作業分析の基礎
IE手法とは?
IEとは、端的に言うとモノづくりにおける3ム(ムダ・ムラ・ムリ)を改善(排除)すること。この中でとくに重要なことはムダに対する考え方であり、その分析と改善の仕方である。
具体的には機械が加工(切削)しているが、1回で削れるのに2回で削るムダ。
スピード100 cm/分送りのところを80 cm/分送りするムダなどがある。
付随・付帯作業では、型替え、脱着、検査などに多くの時間を要するムダ。余裕では、作業者の離席(用達・打合せ・探し)によるムダなどが発生している。
IE手法では仕事そのものを工程の流れ(工程分析・動作研究)と、時間の流れ(稼働分析・時間研究)の面から分析し、そのムダ取りをする。
IEは米国で大規模な生産革新が求められた1900年代初めに理論化され、作業の基本となるF動作研究」をF・B・ギルブレスが、「時間研究」をF・W・テーラーが行った。そしてF・W・テーラーにより1909年に「科学的管理法の原理」が発表された。
日本でこのIEの基本(動作・時間研究)を忠実に実行し、さらに工夫・発展させたのが、トヨタ生産方式:TPS(Toyota Production System) をつくった大野耐一氏である。
IE手法は、英語ではIndustrial Engineering techniques、中国語では工業工程技術(gōngyè gōngchéng jìshù)と訳されます。
関連記事:IE手法とは?
作業動線とは?
「動線図」とはレイアウトにモノや人の動線(モノや人が動く経路を示す線)を描き込む分析図である。作業動線図とも呼ぶ。活動の対象とする職場やライン,フロアーのモノの流れや人の動きを,自分の手で描く。
「動線図」を描くためにまずレイアウトを描いていく。フロアーのどこに何かあるのか,柱の位置はどこか,又、設備が何台あるのか,号機の位置を確認する。さらに作業者の配置も描き込む。
大まかなレイアウトができたら,作業者が運ぶモノの流れをそのままどの場所からどの場所へ動くかという動線を描き込む。製品の種類ごとに違う場合は色別に描いても良い。
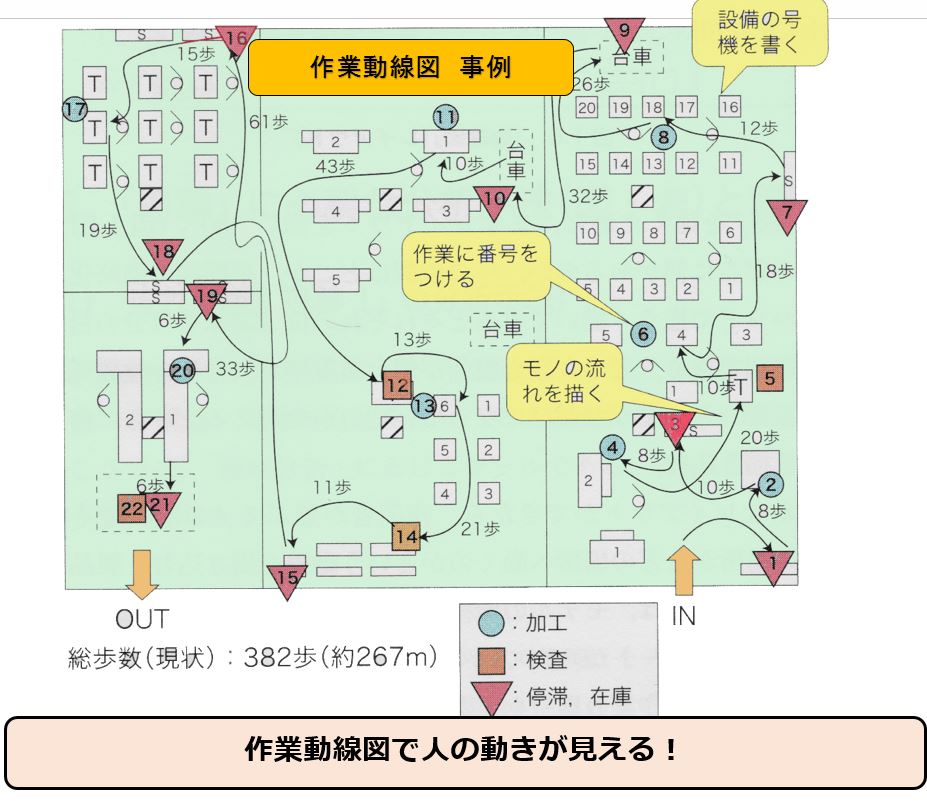
作業動線図とは?
流れ図とは?
流れ図、フローチャート (flowchart) は、プロセスの各ステップを箱で表し、流れをそれらの箱の間の矢印で表すことでプロセスを表現する図である。
流れ図はフリーフォーマットで,メンバーが理解しやすく描き、最初に「流れ図」を描くときは,現状把握として現状を描き、改善が進んだ後は目標とする“めざす姿を描く。
「流れ図」に描く内容を次にあげる。
① モノの加工,検査,作業台などの作業ポイント及び,棚台車による待機,置場などのストックポイント。
② 作業ポイントとストックポイント間のモノの流れ。
③ ポイント間の運搬のタイミング(運搬頻度,運搬の単位など)。
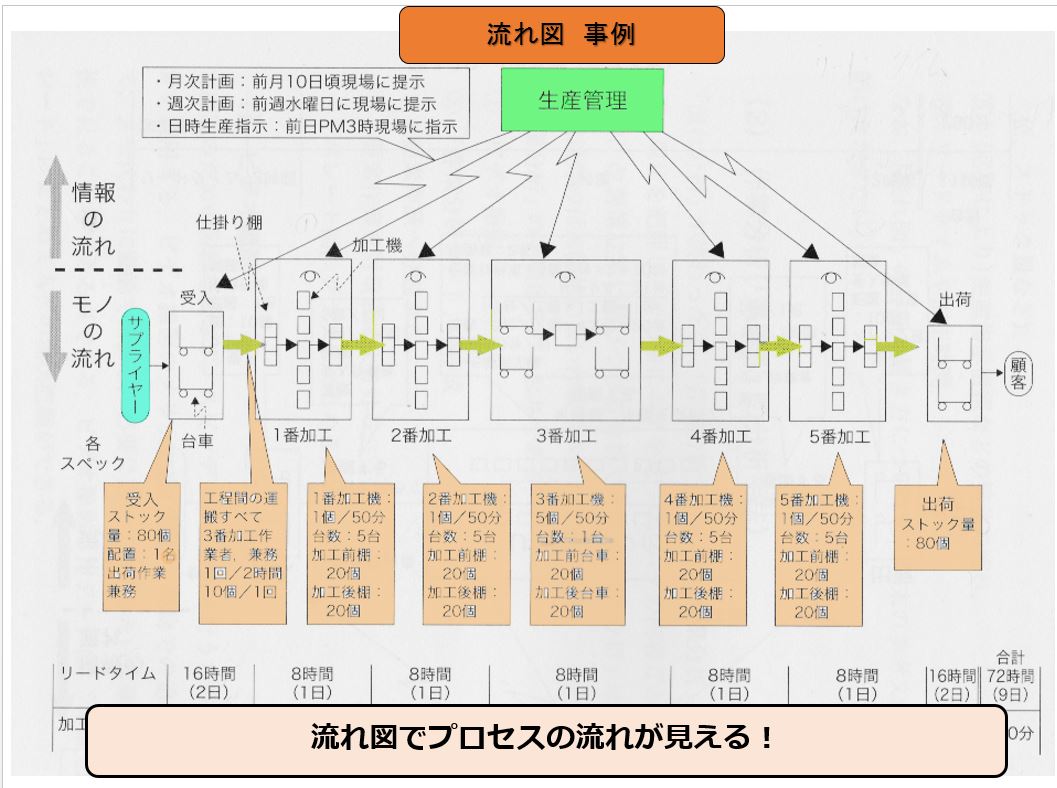
流れ図とは?
作業分析シートとは?
ビデオ撮影したデータをもとに「作業分析」を行い、「作業分析」においては,付加価値作業とその他の付加価値をつけない作業,及びムダに仕分けることが重要であり、仕分けをするためのツールとして「作業分析シート」を作成する。
「作業分析シート」では,人の作業を要素作業に分けて,付加価値作業とそれ以外に仕分ける。この要素作業とは,改善の対象とする作業において,それ以上分割しても改善の検討が行えない最小単位の作業のことである。
したがって,各改善の検討レベルにおいて要素作業の単位が変わることもあるが,データの分析をスピーディーに行うためには,必要以上に細かく要素作業を分割せず,改善の検討レベルにより,要素の大きさを明確にして行うことがポイントである.例えば,運搬,移動,加工などの同じ作業と考えられる動作を動作ごとに,ひとかたまりの要素作業と捉えて分割する。
付加価値作業以外のものには,明らかなムダと付加価値をつけない作業とがあるが,付加価値をつけない作業も,さらに対策や改善のねらい。
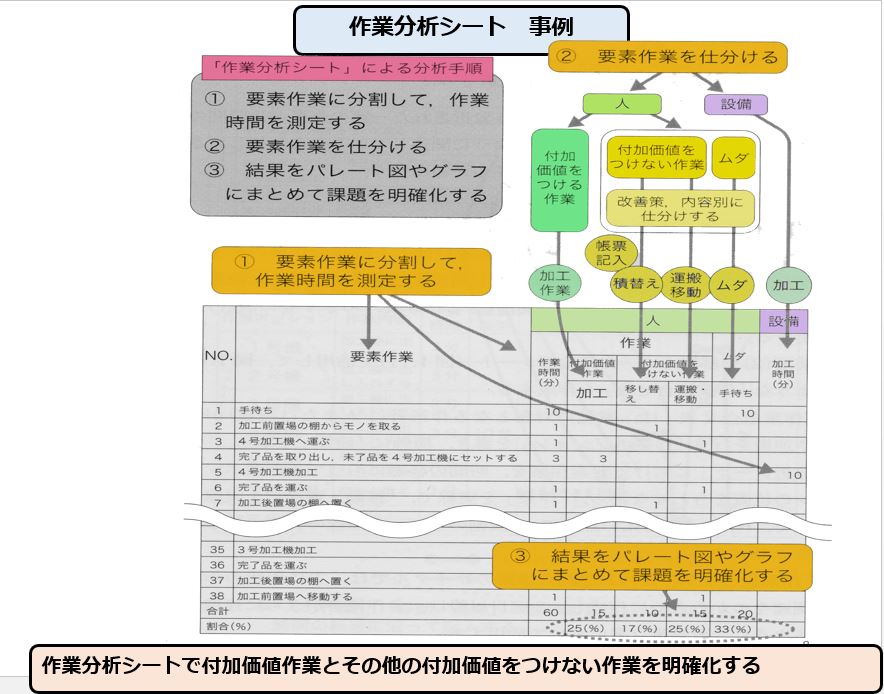
作業分析シート 事例
作業組合せ表とは?
1)「作業組合せ表」により,人と人,あるいは人と設備の作業のタイミングを分析し,作業の組合せや繰り返し精度を改善する。
「作業分析シート」を使用して「作業組合せ表」を作成する。
「作業組合せ表」は,縦軸に対象となる作業者(1人または複数)が作業や運搬を行う「作業ポジション」を書き,横軸に「時間」を取る。
「作業分析シート」における要素作業を,時間の経過に沿って,作業ポジションの位置を合わせながら「作業」を実線で,「移動・運搬」を実線の矢印で,「手待ち」を太い点線で「設備の加工」を点線の矢印で表しながらつないでいく。
「作業組合せ表」は,1巡目の追跡のサイクルでは,主に現状の作業の関連をつかむために作成し,2巡目以降は,各作業者がさらに連携できるように,改善策立案において活用する。
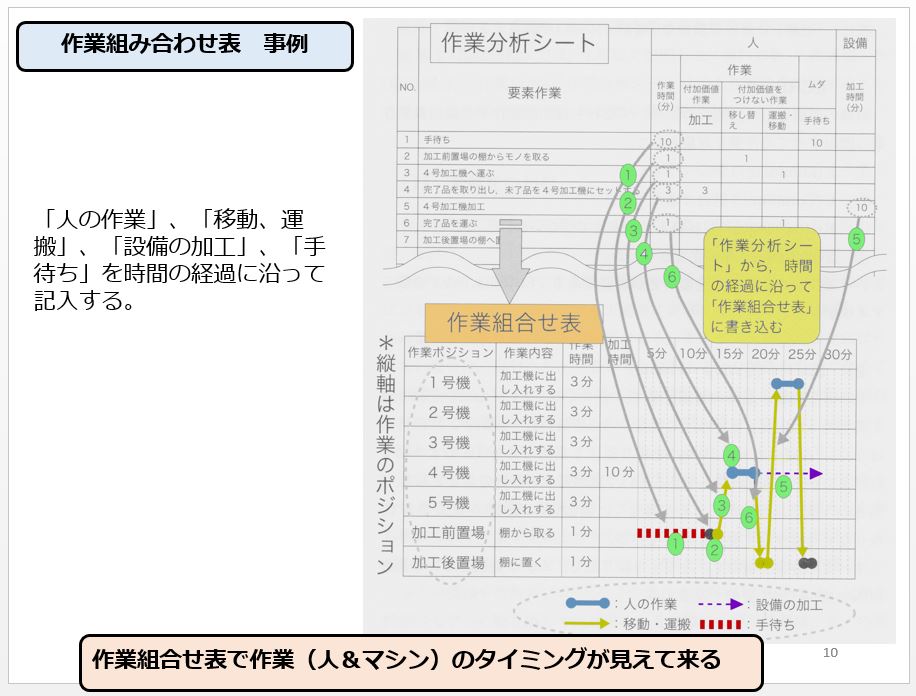
作業組み合わせ表 事例
工程の整流化とは?
「整流化」とは,ジョブショップの工程ごとのフロアー配置からフローショップの機種ごとの工程順配置に変えることを指す(下図)。
「整流化」のねらいは,工程の壁を取り,工程を連結して付加価値作業を最短でつなげることである。作業者には多能工化が要求され作業者レベル向上につながる。
製造業の生産工程や流通業の物流などにおいては製品、情報が入り乱れたり、途中で滞留逆流しムダが発生します、それを整流化によって定められた順序で工程を流れるようにします。
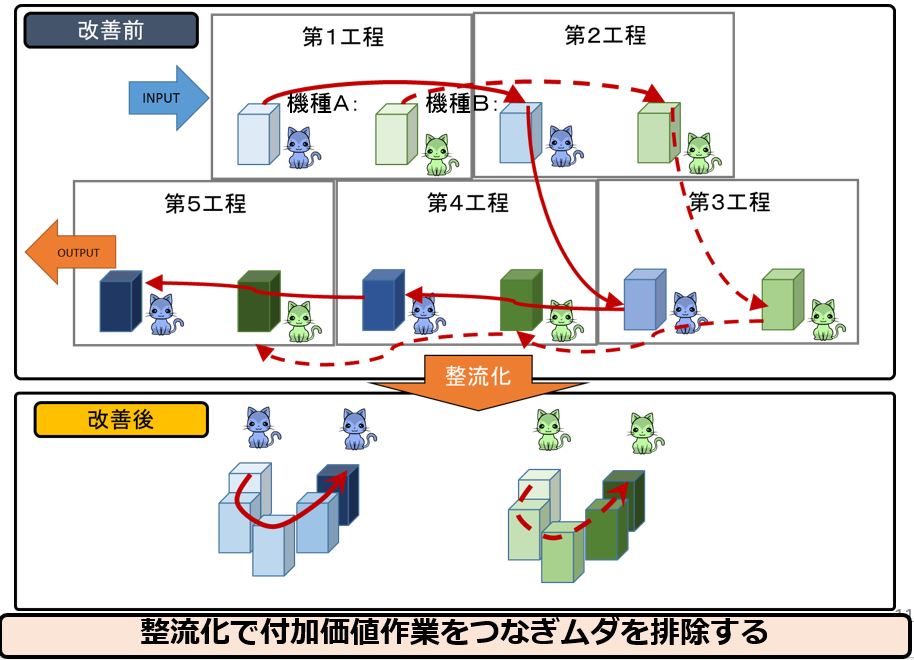
整流化とは
IE分析事例~作業分析 ケーススタディー
ある工場の工程の作業分析事例を基にIE手法を学ぶ。
ケーススタディ工場の概要
ウルトラ社は材料を加工し,ウルトラマンの人形を作る工場である(下図)。
材料を受入から投入し,1番,2番と加工を行うことにより,工程が進行していき,5番の加工を終えると最終製品が完成する、 各工程の加工機は基本的に製品を1個ずつ加工するが3番加工機は5個を一括して(5個を1バッチとして)加工する加工機である。
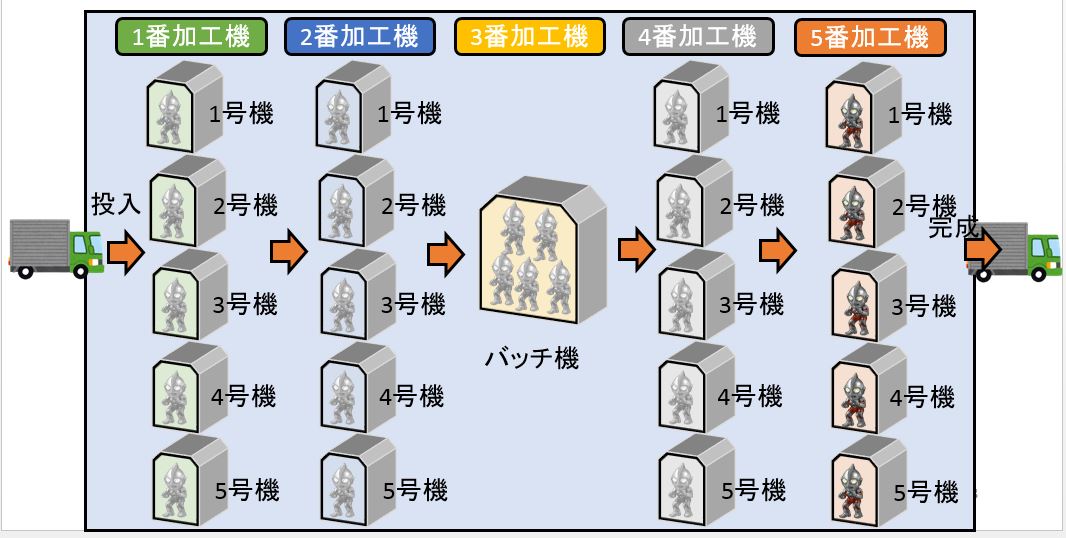
事例工場の概要
下記は工場のレイアウトと運搬者&オペレーターの動線図である。
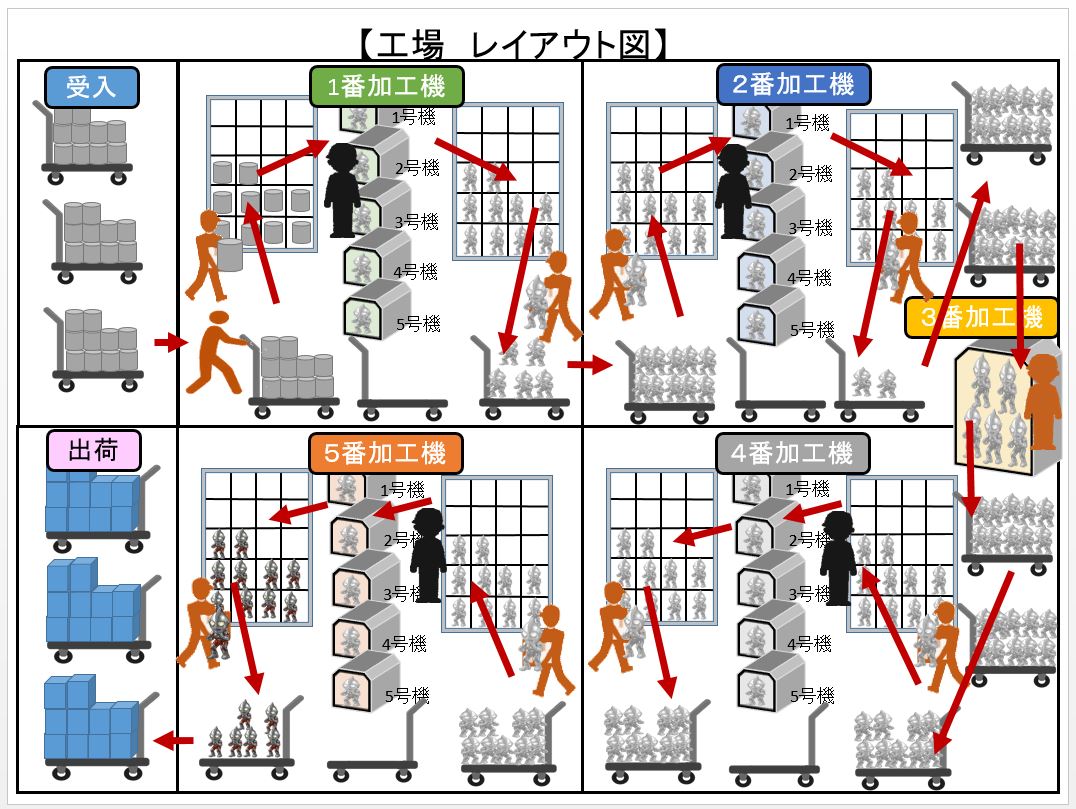
工場レイアウト&動線図
又、オペレーター&運搬車の動きがわかりやすいように分けて描いたモノが下記の図である。
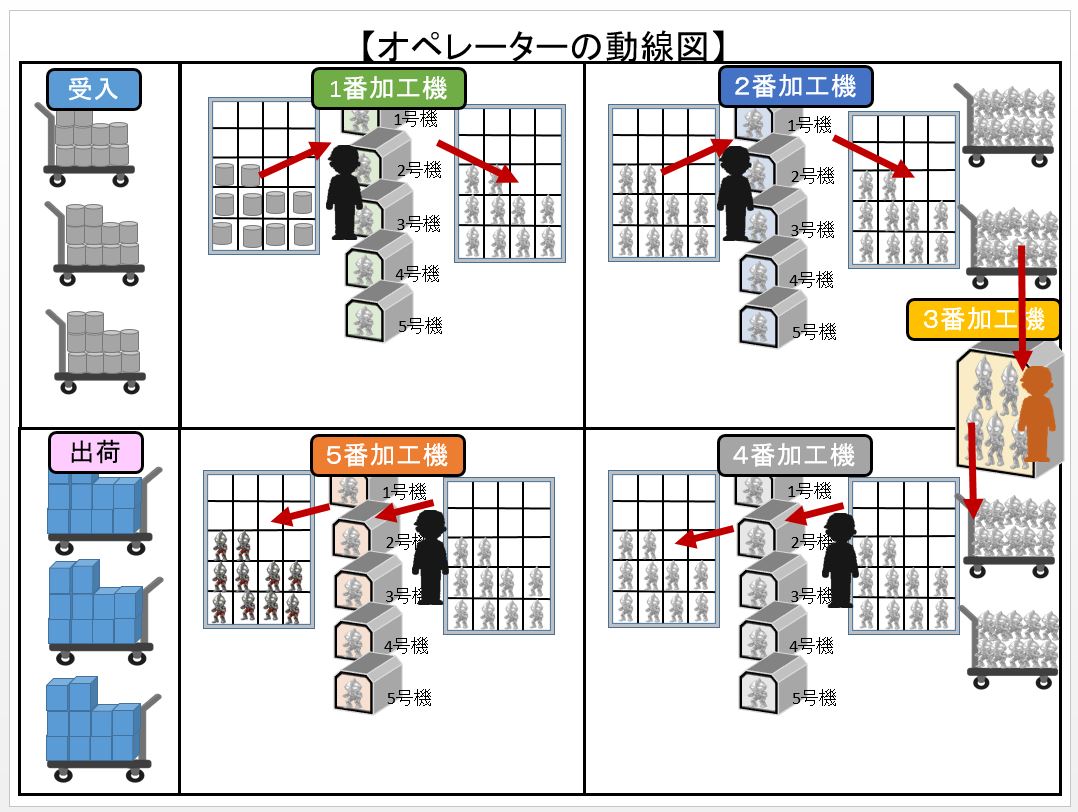
オペレーターの動線図
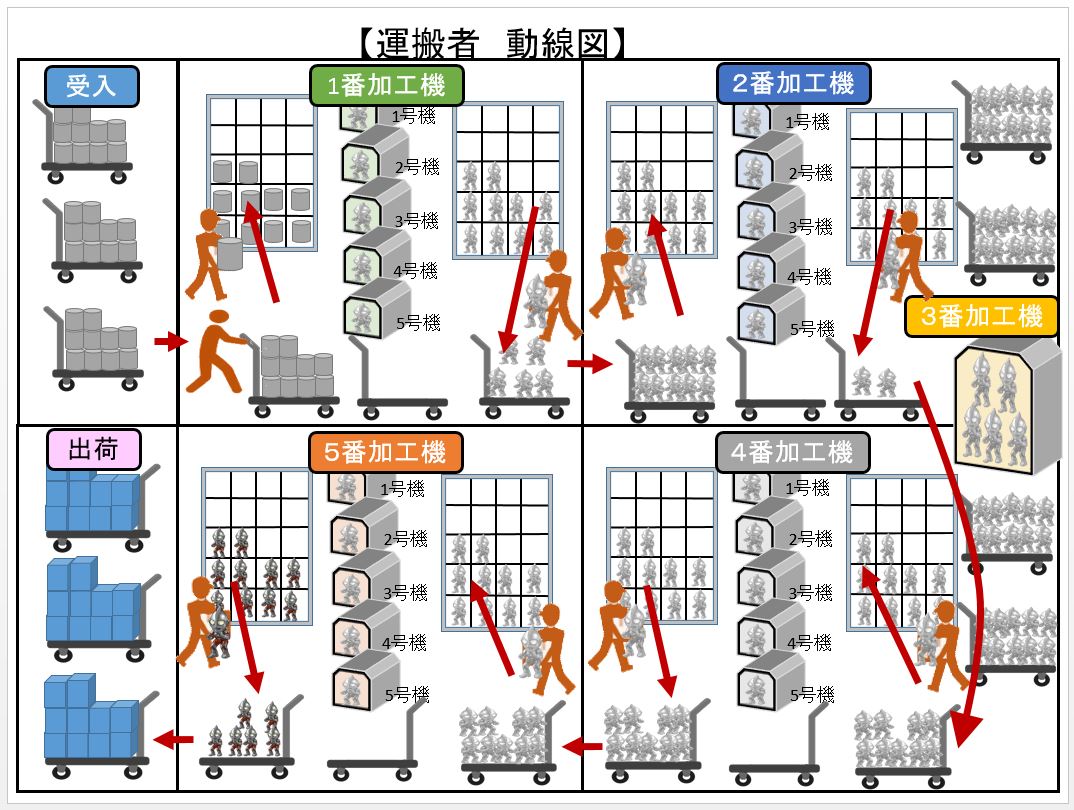
運搬者の動線
現状把握&分析:
1番加工機のオペレター作業
オペレーターは下記の手順で1号機~5号機を巡回し、停止したマシンごとに順に作業を実施。
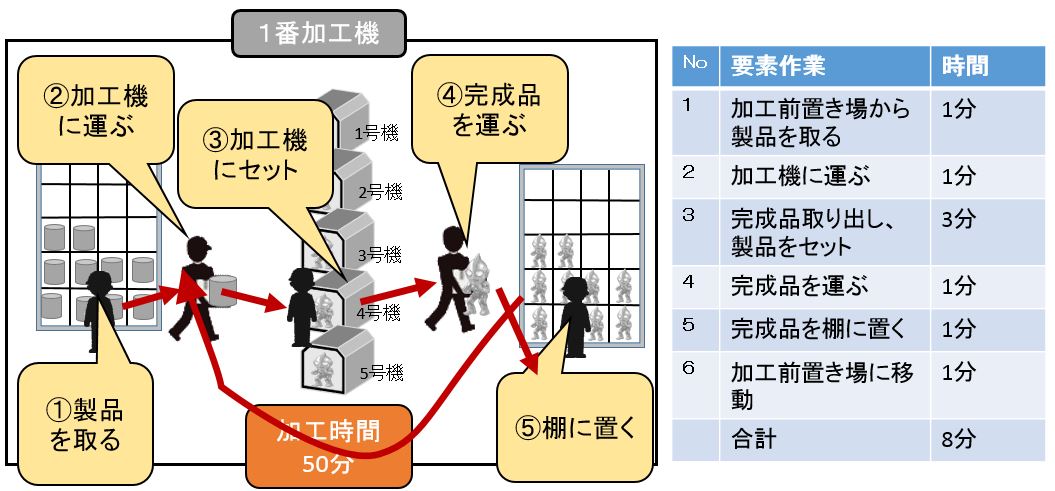
1番加工機の動線
1番加工作業の作業分析シート
1番加工作業をビデオ撮影して作業分析シートを作成し、次に内訳を分かり易くする為にパレート図で表した図が下記であり、加工時間より手待ち時間が多い。
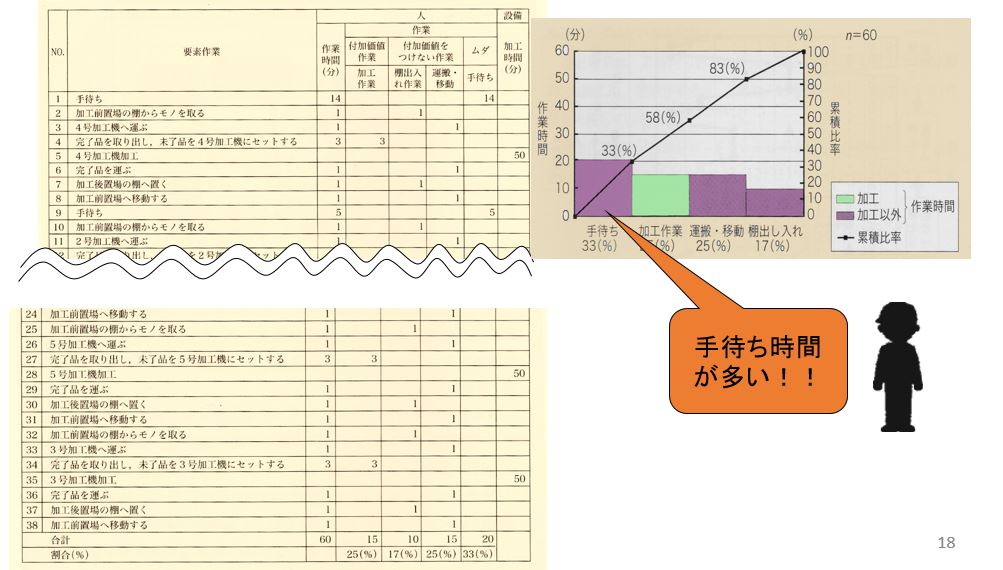
一番加工機の作業分析シート
1番加工作業の「組み合わせ表」
次に作業分析シートから1番加工作業の「組み合わせ表」を作成し、作業に手順、繰り返しを検討して改善を進める。
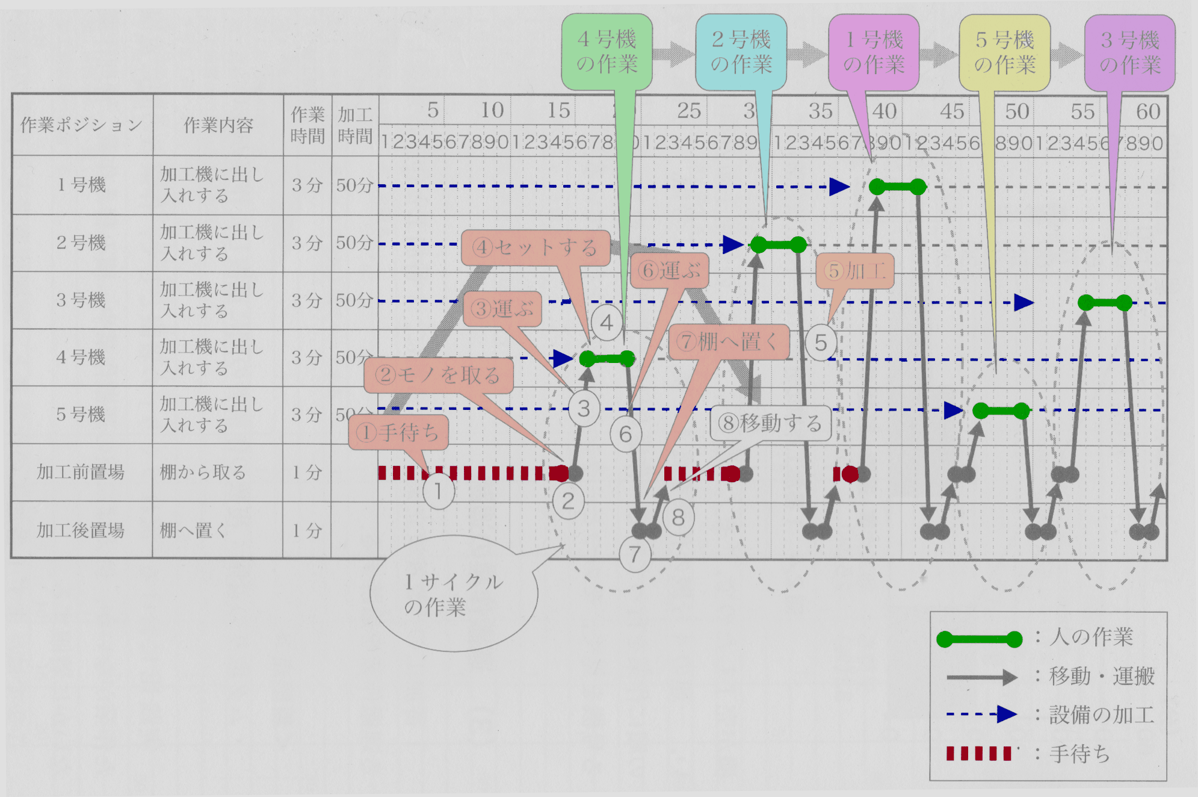
一番加工機の作業組み合わせ表
運搬作業者の作業分析シート
運搬作業者をビデオ撮影して作業分析シートを作成し、パレート図で表した図が下記であり、棚と台車への移し替え作業が半分以上(53%)を占有している。
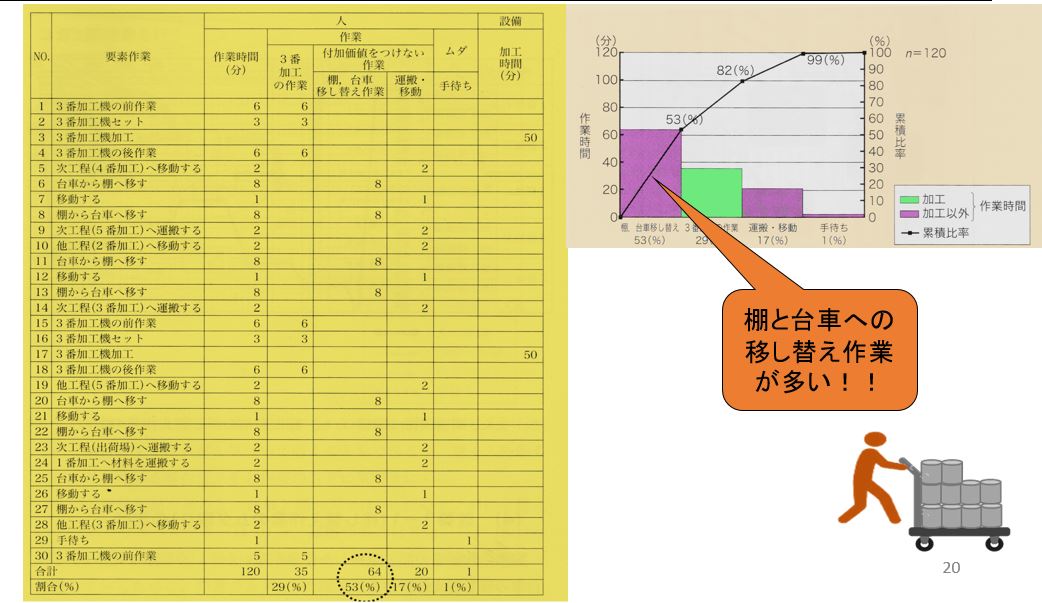
運搬作業者の作業分析シート
作業分析 改善案
作業分析をした結果、次のような6つの改善案が提案された。
①運搬作業の改善⇒移し替え作業のムダ取り
改善1では,在庫数が一目で確認できると理由で以前から設置されていた全加工機の棚を撤去し台車との移し替え作業をなくし,運搬作業者は台車を加工前の置場にそのまま置くように改善した。
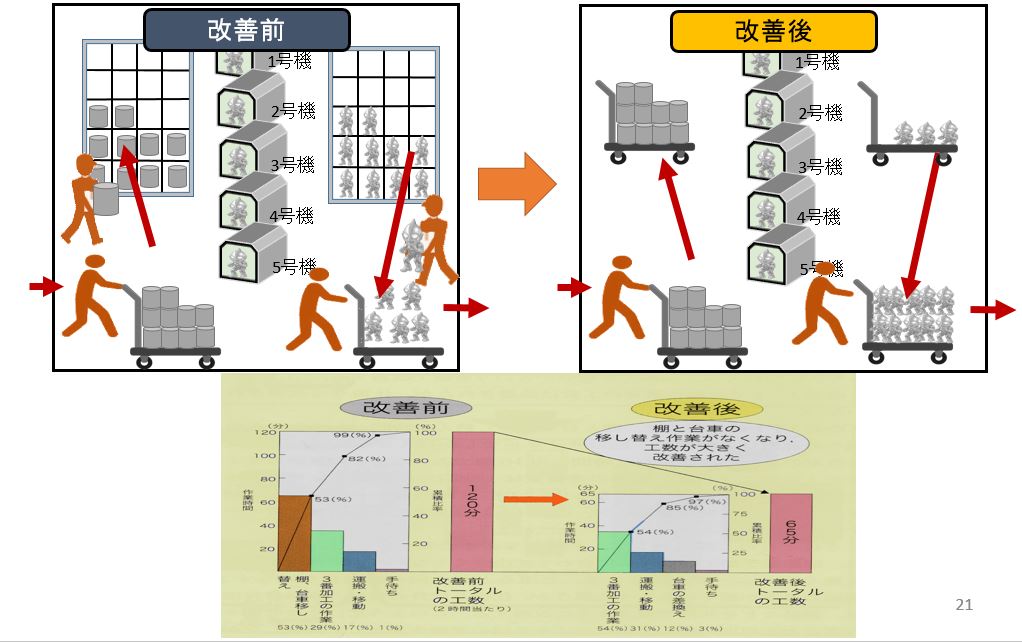
作業改善事例 載せ替え作業 廃止
②リードタイム短縮の改善⇒仕掛品の削減
改善2では1回当たりの運搬量を10個から5個に変更、運搬サイクルは2時間に1回のサイクルから1時間に1のサイクルになるがこの1時間の運搬サイクルにより各台車,置場の量を半減することができる。
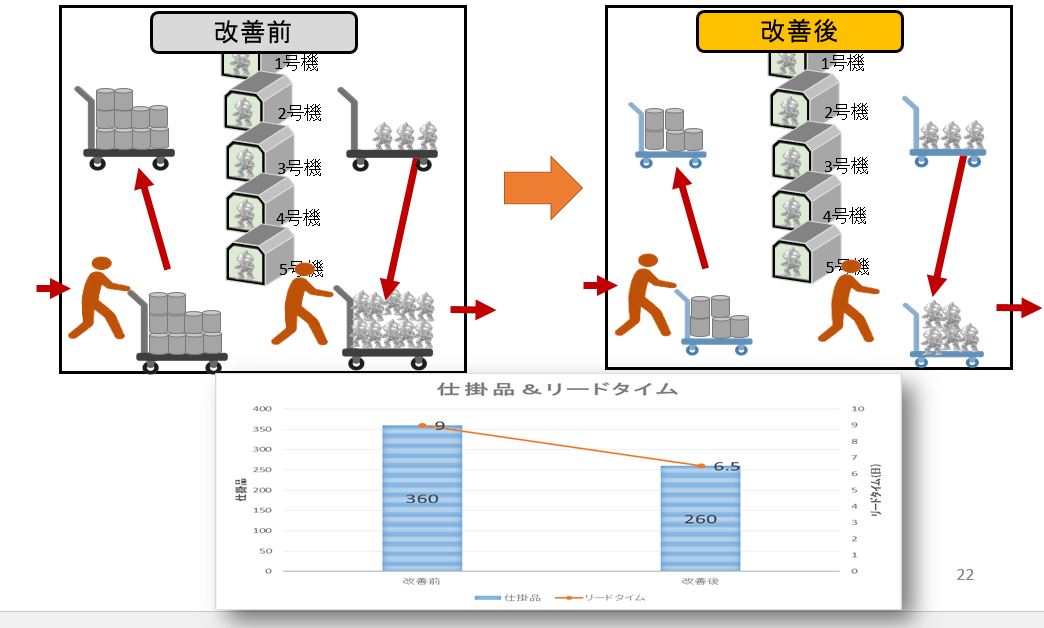
改善事例 仕掛品の削減
ウルトラマン工程のタクトタイム
ウルトラマン工程のタクトタイムは一日の必要台数(営業要望)は40個なので
次式から12分となる。
稼働時間÷必要台数=8時間÷40個=480分÷40個=12分
つまり、一時間当たり5個生産するリズムとなる。
よってウルトラマン工程の作業&運搬のリズムをこのタクトに同期させればムダな作業〔停滞、移動)が解消される。
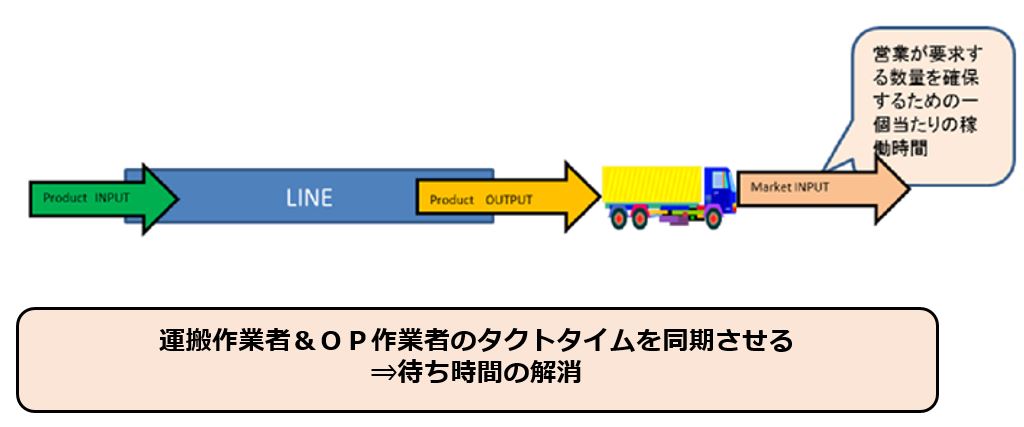
工程のタクトタイム同期化
③運搬作業者の運搬スケジュール改善⇒運搬距離の削減
改善前は運搬作業者は巡回する手順がなく、各加工機で製品が溜まったら運搬していたので運搬時刻、仕掛品が変動しており、運搬距離も変動していた。
改善後はタクトタイムに合わせて運搬経路、時刻を決めたので運搬距離が一定になり
ムダな動きが解消された。
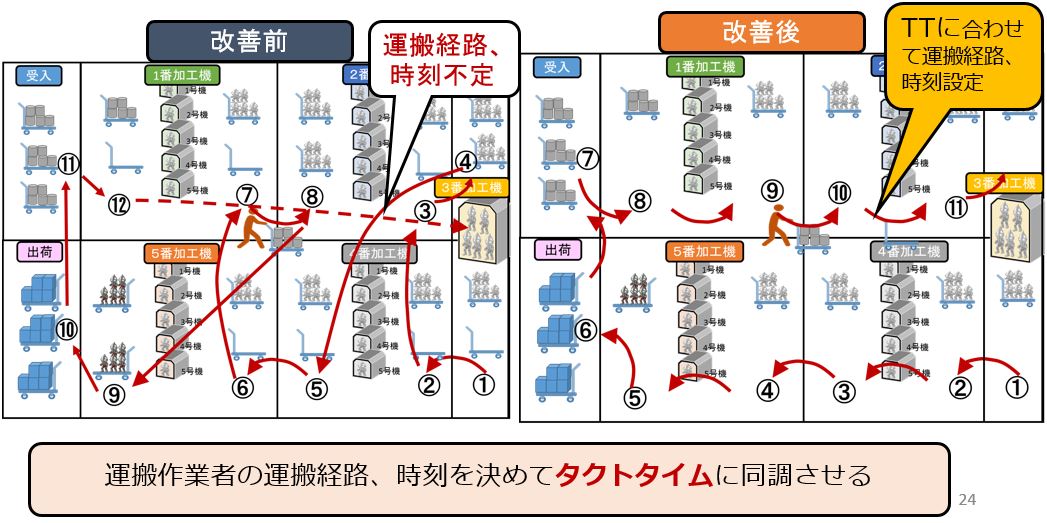
改善事例 タクトタイム同期化
加工機の『作業組み合わせ表』タクトタイムの同期化
改善前は加工機の号機はバラバラに運転しており運搬、OP作業が同期しておらず、バッファーとして余分な仕掛品が必要であったが改善後は一時間一回のサイクルで運搬経路、時刻を決めたので仕掛品が不要になった。更に手待ち時間がまとまったので他の付帯作業が可能になった。
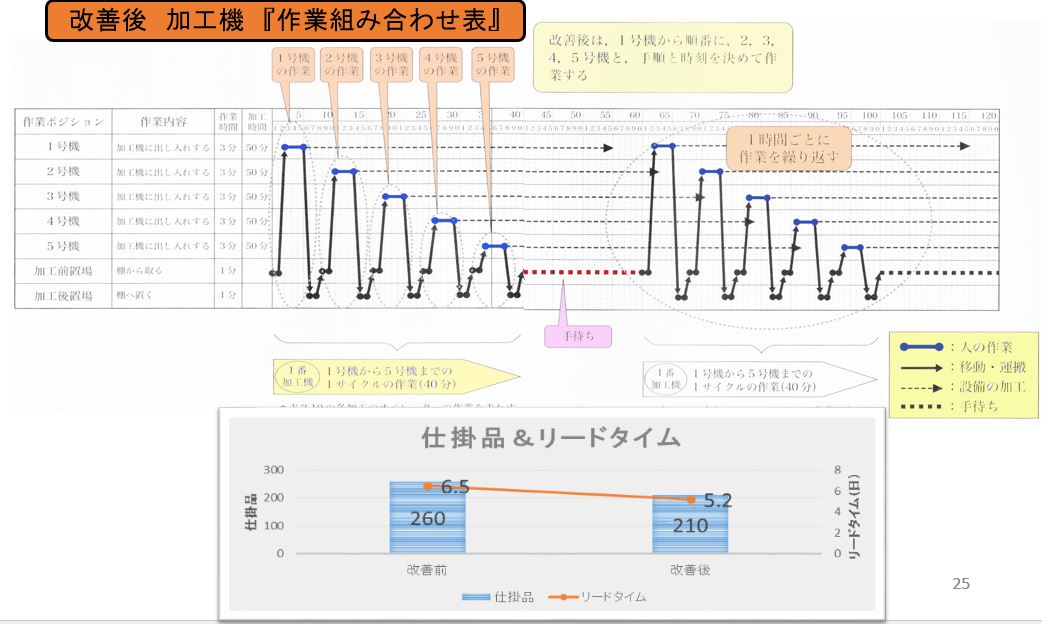
『作業組み合わせ表』タクトタイムの同期化
④工程の整流化 改善
次の改善④として1番~5番の加工機を全て近接させた連結型U字型ラインにレイアウトに変更。
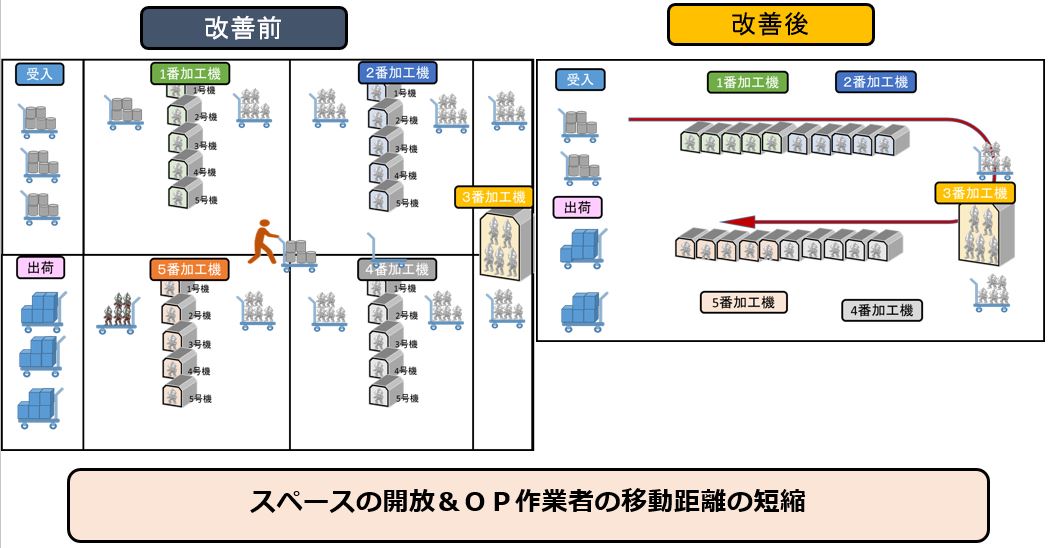
改善事例 工程の整流化
工程の整流化⇒作業者の加工、運搬作業のムダをなくす
A作業者は1番加工機の5台をセッテイング後、台車(5番加工機 加工済み品搭載)をB作業者に受け渡し、同時にB作業者から台車(4番加工機 加工済み品搭載)を受け取って5番加工機の5台をセッテイングする。
次にB作業者はA作業者から台車(1番加工機の加工済み品 搭載)を受け取ってその後、2番加工機(5台)3番加工機(1台)4番加工機(5台)に製品をセッテイングし、最後にA作業者に台車を渡す。
工程の整流化:作業者の具体的な動き&台車の改善
下図に改善案(OPを5人を2人)にした場合の具体的な動きおよび下表に工程連結型ラインのオペレーターの作業手順を示す。
台車も改善し、5個ずつ2工程の仕掛品が一度に搭載できるようにした。
⑤加工機のレイアウト改善
さらにオペレーターの動きを少なくするために,1番加工機と2番加工機,4番加工機と5番加工機を1台ずつ連続して配置した(下図)。
これは少しでも製品の流れの順番に設備を配置することで,製品を直接設備から設備へ運び,台車への出し入れ作業を減らし,生産性を上げる為である。
また,下表に工程連結U字型ラインのオペレーターの作業手順を示す。
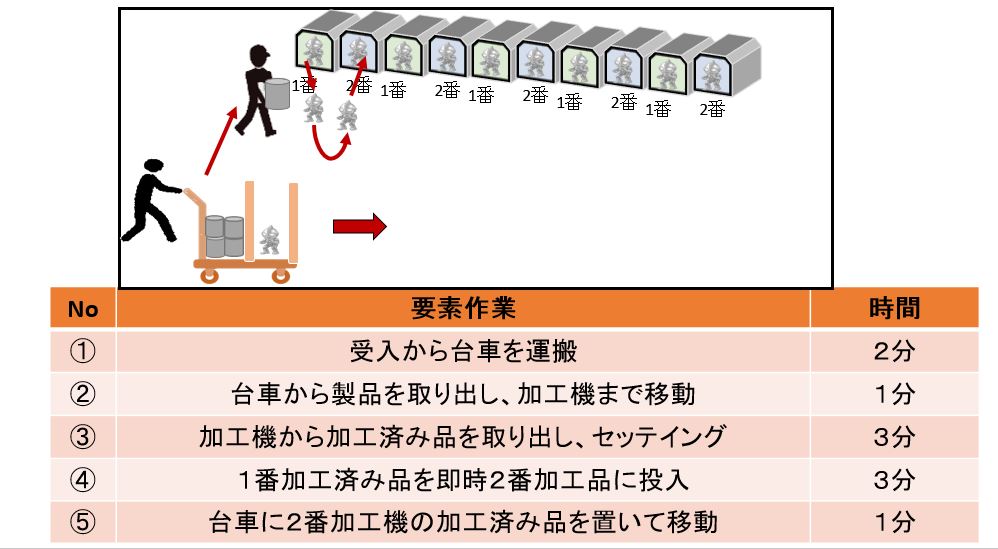
加工機のレイアウト改善事例
6)作業者の多能化 改善:
A作業者の多能工化教育を実施し1番加工から5番加工まですべての加工機を一人で扱うことができるようにする。A作業者は1番加工と2番加工を工程の順に続けて2台を一連の動作で作業を行う。この作業を1~5号機まで5回繰り返し,3番加工機では5個の製品を一括して出し入れ作業を行い,続いて4番加工と5番加工の1号機までを行い,B作業者に台車を受け渡して作業を引き継ぐ。B作業者は,A作業者の残りの作業を担当し,60分の間に23分の作業余裕をつくり,ライン作業とは別の作業を分担させる。
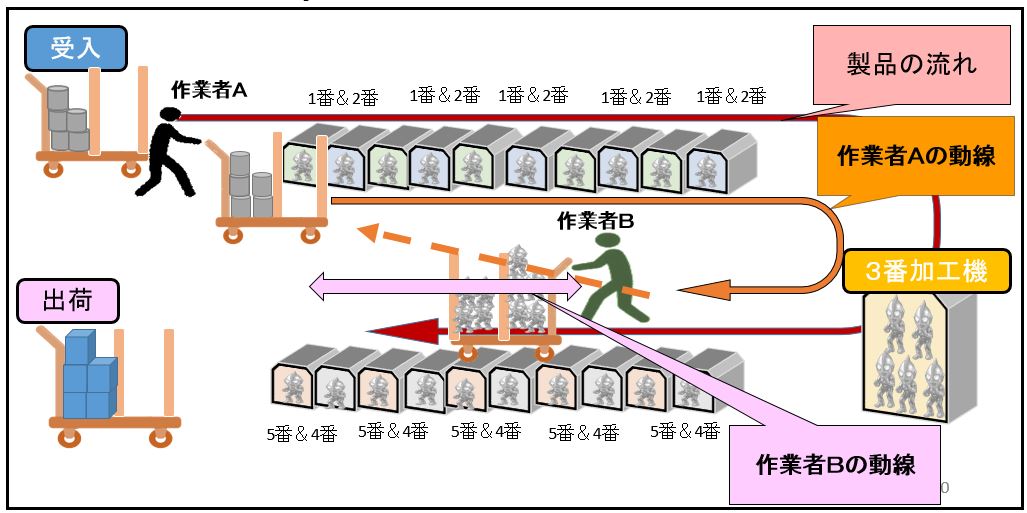
作業者の多能化 改善事例
効果確認:
改善のトータルの成果を振り返ると,改善活動の前は1番加工から5番加工までの作業に5人分の作業工数(1時間のサイクル作業で300分)がかかっていたが改善後は 1.6人分の工数(97分)で同じ仕事ができるように改善された。
仕掛りの改善は改善前の360個から,改善後はわずか55個になった。55個の内訳は,受入出荷場の20個が最も多く,各加工機に仕掛けている25個と2人のオペレーターの台車に積んでいる10個のみとなった。
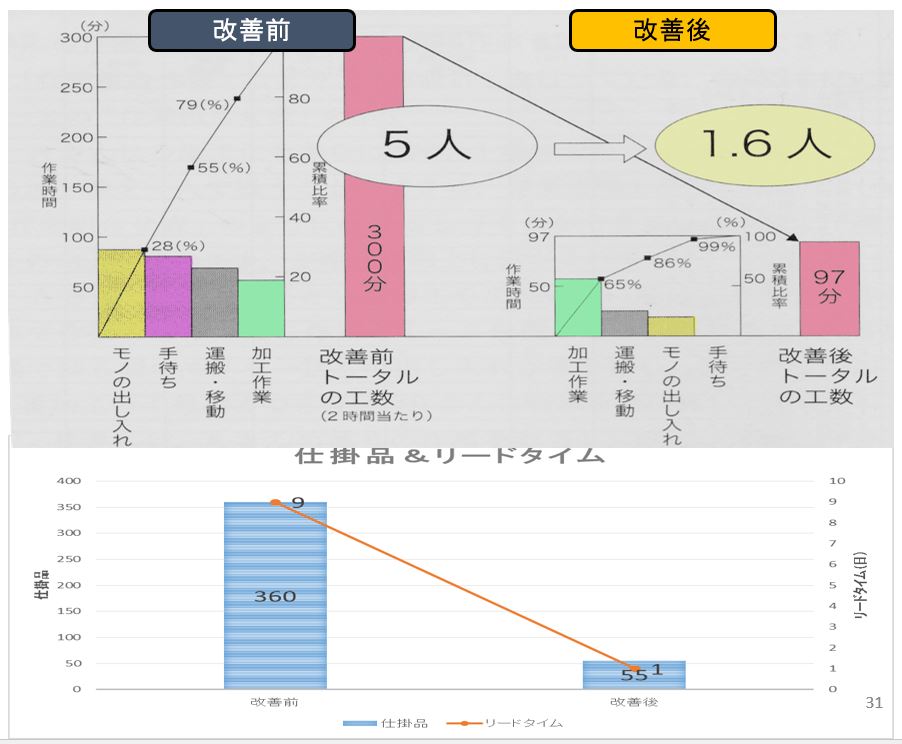
改善効果確認
ケーススタディのまとめ
仕掛品とムダ
リードタイムは部材の投入から製品の出荷までに掛かる時間(期間)である。仕掛りが多ければ,それに比例してリードタイムは長くなる。したがって,仕掛りの量がリードタイムの長さになる.例えば,1時間で5個ずつモノが進むラインで,ラインの仕掛りがトータル50個、あれば10時間のリードタイム, 500個あれば100時間のリードタイムになる。
ウルトラ社の工場の場合、改善前は仕掛品が360個あったが加工中の製品は25個しかなく,したがって,リードタイムで考えると,ほとんどの日数は加工されないまま停滞していることになる。
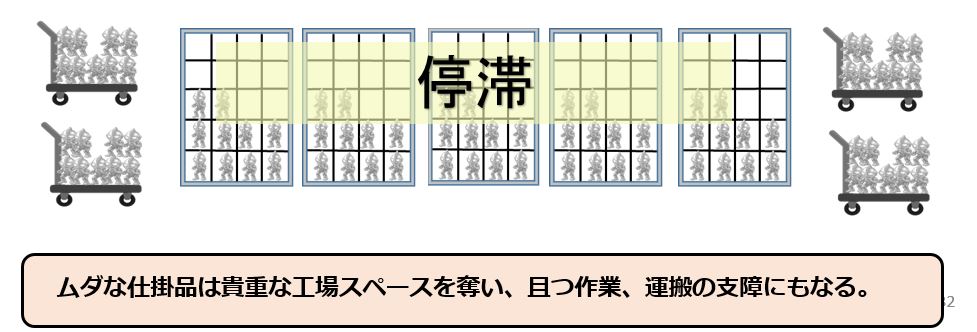
仕掛品の削減改善
付加価値作業とムダ
工場の作業を加工(付加価値作業)とそれ以外の作業(運搬、準備等)に分けて考える、加工は工場の利益を上げる為には必須な作業である、しかしそれ以外の作業(運搬、準備等)は加工作業をサポートする作業であり、可能なら短縮、廃止の改善を検討する。
理想の工場は加工作業だけが可能な限り近接したレイアウトの工程である。
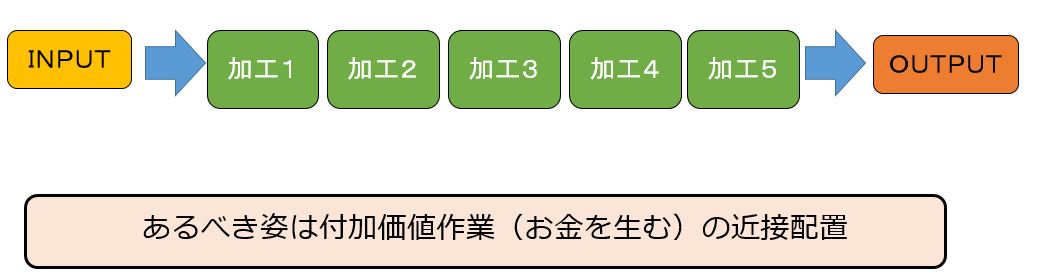
理想の工程レイアウト
リードタイムとコスト
ウルトラ社のお客様の受注が4日間分の製品について確定しているとする。
(4日間までは必ず買っていただける)。
4日間分は100%売り上げになるがその後の受注には変更の可能性があるので,仮に4日以降の3日間は20%の変動リスク(20 %は機種の変更やニーズが変わるなどで,買っていただけない危険度)があるとする。
さらにその後,つまり7日以降は,さらに40%のリスクがあるとする。この変動リスク分は,売れ残りとなる可能性がある。
この売れ残りの製品のために倉庫が必要となり,そのための管理業務も必要となる。最終的に売れ残った製品は陳腐化して廃棄となる場合が多い。仮に売れ残りの半分が廃棄されるとすると,ケーススタディーでは,生産量全体の8%が廃棄されることになる。
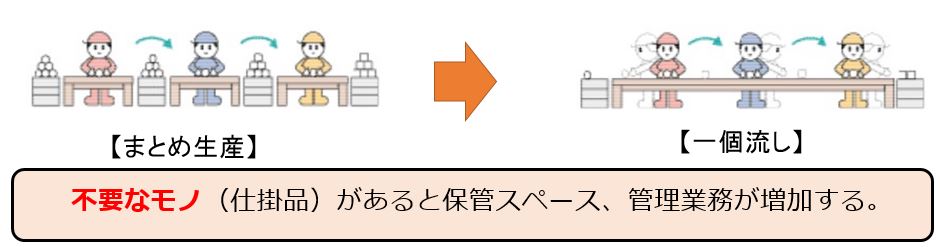
リードタイムとコスト
付加価値作業以外の作業(運搬、準備等)が発生する理由
仕掛品を削減しようとするとその言い訳の理由が色々、でてくる。
例えば設備のチョコ停、トラブル多発、部品の供給不安定、工程間の同期ずれ等
しかし、これらの問題を永久的に仕掛品で解決させてはいけない。
真の問題を早急に解消して仕掛品がなくても円滑に生産できる工場にしなければならない、逆に言うと仕掛品を削減すると真の問題点が見えてくる。
時刻表を見てバス停にいけば待たずに乗れるが行き当たりばったりでは待機時間が発生する。又 通常、人の会う時、時間を指定するがモノを製造する際は正確に各作業間、工程間の同期化をさせてないで生産を行い、多くの仕掛品を滞留させている工場が良く見られる。
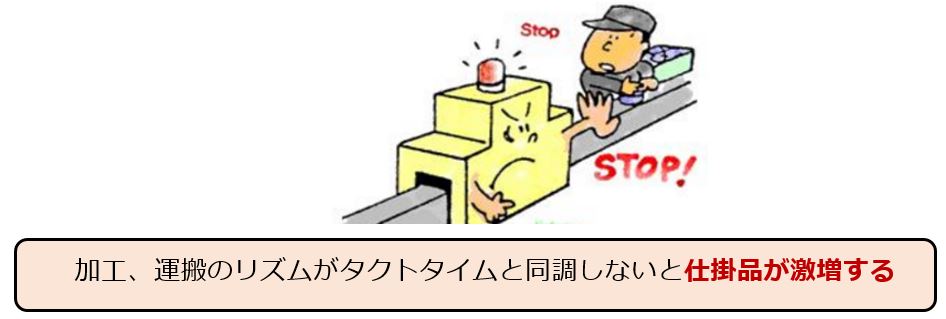
作業、工程間のタクトタイム同期化
IE分析とQC七つ道具
IE分析とQC七つ道具(7つ道具)は、共に「現場改善の武器」ですが、使う目的やアプローチにちょっと違いがあります。
それぞれを整理しながら、どう組み合わせて活用できるかを解説します!
QC七つ道具(Quality Control 7 Tools)とは?
QC七つ道具は、
「品質改善・問題解決」に使われるデータ分析系のツール群です。
7つ道具の一覧と使いどころ:
ツール | 主な目的 |
---|---|
① パレート図 | 重要な要因の優先順位を見つける(80:20の法則) |
② 特性要因図(魚の骨/フィッシュボーン) | 問題の原因を整理する(要因分析) |
③ ヒストグラム | データのばらつきを視覚化 |
④ 管理図 | 品質が安定しているかをモニタリング |
⑤ チェックシート | データ収集を簡単にする |
⑥ 散布図 | 2つの変数の相関を探る |
⑦ 層別 | データをグループに分けて比較する(属性で分ける) |
👉 問題の「原因」や「傾向」をデータから探るのが得意。
関連記事:QC七つ道具
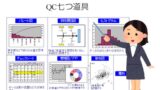
IE分析とQC7つ道具の違い・使い分け
項目 | IE分析 | QC七つ道具 |
---|---|---|
フォーカス | 作業・動作・プロセス | データ・不良・傾向 |
得意なこと | 作業のムダ取り、工程改善 | 品質改善、原因追及 |
使う人 | 現場改善・IE担当者 | 品質管理者・スタッフ |
対象例 | 動作のムダ、移動距離、作業時間 | 不良品の傾向、クレームの原因、品質ばらつき |
組み合わせると最強!
現場改善やプロジェクトで IEとQC7つ道具を組み合わせると、より効果的に改善できます。
例1:不良が多い工程がある
→ QCツールで原因分析(特性要因図、パレート図)
→ IEツールで動作・手順を分析(サーブリッグ、時間分析)
例2:作業が遅れている
→ IEで時間・動線分析し、改善点を特定
→ QCツールで記録と効果測定(チェックシート、管理図)
IE分析 → 「人と動きの改善」に強い
QC七つ道具 → 「問題の原因や傾向分析」に強い |両方組み合わせるとデータと現場の両面から改善ができる!|
トヨタ生産方式に基づくIE手法の実践
「トヨタ生産方式(TPS)」に基づいたIE手法の実践は、まさに現場改善の王道とも言えるアプローチです。
ここでは、TPSの基本思想にIE手法をどう組み合わせて現場で活用していくかを解説します。
トヨタ生産方式(TPS)とは?
TPSは、「ムダを徹底的に排除して価値を最大化する」ことを目指した生産管理の思想です。
2本柱
ジャスト・イン・タイム(JIT)
→ 必要なものを、必要なときに、必要な量だけつくる自働化(じどうか)
→ 異常があれば機械が自動停止する仕組み(人に依存しない品質管理)
TPS × IE手法の実践的アプローチ
TPSの考え方 | IE手法での具体的な実践 |
---|---|
ムダの排除 | 時間分析・動作分析によるムダ(動作・待ち・手持ちなど)の可視化 |
平準化 | 作業時間・負荷バランスを調整するラインバランシング |
標準作業 | タクトタイム・サイクルタイムをもとに作業標準を設計 |
5Sの徹底 | 作業分析を通じて必要なモノの位置や数量を最適化 |
改善(Kaizen) | 現場データをもとに継続的に改善策を提案&実装 |
品質内蔵 | ポカヨケ設計(ミス防止)と作業手順の見直しによる品質確保 |
実践ステップ(例)
現場観察(GEMBA)
→ ストップウォッチ or ビデオ分析で現場の動作・時間を把握ムダの分類(7つのムダ)
→ IEの「サーブリッグの動作分類」や「ECRS原則」で見直し標準作業票の作成
→ タクトタイムに合わせた標準作業組み立てレイアウト・動線改善
→ スパゲッティチャートやフローダイアグラムで最短動線を設計改善前後の比較・効果測定
→ 工数削減率、生産性向上率、安全性向上などを数値で示す
期待できる効果
作業効率の向上(時間短縮・動作削減)
不良率の低下・品質安定
作業者の負担軽減(エルゴノミクス的観点も含む)
柔軟な生産対応(変種変量に強くなる)
実践のコツ
「見える化」が出発点(グラフ・図・数値で納得させる)
IEは「改善の裏付け」として機能(現場説得にも強い)
現場巻き込み型で進める(Kaizen活動と連動)
小さな改善の積み重ねが最終的な大きな成果に
IE分析ツールの選定と活用法
「IE分析ツールの選定と活用法」は、現場改善や生産性向上の効果を大きく左右するポイントです。
ここでは、目的別に使えるIEツールの種類と、選び方・使い方のコツを分かりやすく整理します。
IE分析でよく使われるツール一覧(目的別)
分析目的 | 使用ツール | 内容・特徴 |
---|---|---|
時間の分析 | ストップウォッチ法 / タイムスタディソフト | 作業時間を計測し、標準時間を算出 |
動作の分析 | サーブリッグ分析 / ビデオ分析 | 作業のムダ・改善点を動作単位で評価 |
作業の標準化 | 標準作業票 / タクトタイムシート | 各作業者の役割と作業時間を定義・可視化 |
動線・レイアウト | スパゲッティチャート / フローダイアグラム | 人や物の動き・配置のムダを見つける |
稼働率の分析 | 稼働分析シート / ヒストグラム | 稼働・停止・待ち時間の割合を分析 |
工程全体の見える化 | プロセスマップ / VSM(バリューストリームマップ) | 全体の流れを見える化してムダを抽出 |
工程改善の提案 | ECRSチェック / PQ分析 | 排除(Eliminate)・結合(Combine)などの視点で改善策を考える |
スパゲッティチャートとは?
作業者やモノの動線(移動の軌跡)を、実際のレイアウト図の上に線で描いた図のことです。
たとえば…
工場のレイアウト図に、作業者が歩いた経路を線で記録していくと、
ぐちゃぐちゃに交差してスパゲッティのようになる…
👉 これが「動線にムダがある」サインです!
SM(Value Stream Map)とは?
**VSM(バリューストリームマップ)**は、
製品やサービスが顧客に届くまでの一連のプロセス(価値の流れ)を可視化する図です。
💡「Value Stream」=「価値の流れ」
つまり、付加価値のある作業(value)と、ムダな作業(non-value)を見える化して、全体改善につなげるのが目的です。
ツール選定の考え方
目的を明確にする(「どこに課題があるか」)
時間?動作?レイアウト?品質?
現場に合った粒度を選ぶ
大雑把な流れを見るなら「フロー図」や「VSM」
細かく改善したいなら「サーブリッグ分析」や「動画解析」
記録手段を考慮
手書き・Excelベースでやるか、ソフト・アプリで効率化するか
よく使われるIE分析支援ツール(デジタル)
ツール名 | 主な機能・特徴 |
---|---|
MotionBoard | 動作・作業時間を可視化し、BI的に分析可能 |
TimePrism | 動画を使った動作分析(サーブリッグ分類が可能) |
OTRS(オーティーアールエス) | ビデオ分析の定番。標準時間算出や帳票出力も可能 |
Excelテンプレート | 標準作業票、ECRS、工程分析などカスタム自在 |
VSMツール(iGrafxなど) | 全体のプロセスと情報・物流の流れを一括管理 |
活用の流れ(例:作業改善)
現状把握
動画やタイムスタディで現場観察
分析
動作を分類(例:サーブリッグ)し、ムダを可視化
課題の抽出
タクト超過、不要動作、重複など
改善案の立案
ECRS原則や改善事例を参考に
標準作業の更新
作業票を更新して現場へ展開
定着・再分析
改善後の効果を数値で検証し、次のサイクルへ
IEツール活用のコツ
見える化を最優先:「誰でも理解できる」資料を作る
現場巻き込み型で進める:作業者の声を反映すると改善効果UP
小さく始めて効果検証:大きな改善より、まず1工程・1人から
改善後も定期観測:標準作業は「生き物」。定着を確認
今後のIE分析の展望、未来
IE(Industrial Engineering:インダストリアル・エンジニアリング)分析の未来について考えると、以下のような進化や方向性が見えてきます:
デジタル技術との融合(DXの加速)
IoT・センサー技術の進化により、現場の作業データをリアルタイムで収集・分析可能。
AI・機械学習による工程最適化や予測分析が、IE分析の中心に。
デジタルツイン(現実の工場と同じ仮想モデル)を使って、改善策のシミュレーションが現実に。
ビッグデータ分析との連携
現場だけでなく、サプライチェーン全体のデータを統合的に分析。
作業時間、在庫、品質など多変量データをもとに、全体最適を目指す方向へ。
人とロボットの協働最適化
作業者の動きとロボットの動作の最適な分担をIE分析で設計。
**エルゴノミクス(人間工学)**と連携して、働きやすい環境を定量的に構築。
サステナビリティ(持続可能性)とESG視点の導入
IE分析に環境負荷の最小化やエネルギー効率といった観点が組み込まれるように。
社会的責任を果たすプロセス設計が重視される。
**「ESG視点」**は、サステナビリティと深く関係していて、今の時代の企業評価・経営の重要なキーワードです。
ESGは、次の3つの頭文字をとった言葉です:
E:Environment(環境)
→ 地球環境への配慮。
例:CO₂削減、再生可能エネルギー、廃棄物削減、資源の効率利用など。S:Social(社会)
→ 社会や人への責任。
例:労働環境の改善、人権の尊重、多様性(ダイバーシティ)、地域貢献など。G:Governance(ガバナンス)
→ 組織運営や意思決定の透明性。
例:不正防止、取締役会の機能、説明責任(アカウンタビリティ)など。
IE(インダストリアル・エンジニアリング)とESGの関係
ESG視点 | IE分析で貢献できること |
---|---|
E(環境) | エネルギー効率の改善、廃棄ロス削減、省資源の工程設計 |
S(社会) | 安全な作業設計、人にやさしい職場(エルゴノミクス) |
G(ガバナンス) | データに基づく改善・透明性のあるプロセス管理 |
ナレッジベースの構築と共有
経験豊富なIE技術者の知識を形式知化し、AIに学習させる。
ベテランの暗黙知を次世代へスムーズに継承できる仕組みが必要に。
**ナレッジベース(Knowledge Base)**とは、
業務に必要な知識やノウハウをまとめて蓄積・共有する仕組みやデータベースのことです。
簡単に言えば、「人の頭の中にある経験や知識を、みんなで使えるようにする情報の宝庫」です。
IEの現場での使い方
IE分析の現場では、ナレッジベースを活用することで:
同じ改善を繰り返さない(過去の改善履歴を参考にできる)
工程設計・レイアウト設計のテンプレートが使える
動作分析・時間分析のツールや事例が整理されている
ノウハウのデジタル化でAIやRPAに活用しやすくなる
教育・スキルの変化
従来の「時間研究」「動作分析」だけでなく、データサイエンス・プログラミングスキルもIEに必須に。
マルチスキルなIEエンジニアが求められる時代へ。
Slideshare 無料 ダウンロード作業分析 資料
参考文献:
コメント