作業分析の基礎
IE手法とは?
IEとは、端的に言うとモノづくりにおける3ム(ムダ・ムラ・ムリ)を改善(排除)すること。この中でとくに重要なことはムダに対する考え方であり、その分析と改善の仕方である。
具体的には機械が加工(切削)しているが、1回で削れるのに2回で削るムダ。
スピード100 cm/分送りのところを80 cm/分送りするムダなどがある。
付随・付帯作業では、型替え、脱着、検査などに多くの時間を要するムダ。余裕では、作業者の離席(用達・打合せ・探し)によるムダなどが発生している。
IE手法では仕事そのものを工程の流れ(工程分析・動作研究)と、時間の流れ(稼働分析・時間研究)の面から分析し、そのムダ取りをする。
IEは米国で大規模な生産革新が求められた1900年代初めに理論化され、作業の基本となるF動作研究」をF・B・ギルブレスが、「時間研究」をF・W・テーラーが行った。そしてF・W・テーラーにより1909年に「科学的管理法の原理」が発表された。
日本でこのIEの基本(動作・時間研究)を忠実に実行し、さらに工夫・発展させたのが、トヨタ生産方式:TPS(TOYOTA Production Systemt) をつくった大野耐一氏である。
関連記事:IE手法とは?
作業動線とは?
「動線図」とはレイアウトにモノや人の動線(モノや人が動く経路を示す線)を描き込む分析図である。作業動線図とも呼ぶ。活動の対象とする職場やライン,フロアーのモノの流れや人の動きを,自分の手で描く。
「動線図」を描くためにまずレイアウトを描いていく。フロアーのどこに何かあるのか,柱の位置はどこか,又、設備が何台あるのか,号機の位置を確認する。さらに作業者の配置も描き込む。
大まかなレイアウトができたら,作業者が運ぶモノの流れをそのままどの場所からどの場所へ動くかという動線を描き込む。製品の種類ごとに違う場合は色別に描いても良い。
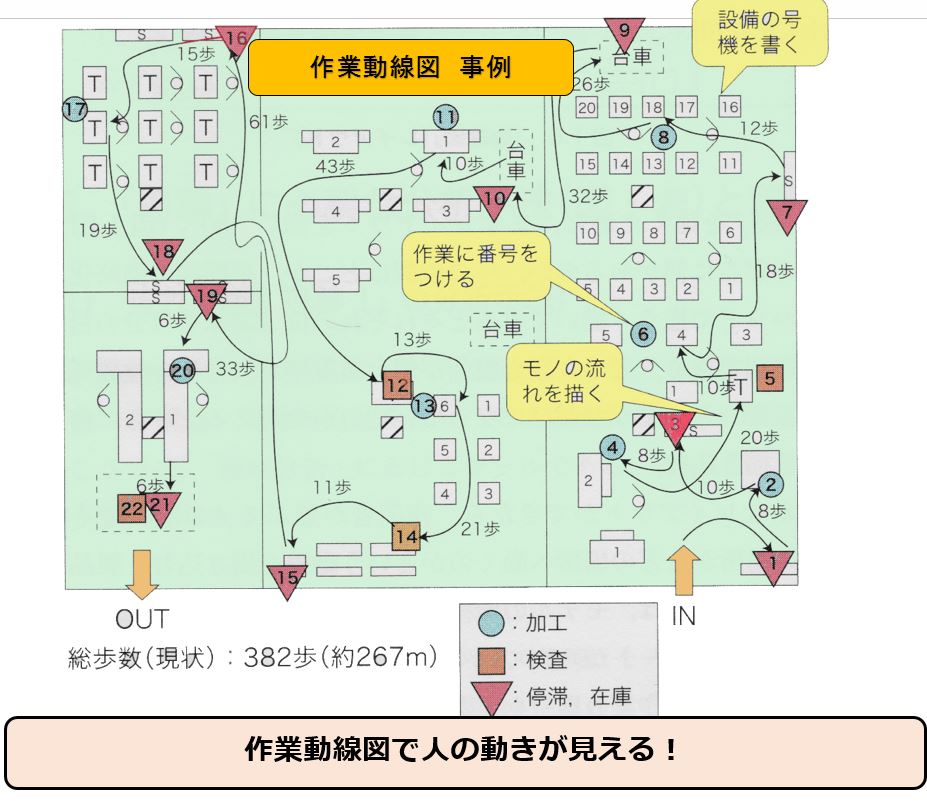
作業動線図とは?
流れ図とは?
流れ図、フローチャート (flowchart) は、プロセスの各ステップを箱で表し、流れをそれらの箱の間の矢印で表すことでプロセスを表現する図である。
流れ図はフリーフォーマットで,メンバーが理解しやすく描き、最初に「流れ図」を描くときは,現状把握として現状を描き、改善が進んだ後は目標とする“めざす姿を描く。
「流れ図」に描く内容を次にあげる。
① モノの加工,検査,作業台などの作業ポイント及び,棚台車による待機,置場などのストックポイント。
② 作業ポイントとストックポイント間のモノの流れ。
③ ポイント間の運搬のタイミング(運搬頻度,運搬の単位など)。
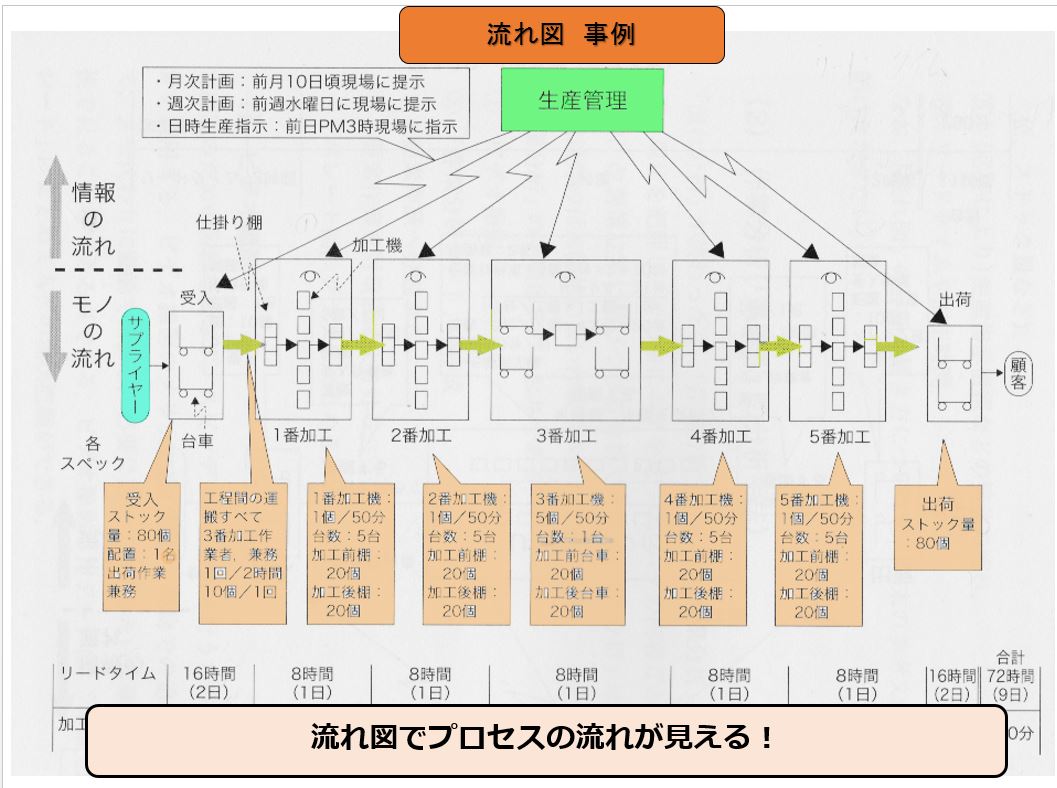
流れ図とは?
作業分析シートとは?
ビデオ撮影したデータをもとに「作業分析」を行い、「作業分析」においては,付加価値作業とその他の付加価値をつけない作業,及びムダに仕分けることが重要であり、仕分けをするためのツールとして「作業分析シート」を作成する。
「作業分析シート」では,人の作業を要素作業に分けて,付加価値作業とそれ以外に仕分ける。この要素作業とは,改善の対象とする作業において,それ以上分割しても改善の検討が行えない最小単位の作業のことである。
したがって,各改善の検討レベルにおいて要素作業の単位が変わることもあるが,データの分析をスピーディーに行うためには,必要以上に細かく要素作業を分割せず,改善の検討レベルにより,要素の大きさを明確にして行うことがポイントである.例えば,運搬,移動,加工などの同じ作業と考えられる動作を動作ごとに,ひとかたまりの要素作業と捉えて分割する。
付加価値作業以外のものには,明らかなムダと付加価値をつけない作業とがあるが,付加価値をつけない作業も,さらに対策や改善のねらい。
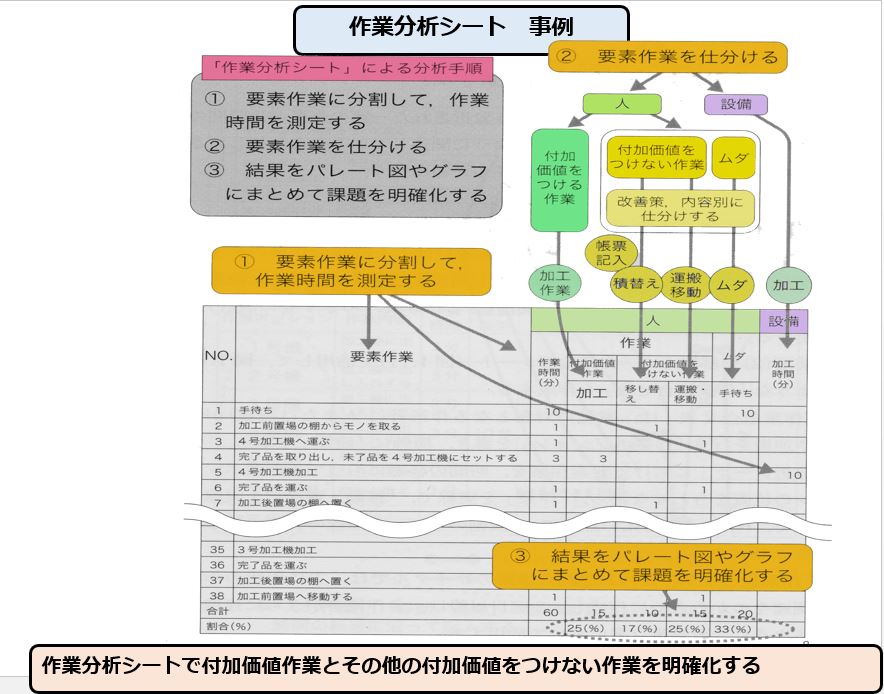
作業分析シート 事例
作業組合せ表とは?
1)「作業組合せ表」により,人と人,あるいは人と設備の作業のタイミングを分析し,作業の組合せや繰り返し精度を改善する。
「作業分析シート」を使用して「作業組合せ表」を作成する。
「作業組合せ表」は,縦軸に対象となる作業者(1人または複数)が作業や運搬を行う「作業ポジション」を書き,横軸に「時間」を取る。
「作業分析シート」における要素作業を,時間の経過に沿って,作業ポジションの位置を合わせながら「作業」を実線で,「移動・運搬」を実線の矢印で,「手待ち」を太い点線で「設備の加工」を点線の矢印で表しながらつないでいく。
「作業組合せ表」は,1巡目の追跡のサイクルでは,主に現状の作業の関連をつかむために作成し,2巡目以降は,各作業者がさらに連携できるように,改善策立案において活用する。
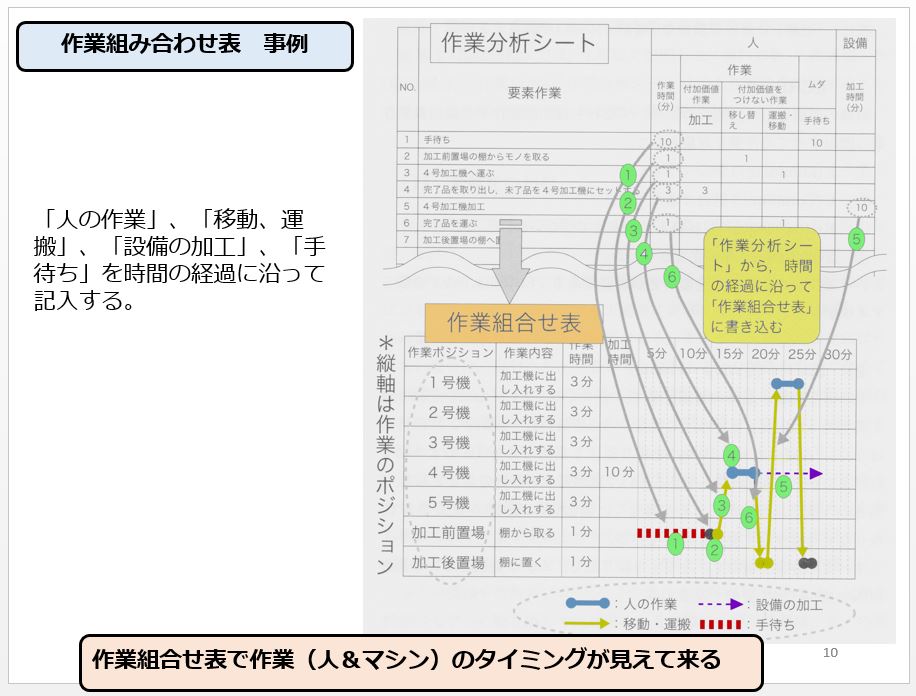
作業組み合わせ表 事例
工程の整流化とは?
「整流化」とは,ジョブショップの工程ごとのフロアー配置からフローショップの機種ごとの工程順配置に変えることを指す(下図)。
「整流化」のねらいは,工程の壁を取り,工程を連結して付加価値作業を最短でつなげることである。作業者には多能工化が要求され作業者レベル向上につながる。
製造業の生産工程や流通業の物流などにおいては製品、情報が入り乱れたり、途中で滞留逆流しムダが発生します、それを整流化によって定められた順序で工程を流れるようにします。
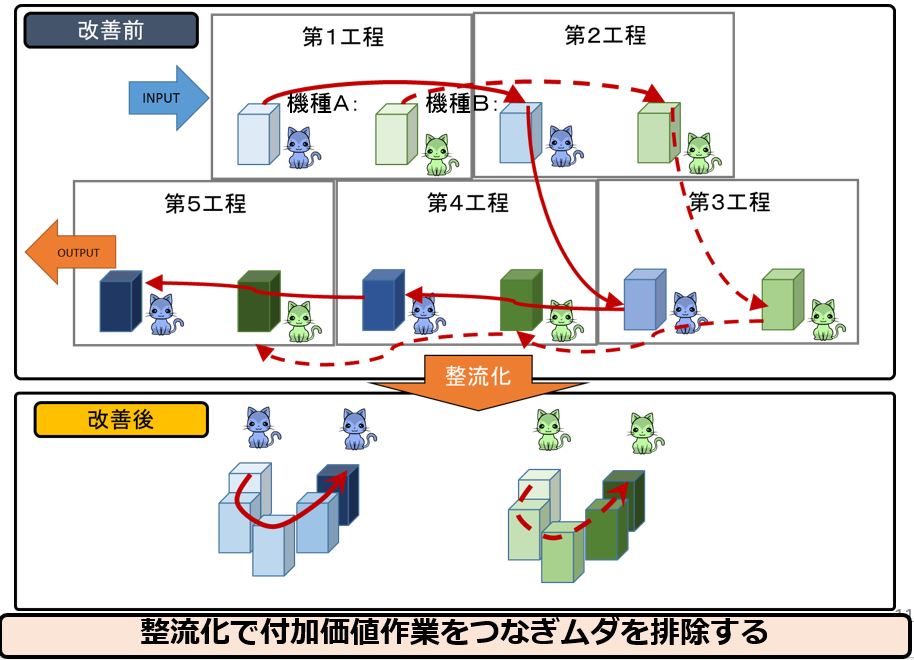
整流化とは
IE分析事例~作業分析 ケーススタディー
ある工場の工程の作業分析事例を基にIE手法を学ぶ。
ケーススタディ工場の概要
ウルトラ社は材料を加工し,ウルトラマンの人形を作る工場である(下図)。
材料を受入から投入し,1番,2番と加工を行うことにより,工程が進行していき,5番の加工を終えると最終製品が完成する、 各工程の加工機は基本的に製品を1個ずつ加工するが3番加工機は5個を一括して(5個を1バッチとして)加工する加工機である。
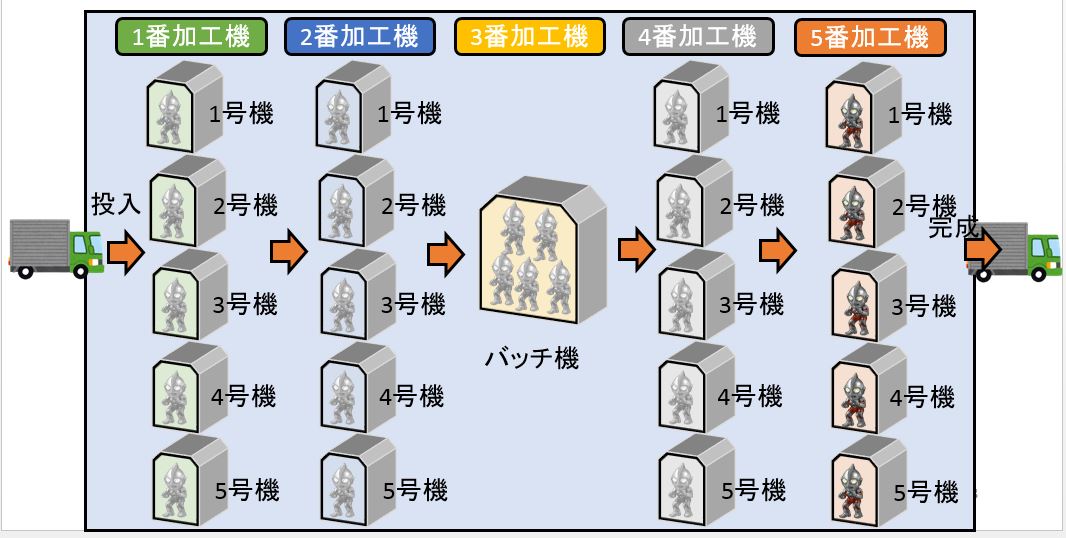
事例工場の概要
下記は工場のレイアウトと運搬者&オペレーターの動線図である。
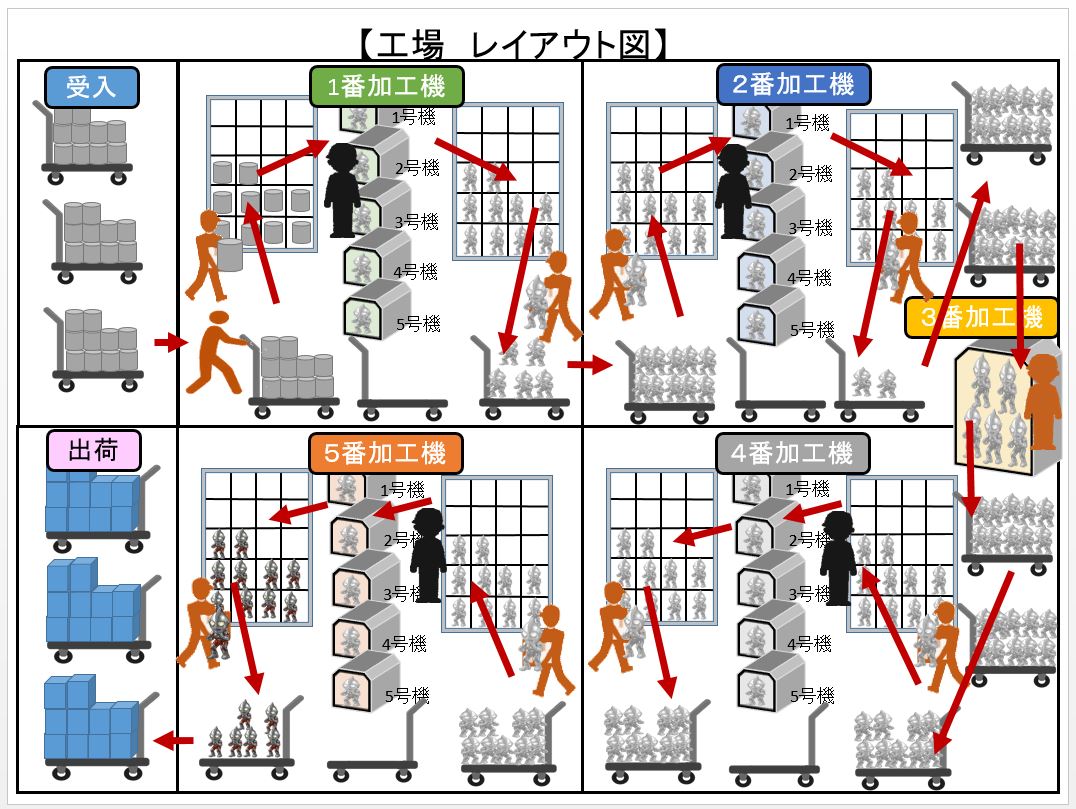
工場レイアウト&動線図
又、オペレーター&運搬車の動きがわかりやすいように分けて描いたモノが下記の図である。
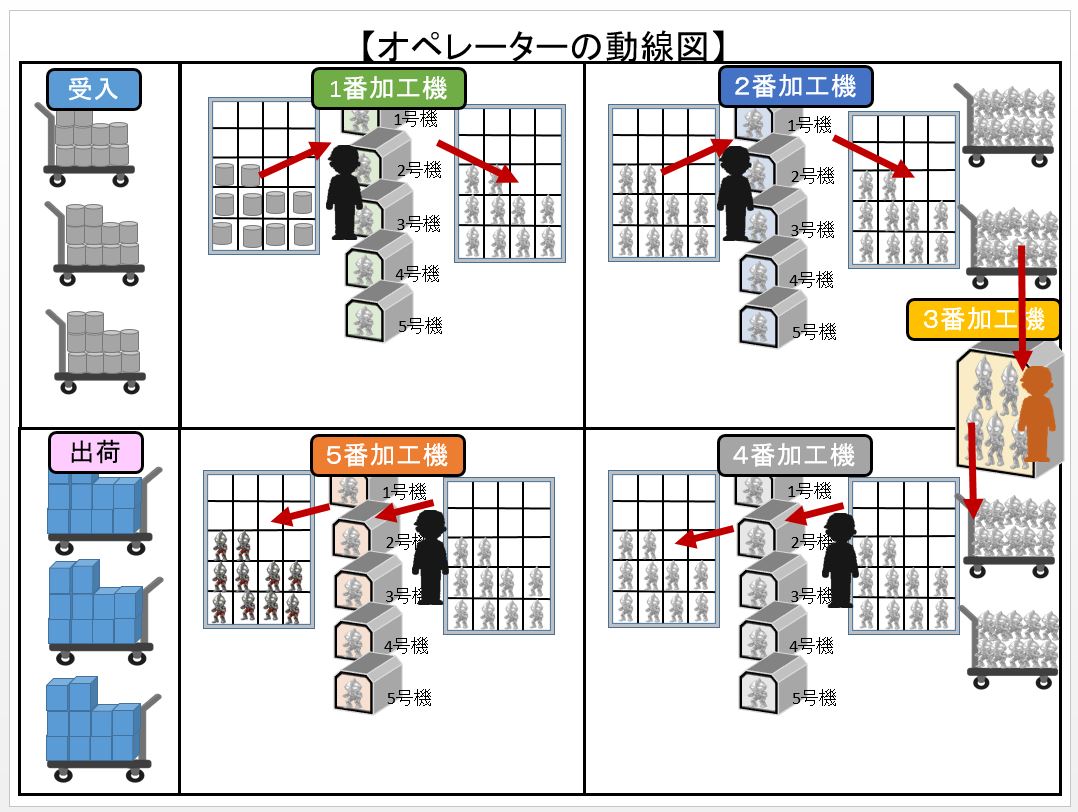
オペレーターの動線図
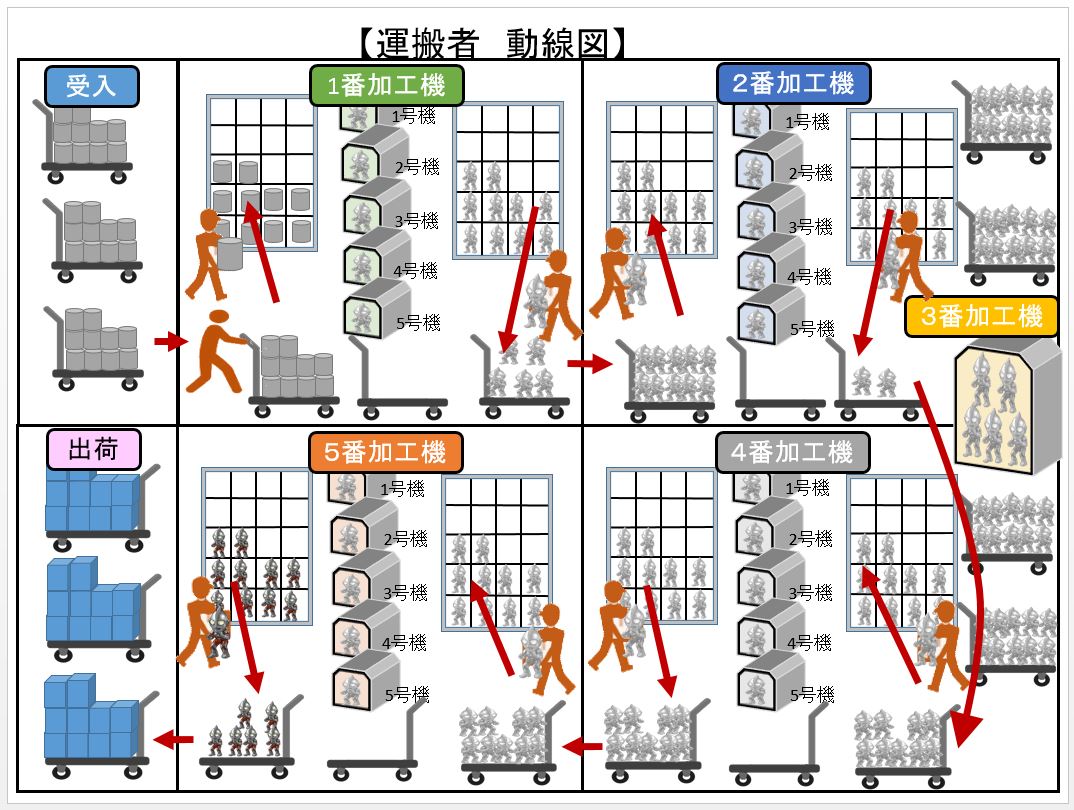
運搬者の動線
現状把握&分析:
1番加工機のオペレター作業
オペレーターは下記の手順で1号機~5号機を巡回し、停止したマシンごとに順に作業を実施。
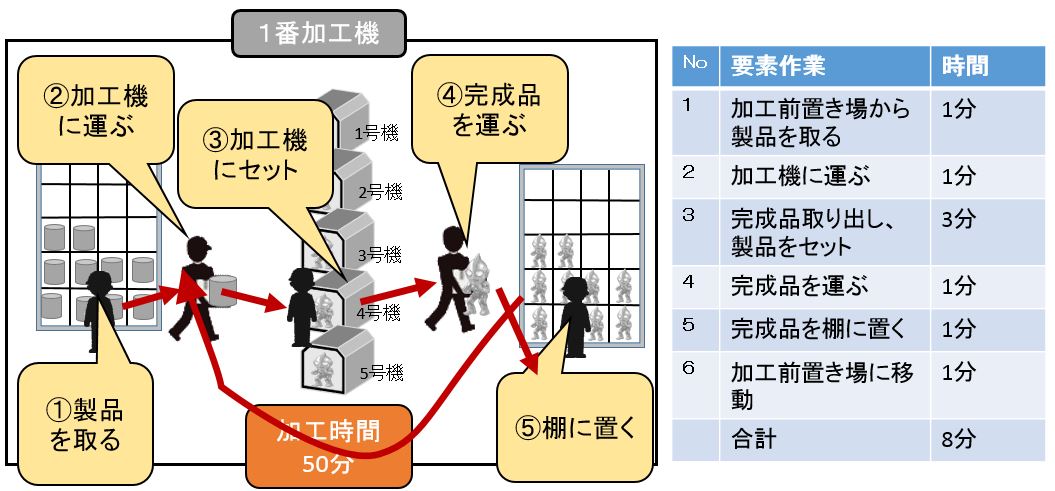
1番加工機の動線
1番加工作業の作業分析シート
1番加工作業をビデオ撮影して作業分析シートを作成し、次に内訳を分かり易くする為にパレート図で表した図が下記であり、加工時間より手待ち時間が多い。
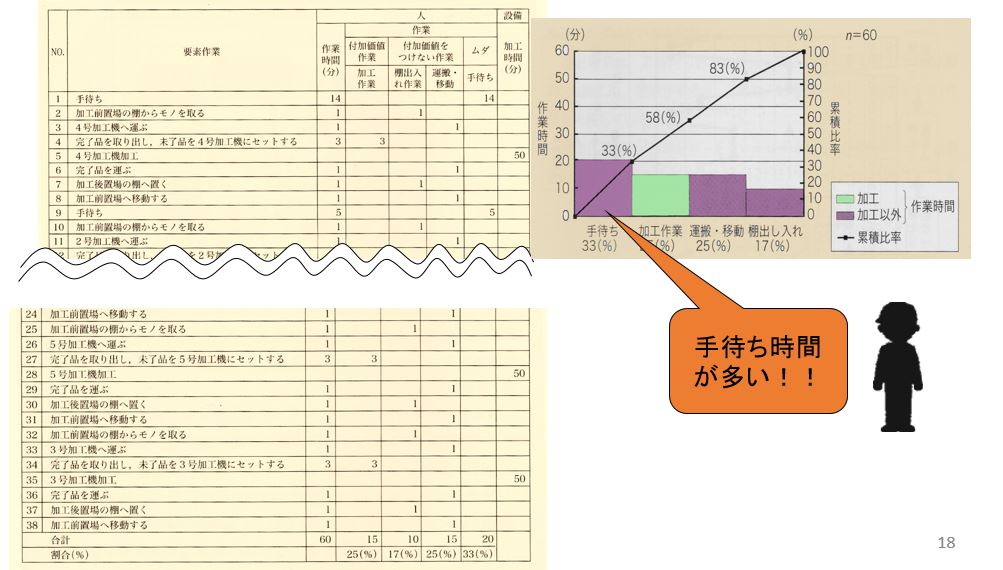
一番加工機の作業分析シート
1番加工作業の「組み合わせ表」
次に作業分析シートから1番加工作業の「組み合わせ表」を作成し、作業に手順、繰り返しを検討して改善を進める。
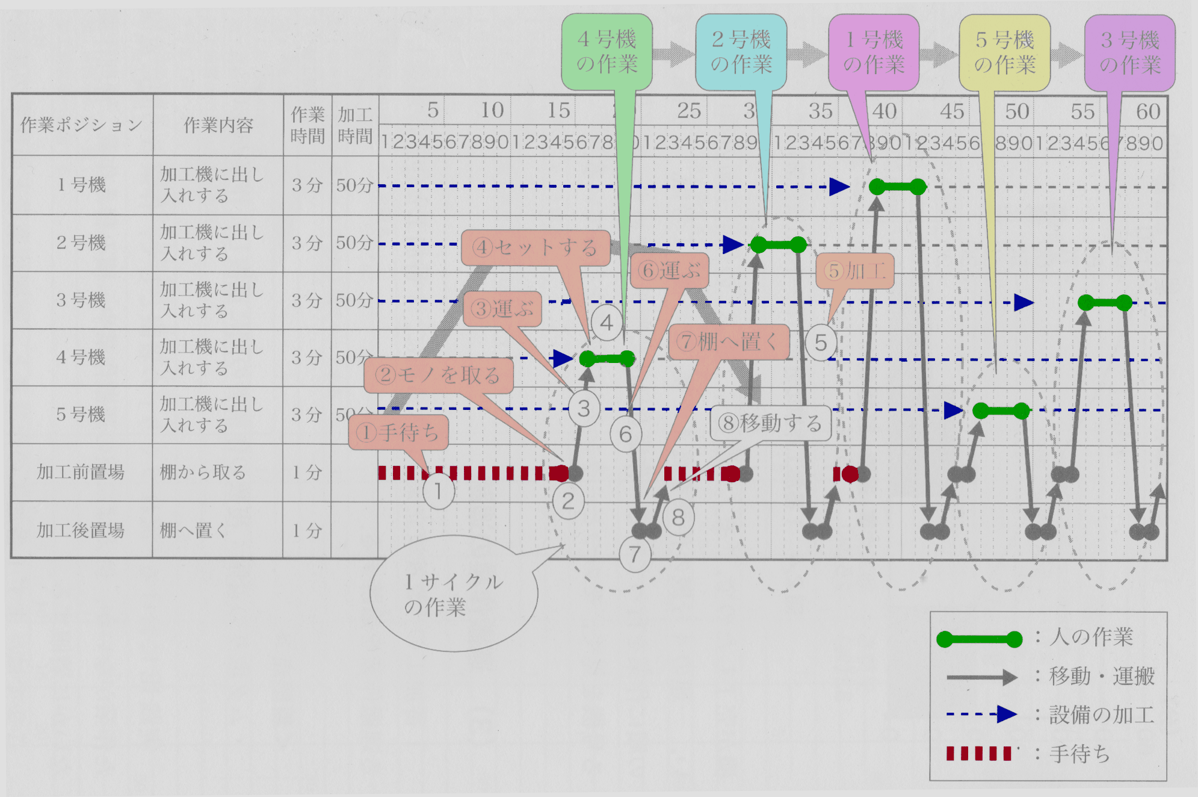
一番加工機の作業組み合わせ表
運搬作業者の作業分析シート
運搬作業者をビデオ撮影して作業分析シートを作成し、パレート図で表した図が下記であり、棚と台車への移し替え作業が半分以上(53%)を占有している。
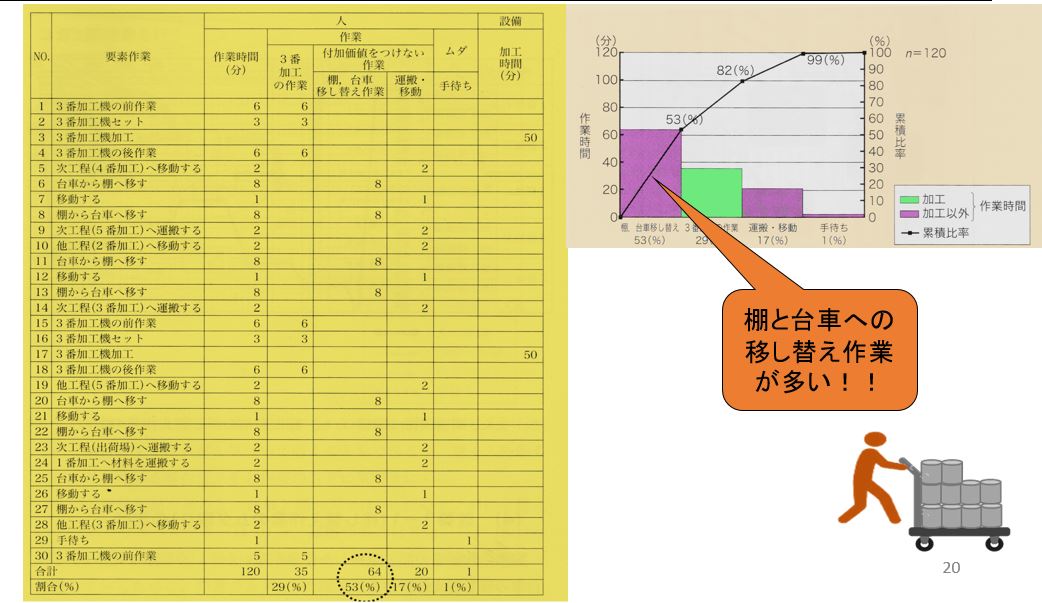
運搬作業者の作業分析シート
作業分析 改善案
作業分析をした結果、次のような6つの改善案が提案された。
①運搬作業の改善⇒移し替え作業のムダ取り
改善1では,在庫数が一目で確認できると理由で以前から設置されていた全加工機の棚を撤去し台車との移し替え作業をなくし,運搬作業者は台車を加工前の置場にそのまま置くように改善した。
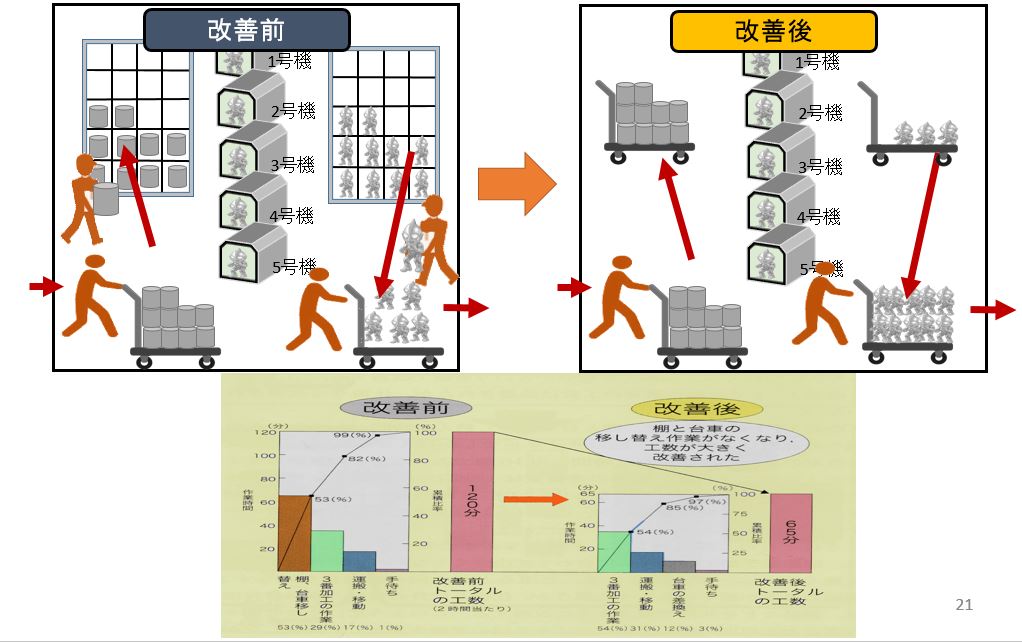
作業改善事例 載せ替え作業 廃止
②リードタイム短縮の改善⇒仕掛品の削減
改善2では1回当たりの運搬量を10個から5個に変更、運搬サイクルは2時間に1回のサイクルから1時間に1のサイクルになるがこの1時間の運搬サイクルにより各台車,置場の量を半減することができる。
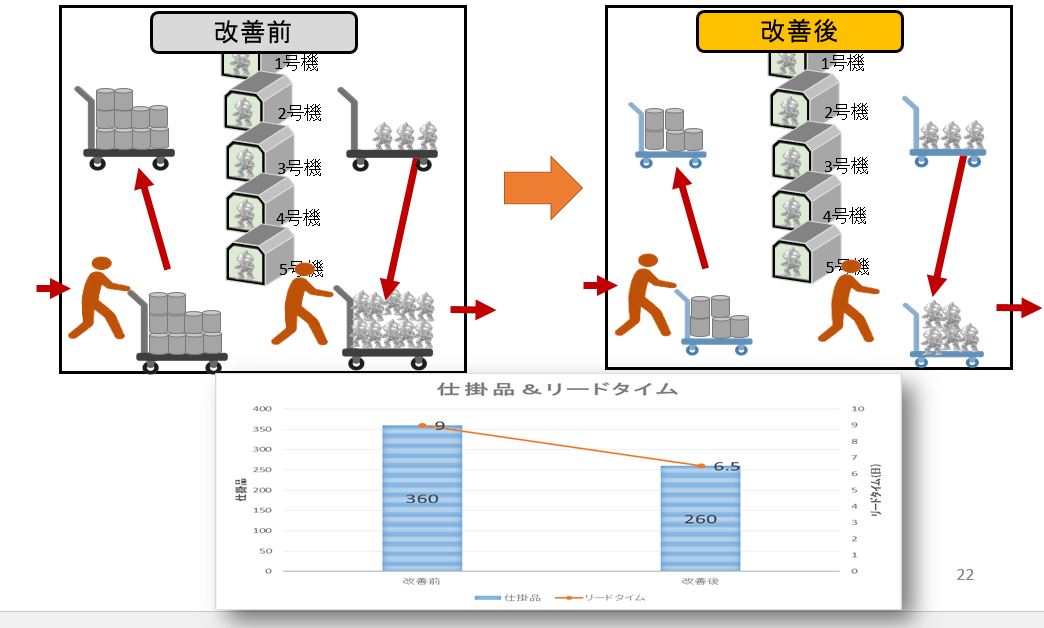
改善事例 仕掛品の削減
ウルトラマン工程のタクトタイム
ウルトラマン工程のタクトタイムは一日の必要台数(営業要望)は40個なので
次式から12分となる。
稼働時間÷必要台数=8時間÷40個=480分÷40個=12分
つまり、一時間当たり5個生産するリズムとなる。
よってウルトラマン工程の作業&運搬のリズムをこのタクトに同期させればムダな作業〔停滞、移動)が解消される。
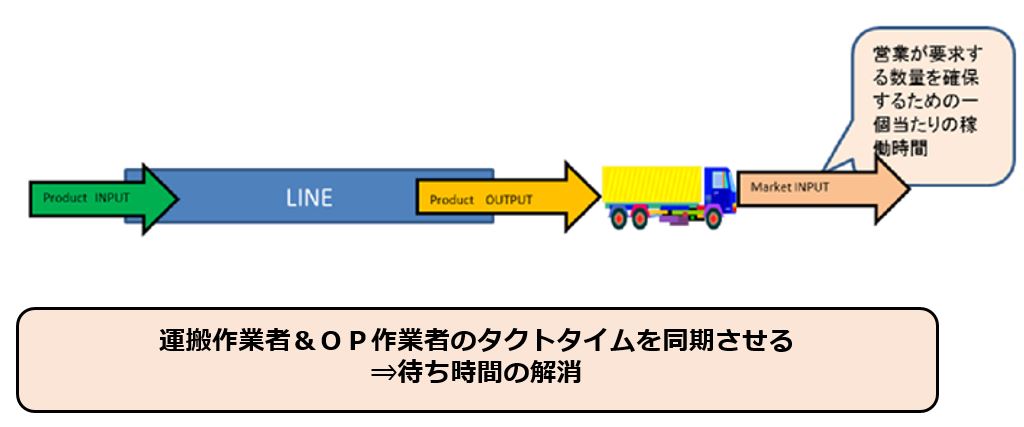
工程のタクトタイム同期化
③運搬作業者の運搬スケジュール改善⇒運搬距離の削減
改善前は運搬作業者は巡回する手順がなく、各加工機で製品が溜まったら運搬していたので運搬時刻、仕掛品が変動しており、運搬距離も変動していた。
改善後はタクトタイムに合わせて運搬経路、時刻を決めたので運搬距離が一定になり
ムダな動きが解消された。
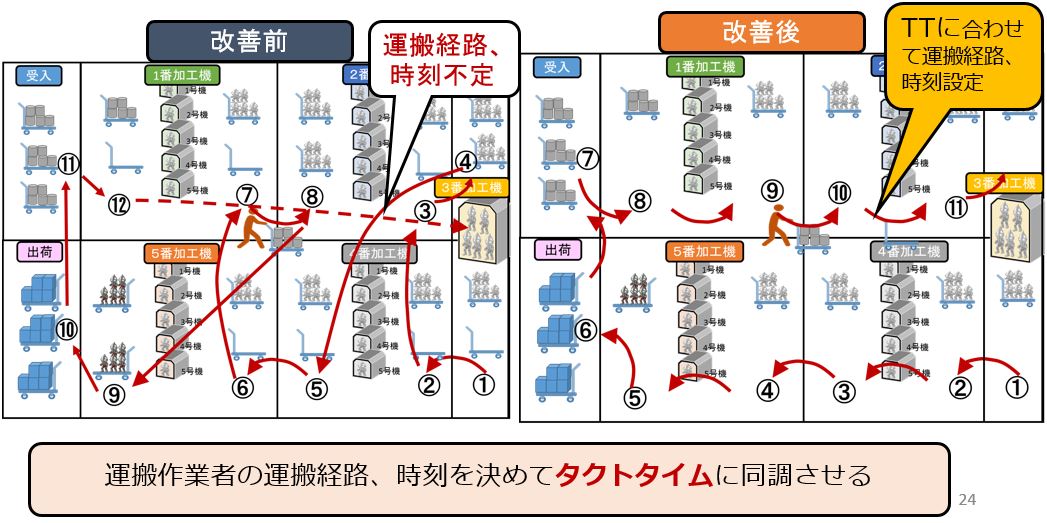
改善事例 タクトタイム同期化
加工機の『作業組み合わせ表』タクトタイムの同期化
改善前は加工機の号機はバラバラに運転しており運搬、OP作業が同期しておらず、バッファーとして余分な仕掛品が必要であったが改善後は一時間一回のサイクルで運搬経路、時刻を決めたので仕掛品が不要になった。更に手待ち時間がまとまったので他の付帯作業が可能になった。
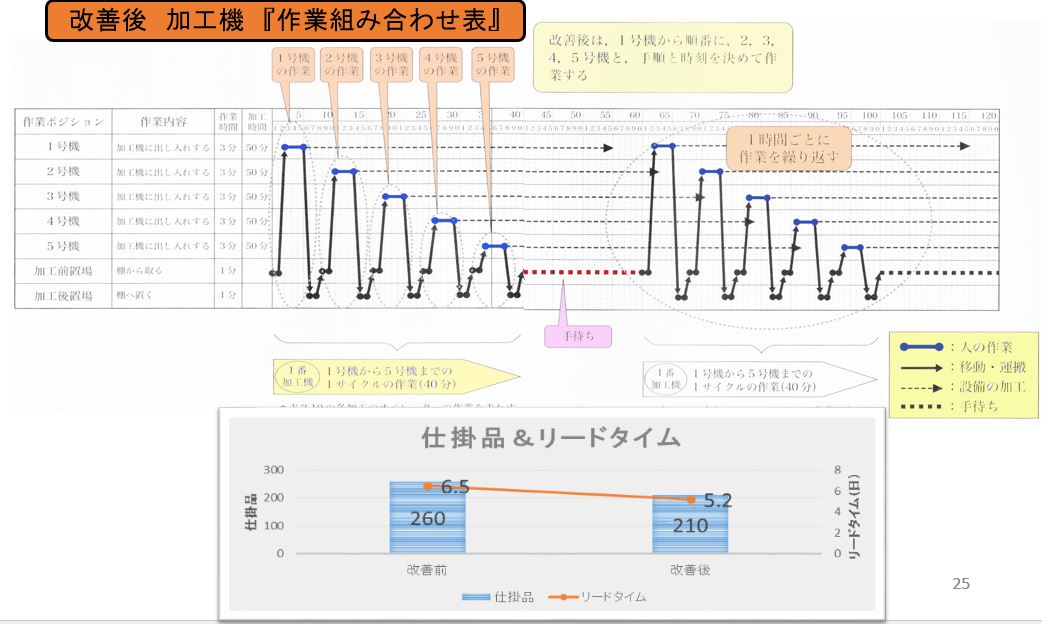
『作業組み合わせ表』タクトタイムの同期化
④工程の整流化 改善
次の改善④として1番~5番の加工機を全て近接させた連結型U字型ラインにレイアウトに変更。
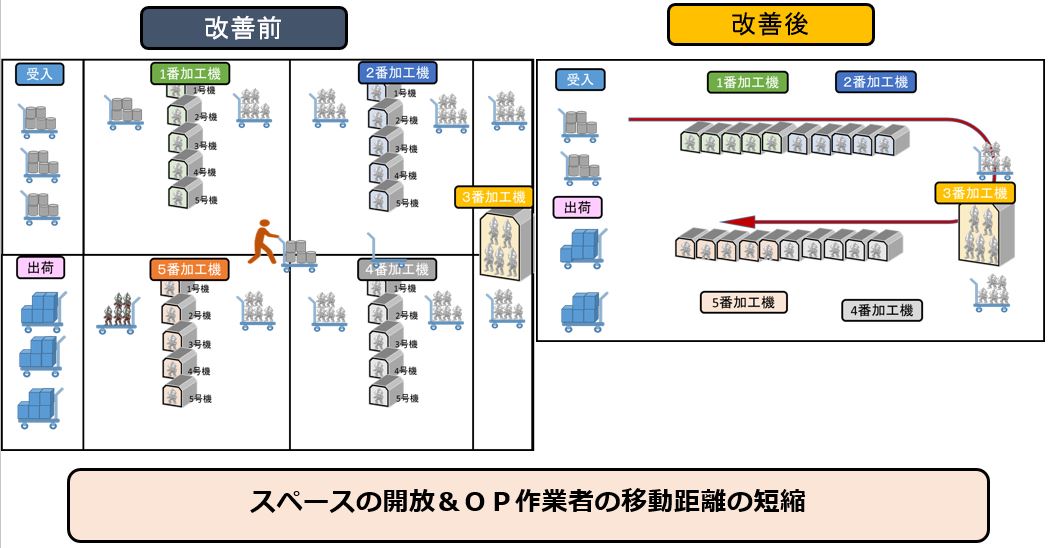
改善事例 工程の整流化
工程の整流化⇒作業者の加工、運搬作業のムダをなくす
A作業者は1番加工機の5台をセッテイング後、台車(5番加工機 加工済み品搭載)をB作業者に受け渡し、同時にB作業者から台車(4番加工機 加工済み品搭載)を受け取って5番加工機の5台をセッテイングする。
次にB作業者はA作業者から台車(1番加工機の加工済み品 搭載)を受け取ってその後、2番加工機(5台)3番加工機(1台)4番加工機(5台)に製品をセッテイングし、最後にA作業者に台車を渡す。
工程の整流化:作業者の具体的な動き&台車の改善
下図に改善案(OPを5人を2人)にした場合の具体的な動きおよび下表に工程連結型ラインのオペレーターの作業手順を示す。
台車も改善し、5個ずつ2工程の仕掛品が一度に搭載できるようにした。
⑤加工機のレイアウト改善
さらにオペレーターの動きを少なくするために,1番加工機と2番加工機,4番加工機と5番加工機を1台ずつ連続して配置した(下図)。
これは少しでも製品の流れの順番に設備を配置することで,製品を直接設備から設備へ運び,台車への出し入れ作業を減らし,生産性を上げる為である。
また,下表に工程連結U字型ラインのオペレーターの作業手順を示す。
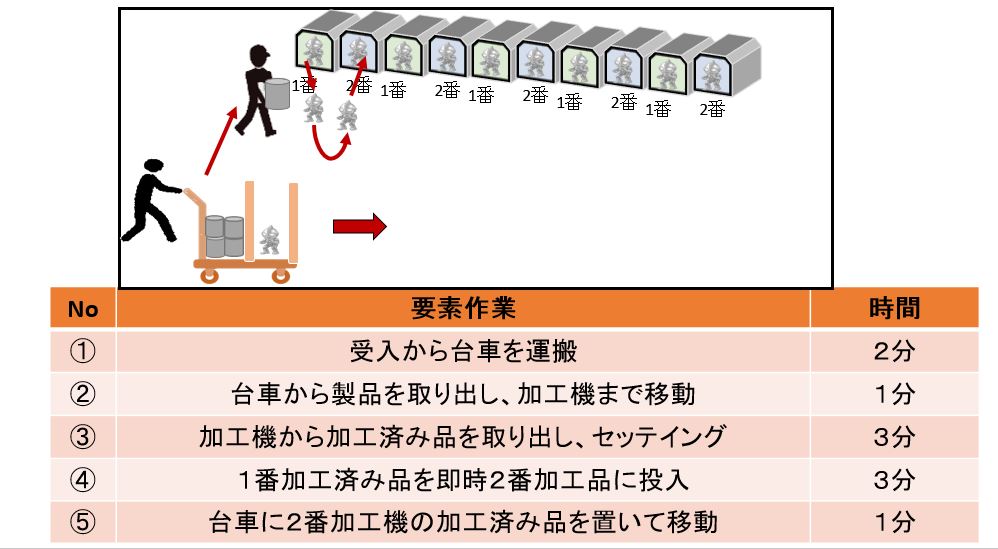
加工機のレイアウト改善事例
6)作業者の多能化 改善:
A作業者の多能工化教育を実施し1番加工から5番加工まですべての加工機を一人で扱うことができるようにする。A作業者は1番加工と2番加工を工程の順に続けて2台を一連の動作で作業を行う。この作業を1~5号機まで5回繰り返し,3番加工機では5個の製品を一括して出し入れ作業を行い,続いて4番加工と5番加工の1号機までを行い,B作業者に台車を受け渡して作業を引き継ぐ。B作業者は,A作業者の残りの作業を担当し,60分の間に23分の作業余裕をつくり,ライン作業とは別の作業を分担させる。
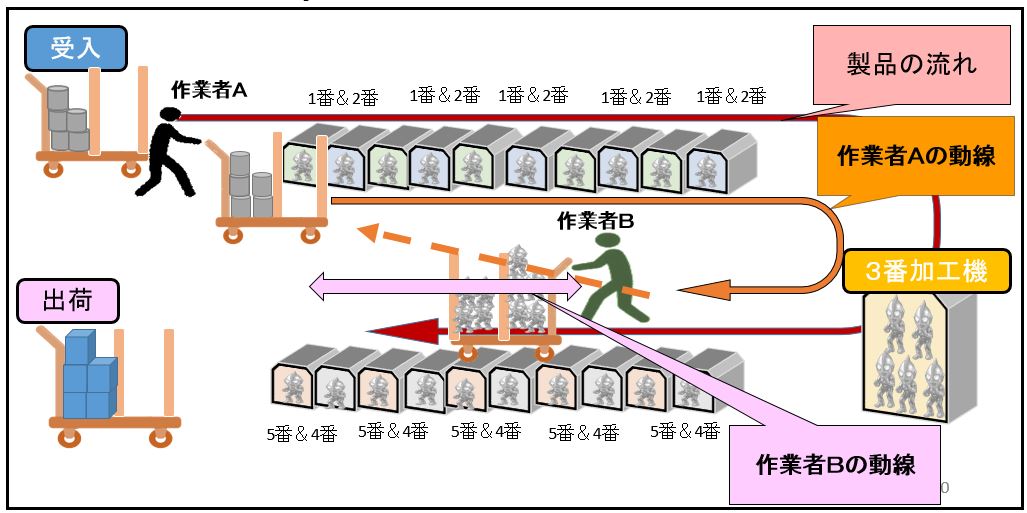
作業者の多能化 改善事例
効果確認:
改善のトータルの成果を振り返ると,改善活動の前は1番加工から5番加工までの作業に5人分の作業工数(1時間のサイクル作業で300分)がかかっていたが改善後は 1.6人分の工数(97分)で同じ仕事ができるように改善された。
仕掛りの改善は改善前の360個から,改善後はわずか55個になった。55個の内訳は,受入出荷場の20個が最も多く,各加工機に仕掛けている25個と2人のオペレーターの台車に積んでいる10個のみとなった。
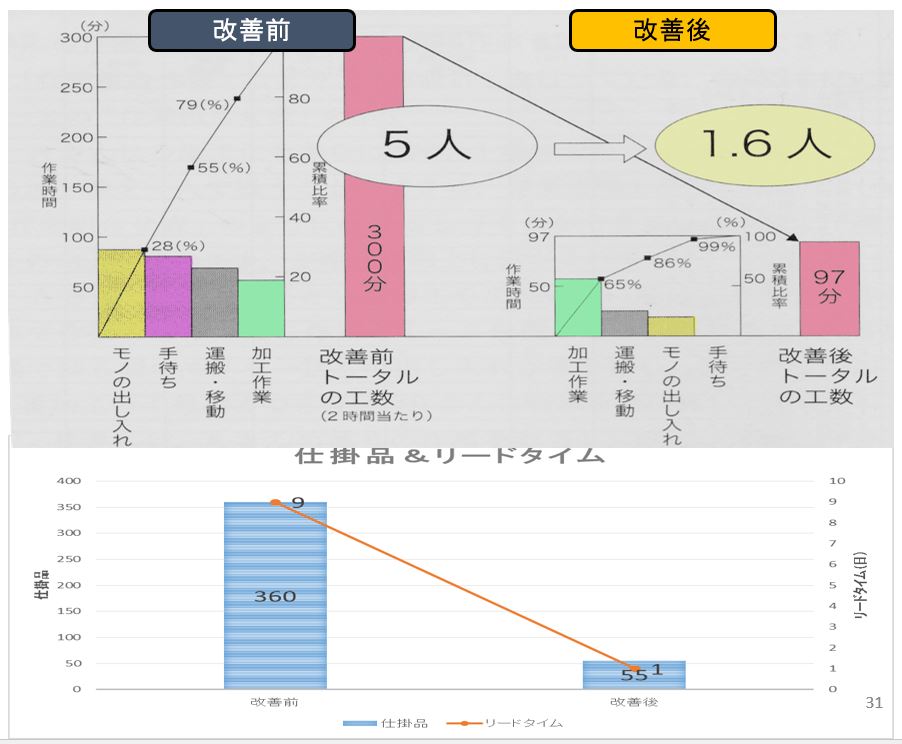
改善効果確認
ケーススタディのまとめ
仕掛品とムダ
リードタイムは部材の投入から製品の出荷までに掛かる時間(期間)である。仕掛りが多ければ,それに比例してリードタイムは長くなる。したがって,仕掛りの量がリードタイムの長さになる.例えば,1時間で5個ずつモノが進むラインで,ラインの仕掛りがトータル50個、あれば10時間のリードタイム, 500個あれば100時間のリードタイムになる。
ウルトラ社の工場の場合、改善前は仕掛品が360個あったが加工中の製品は25個しかなく,したがって,リードタイムで考えると,ほとんどの日数は加工されないまま停滞していることになる。
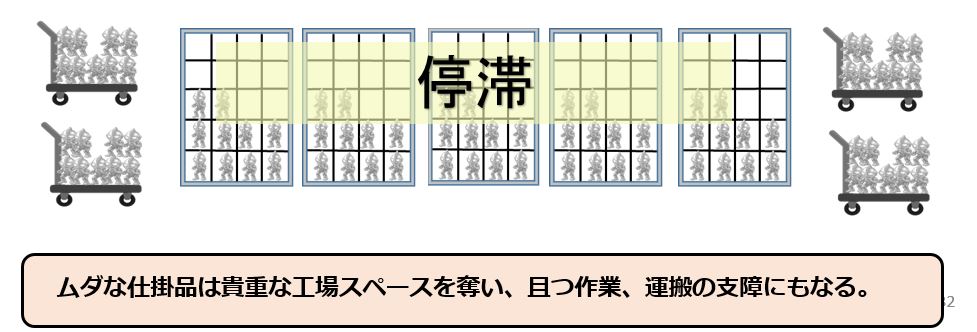
仕掛品の削減改善
付加価値作業とムダ
工場の作業を加工(付加価値作業)とそれ以外の作業(運搬、準備等)に分けて考える、加工は工場の利益を上げる為には必須な作業である、しかしそれ以外の作業(運搬、準備等)は加工作業をサポートする作業であり、可能なら短縮、廃止の改善を検討する。
理想の工場は加工作業だけが可能な限り近接したレイアウトの工程である。
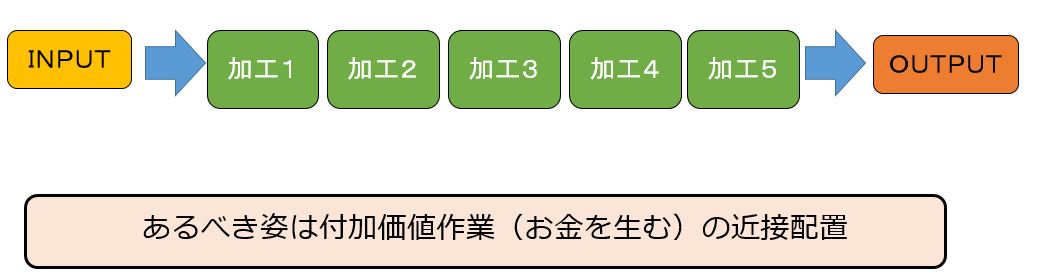
理想の工程レイアウト
リードタイムとコスト
ウルトラ社のお客様の受注が4日間分の製品について確定しているとする。
(4日間までは必ず買っていただける)。
4日間分は100%売り上げになるがその後の受注には変更の可能性があるので,仮に4日以降の3日間は20%の変動リスク(20 %は機種の変更やニーズが変わるなどで,買っていただけない危険度)があるとする。
さらにその後,つまり7日以降は,さらに40%のリスクがあるとする。この変動リスク分は,売れ残りとなる可能性がある。
この売れ残りの製品のために倉庫が必要となり,そのための管理業務も必要となる。最終的に売れ残った製品は陳腐化して廃棄となる場合が多い。仮に売れ残りの半分が廃棄されるとすると,ケーススタディーでは,生産量全体の8%が廃棄されることになる。
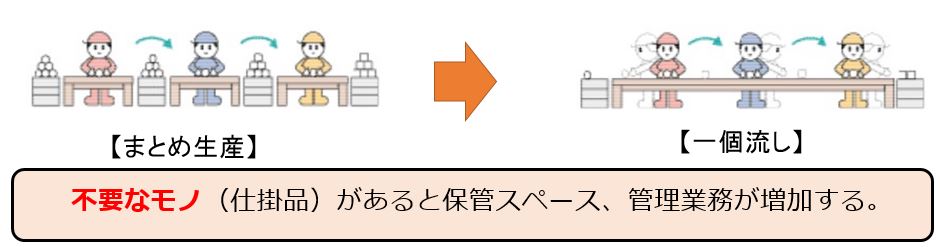
リードタイムとコスト
付加価値作業以外の作業(運搬、準備等)が発生する理由
仕掛品を削減しようとするとその言い訳の理由が色々、でてくる。
例えば設備のチョコ停、トラブル多発、部品の供給不安定、工程間の同期ずれ等
しかし、これらの問題を永久的に仕掛品で解決させてはいけない。
真の問題を早急に解消して仕掛品がなくても円滑に生産できる工場にしなければならない、逆に言うと仕掛品を削減すると真の問題点が見えてくる。
時刻表を見てバス停にいけば待たずに乗れるが行き当たりばったりでは待機時間が発生する。又 通常、人の会う時、時間を指定するがモノを製造する際は正確に各作業間、工程間の同期化をさせてないで生産を行い、多くの仕掛品を滞留させている工場が良く見られる。
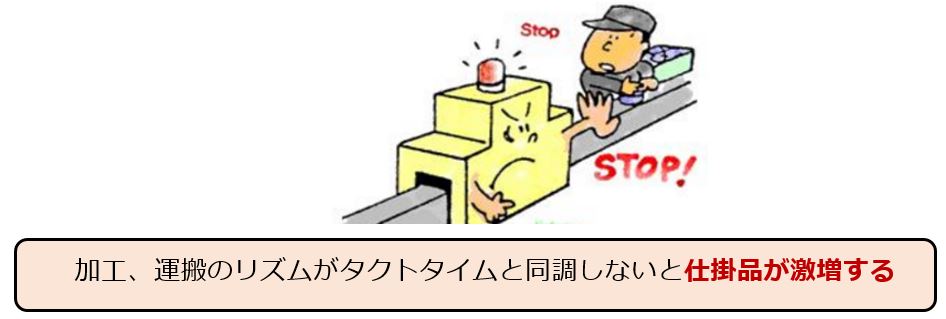
作業、工程間のタクトタイム同期化
Slideshare 無料 ダウンロード資料
参考文献:
実践IEの進め方 著者:香川博昭
IE 七つ道具 著者:実践経営研究会
よくわかるIE 七つ道具 著者: 藤井春雄
;
コメント