連続時間分析による作業改善
仕事量は、時間という尺度で数値化し、さまざまな作業を時間分析し、問題点を見つけ改善していきます。時間分析とは、ある作業を細かな要素作業、または単位作業に分け、それらの時間値を観測、記録し、分析することで、作業方法、作業条件、作業環境を検討し、改善につなげる手法ということができます。
時間分析の種類は、用いる時間測定の道具によって、「ストップウォツチ法」と「フィルム分析法」に大別されます。分析概要としては、現在の作業を各要素作業に分け、要素作業ごとに時間を測定します。測定は一般に、ストップウォツチ観察法を用います。練習することで、誰もが観測できるようになリますが、実践に活かすとなると工数がかかり大変です。
しかし、分析機器の進歩は、分析を容易にしてくれます。市販のスマホ、デジタルカメラを使用すると簡単に分析でき、効率よく実践に活かすことができます。
要素作業分解のポイント
①他の要素作業との区分を明確にします。
②観測可能な範囲と程度は、目的に応じて決めます。
③同じ目的の動作を一つの構成とします。
④手作業時間(手作業は機械に拘束されるか否かで区別)と機械作業時間を区別します。
⑤定数的作業(方法や時間がほぼ一定)と変数的作業(要素の時間が材料の違いなどで変
化)を区別します。
⑥サイクル作業とサイクル外作業を区別します。
スマホ、デジタルカメラを使う連続時間分析
ここでは、分析の容易なスマホ、デジタルカメラを使う連続時間分析を説明していきます。
分析の流れの概要
① カメラ設置と録画
作業エリアに固定カメラを設置(作業者の動線が分かるように)
一連の作業(例:部品の組立て、検査、梱包など)を録画
② 作業の分類
録画された作業を以下のように分類します(IE手法の一部):
作業カテゴリ | 内容の例 |
---|---|
正味作業 | 組立・溶接・ネジ締めなど生産に直接関わる動作 |
付随作業 | 工具の準備・部品の受け取りなど |
無駄 | 探す・待つ・探す・動線が長すぎるなど |
手待ち | 材料待ち・機械待ちなど |
移動 | 材料や工具の取りに行く、戻るなど |
③ 時間計測と分析
動画を見ながら、作業ごとの連続時間を計測し、集計します。
作業内容 | 回数 | 平均時間(秒) | 合計時間(分) |
---|---|---|---|
正味作業 | 30 | 45 | 22.5 |
無駄動作 | 15 | 20 | 5 |
移動 | 10 | 30 | 5 |
→ これにより、「どこにどれくらいの時間を使っているか」が見える化されます。
改善に活かす視点
無駄動作の削減:よく探している道具は置き場所を改善できるか?
移動時間の短縮:動線レイアウトを見直せないか?
手待ち時間の解消:材料や情報の流れにボトルネックはないか?
撮影後に使用する分析用紙
撮影後に使用する分析用紙には、いろいろなタイプのモノがあります。分析様式を大別すると、下図のように、「サイクル作業用」と「非サイクル作業用」に分けられます。自社にあったモノをつくればよいでしょう。
要素作業の観測時の手順
①分析の対象を明確にする
②対象作業と対象作業者を決める
③観測用紙など分析の準備をする
④予備調査をして要素作業を分解する
⑤観測回数を決める
⑥観測を実施する
スマホ、デジタルカメラ分析の場合、ある程度のポイントが絞れればあとで分析できますので、①と②が重要になってきます。
スマホ、デジタルカメラ分析の分析記録と整理の仕方
下図に示す、組立ラインの最終工程(検査、箱詰め、部品づくり)の事例で、分析記録のとり方を説明します。
①分析開始は、要素作業の区切りのよいところから始めます。
②要素作業の測定ポイント(区切り)の時刻を読み取り、順次記録します。区切りの目安は、作業の変わった箇所を中心に行います。ロスの多そうな箇所は、さらに細かく区切っていきます。
③読み取った時刻は、分析用紙の読み記号”の欄に記入します。
時間分析の記録のとり方
時問分析の記録の要領は、次のように行います。
①分の位が前の要素作業と同じ場合には、分の位を省略してもかまいません。
(例)製品の検査をしてポリ袋へ入れる(50’50” 50分50秒⇒50秒)
②違う分単位にまたがって要素作業が行われた場合、記録する時間は、必ず分の位から記人します。
(例)合紙(スチレンシートと板紙)を箱へ入れる(0” 0秒⇒51分0秒)
③観測中に事故や通常のサイクルと違った動きがあった場合、記録する時間は、必ず分の位をつけることを忘れないようにします。
(例)サンプル検討(45” 45秒 ⇒53分45秒)
④作業の1サイクルの最初と最後には、分の位をつけておくことが必要です(短い時間のサイクルならデジカメにも記録されているので不要)。
⑤不規則的要素作業の時間記録に当たっては、分の位を必ずつけます。
(例)バッテリー端子の修正(14” 14秒⇒53分14秒)
⑥不規則的要素作業が発生したら、要素作業名をそのつど、余白の予備欄へ記録します。そして対応する規則的要素作業の読み時問とこの不規則的要素作業の読み時間に合わせて記号(*、△等)をつけ、関連を明らかにします。
(例)△53’29と△53’45は通常の作業では生じないが、管理者がサンプルの提示を求めた。
⑦要素作業および不規則的要素作業でも、測定できないモノはその要素作業を分析用紙の余白に書き、読み時間に分かる印を記入しておきます。
(例)部品を床の上に落したときは”オ”と記入。
⑧規則的要素作業が省略されたときは、”↓”を読みの欄に記入しておきます。
⑨なんらかのトラブルで記録できなかった場合は、要素作業の読み欄にM(Miss)と記入し
ておきます。
⑩要素作業が細かい動作の繰り返しで、しかもその回数を知っておく必要のある場合には、読み時間の欄を利用して、その回数を記録します。動画は繰り返し見ることができるので、1個ずつ秒単位で記録します。バラツキから改善点を発見できることが多いものです。
(例)回数を正の数で表示する場合(正正……)
流れ作業のムダの見つけ方
生産を流れ作業方式で行うとき、知っておきたいのがラインバランスの考え方です。
「流れ作業方式」とは、1つの作業をいくつかに分け、それを数人の人で分担し、作業を行うことで、個々の作業者に作業を習熟してもらい、効率化を図ろうとした生産方式です。
1つの仕事を数人に分けるのですから、各作業者の作業を分析して、適正な作業順序、作業時間を決め、作業対象物が一定の速度で流れるようにする必要があります。
「ラインバランス」とは、生産ラインを構成する各工程での所要時間のバランス状態のことで、各工程を受け持つ作業者の作業時間をできるだけ同じにして、工程問のロス時間をなくしていこうとするものです。
ラインバランスがとれていないと、下図(改善前)の3工程では、2工程から流れてきた仕掛品が停滞し、5工程では手待ちが発生します。3工程の作業者は、仕事に追われ、たえず負荷がかかり、疲労も大きくなリミス発生につながっていきます。
逆に、5工程の作業者は仕事に余裕があるため、手待ちでいるのは他の作業者に悪いと思い、見かけの作業を行い、余分につくつてしまうことになります。
楽な工程、忙しい工程は作業者が一番知っているため、工程間のバラツキが大きければ大きいほど、作業者問に不満が蓄積することになります。
下図(改善後)は作業量を各工程で均等になるように分担したものです。作業量が均一化され、問題工程(改善前の3工程と改善後の4工程)で比較すると、27秒の作業時問短縮がなされたことになります。
ラインバランス分析の仕方
ラインバランス分析は、次のような目的のときに使用します。
①各工程の所要時間を把握し、工程全体の時間の均一さの度合いを客観的につかみたいとき。
②作業時間のもっとも長くかかっている問題(ネック)工程を見つけ出したいとき。
ラインバランス分析グラフの作成手順
①下図のようなグラフをつくるので、グラフ用紙を準備します。
②横軸に工程名を、縦軸に作業時間を描きます。
③各工程の下に、作業人員、各工程の正味時間、その他重要な事項を記入します。
④縦軸に時間値を書き、工程の中で一番長くかかっている時間を目安にして、その時関の分
だけ目盛をといます。
⑤各工程の上にそれぞれの工程の所要時間をメモし、棒グラフを作成します。
⑥一番長くかかっている工程の棒グラフの上に、横に長い線を引きます。
⑦ピッチタイム(ラインの速度、1個の製品のできる時間)を時間の目盛にとり、横に長い
破線を引きます。
⑧上記の⑥と⑦で引いた横線間と棒グラフとの間に斜線を引きます。
改善後のラインバランスは、現状での作業実力です。現状の理想としてもっとも早い作業スピードで製品ができあがる時間であり、タクトタイムとは違います。
ラインバランス改善の考え方
ラインバランスの状態を分析し、改善する考え方として次のようなものがあります。
ラインの内でもっとも時間値の長いネックエ程を対象に、時問短縮を行います。(下図①)
作業時間の長い工程についての改善の考え方
①作業で分担できるものは分割し他の工程に分配します。(下図②)
②作業者数を増やします。(下図③)
③作業の改善(動作分析、動作経済の原則、機械化、自動化、設備、治工具の選択など)を行います。(左図④)
④熟練者を配置します。
⑤リリーフマンを準備します。工程の負荷変動が多いとき(トラブルに対応)などのとき、ライン全体にそのつど、応援可能な人を準備します。
作業時間の短い工程についての改善の考え方
①他工程から作業の一部を移し、一人当たりの作業量を増やします。
(左図②、⑤)
②作業で分担できるものは分割し、他の工程に分配し、その工程をなくします。(左図⑤)
左図①でネックエ程は3工程になりますので、最初は3工程の時間短縮に取り組まねばなりません。
しかし、3工程をどれだけ時間短縮しても、作業時間が5工程以下になると、全体の効率にはつながらなくなります。次のネックエ程は5工程になりますので、5工程の時間短縮が必要になってくるのです。
連続時間分析の改善事例の紹介
【事例1】組立作業のムダ時間を削減(精密機器メーカー)
背景・課題
精密機器の組立ラインで「作業者ごとの作業時間差が大きい」という課題があった
生産性にムラがあり、1日あたりの生産数にもバラつき
分析方法
組立作業をデジタルカメラで録画
作業を分類(組立、工具準備、探す、移動など)して、各作業の連続時間を計測
IE手法に基づいて「正味作業」「ムダ」「移動」などに分類・可視化
分析結果
工具を探す・取りに行く「ムダな動き」が1人あたり1日約25分間発生
組立台に必要工具が全て揃っていないケースが多かった
改善内容
作業台に工具ホルダーと部品トレイを設置(5Sの徹底)
よく使う道具を“定位置化”し、動線を短縮
改善効果
無駄動作が1人あたり1日25分 → 5分に短縮
ライン全体の組立効率が15%向上
作業者の疲労感・ストレスも軽減された
【事例2】検査工程の「手待ち時間」を可視化して改善(食品工場)
背景・課題
製品の目視検査ラインで、作業者がしばしば「何もしていない時間」が発生
検査対象が来るまでの“手待ち時間”が見えにくい
分析方法
カメラで検査ラインを録画
「検査している時間」「手待ち時間」「整理・報告」などをフレームごとに分析
ガントチャートで時間の流れを可視化
分析結果
検査対象の供給が不安定で、1時間あたり約20分が手待ち状態
原材料供給ラインとの連携が弱かった
改善内容
原材料供給担当者と検査担当者でタイミングの共有ルールを策定
補助的に「供給準備サイン」を導入(ランプ点灯)
改善効果
手待ち時間が20分 → 5分に短縮
検査ラインのスループット(通過量)が1.2倍に向上
分析ポイント | 成果 |
---|---|
無駄動作の可視化 | 動線改善、道具配置で効率アップ |
手待ち時間の分析 | 情報連携・サイン導入で作業平準化 |
動画での記録 | 客観的な証拠として共有・教育にも活用 |
工場での生産性改善 連続時間分析の未来の展望
AIによる動画自動解析の普及
◆ 今まで
録画した動画を人の目で見て、作業を手動で分類・計測する必要があった
労力が大きく、継続的な改善活動の障壁になりがち
◆ これから
AIがリアルタイムで映像から作業動作を識別し、
「作業開始〜終了の時間」「作業種別」などを自動でタグ付け・可視化学習済みモデルで作業ごとの動作パターンを記録・比較できるようになる
✅ 期待効果:時間分析の工数削減/改善速度の向上/客観性の強化
IoTセンサーとの連携による“多角的分析”
◆ 進化ポイント
デジタルカメラ + 動作検知センサー + 位置情報(ビーコン) + 作業者のウェアラブルデバイス を組み合わせ
映像だけでなく、「誰が、どこで、どの作業を、どれだけの負荷で行っているか」がリアルタイムで取得可能
期待効果:
作業負荷や移動時間のリアルな把握
作業者ごとの癖・疲労状況に合わせた改善が可能に
デジタルツインでの“仮想改善”シミュレーション
◆ 概要
工場の作業環境や動線を3Dで再現した「デジタルツイン」上で
連続時間分析データを元に仮想的な改善案のシミュレーションができる
◆ 例
レイアウトを変更すると移動時間が何秒短縮されるか?
工具の配置変更で無駄動作はどれだけ減るか?
期待効果:改善前に“効果の見える化”ができ、実行リスクが減る
個別最適化(パーソナライズド改善)
◆ これまで
工程単位での標準化・改善が主
◆ これから
時間分析+バイタルデータ(心拍・姿勢など)を組み合わせて
作業者一人ひとりに合った改善(椅子の高さ、作業割り振りなど)を実現可能に
期待効果:
安全性・快適性の向上
労災リスクの軽減、定着率向上にもつながる
最終的なビジョン:“自律的に改善するスマート工場”
デジタルカメラとセンサーが全作業をモニタリング
AIが連続時間をリアルタイム分析し、改善提案を自動で通知
管理者は「AIが提案した改善案を確認・承認する」だけで済む世界へ
未来のキーワード
キーワード | 概要 |
---|---|
AI解析 | 映像から自動で動作・時間を識別 |
IoT連携 | 実作業データと映像の統合分析 |
デジタルツイン | 仮想空間で改善をテスト・検証 |
パーソナライズ改善 | 一人ひとりに合わせた作業最適化 |
自律的改善 | AIが提案・人が判断というスマート運用 |
こうした未来の展望は、大手企業だけでなく中小工場でも十分に活用可能になってきています。
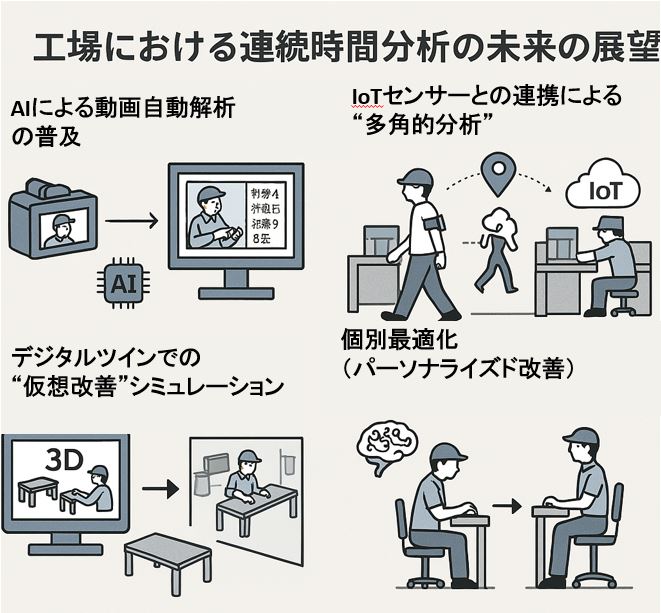
連続時間分析の未来の展望
*工場のIE手法については下記の文献に色々な活動事例等が更に詳細に記載されています。
参考文献: