セル生産方式 基礎知識
1人、または少数の作業者チームで製品の組み立て工程を完成(または検査)まで行う。ライン生産方式などの従来の生産方式と比較して、作業者一人が受け持つ範囲が広いのが特徴。
グループテクノロジーを利用した生産方式.
部品の類似性に基づいて部品をクループ化すると一般に部品のグループとそれらを加工する機械の間には,それぞれの部品のグループは機械全体の一部から構成された機械グループによって加工が行えるという高い関連性が見いだされる.そのような機械のグループとしてさまざまのセルを構成すると,部品の運搬の手間や時間が省かれ,仕掛量は減少して生産リードタイムが短縮する.
ラインを用いずに一人の作業者や複数の作業者が製品を組み立てる方式をセル生産と呼ぶことがあるがグループテクノロジーが利用されていないために学術用語としては,その名称は適切でない。
引用先:クォリティーマネジメント用語辞典 日本規格協会
関連用語:セル生産方式
セル生産方式とは?
セル生産の定義としては、「一人ないし数人の作業者がひとつの製品を作り上げる、自己完結性の高い生産方式」と言うことができます。
従来のコンベアを主体とした生産方式に比べて、一人の作業者の組立点数が増え、求める技能レベルは高くなる反面、生産量の変動や仕掛り量の削減など、現代の製造メーカーが抱える問題を解決くれる生産方式です。
従来の生産方式(特にコンベア方式)が分業を前提とし、一人当たりの作業を単純化していくことを目指していくことに対して、セル生産では一人当たりの作業工数を増やし、少人数で最後まで製品を作り上げていくことを目指しています。
セル生産方式の命名は、元ソニー(株)生産革新センター所長 金辰吉氏、正式には「ワークセル」生産方式、作業台が「コ」の字型に囲む様子を細胞(英語:cell)と似ているためにセル生産方式と名付けられた、別名『「1人屋台生産方式」とも呼ばれる。
英語:cellular manufacturing system
セル生産方式の歴史
“セル生産の起源は、フォードに代表される大ロットコンベア生産が普及する以前の手作り生産にあります。
昔は一人の職人が最初から最後まで作り込んでいくモノづくりが主流でしたがその職人の手作り生産に各種の科学的思想・手法を組み合わせて各種の問題点を解決し、出来上がっだのがセル生産と言うことができるのです。
近代のセル生産方式の基本はGT(Group Technology)の概念に基づいて1940年代後半にソビエト連邦のMitrofanofとSokolovskiiによって提案されたのがその始まりとされており、第2次世界大戦後、東ヨーロッパ、西ヨーロッパ、インド、香港、日本そしてアメリカなどに伝わり、研究されるようになりました。
つまり、セル生産とは決して新しいものではなく、有史以前から人が行ってきた生産活動の原点そのものであり、モノづくりの原点なのです。
厳しい納期設定、低コストに対応するためには、大きなリードタイムの短縮と工数低減を行わなければなりませんが、通常のコンベア生産ではバランスロスや切り替えロスが発生し、効率的に生産することができません。そのため小ロット品はメインのコンベアラインから切り離し、小ロット専用のラインを組んだことが現在のセルの始まりです。
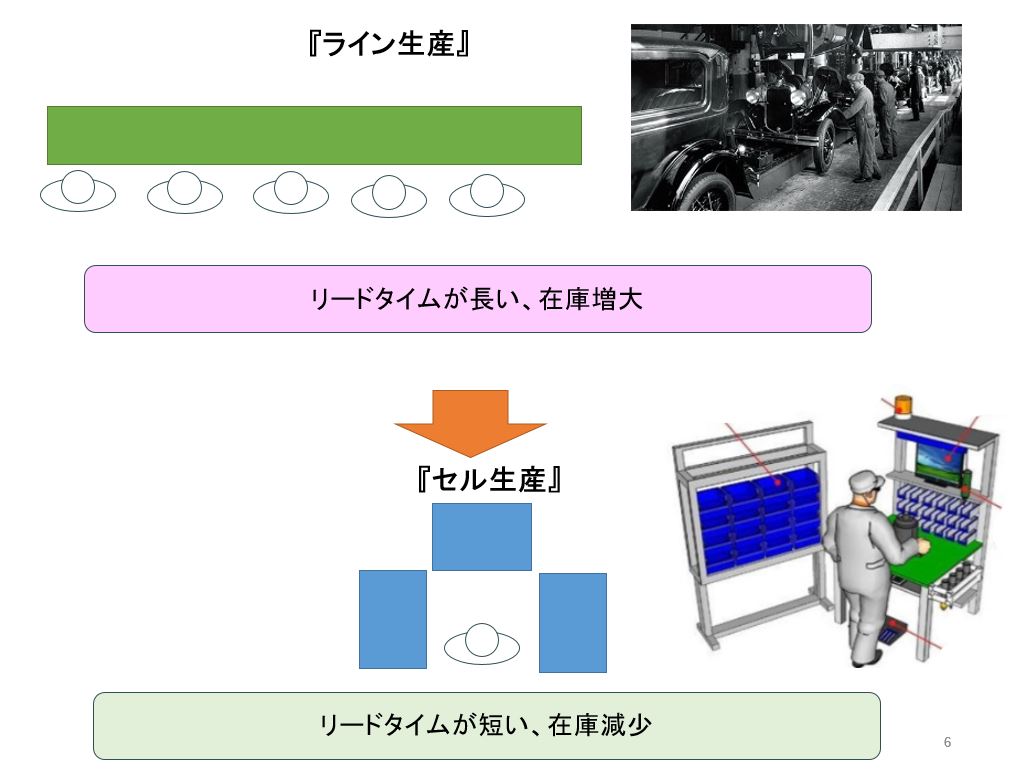
ライン生産とセル生産の違い
セル生産方式の考え方
セル生産の定義である「自己完結性の高いモノづくり」は技術というより論理思考です。
ですから、セル生産の考え方は組立作業以外にも十分に通用します。ちなみに、機械加工部門では昔からあるU字ラインもセルということができますし、数台の機械を連結したミニラインもセルということができます。
また、間接部門では組織階層構造のフラット化や必要以上の細かな分業からの脱却もセル化の一例です。
仕事の効率を上げるためにシステム、業務を分業する考え方から自己完結できトータル的にシステム、業務ができる考え方がセル生産方式の思想です。
ライン生産方式の問題点
セル生産とよく比較されるのが、大ロット連続生産を前提としたコンベアを用いたライン生産方式です。ライン生産はフォードシステムをその根源としますが、その考え方は現在でも多くの企業に採用されており、特に組立系の職場に数多く見受けられます。
ライン生産は基本的に大ロット・大量生産を前提としており、数少ない品種を大量かつ高速に作るのに最も適したシステムであるといえるでしょう。過去日本においてもコンベア生産は非常に有効なシステムとして種々の企業に採用され、日本の高度成長に多大な貢献をしてきています。
近年、作業効率を上げコンベアに携わる人員を削減するために積極的に自動化が進められ、無人ラインに近いものも現れています。しかしながら現在においては、コンベア生産における前提条件(大ロット生産、連続生産など)が崩れ去っており、逆にコンベア生産を行うことにより多大なロスを発生させている。
結局そのような企業は在庫を管理しきれなくなり、膨大な不良在庫を抱えつつ、「ITシステムを導入すれば何とかなる」として巨大なIT投資に走り、失敗しているのが現実の姿である。
セル生産方式のメリット
①同期化が進み製造リードタイムが短くなる。
②在庫・仕掛りが減少し、キャッシュフローが向上する。
③生産性が向上する。
④品質向上、不良の低減。
⑤多品種少量生産に柔軟に対応できる。
⑥段取替え時間の短縮。
⑦過大な設備投資を必要とせずライン変更が可能。
⑧「私達のライン」意識が作業者のヤル気を高める。
⑨現場の小改善が促進される。
⑩面積生産性の向上によるスペース確保。
在庫が減る
セル生産を実施した場合の成果のうち、最も大きな成果を示すものの一つに在庫低減があります。在庫は大きく製品在庫と仕掛り在庫に分けられますが、セル生産では両方とも在庫の半分を減らすことが可能です。
①製品在庫の削減
セル生産の場合、少人数でライン構築が可能になるので複数のラインを同時に動かすことが可能になります。そのため、同時に数種類の製品を完成させることができるようになるのです。また、セル生産を行っていくと製造リードタイムが短くなるので、顧客要望に応じた生産が可能になり、必要以上に在庫を持ち貯めしなくても対応できるようになってきます。つまり、常時在庫補充が可能になるため、在庫を持つ必要性自体がなくなってくるのです。
②仕掛り在庫の削減
セル生産の場合、仕事の自己完結性が上がるため、作業工程ごとに仕掛りを持つ必要性がなくなります、一般的に仕掛り在庫は各工程間、作業者間の処理能力の差により発生するものですがセル生産の場合、各工程が完全に連結しているため工程間の仕掛りはほとんど発生しません。
リードタイム 短縮
セル生産を行った場合に、まず大きく短縮できるのは製造リードタイムです。
セル生産を行っていくと各作業工程が連結していくため、必然的にリードタイムは短くなってきます。
一般に製造リードタイムの実態調査を行うと、実際にかかったリードタイムの80~90%は停滞時間で、これは製造口ットが大きいほどその影響は大きくなってきます。従来の大型・高速コンベアラインでは停滞時間が長くなるのはこのためです。セル生産の場合は、小ロットであることも含めて流れの中でモノを造る形になるため、
停滞時間は大きく減少していきます。
営業部門や業務部門がセル生産の考え方によって、改善を進めていくと事務処理時間が短くなるので、情報処理リードタイムは短くなってきます。また調達部門が改善活動を行っていくと調達リードタイムが短縮してきます。
実はリードタイム短縮活動の中で最も難しいのは、この調達リードタイムの短縮で、ここを短くしていくためにはサプライヤーの協力が不可欠になります。
そして営業部門、出荷部門の改善によって物流リードタイムが短くなってきます。このように製造リードタイムの短縮だけならば製造部門だけでできますが、全社的なトータルリードタイムの短縮を行っていく場合には、全社的な協力が不可欠になります。
作業不良が低減!
セル生産を行うことによって作業者のモチベーションが向上してくると、作業に
対する注意力も向上してくるので、人に起因する不良が減少してくるのです。
ただし、当然のことながら、不良の低減は作業者のモチベーションの向上だけに頼
らず、ポカヨケの設置や標準の設定、工法の変更など仕組み面からのアプローチも忘れてはなりません。
またセル方式に転換した直後に一時的に不良率が上がる場合がりますが、これは作業者の技能が不十分な場合に発生しやすく、習熟度が上がるにつれて減少してくる傾向があります。
生産性の向上!
セル生産を行うと生産性は大きく向上しますが、それはムダ作業削減(運搬・物流のムダ、手待ちのムダなど)や生産の変動に対する適応力、作業者のモラル向上などを起因としています。一般的にセル生産システムを導入した場合、30~50%の生産性の向上が見込めますが、場合によっては100%以上の生産性向上が図れる場合もあります。
また上記以外にも、不良の低減、作業編成効率の向上、停滞時間減少による手待ち時間の減少、段取替え時間の削減などにより生産性が向上する要因となります。
コンベア生産においては、その生産性はラインスピードに影響され、作業者のモチベーションにはさほど影響を受けませんが、セル生産は人間的要素が色濃く出るために、生産性の向上に関しては作業者のモチベーションと密接な関係があります。つまり、作業者のモチベーションが高い場合においては、コンベア生産に比較して、かなり高い生産性を発揮する反面、モチベーションが低いとコンベア生産よりも生産性が下がってしまう特徴があります。
セル生産を導入したほとんどの企業は実際に生産性が向上します。その理由は、セル生産においては各人の能力と同等の結果が出ますが、コンベア生産においてはライン中の最も能力の低い人に全員が合わせざるを得ないためなのです。
設備投資コストがかからない!
セル生産のメリットのひとつとして設備投資がほとんどかからないという点です。
大量生産を前提としていた時代の完全自動化、大量処理、高速化を目指した大型設備・大型投資とは一線を画するものなのです。
セル生産の場合、自動機をラインの中に入れるにしてもその前提はLCA化(ローコストオートメーション)であり、作業者の智恵と工夫をその起源として、徹底
的に安いコストで作成した設備を使用することになります。
また作業の自己完結性が高いため、モノを運搬するための高額なコンベアラインやコンピュータ制御された自動台車などは必要としませんし、在庫が極小化するため高価な立体型自動倉庫システムなどは不要なのです。
セル生産において必要なのは作業テーブルと治工具、部品を入れる棚程度であり、最も簡素化された生産システムということができます。
このような設備投資金額の低減は、商品のライフサイクルが短くなった現代においては極めて重要な施策です。
生産量の変動に対応できる!!
セル生産では『種類&生産量の変動』に対応することが可能です。
①種類の変動:従来のコンベア生産では品種の切り替え時に相当な工数を必要としていました。特にフリーフローラインなどはパレットの入れ替えを行ったり、ライン幅の変更、検査機の調整など数時間単位の段取替えが必要となっていました。
しかし、セル生産では複数のラインができるので段取替え自体が少なくなってきます
し、仮に段取替えをしても作業テーブルと治具などしかありませんから時間はほとんどかかりません。
②生産量の変動:従来のコンベアラインでは生産量が多かろうが少なかろうが、ラインを稼働させるために必要な人員は決まっていますので、一人でも欠けたらラインを動かすことはできません。そのため少量の生産でもメインラインを動かさざるを得ず、大きな囗スを発生させていたわけです。
しかし、セル生産では基本的に各セルが独立していますので、生産量に応じた数だけのセルを稼働させ、必要の無いセルは停止させておけば良いのです。また巡回方式のセルを採用している場合には、セルの中で作業する人員数を増減させることにより、時間当たりの生産数を増減させることができます。
セル生産方式のデメリット
①作業者個人の技量差が大きく出る
セル生産の場合、作業者の熟練度、多能化度、モチベーションの程度によってその作業速度は大きく変化します。現実的に作業のスピードが毎回変化してしまうと生産統制が取れなくなるので、セル生産においてはそのスピード制御(セル制御)をかけていく必要があります。
②責任意識が時としてストレスとなる
セル生産の場合、作業の受け持ち範囲が広くなるため、各作業者に対する責任は大きくなってきます。そして人によってはその責任意識がプレッシャーとなり、
ストレスとなる場合があります。そのため、不良などが発生した場合、その責任を個人に押し付けるのではなく、仕組みの悪さ(ポカヨケなどの未設置)としてとらえることが大切です。
③より幅広い多能工が求められる
セル生産は自己完結性の高い生産方式であるため、今まで以上に作業者の多能工化を要求することになります。必然的に作業習熟にかなりの時間を要することになるので、セル化にあたっては、作業訓練、教育に十分な時間をかける必要があります。また、効率的な教育を行うためには作業標準書、基準書などが不可欠ですし、短時間で効果を上げるための各種ツールが必要となります。
多能工化の教育
ひとつの工程の作業しかできない単能工ばかりではセル生産方式は不可能です。
そのため多能工化の教育はセル生産を行っていく上で必須条件です。
よってセルに配員してから仕事を憶えさせるようなOJT中心の教育も場合によっては必要です。
又、新人に作業を教える時は必ず分かり易い手順書を見ながら行います。
最近では教育専用のセルを作るところも増えています。本来のセルと同等のセル
で新人の教育を中心に行うセルのことです。
〈単能工〉単一の作業もしくは簡単な作業しかできないレベルの作業者。
〈多能工〉多工程の作業および複数の商品の作業を行えるレベルの作業者
〈全能工〉複数の商品の初工程から最終工程までを 一人でできる作業者
セル生産方式の種類
セル生産でのモノの作り方は大きく分けて、作り方と流し方の2通りが考えられ、作り方としては3種類、流し方としては2種類があり、合わせると6通りのパターンが存在する。
セル生産方式の特徴
①少人数(一人または数人)であること
セル生産の場合、ひとつのセルの中で作業する人員は1名または数人であり、比較的大きな量産を意図した巡回型のセルでも、通常は4~5名程度です。本来、セルは一人で最後まで組み立てる一人方式が望ましいのですが部品点数が多くなってくると一人では対応できなくなります。
その場合、人員数を増やしたセルを構築するわけですが、7人以上のセルになると弊害が多発してくるので、その場合は一つのセルで対応するよりも、いくつかのセルに分散させるモジュール化を推進していきます。
②自己完結性が高いこと
セルの最大の特徴の一つがこの自己完結性の向上です。セル生産では、相当数の部品を組み付けることになるので、「自分で作った商品」という意識が芽生え、不良低減や作業者のモチベーションの向上、創意工夫の実施などに結びついてきます。
③最小単位での生産であること
1個ずつモノを作り上げる1個作り生産であり、従来のような大きなロットの生産ではありません。
セル生産 作り方 種類
①完全な1個作り
1個ずつ完成させていく方式であり、従来より1個作りと呼ばれている方法、セル生産においても最も基本的な作り方。
②小ロットー個作り
製造を小ロット(一般には10個以内)単位で行うもので、基本的には1個作りです。完全な1個作りでは完成のつど、後工程に送っていきますが、小ロットー個作りでは、1個ずつ作りながら完成品が複数たまってから、まとめて後工程に送る方式です、特に小型の製品、部品を作る時に採用される場合が多い。③小ロットまとめ生産
製品ロットを極めて小さくするのは小ロットー個作りと同じですが、工程ごとのまとめ生産を行っていく方法です。複数個を各工程ごとに作る方式であり、従来のまとめ生産に近い。
セル生産 流し方 種類
①混流生産
毎回違う製品を流す方式であり、自動車に代表される流し方です。
必然的に連続生産よりもその難易度は高くなります。セル生産の方式としても採用されていますが、作業者の高いスキル、生産管理システムの高度化、調達方式の高度化などクリヤすべき課題も多い。
②連続生産
ある程度、流す製品の順番を定めるやり方です、基本的に小ロットが前提になります。小ロットベースで数量を取りまとめて流すため、特に問題なく採用できます。
セル生産 一人方式
一人方式の特徴は文字通り一人で作業を完結することにあります。
仕掛りの減少、リードタイムの短縮などの利点があります、欠点としては、作業者の習熟に時間がかかる、量産に対応しづらい、部品供給が多頻度、小ロットになりやすい等が挙げられます。
一人方式は1名の作業者で製品を完成させる極めて自己完結性の高い生産方式であり、一人で作業を行うので、常にバランス効率は100%です。しかしその反面、作業者自身が作業スピードを決定することになるために何らかの規制をかけることも必要です。
一人方式を採用する場合は30~50個以内の部品で作られる製品に適しています。
この方式で量を作ろうとすればセルの数ばかりが異常に増え、それにつれて場内物流工数や投資額も増大していくので注意が必要です。
この一人方式は以下の場合によく採用されます。
・技術的難易度の高いもの、精密さを要求される製品
・作業者のスキルが高い場合
・生産量の少ないもの、切り換えの多い製品の場合
セル生産 巡回方式
セル内に複数の作業者がおり、作業者が各自組み立てを行いながらセルを巡回し、一巡したところで製品を完成させます。
量に対する対応力が最も高く、人員数を調整することにより生産量を調整します。作り方は1個作りが基本であり分業は行いません。
この巡回方式のレイアウト自体は分割方式と変わりませんが、作業の割り当て方が違います。これは一人の作業者が製品を完成させる方式です。
また、セルを大型化し巡回人員を増やすことにより、量産を指向したセルを作ることも可能です。ただし、一般的にセルの巡回人員は5~6名以内で抑えないと、作業のスピード差による停滞が発生し、生産性を低下させることになるので注意が必要です。
巡回方式を採用した場合には、必ず「追い抜き可能場所」を作る必要があります。それは、作業者の追い抜きを可能にしないと、スピードの遅い人に全体が影響され、生産性が上がらなくなってしまうからです。
この巡回方式は、以下の場合によく採用されます。
・量産を意図したセルを作る場合
・作業者のスキルが同等か、よく習熟している場合
・組立部品数がそれほど多くない場合
・生産量の変動が大きく発生する場合
セル生産 分割方式
この方式はセル内に複数の作業者がおり、作業を分担して進めていくことです。
一般的にはU字型のセルに用います、作業を分担しているので、多能工化が進んでいない場合に適しています。
この方式は、従来のコンベア生産をセルにする場合に最もやりやすい方式で、コンベアを撤去した後に適切な大きさのセルを作り、作業を数名で分担して製品を完成させる形になります。
巡回型に相似していますが作業の分担方式が違います。
分割方式では一人で製品を完成させるのではなく作業工程別に担当を決め、自分の工程が終了したら次の作業者に渡す形をとります。当然、各作業者ごとに分担はあるものの、コンベア生産時よりも多くの工程を受け持つことになります。また作業が人別に分断されているためにバランスロスが発生する場合があるので、作業者別の工程タクトの設定が重要です。
また、仕掛りも作業者間で発生するので、数個以内に量を定めて規制をかける必要があり、作業者が習熟してきた場合には、各作業者間に「助け合いゾーン」を設置する場合もあります。
この分割方式は、以下の場合によく利用されます。
・コンベア生産からセル生産に移行した当初
・作業者の多能工化が十分に進んでいない場合
・組立部品数が極めて多い場合
・かなり精密な作業を要する場合
セル生産 インライン方式
インラインセルにおいては3通りのパターンがあります。
一つめのパターンは、一人方式のセルの完成品搬出経路をコンベアを使用した場合で、本質的には一人方式のセルです。
二つめのパターンとしては、分割セルの直線ライン版です。この場合においてもコンベアを搬送手段として使用しています。上流のセルが途中まで組み立てたものを下流工程までコンベアで送り、下流工程では流れて来たものをコンベアからピックアップし、組立作業を継続する。作業が終了すれば同様に下流工程に送っていく。この方式は、コンベア生産とセル生産との中間型と言えるものであり、コンベア生産から最も移行しやすい形態といえるでしょう。しかし、工程間の同期をとるのが難しく、バランス囗スも発生しやすいです。
三つめのパターンとしては、モジュールーユニット製造ライン、または部品組み立て用のセルラインとして使用するパターンです。この場合、各セルでは一つの製品用の各部品を組み立て、コンベアを使用して後方に送り、本組立セルに供給していく。つまり、インラインセルの後方には本組立セルがあり、本組立セルに供給する部品をインラインセルで作るという複合型セルラインの一部分としての用いる場合です。
セル生産方式 導入
セル生産方式はソニー、キャノン、NEC、Panasonic等で導入され、成功していますが各社のセル生産方式は各現場に適したものであり、独自のセル生産方式であり他の会社にそのまま、持ち込んでも使用できません。
但し、各社に共通するセル生産方式 導入手順はあり、ここではそれを説明します。
セル生産 導入 9Step
①対象商品の選定(PQ分析)
②セル工程設計(アウトラインの決定)
③現状の実態把握(現場のムダ確認と排除)
④セルラインを試作
⑤負荷バランス調整
⑥工場内物流のレイアウト
⑦作業者の教育・訓練
⑧セル生産を実施
⑨評価、フィードバック(改善)
*綿密な計画を立てたとしても机上の理論では限界があり、最初から十分に機能するセルを作ること困難であるので評価し、フィードバック(改善、是正)することが大切である。
対象商品の選定
PQ分析において、生産量に応じて3ランク程度に分けることによりセル生産の対象を決定します。ランクは累計シェアによって分類し、Aランクは累計シェア70%まで、Bランクは70~90%、Cランクは90~100%までということになります。
基本的にどのランクにおいてもセル生産を実行することは可能ですが、初めてセル生産を行う場合はBランクを対象として行った方が最適です。
*PQ分析とは生産品種(P)と生産量(Q)をグラフの横軸と縦軸にとり、品種と量の関係を示したものです。生産量の多いものから順に並べていき(棒グラフ部分)、その累計値を折れ線グラフとしてプロットしていきます。
セル工程設計
①セルの方式の設計選択:
分割方式、巡回方式、一人方式若しくは他の方式
②セルでのモノの流し方の選択:
混流生産or 連続生産
③セルでのモノの作り方 選択:
1個流し、小ロット流し
④全体的なレイアウトイメージ:
⑤日程スケジュール:
期限、担当者
*セル生産導入の工程設計ためにはモノの流れ、モノの保管状況、工程間の流れ、つながり、セル間の関係を明確にするために人の動きを記録した動線図を作成し、作業のムダや動作のムダを発見し、それを是正した内容を工程設計に織り込みます。
現状の実態把握(現場のムダ確認と排除)
セル生産導入に当たって現状ラインの問題点を把握することは極めて重要です。製造現場の問題点は生産システムに起因するものもありますが、その多くは職場の体質や管理システムの悪さ、作業者および管理者のモラルに起因するからです。このような体質のままではいくら良い生産システムを導入したとしても有効に機能することはありません。
新しい生産システムを導入しても過去の問題点の原因を取り除かなければ
そのまま、問題は残ります。
セル生産においても同様で、いくら有効なセルを導入してもその後の維持安定化、セルの進化が見られなければセル生産の本当のメリットを享受することはできないのです。そのためセル生産導入に当たっては事前に現状の問題点を調査分析し、その是正を図らなければなりません。
セル ラインを試作
このステップでは現場に実際にセルを作ることを前提として詳細なセルデザインを行います。また実際に作ったセルをテスト的に運用してみることも行います。
選定する内容としては以下のものがあります。
①セルの大きさとセル内の人員数
②工程連結の程度(セル間の同期化の程度)
③原材料の供給方法と製品の搬出方法
④セル内の工具、治具の置き場所や置き方
⑤電気やエアの配管、その他ユーティリティの準備
注意点:従来のコンベアラインを工程別に切り取り、工程別の安易なセル
を作らないことです。このようなセルはコンベアをU字型に曲げただけで、全くセルとしての機能を発揮しません。セルを作るときは一つのセルに全ての工程を含むような形で作るのが重要で、そのような形であるからこそ多品種対応力や生産変動対応力、仕掛り削減、リードタイム短縮が行えるのです。
バランスを調整
バランス調整の目的は、セル間の負荷、作業者間の負荷のバランスを調整および是正することにあります。
単体のセルにおいては作業者間の負荷バランス(分割型のセルの場合)、複合型のセルの場合はセル間の負荷バランスを調整することになってきます。
セル生産の目的は、最終的には工場全体が同期し、各種のムダが省かれた状態を目指すのですから、バランス調整もしっかりと実施していかなければなりません。
セル生産はSCMの解決策であり、顧客の要望に対応するための生産システムです。ですからセルにおける生産スピードは設備や作業の都合で決まるサイクルタイムではなく、顧客の要望から発生する受注量を前提にしたタクトタイムを前提としなければなりません。つまり、セルにおける生産スピードは常に可変であり、生産量に合わせて設定すべきものであるということです。
工場内物流のレイアウト
工場内物流のレイアウトとは、セルに対する資材の供給方式、供給タイミングおよび完成品の搬出を含めた場内物流レイアウトのことです。
その範囲は資材の入庫から保管、ピッキング、出庫、各セルヘの供給から製品の搬出までを含み、この物流レイアウトが確立しないとセルは有効に機能することはできません。
セルを完成させるためにこの物流レイアウトは非常に重要であり、セルが必要とするものを、必要とする時に、必要なだけ供給できる物流レイアウトをデザインします。
セル生産の場合、作業スペースが狭いのでラインサイドに大量の資材を置くことができません。そのため多頻度少量供給が前提となります。通常は1時間分程度の材料を随時供給する形を取った方がベターです。
作業者 教育
教育・訓練を行っていく場合に必要なことは、訓練を受ける人に対して必要とされる技能は何なのかを明確にすることと、目標を立てさせること、明確なスケジュールを作ることです。
管理者側のポイントとしては、教育・訓練ツールを充実させること、Know-Why教育(作業の意味と目的を伝える)を指向していくことにあります。
①必要とされる技能を明確
セル生産を行うにあたっては、従来の作業よりも多くの作業ができるようにしなければなりません。一般的には数種の製品の作業の内訳を示し、どの作業ができるようになってほしいのかを明確に伝えることが必要です。
②目標を立案
いつまでにどの作業ができるようになるのか、目標を立てることが大切です。目標に関しては管理者が指示するのが通例ですが、その際には作業者の要望をよく聞くことも大切です。
③スケジュールを作る
スケジュールは多能化マップなどを使用して管理していきます。技能の目標到達点はあらかじめ明確にしておき、教育専門員または管理者が実際にその作業を確認して合否判定を行うようにします。
セル生産の実施
準備が整った段階でセル生産を実行していきます。当初1週間程度はいろいろなトラブルが発生しますが徐々に落ち着いてきます。
1週間程度以降は落ちついてくるので出来高の向上を目指します。
通常は約1週間~10日ほどで従来のコンベアラインとほぼ同等の生産性を示すようになり、この後は生産性は向上します。
セル生産実施にあたって管理者が注意すべきポイントは以下の6点です。
①日々の問題点は日々解決する
②管理者は常に現場にいること
③当面の生産性は気にしない(記録は詳細に)
④作業者の要望を引き出す
⑤実運用では動作レベルの改善が必要
⑥モノの動き、流れ、停滞を見定める
評価、フィードバック(改善)
効果を正確に検証することが次の改善につながります。
その場合、生産性だけではなく、できるだけ多面的な検証を行うことを心がける必要があります。
セル生産の場合、ラインとしての評価は比較的容易に上がりますが、大切なのは、顧客視点の評価がどれだけ上がるかです。顧客視点の評価とはトータルリードタイムであり、原価低減、品質の向上です。
①ラインとしての効果検証
当面はセルラインとしての効果を検証することになります。セルラインとしての効果としては生産性、生産リードタイム、ライン内仕掛り量、人員削減数です。
②工場としての効果検証
セル生産を行っていく場合、最終的に必要なのは工場としての成果であり、経営成果なのです。ここが改善されなければ改善の意味がないのです。
セル生産方式のキーポイント
セル生産方式に適している商品
セル生産は原則的にはどのようなものにも対応できますが、対象となる製品がセル生産に適しているかどうかを商品の形態や重量で決めるのではなく重要なのはセル生産を行う必要があるかどうかを検証する事です。
セル生産はどんなものにでも対応できますが例えば生産タクトタイムが数秒(5秒前後)というような非常に短いものは、それに対応するセルを構築するためには、相当の努力が要ります。
それだけの短いタクトで製品を作るということは、かなりの生産数量があることが予想されますが、そのようなものに対応するセルを作ろうとするとセルの数ばかりが増えて、場内物流に相当の工数をかけなければ対応できないということになります。
つまり、このような環境下にある製品の場合はセル生産を行うよりもコンベア生産を見直し、ラインバランスを適性に管理していくほうが現実的です。
セル生産方式の最適人数
分割方式の場合、セル内の人数が多くなると仕事が細分化され、コンベア生産に近い状況になります。これはセル生産においても分割方式の場合は「ラインバランス」が存在するということです。当然のことながらラインバランスは人員数が多いほど低下していきます。
またセル内の人員が増えると手渡し生産(人がモノを移動させて隣の人に渡す方式)になる場合があり、大きく生産性を低下させる危険性があります。
巡回方式においてもセル内の人員が増加すると必然的にセルが大型化するため、人の移動距離が増加し組立時間よりも歩行時間の方が大きくなるといった現象も見受けられるようになります。
セル内の人員数と生産性には相関があり、必要以上にセルを大型化してしまうとかえって生産性が低下すという現象が起こるようになります。
セル内の最適人員は一般的には5名前後が最適の基準です。
セル生産方式 部品点数
セル生産は自己完結性を上げた生産方式ですから、必然的に一人当たりの組立部品数はコンベア生産よりも多くなります。また製品1個あたりの組立時間数もかなり多くなります。
分割セルの場合は一人当たり20~30点、巡回方式で30~40点、一人方式で50点前後の部品数を目安です。
また、一人1製品あたりの作業持ち時間数は15~20分程度が目安です。
*部品点数が多いので取り付け忘れを防止する為に次ページのようなポカヨケ対策もあります。
万能のセルはない
セル生産を行っていくうえで大切なポイントは、各セルの目的を明確にしていくことです。
セル生産は量産対応にも小ロット生産にも、複雑な工程の製品でも、でもいろいろな場面で活用することのできる生産手法ですが、全ての環境に対応できるマルチタイプのセルというものは存在しません。それは求めるものが違えば必然的に形が変わってくるからです。
簡単に言えば巡回タイプのセルは量産対応や生産量の変動には比較的対応しやすいのですが、精密さや部品点数の非常に多い製品、また作業者の習熟度が低い場合には残念ながら適していません。
分割タイプのセルは作業者の習熟や作業の精密度の違いには比較的対応しやすいのですが、生産量の変動の多い商品には対応しにくい部分があります。
一人方式のセルは近年採用されているところが多いようですが、たしかに小ロットの生産や複雑な工程の製品には適していますが量産対応やタクトタイムの短いもの、製品のライフサイクルの極めて短いものには適していません。
作業者のモチベーション
どんなに優秀な方がセルを工程設計しても100点のセルはデザインできません、現場の作業者の創意工夫、知恵によって100点のセルが完成します。
作業者が自分たちの仕事を見つめ直して、知恵を発現させて初めて100点満点のセルになるのです。セルを作るときは必ず現場作業者の方の意見を考慮しながらデザインしていってください。
また、作業者のヤル気を高めるためのいろいろな施策も大切です。各セル間競争を促したり、技能認定システムを構築したり、必要に応じて出来高制の給与システムを作ることも必要です。
いずれにしても作業者の方のヤル気を引き出すことが生産性を高める重要な要素です。
セル間を同期化
工程間の同期化ができていない状況でセル生産を行った場合、その効果は限定的で、たしかにセル内はリードタイムが短くなったり、仕掛りが減ったりしますが、工場全体で見るとほとんどリードタイム、仕掛りは減っていないということになります。
よって、工程間の同期化を考える場合は、単に一つのセルだけではなく生産工程全体、全工程を視野に入れて考えていかなければなりません。
セル間を同期化するためには詳細な生産計画を立てることが重要でそのためには、ネックエ程を正確に把握し、ネックエ程の能力を最大化させる形で生産計画を組み、ネックエ程能力に合わせた生産をします。
又、セル間の同期化を検討する場合、『同期の期間』を1時間単位の同期化なのか、1日単位の同期化なのかを明確にします。
通常は「半日単位の同期化」が多いです。
サプライヤーと共存しWIN-WINの関係を
セル生産で短納期調達を行う場合、サプライヤーの協力があって初めて達成が可能になります。
又、サプライヤーに対しては荷姿の変更、小ロット多頻度納品、品質の安定化、コストダウンも要求する場合があるので一方的に要求を突きつけるだけ
ではなく『Give and Take』で要望するモノを与えWIN-WINの関係になる
ことが大切です。
サプライヤーに対して与えられるものは一般的には以下があります。
①取引業者数を絞ることによって1社当たりの購買量を増加。
②正確な情報を出すことによってサプライヤーの生産工程を安定化。
③原材料業者との価格交渉を共同実施。
④品質技術管理技術などソフト面での協力。
⑤各種改善案の提示と改善に対するノウハウの提供。
トヨタ自動車株式会社のセル生産方式事例
トヨタ自動車は、トヨタ生産方式(TPS)を基盤として、セル生産方式を導入し、生産効率と品質向上を目指しています。
トヨタの生産システムとセル生産
トヨタ生産システム(TPS)とセル生産方式は、密接な関係にあります。以下に、両者の関連性とトヨタ自動車におけるセル生産の活用事例について解説します。
トヨタ自動車におけるセル生産の活用事例
- トヨタ自動車は、GRファクトリーなどでセル生産システムを採用し、多品種少量生産に対応しています。
- 車両試作工場では、AGV(無人搬送車)と作業者が連携し、効率的な組み立て作業を行っています。
- 働く人をより働きやすく、楽にすることを前提に、「お客様にご注文いただいたクルマを、良い品質で、安く、タイムリーにお届けするために、徹底的にムダを無くし、リードタイムを短くする」ことを目的にしたものです。
トヨタにおける多品種少量生産の実現
セル生産方式の導入
- 従来のライン生産方式とは異なり、一人または少人数の作業者が製品の組み立てを一貫して行う方式です。
- 多品種少量生産に柔軟に対応でき、生産量の変動にも迅速に対応できます。
- 作業者の多能工化を促進し、工程間の仕掛品の在庫削減やリードタイム短縮に貢献します。
- GRファクトリーなどで採用されています。
*GRファクトリーとは
トヨタ自動車が展開している「GR(GAZOO Racing)」ブランドの特別な生産工場です。
GRファクトリーは、主にトヨタのスポーツモデル(例:GRヤリス、GRスープラなど)を生産するために設立された、特別な手作業と品質重視の生産ラインを備えた工場。
通常の量産ラインと異なり、熟練の技術者が手作業を交えながら組み立てを行い、高い品質とパフォーマンスを実現。
名古屋市近郊の「元町工場」内にある専用施設です。
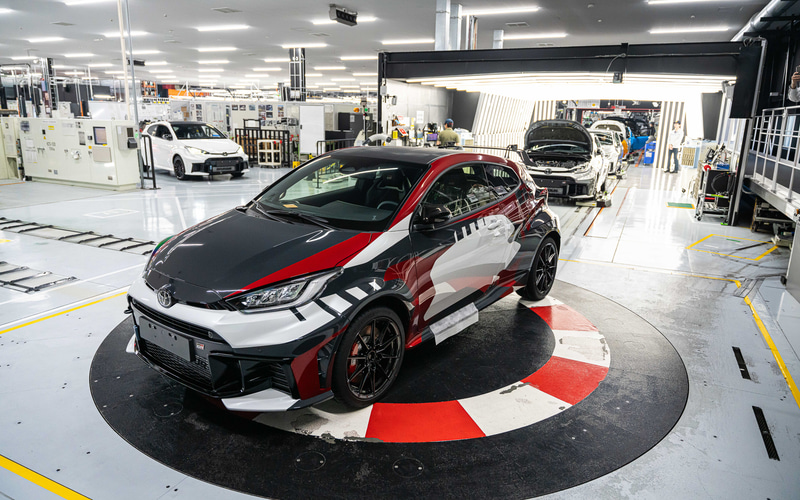
GRヤリス
フレキシブルな生産ラインの構築
- 生産ラインのレイアウトを柔軟に変更できる仕組みを導入し、多品種少量生産に対応します。
- U字ライン等の導入により作業者の動く範囲をせまくし、多工程を短時間でこなせるような工夫がされています。
- AGV(無人搬送車)などの自動化技術を活用し、効率的な部品供給や搬送を実現します。
セル生産方式のメリットとデメリット
セル生産方式は、従来のライン生産方式とは異なり、一人または少数の作業者が製品の組み立てを一貫して行う生産方式です。多品種少量生産に適しており、生産量の変動にも柔軟に対応できるというメリットがある一方で、デメリットも存在します。以下に、セル生産方式のメリットとデメリットをまとめました。
メリット
- 多品種少量生産への対応:
- ライン生産方式に比べて、製品の種類や生産量の変更に柔軟に対応できます。
- 多種多様な顧客ニーズに合わせた製品を効率的に生産できます。
- 生産量の変動への柔軟な対応:
- 需要の変動に合わせて、生産量を調整しやすいです。
- 過剰な在庫や生産不足を防ぎ、効率的な生産体制を維持できます。
- 仕掛品の在庫削減:
- 工程間の仕掛品の在庫を削減し、リードタイムを短縮できます。
- 資金効率の向上や、保管スペースの削減につながります。
- リードタイムの短縮:
- 製品の完成までの時間を短縮し、顧客への納期を短縮できます。
- 顧客満足度の向上や、競争力強化につながります。
- 作業者の多能工化:
- 作業者が複数の工程を担当することで、スキルアップにつながります。
- 作業者のモチベーション向上や、人材育成にもつながります。
- 初期コスト削減:
- 大規模な設備投資が不要なため、初期コストを抑えることが可能です。
デメリット
- 作業者の多能工化にはコストがかかる:
- 作業者の教育や訓練に時間とコストがかかります。
- 多能工の育成には、長期的な視点が必要です。
- 作業が属人化しやすい:
- 作業者のスキルや経験に依存するため、作業が属人化しやすいです。
- 特定の作業者が不在の場合、生産性に影響が出る可能性があります。
- ライン生産ほどの大量生産には向かない場合がある:
- 大量生産には、ライン生産方式の方が効率的な場合があります。
- 各セルの生産能力には限界があり、需要が急増した際に短期間で生産量を増やすことが難しい。
- 品質の安定化が難しい場合がある:
- セル生産方式は、作業者が複数の工程を担当するため、自動化が進んだ大規模な生産ラインに比べて労働力が必要であり、自動化が困難です。例えば、精密機械の生産などでは、品質の安定化が難しい場合があります。
セル生産方式は、メリットとデメリットを考慮し、製品の種類や生産量、作業者のスキルなどを総合的に判断して導入する必要があります。
ダイナミックセル生産方式の活用事例
ダイナミックセル生産方式とは、製品の種類や生産量の変化に応じて、柔軟に作業セル(チームや設備の配置)を組み替える方式です。固定されたラインではなく、製造現場の状況に応じて最適な作業ユニットを構成できるのが特徴です。
活用事例①:トヨタ自動車
背景:多品種少量生産への対応
トヨタでは従来のライン生産に加え、セル生産やU字ラインを組み合わせて、柔軟な生産を行っている。
一つのセルで複数工程を担当することで、設備の稼働率向上やリードタイム短縮を実現。
製品や需要に応じて、作業員の配置やセル構成を動的に変更。
活用事例②:カシオ計算機
背景:デジタルカメラや腕時計の多品種生産
カシオでは「ワンマンセル方式」を進化させ、ダイナミックセル方式を採用。
作業者が1人で複数の工程をこなし、必要に応じてセル単位の編成を変更。
結果として、在庫削減・リードタイム短縮・人員の有効活用を実現。
活用事例③:電子部品メーカー(例:京セラ)
背景:製品ライフサイクルの短命化に対応
京セラではセル方式を進化させ、製品仕様や工程変更に応じた柔軟なレイアウト変更が可能な生産体制を整備。
モジュール化された装置を使い、レイアウト変更を短時間で実行。
作業員の多能工化と合わせて、急な製品切り替えにも対応可能。
ダイナミックセル方式のメリット
多品種少量生産に対応しやすい
工程の無駄・待ち時間の削減
作業員のスキルアップ(多能工化)
スペース効率の向上
セル生産における作業者の役割
多能工(マルチスキル作業者)
複数の工程を一人でこなすことが求められる。
組立・検査・梱包までを担当するケースもあり。
繁閑に応じて役割を切り替える柔軟さも重要。
例:ある腕時計の製造では、1人の作業者が部品の取り付け、調整、検査をすべて行う。
セル内の工程改善への貢献
作業者は現場の課題を最もよく知る存在。
改善提案(カイゼン活動)を積極的に行い、生産性や品質向上に貢献。
自分の工程だけでなく、セル全体の流れを意識するのがポイント。
チームワークと協調
複数人でセルを構成する場合は、作業分担と連携が鍵。
他のメンバーの状況を見ながら、支援や調整を行う。
セル全体の出荷目標や品質に責任を持つ。
品質管理
不具合が発生した際は、即座に自工程で止める「自工程完結」が基本。
検査工程も自ら行うことで、品質の作り込みを実現。
不良を次工程に流さない意識が重要。
柔軟な対応力
ダイナミックセル生産では、製品や数量の変化に応じてセルの再編成が発生。
作業者は、その都度異なる役割や配置に適応する必要がある。
設備操作や作業指示の理解も求められる。
求められる資質・スキル
幅広い作業知識と技能
改善マインド
チームコミュニケーション力
柔軟性・適応力
品質意識の高さ
セル生産方式の現場での活用例
セル生産方式は、様々な現場で活用されています。以下に、具体的な活用例をいくつかご紹介します。
自動車産業
- トヨタ自動車のGRファクトリー:
- 多品種少量生産に対応するため、セル生産システムを採用。
- 作業者が複数の工程を担当し、効率的な組み立て作業を実現。
- 車両試作工場:
- AGV(無人搬送車)と作業者が連携し、柔軟な生産ラインを構築。
電子機器産業
- スマートフォンやパソコンの組み立て:
- 多品種少量生産に対応するため、セル生産方式を導入。
- 作業者が複数の部品を組み立て、製品を完成させる。
- プリント基板の実装:
- 多品種の基板を効率的に生産するため、セル生産方式を導入。
- 作業者が複数の工程を担当し、高品質な製品を生産。
精密機器産業
- 時計やカメラの組み立て:
- 高い精度が求められる製品の組み立てに、セル生産方式を活用。
- 熟練作業者が、高いスキルを活かして製品を組み立てる。
- 医療機器の製造:
- 多種多様な医療機器を、高い品質で生産するためにセル生産方式が活用されています。
その他
- 航空機産業:
- 多品種少量生産に対応するため、セル生産方式を導入。
- 作業者が複数の工程を担当し、効率的な組み立て作業を実現。
- 家具製造:
- 顧客のニーズに合わせた多種多様な家具生産にセル生産方式が活用されています。
セル生産方式の活用におけるポイント
- 作業者の多能工化:
- 複数の工程を担当できる作業者の育成が不可欠です。
- 教育や訓練を通じて、作業者のスキルアップを図る必要があります。
- 作業環境の整備:
- 作業者が効率的に作業できるような、レイアウトや作業環境を整備する必要があります。
- 作業者の負担を軽減するような、作業補助具や自動化設備の導入も検討する必要があります。
- 品質管理:
- 作業者のスキルに依存する部分が大きいため、品質管理を徹底する必要があります。
- 作業標準の明確化や、検査体制の強化が重要となります。
セル生産方式は、様々な現場で活用されており、その効果を発揮しています。導入にあたっては、メリットとデメリットを十分に理解し、自社の製品や生産体制に合わせた最適な方法を選択することが重要です。
セル生産方式の今後の展望
セル生産方式は、多品種少量生産への対応や生産量の変動への柔軟性など、多くのメリットを持つ生産方式ですが、今後の展望としては、以下のような点が考えられます。
デジタル技術との融合
- IoT(モノのインターネット)やAI(人工知能)などのデジタル技術を活用することで、セル生産方式の効率化や高度化が進むと考えられます。
- リアルタイムなデータ収集・分析による、生産状況の可視化や最適化
- AIによる作業支援や自動化による、作業者の負担軽減や生産性向上
- デジタルツイン技術による、シミュレーションや検証の効率化
- これにより、より柔軟で効率的な生産体制の構築が可能となり、顧客ニーズへの迅速な対応や、生産コストの削減が期待されます。
作業者の多能工化と技能伝承の高度化
- セル生産方式では、作業者の多能工化が重要な要素となります。
- デジタル技術を活用した教育・訓練システムの導入による、多能工育成の効率化
- 熟練作業者の技能をデジタル化し、伝承を支援するシステムの構築
- これにより、作業者のスキルアップや、技能伝承の効率化が図られ、高品質な製品の安定供給が実現されます。
サプライチェーンとの連携強化
- セル生産方式は、サプライチェーン全体の効率化にも貢献できます。
- サプライチェーン全体の情報を共有し、需要変動に迅速に対応できる仕組みの構築
- 部品メーカーとの連携を強化し、必要な部品を必要な時に必要な量だけ調達できる体制の構築
- これにより、サプライチェーン全体の最適化が図られ、リードタイムの短縮や在庫削減が実現されます。
人間中心のセル生産方式の追求
- セル生産方式は、作業者の負担軽減や働きがい向上にも貢献できる生産方式です。
- 人間工学に基づいた作業環境の整備や、作業補助具の導入
- 作業者のスキルや経験を活かせるような、柔軟な作業分担や作業計画
- これにより、作業者のモチベーション向上や、離職率低下が期待されます。
環境への配慮
- 持続可能な社会の実現に向けて、環境負荷の低いセル生産方式への転換が求められます。
- 省エネルギー化や資源の有効活用
- 廃棄物の削減やリサイクル
- 環境に配慮した材料や部品の選定
- これにより、環境負荷の低減と、企業の社会的責任の遂行が両立されます。
セル生産方式は、デジタル技術との融合や、人間中心の考え方を取り入れることで、さらなる進化を遂げると考えられます。
セル生産方式の導入手順と注意点
セル生産方式の導入は、生産効率と柔軟性を向上させるための有効な手段ですが、成功させるためには適切な手順と注意点があります。以下に、セル生産方式の導入手順と注意点をまとめました。
導入手順
- 目的の明確化:
- セル生産方式を導入する目的を明確にします。
- 生産効率の向上、多品種少量生産への対応、リードタイムの短縮など、具体的な目標を設定します。
- 対象製品の選定:
- セル生産方式に適した製品を選定します。
- 多品種少量生産、工程の複雑さ、作業者のスキルなどを考慮します。
- セル設計:
- 最適なセルレイアウトを設計します。
- 作業者の動線、部品の配置、作業スペースなどを考慮します。
- 作業分析と標準作業の設定:
- 各工程の作業を分析し、標準作業を設定します。
- 作業時間、作業手順、品質基準などを明確にします。
- 作業者の多能工化:
- 作業者が複数の工程を担当できるように、教育・訓練を行います。
- スキルマップを作成し、作業者の習熟度を管理します。
- 試運転と評価:
- セル生産方式を試運転し、問題点を洗い出します。
- 生産効率、品質、作業者の負担などを評価し、改善点を見つけます。
- 本格稼働と継続的な改善:
- 試運転の結果を踏まえ、セル生産方式を本格稼働させます。
- 定期的に改善活動を行い、生産効率と品質の向上を図ります。
注意点
- 作業者の負担軽減:
- 立ち作業や移動が多くなるため、作業者の負担を軽減する工夫が必要です。
- 作業補助具の導入、作業環境の改善などを検討します。
- 品質管理の徹底:
- 作業者のスキルに依存する部分が大きいため、品質管理を徹底する必要があります。
- 作業標準の明確化、検査体制の強化、ポカヨケ対策などを実施します。
- 作業の属人化防止:
- 作業が属人化すると、特定の作業者が不在の場合に生産が滞る可能性があります。
- 作業手順の標準化、多能工育成、作業記録の共有などを徹底します。
- 生産計画の柔軟性:
- 多品種少量生産に対応するため、柔軟な生産計画が必要です。
- 需要変動に迅速に対応できるような、生産計画システムを導入します。
- コミュニケーションの活性化:
- 作業者間のコミュニケーションを活性化し、情報共有や問題解決をスムーズにします。
- 定期的なミーティングや、意見交換の場を設けます。
- トップの理解とコミットメント:
- セル生産方式の導入には、トップの理解とコミットメントが不可欠です。
- トップが積極的に関与し、現場を支援する体制を構築します。
セル生産方式の導入は、組織全体で取り組む必要があります。上記の注意点を参考に、慎重に導入を進めることで、セル生産方式のメリットを最大限に引き出すことができます。
スライドシェア 中小企業のIoT導入 資料(PDF版)
セル生産方式ライン 資料(PDF版)無料でダウンロードできます。
参考文献:
コメント
[…] 関連記事:セル生産方式ライン […]