短縮と荷積み・荷降ろしの時間を短縮することが課題となる。
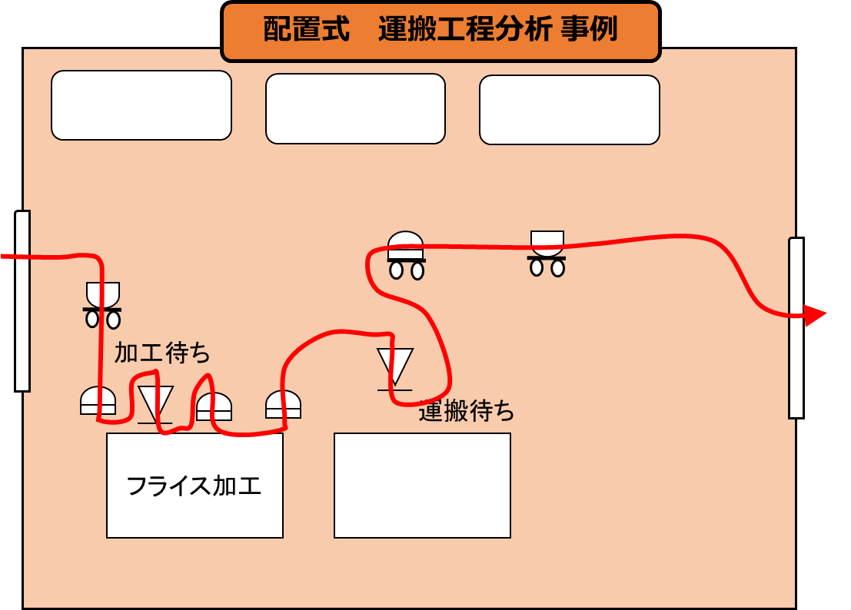
運搬時間の短縮
(8)停滞時間の短縮方法④ 段取り替え時間の短縮
後工程の生産が平準化すると、前工程は多品種を小ロットで生産できなくて
はならない。しかし、生産設備を品種で共用している場合、品種の切り替えの
ための段取り替えが頻発する。もし、段取り替えに長く時間がかかると、実際
に生産をする時間が短くなってしまう。したがって、多品種を毎日生産できるようにするためには、段取り時間を短縮することが課題となる。そのためには、機械を止めて段取り替えを行う時間、いわゆる内段取り時間を短縮する必要がある。そのためには、さまざまな作業改善や冶工具の改善が必要となる。
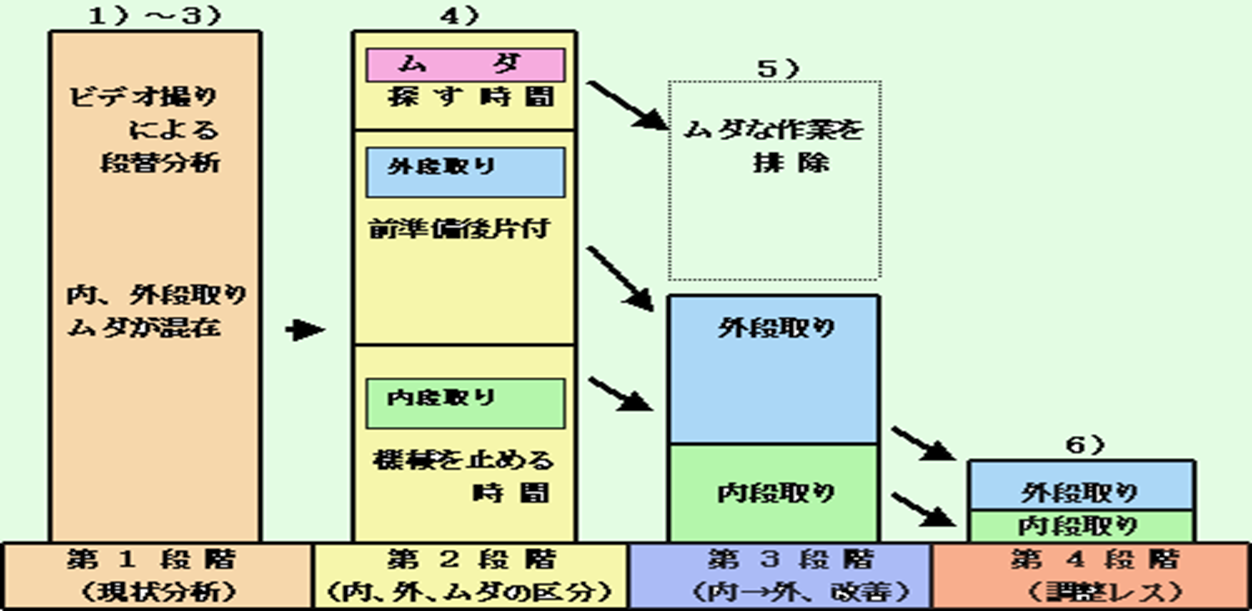
段取り時間の短縮
(9)製造プロセスを整流化
運搬時間を短くし、かつ、工程の同期化を図るために、製造プロセスを“整流化”する必要がある。整流化とは、製造設備を工程の順番に近接して配置し、かつ、工程間の生産速度を同期化することである。これが実現できれば、前工程から後工程まで、部品を一つずつ手渡しにすることができ、運搬時間の問題はなくなる。
生産速度の同期化のためには、まず、製品1個をどんな速度で作らなくてはいけないかを決める。これをタクトタイムという。そして各工程の生産速度をこのタクトタイムに合わせるべく、調整・改善する。
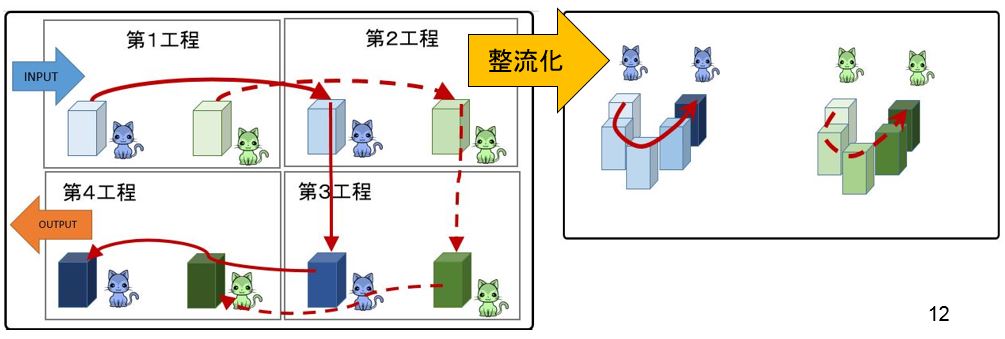
整流化
かんばん方式の体系、目的
下図はカンバン方式の目的、手段を体系化したモノである。
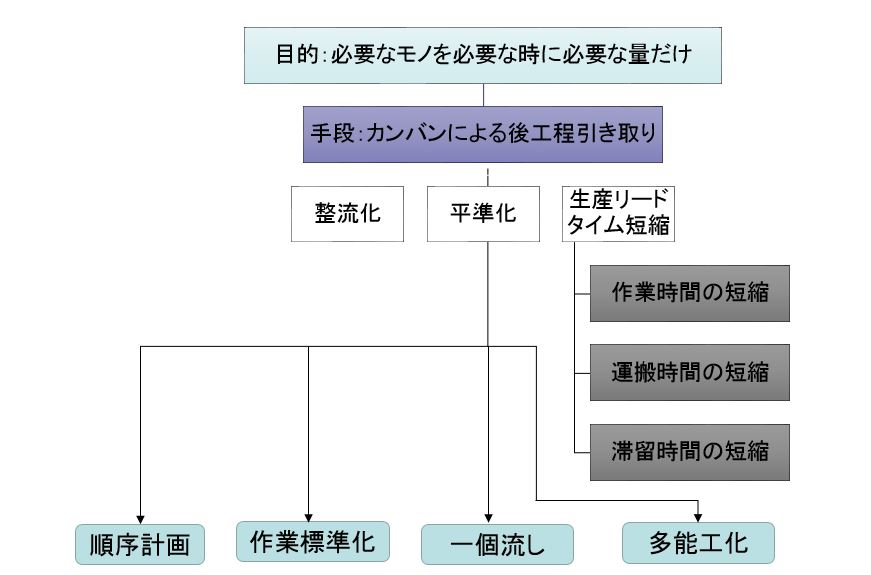
かんばん方式体系化
引き取り生産&押し出し生産
(1)プッシュ生産とは何か?
プッシュ生産(押し出し生産)では、重要の予測情報に基づいて、各工程の週次や月次の生産計画が作成され、上流工程の完成品は下流工程へ自動的に押込まれていく。
プッシュ生産(押し出し生産)の欠点
・後工程にトラブルが発生して生産が遅れても前工程は後工程にモノを押込むので、仕掛在庫が過大になる。
・前工程の生産が遅れると後工程は手待ちになるか、計画外の生産をして不要在庫をため込む。
・各工程の計画を作成するので管理工数が大きくなる。
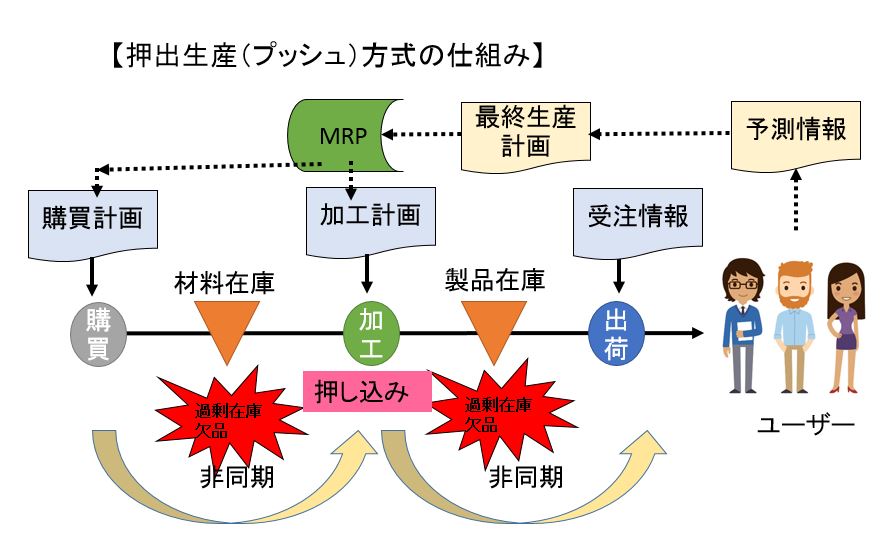
押し出し生産(プッシュ生産)
(2)後工程引き取り、プル生産とは何か?
後工程引き取り、プル生産は、後工程が必要な材料や部品を前工程から引き取り、前工程は引き取られたモノを引き取られた数量のみ補充する生産方式である。 プル生産では、生産計画は最終製品の製造工程のみにしか作成されない。前工程は、後工程から引き取られたモノを引き取られた量だけ生産して在庫を補充する。
後工程引き取り、プル生産の利点
・各工程は後工程から引き取られたモノのみしか生産しないので、不要/過剰在庫がなくなる。
・市場の需要とリンクしているので作りすぎや在庫のムダはない。
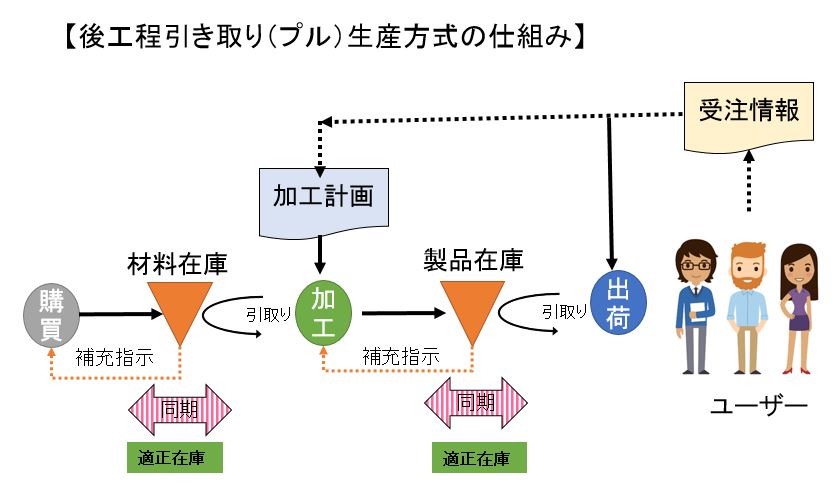
後工程引き取り、プル生産
かんばんの種類
(1)かんばんは指示情報を伝えるツール
①工場でモノを生産するためには、材料を“引き取り” しなくてはならなず、そして材料の引き取りをするためには何をいくつ引き取ってきなさい”という情報が運搬者に必要である。もし、適切な引き取り指示情報がないと加工工程で材料切れを起こし、作業者は手待ち状態になってしまう。
② “必要なモノを必要な時に必要な量だけ作る”ためには、正確な「引き取り指示情報」と「生産指示情報」が必要であり、そのツールとして「かんばん」が考案された。
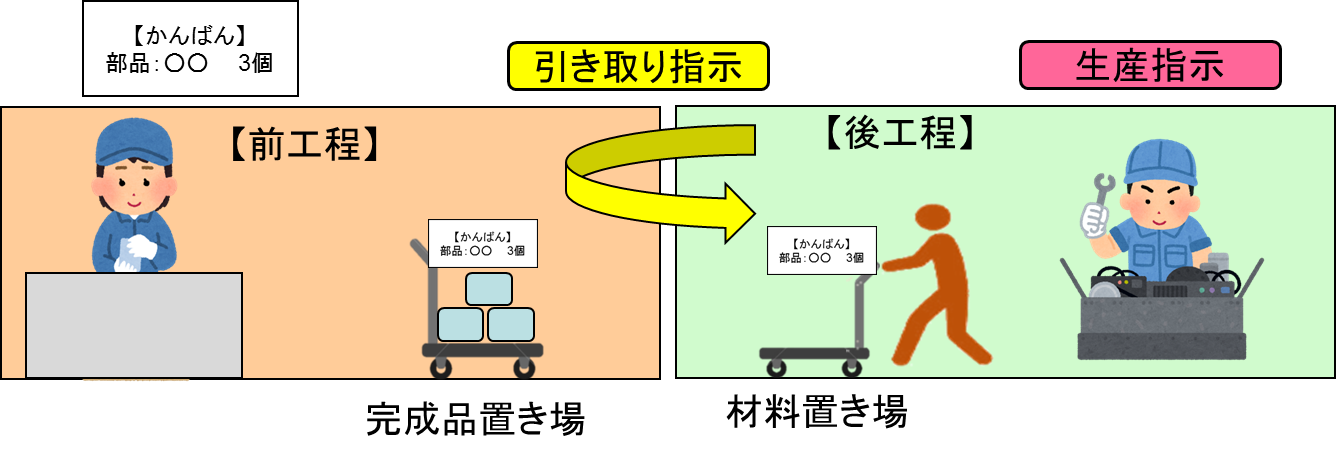
カンバン方式とは
(2)かんばんの種類と機能
かんばんは、機能面から「生産指示かんばん」と「引き取りかんばん」に分類できる。
①「生産指示かんばん」は、運用形態からさらに「生産かんばん」と「信号かんばん」に分類できる。
・「生産かんばん」は、製造工程に対して、一箱単位で生産指示を行うために使われる(機械加工、組み付けラインなどで使用)。
・「信号かんばん」は、製造工程に対して、ロット単位で生産指示を行うために使われる(プレスエ程、成形工程などで使用)。
②「引き取りかんばん」は、運用形態から「引き取りかんばん」と「外注かんばん」に分類できる。
・「引き取りかんばん」は、自社内の前工程から、材料を引き取る指示を行うために使われる。
・[外注かんばん]は外注先から材料を引き取る指示を行うために使われる。
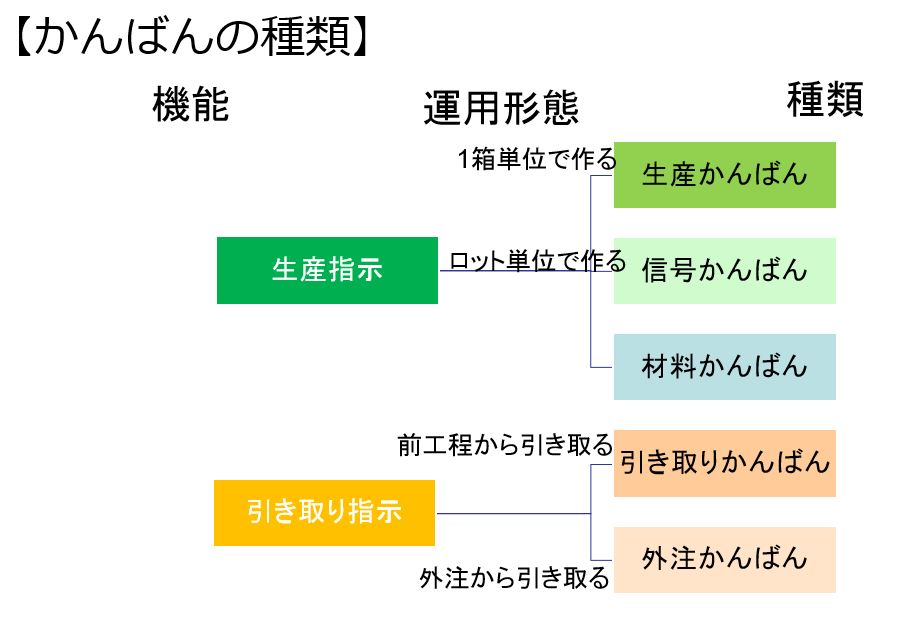
カンバン方式の種類
生産かんばんの使い方
(1)生産かんばんの記載内容
①工程名:
かんばんに記載されている製品を製造する工程名である。工程は単独の設備
であることも、一つの加エセルや組立ラインであることもある。
例では加エセル#1となっている。
②ストア#:
工程の完了品置場を示す。通常は、工程のすぐそばに設置されるが、製品倉
庫に設置される場合もある。後工程へ売る製品を置く場所という意味でストア
(=店)と呼ばれる。
③背番号:
顧客の品番は桁数が長いので、呼びやすくしたり、表示を容易にするために、
桁数の短い番号を自社内で付ける。
④荷姿:
完成品を収容する容器の種類を示す。通い箱、台車など。
⑤収容数:
1つの容器への収容数=1つのかんばんの生産指示数である。
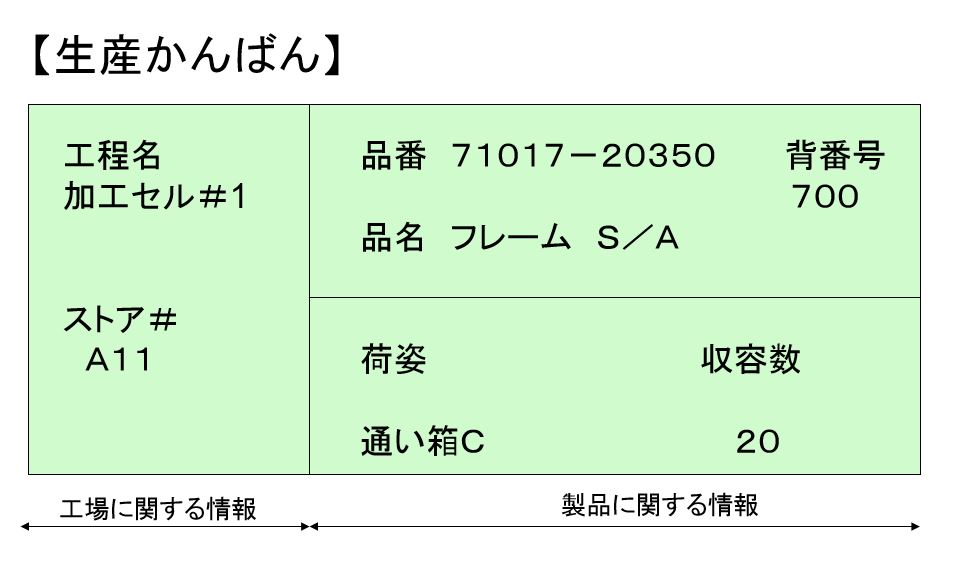
生産かんばんの使い方
(2)生産かんばんの使い方
かんばん生産を行う生産工程は、次ページの図のように生産工程そのもの、完成品ストア、かんばんポスト、スケジュール板から構成されている。
①後工程が前工程の部品を引き取りにくると、部品箱から生産かんばんを外して、かんばんポストに入れる。
②かんばんポストの生産かんばんは定期的に回収され、スケジュール板に作る順番に投入される。最近では、スケジュール板をかんばん一枚分の細かい時間単位(スロット)に区切って、かんばん一枚単位で生産指示を行う企業も増えている(“チョロ引き”と呼ばれている)。
③スケジュール板に投入された順番に従って、かんばん枚数分の生産を順次行う。かんばんは、1個目のワークに付けて生産工程に流す。
④生産が完了した部品は部品箱に入れ、部品箱に生産かんばんを付けて、完成品ストアに置く。
以上の①から④までの手順を繰り返すことによって生産が進行する。スケジュール板を見れば、あとどれだけの仕事が残っているのかがわかる。
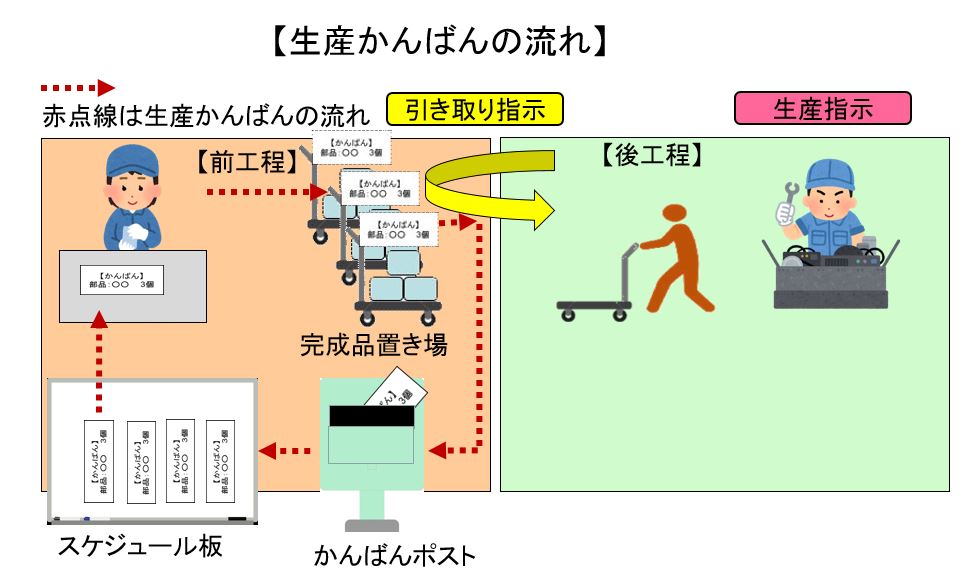
生産かんばんの流れ
信号かんばんの使い方
(1)信号かんばんの記載内容
プレスエ程や成形工程のように、段取り時間にくらべて、加エスピードが速い工程では、一箱ずつではなく、まとめてロット単位で生産する。このような部品をどのタイミングで作るのかという信号を出すのが「信号かんばん」である。信号かんばんに記載されている重要な内容は以下のとおり。
①発注点:後工程で部品在庫が発注点までに減った時、ロット生産工程に対して補充生産を指示する。次の例では200個だが、「2」というように、箱数で示されることもある(発注点は「基準数」と呼ばれることもある)。
②ロット数:ロット生産工程に指示する発注量を示す。次の例では400個だが、「4」というように箱数で示されることもある。
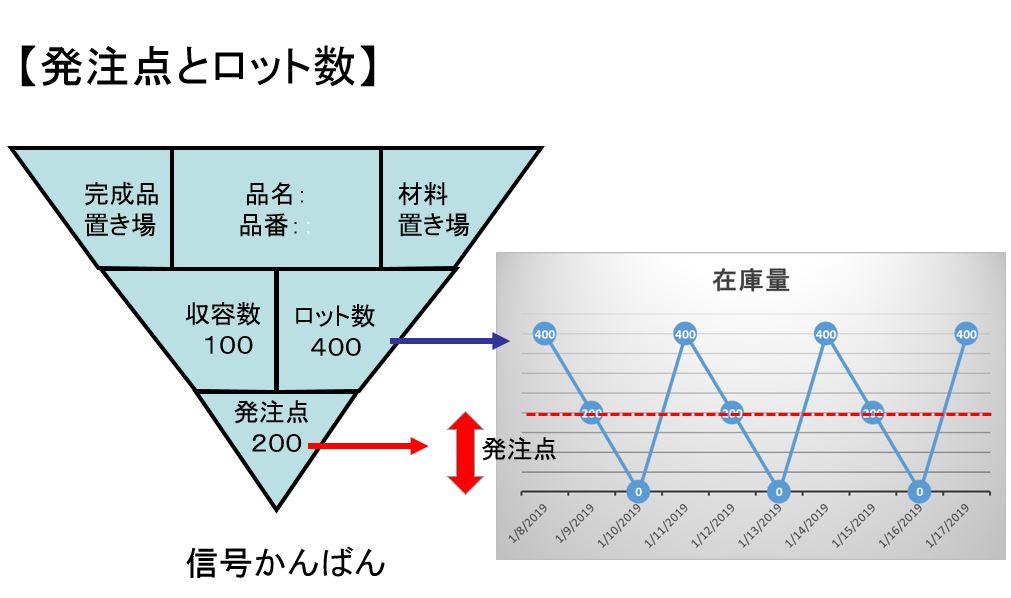
信号カンバン記載内容
(2)信号かんばんの使い方
①後工程からの引き取りによって、部品在庫が減少し、信号かんばんが掛けられた部品箱(=発注点)が引き取られる時、信号かんばんが外されてかんばん掛けに掛けられる。
②かんばん掛けに掛けられた順番に、信号かんばんに記載された部品を、指定のロット数分だけ生産する(図の例では400個=4箱分)。
③ロットサイズ分の生産が完了したら、信号かんばんを発注点の位置に掛けて(下図の例では200個=2箱目)、完成品ストアへ運搬する。
以上、①~③の手順を繰り返すことによって、ロット生産工程の生産が行われる。
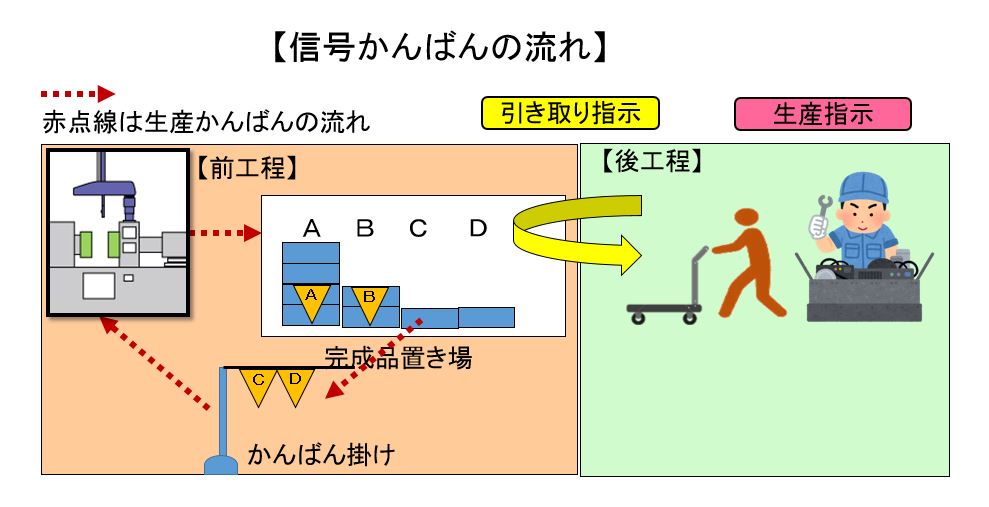
信号かんばんの流れ
材料かんばんの使い方
(1)材料かんばんの活用
プレスなどのロット生産工程においては、信号かんばんが外れると生産指示が掛かるが、生産を始めるまでに材料が揃ってないといけない。材料を別の工程で前もって準備しなくてはならないときに、材料かんばんを使って、信号かんばんが外れる前に、材料工程に生産指示をすることができる。材料かんばんには信号かんばんと同じように、発注点とロット数が記載されている。
完成品ストアから部品が引き取られて材料かんばんが外されると、材料工程で材料を加工し、プレス生産工程の材料置場まで運搬する。
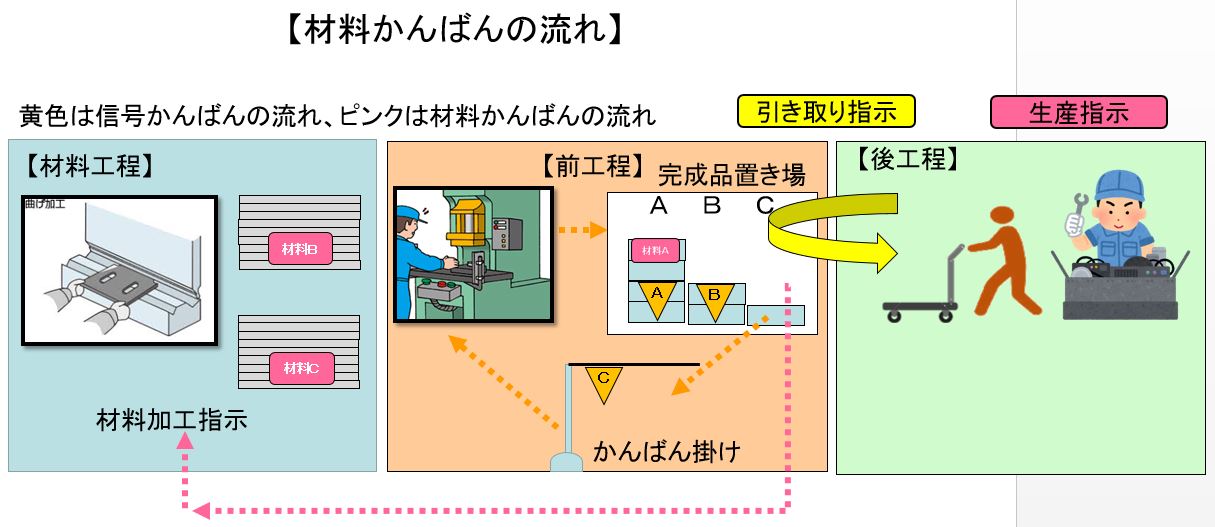
材料かんばんの流れ
引き取りかんばんの使い方
(1)引き取りかんばんの記載内容
社内の工程間で使われる「引き取りかんばん」には、部品がどこからどこへ引き取られるのかの前後工程に関する情報、および引き取られる部品の情報が記載されている。
①前工程、後工程:下図の例では、前工程である鍛造工程から後工程である機械加工工程へ部品が引き取られることを示している。
②ストア、棚番号:前工程の完了品の置場(ストア)の棚番
③背番号:正式品番の代わりに社内で使う簡略した識別番号
④発行番号:かんばんを紛失・破損した場合に再発行したり、かんばん
を識別するための管理番号
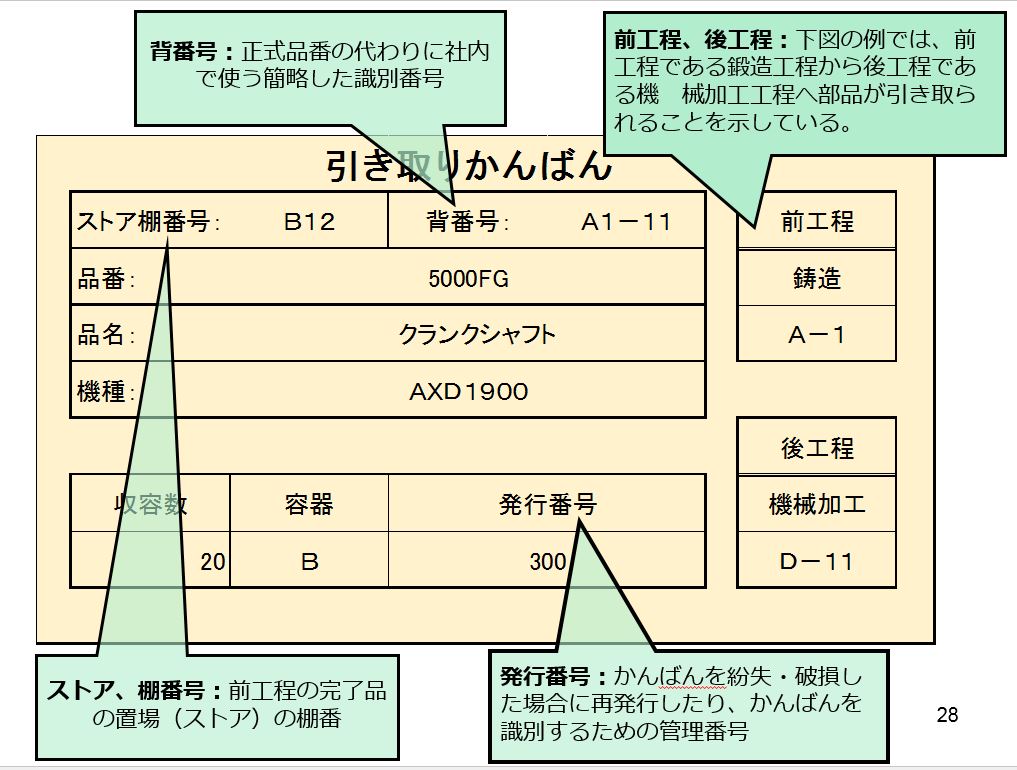
引き取りかんばん記載内容
(2)引き取りかんばんの使い方
引き取りかんばんは、後工程が使った部品を補充するために、前工程から部品を引き取るために使う。
①後工程で部品箱の1個目の部品が使用されると、部品箱から引き取りかんばんが外され、「かんばんポスト」に入れられる。
②かんばんポストの引き取りかんばんを、定期的に運搬担当者が回収し、空箱とともに、前工程に部品を引き取りにいく。
③運搬担当者は、引き取りかんばんの枚数分だけ、完成品ストアの部品箱から生産かんばんを外して、生産かんばんポストに入れる。この際、空箱を前工
程に返却する。
④運搬担当者は、外した生産かんばんの代わりに、持ってきた引き取りかんばんを部品箱に付ける。その後、後工程の部品置場に置く。
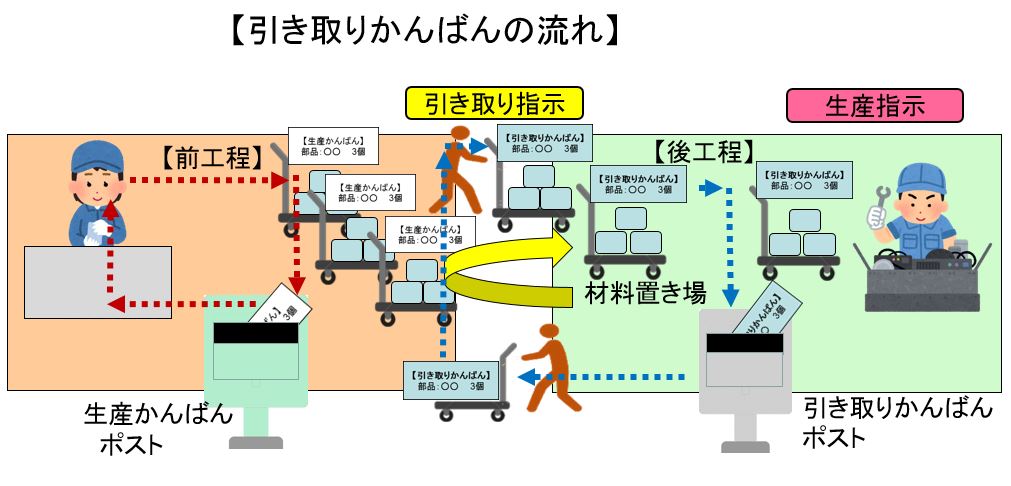
引き取りかんばんの流れ
外注引き取りかんばんの使い方
(1)外注引き取りかんばんの記載内容
「外注引き取りかんばん」は、発注企業がサプライヤーから部品を引き取るために使う。外注かんばんには、サプライヤーに関する情報、部品情報、発注企業の受入先に関する情報が記載されている。
・納入時間:発注企業と外注先とで取り決めた納入時間
・納入サイクル:親企業と外注先とで取り決めた納入方法
次図の納入サイクル欄の1-6-2は、納入頻度が毎日6回、納期は2便後を意味している。次ページの図の例では、外注企業が8時に親企業に納入したときに持ち帰ったかんばんに対して、2便後の15時に納入しなくてはならない。
・管理NO.:発注企業がかんばんを特定・追跡するなどの管理するための識別番号
・納入ストアの棚:サプライヤーが部品を最終的に運搬する場所を示している
・受入場所:サプライヤーがどこで部品を降ろせばよいかを示している
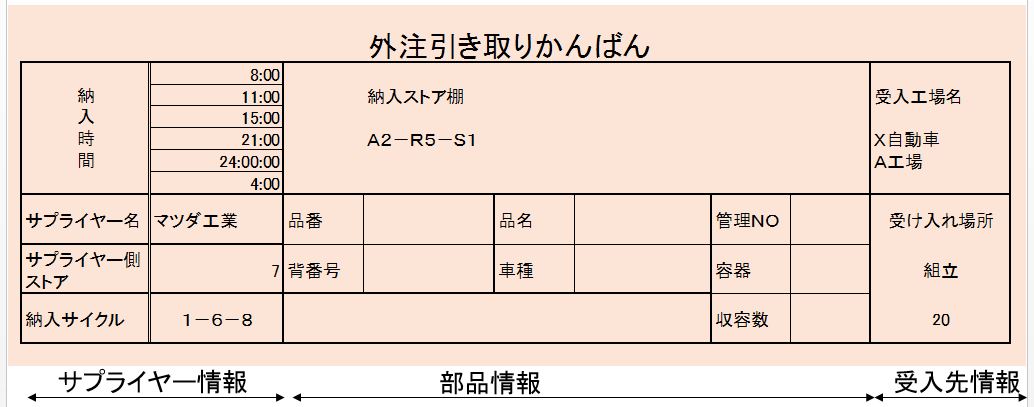
外注引き取りかんばん
(2)外注引き取りかんばんの使い方
発注企業が部品を仕入れるために、次ページの図のように外注かんばんを使う。
・発注企業で外された外注かんばんは、かんばんポストに入れられる。
・外注かんばんはポストから定期的に回収された後、外注先別に仕分けされ、 外注棚に入れられる。この時、納品書と受領書も一緒に入れておく(本来、 納品書類は納入企業が作成すべきものだが、業務のシステム化を図るために発注企業が発行する場合が多い)。
①外注先企業は、部品の納入時、発注棚から外注かんばんを持ち帰る。この時、納品書と受領書もセットで持ち帰る。
②外注先に持ち帰られたかんばんは、部品別・便別に仕分けされ、仕分け棚へ入れられる。
③外注先企業では、納入便に間に合うように、外注かんばんを持って、部品ストアから部品を集荷する。集荷した部品箱には外注かんばんを付ける。
④外注先企業は、納入時刻に間に合うように、部品を運搬する。この時納品書と受領書も一緒に運ぶ。
⑤外注先企業は、受入場で荷物を降ろし、ライン側まで搬入する。受領書に受領印をもらい、再び次のかんばんとともに持ち帰る。
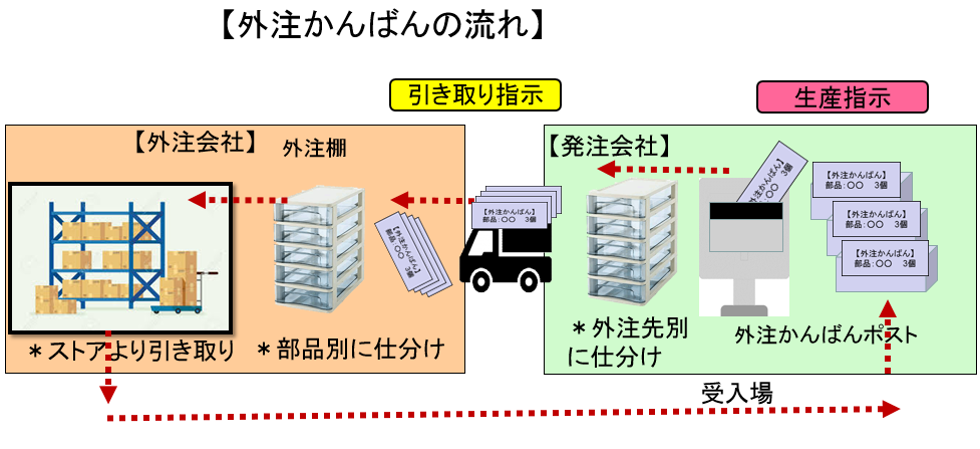
外注かんばんの流れ
生産進捗管理ボード
進捗とは「仕事の進行状況を把握し、日々の仕事の進み具合を調整する活動」であるが工程の生産進捗をかんばんを用いて掲示したモノが生産進捗管理ボードである。
時間毎の目標と実績値が表示されるのでその工程、ラインの生産性の進捗が一目で把握できる。
下記のような生産進捗管理ボードはホワイトボードがあれば即時、可能であり、職場にあったアレンジも容易である。
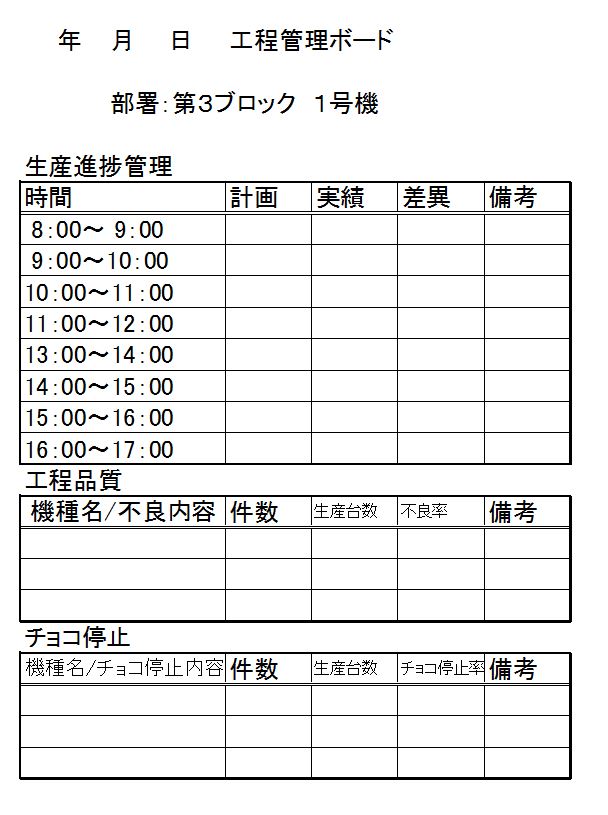
生産進捗管理ボード 縦タイプ
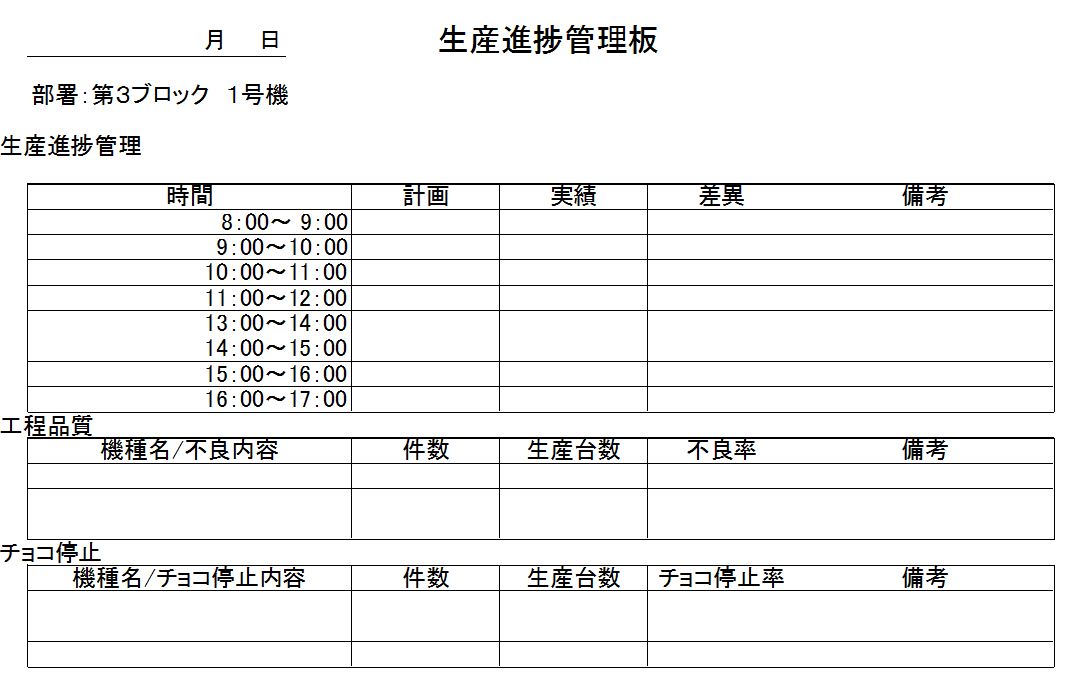
生産進捗管理ボード 横タイプ
上記の生産進捗管理ボードのエクセル版は下記からダウンロード可能です。
かんばん方式の利点、欠点?
このカンバン方式を採用すると情報共有がしやすくなるため、ムダな在庫を持たず、人件費が削減でき生産性を向上することが可能です。
しかし、かんばん方式では余分な在庫を持たないため、欠品や不良品の発生といったトラブルの影響を受けやすい欠点があります。
かんばん方式は需要変動が大きい製品、賞味期限が短い製品には不向きな生産管理方式です。
トヨタのかんばん方式のデメリット
トヨタのかんばん方式は、効率的な生産管理システムとして広く知られていますが、いくつかのデメリットも存在します。主なデメリットとしては、以下の点が挙げられます。
外部環境の変化に弱い
- かんばん方式は、需要の変動やサプライチェーンの混乱など、外部環境の変化に弱いという側面があります。
- 必要な時に必要な分だけ生産するため、予期せぬ事態が発生すると、生産ラインが停止してしまう可能性があります。
- 特に、部品の供給が滞った場合、全体に影響が及び、生産計画の大幅な見直しが必要になることがあります。
情報伝達の遅延
- かんばん方式は、かんばんという物理的なツールを用いて情報を伝達するため、情報伝達に時間がかかる場合があります。
- 特に、広範囲にわたるサプライチェーンでは、情報伝達の遅延が大きな問題となることがあります。
- リアルタイムでの情報共有が難しい場合、迅速な対応が困難になる可能性があります。
システム構築・維持の難しさ
- かんばん方式を効果的に運用するためには、緻密な計画と管理が必要です。
- かんばんの枚数や運用ルールなどを適切に設定し、維持していくためには、多大な労力と時間が必要となります。
- また、関係者全員がシステムを理解し、適切に運用する必要があります。
大量生産への不適合
- かんばん方式は、多品種少量生産には適していますが、大量生産には不向きな場合があります。
- 大量生産では、かんばんの管理が煩雑になり、かえって効率を低下させる可能性があります。
- 大量生産を行う場合は、他の生産管理システムとの併用を検討する必要があります。
依存度の高さ
- かんばん方式は、サプライヤーとの連携を密に行う必要があります。
- そのため、サプライヤーへの依存度が高くなり、サプライヤーの状況によっては生産に影響が出る可能性があります。
- 複数のサプライヤーを確保するなど、リスク分散の対策が必要です。
人的ミス
- かんばん方式は、人の手によって運用される部分が多いため、人的ミスが発生する可能性があります。
- かんばんの付け間違いや紛失などが起こると、生産ラインの混乱を招く可能性があります。
- システム化や自動化を進めることで、人的ミスを減らすことができます。
デジタル技術の進化とのギャップ:
- かんばん方式は、物理的な「かんばん」というツールを用いて情報を伝達するため、情報伝達に時間がかかる場合があります。
- 一方、現代の生産管理システムは、IoT、AI、ビッグデータなどのデジタル技術を活用し、リアルタイムでの情報共有や高度な分析を可能にしています。
- このようなデジタル技術の進化に比べると、かんばん方式は情報伝達の速度や柔軟性の面で遅れをとっていると言えます。
*工場のカンバン方式については下記の文献に色々な活動事例等が更に詳細に記載されています。
参考文献:
日本のモノづくり トヨタ生産方式の基本としくみ 佃 律志 (著)
すぐに使えるトヨタ生産方式 導入・実践ノウハウ集 (工場改善シリーズ) 竹内 鉦造 (著)
スライドシェアー かんばんの基本知識 ~無料ダウンロード
トヨタ生産方式のかんばん生産のポイントを紹介!