マテハン分析の基礎
物流センター、工場倉庫でのマテリアルハンドリングの分析、改善方法を解説、物流改善の基本については下記の記事が参考になります。
関連記事:物流改善の進め方【図解】
マテリアル・ハンドリングとは
マテリアル・ハンドリング(Material Handling、MHまたはマテ・ハン)とは、商品を仮置(停滞)している状態から移動することを言い、自社内での荷降ろし・積替え・集荷・移動・積込み・出荷作業などの一貫した品物の取扱いをマテ・ハンと言う。
このマテ・ハンに要する費用はどの企業でも高額であり、とくに鉄鋼業などにおいてはコスト削減の最大の対象であった。その後もあらゆる分野で小ロット化、タイムリー化か客先二-ズとしてクローズアップされる中、コスト増の最大の問題となり続けている。
生産工場でのマテ・ハンを次の図表のように分類される。
①工場・資材倉庫での貯蔵段階マテ・ハン
②工程間運搬作業でのマテ・ハン
③配送センターでのマテ・ハン
マテハンの分類
①工場・資材倉庫での貯蔵段階マテ・ハン
貯蔵段階としては、資材・部品などの補給機能がある。一般的に倉庫は主要機能でないために工場の遠い位置に設置されるケースが多く、その分運搬距離も長くなる。そこで、できる限り外部から搬入時、工程前直入を図り、ハンドリング回数の削減のための生産管理改善が必要である。
②工程間運搬作業でのマテ・ハン
エ程間作業には必ずマテ・ハンが付きまとう。たとえば加工・組立・梱包前後の移動・準備・位置決めなどがある。ここでは工程後の仮置き・運搬などをなくし、できる限り加工→即梱包、組立→検査→梱包と連続して作業可能にレイアウトを計画すべきである。
③配送センターでのマテ・ハン
配送センター、製品倉庫でのマテ・ハンのために多くの作業者を必要としているところも多い。問題は在庫が多いために置場不足と配置換え、ハネ出し作業増がある。そこで出荷情報の精度向上と、積込時間の短縮などでの効率アップが望まれる。
マテハンの流れを記号で表現したモノが下記の図である。
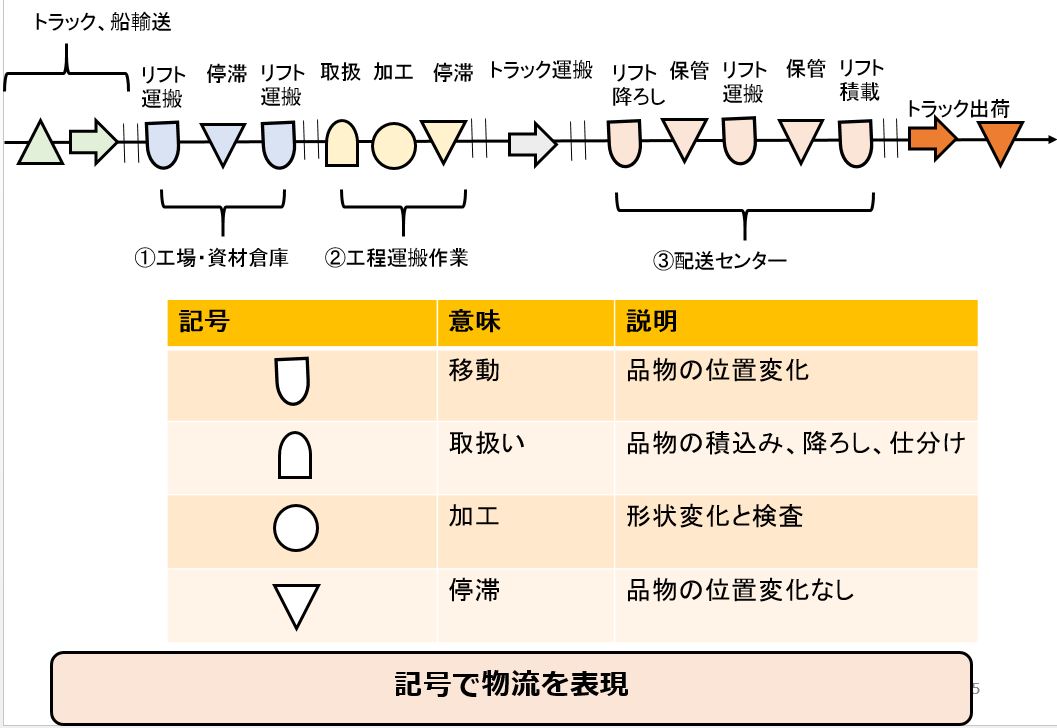
マテハン流れ図
マテリアル・ハンドリング分析の種類
マテハンの運搬分析はその対象とするものによって幾つかの種類に分けられるが主な分析手法は次のとおりである。
(a)運搬工程分析
これは,観測対象となる品物が流れていく状況を順を追って調べ,その取り扱われ方や置かれ方を「運搬工程記号」を用いて記録し,分析・検討する方法である。これには,「直線式運搬工程分析」と「配置図式運搬工程分析」がある。
(b)運搬活性分析
これは,「活性」(置かれた品物の移動のしやすさ)の維持という観点から品物の置き方や荷姿について分析・検討する方法である。
(c)カラ運搬分析
品物の移動をともなわずに,運搬設備・器具のみの移動のために行われる運搬を「カラ運搬」という。「カラ運搬分析」では,運搬の状態を分析・検討してカラ運搬を減少させることをねらいとしている。
運搬工程分析とは?
品物の流れのなかで,特に「品物の動き」に主眼をおいて行う分析手法である。この分析のやり方は,基本的には工程分析と同じであるが使用する分析記号が若干異なる。すなわち,運搬工程分析には,次のような記号が使われる。
① 基 本 記 号
品物の扱われ方による作業の区分を示すもので,工程分析と異なる点は運搬が移動と取扱いに分かれる点である(下表)。
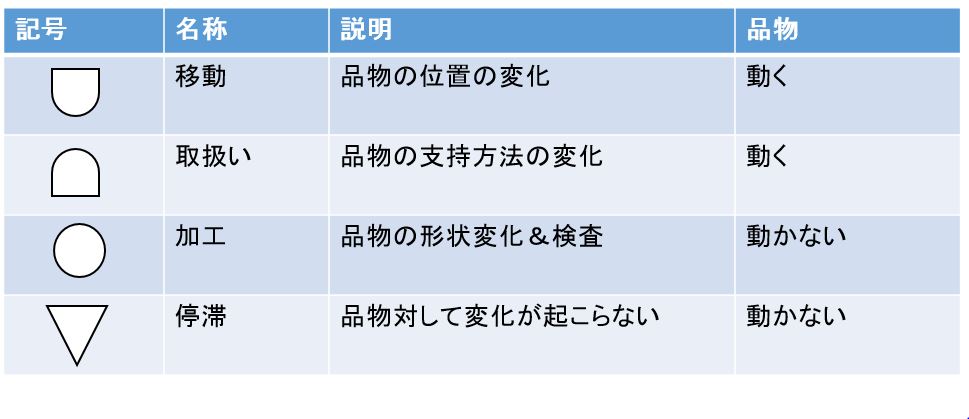
運搬工程分析 基本記号
② 台 記 号
品物の置かれた状態を示し,運び出しやすさを区分するものである。基本記号に付記して用いる。この記号によって,運搬のしやすさを把握することができる(下表)
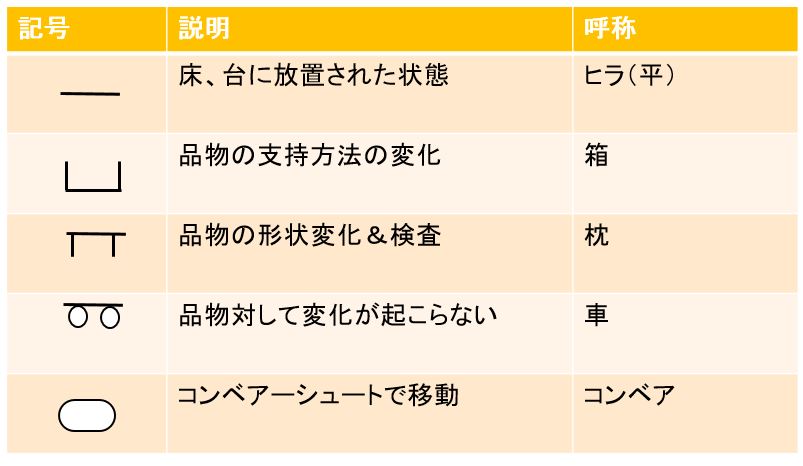
工程運搬分析 台 記号
③ 動力記号
品物の移動、加工する為の動力が何であるかの区分と人手の要不要を記載。
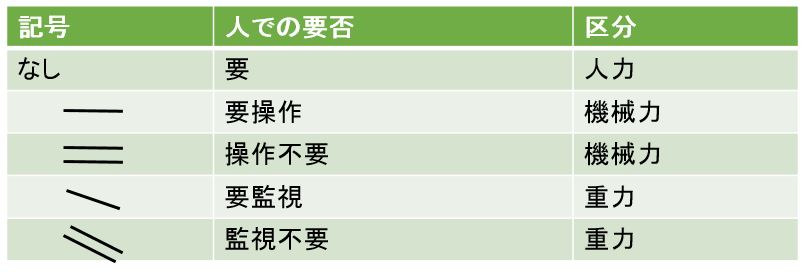
工程運搬分析 動力
④ 移動線
分析記号をつないで品物、人、運搬器具の動きを示すもの。
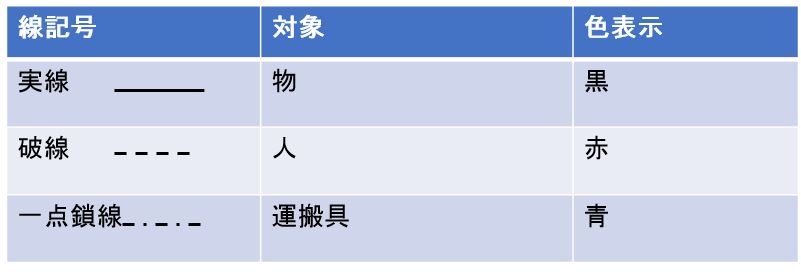
工程運搬分析 線記号
運搬工程分析の分類
運搬工程分析には下記の2つがあり、目的によって使い分ける。
① 直線式 運搬工程分析
品物の流れる工程を分析記号で表してこれらの記号を移動線で結び、必要に応じて左側に「所要時間」「距離」右側に「作業者」「場所」「運搬具」「重量」などを記入し、これらを分析して改善案を提起する。
この方法は運搬の状況を定量的に記録することによって問題点を明確にできる。
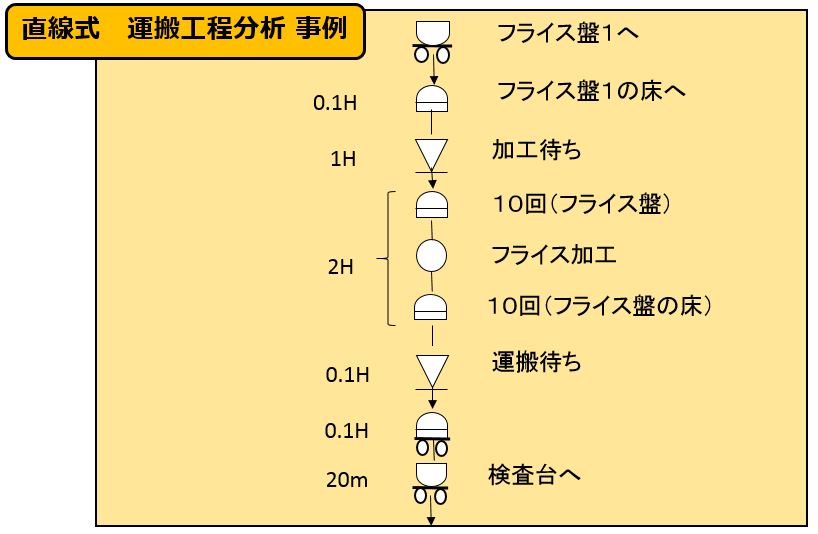
直線式 工程運搬分析
② 配置式 運搬工程分析
実際の現場配置を調査し、直線式運搬工程分析の情報を基に運搬経路を線で結んで記入、この方法は「運搬の流れ」「運搬距離」が目で見て分かるのでレイアウトの欠点が一目でわかるので運搬改善を検討するのに効果的である。
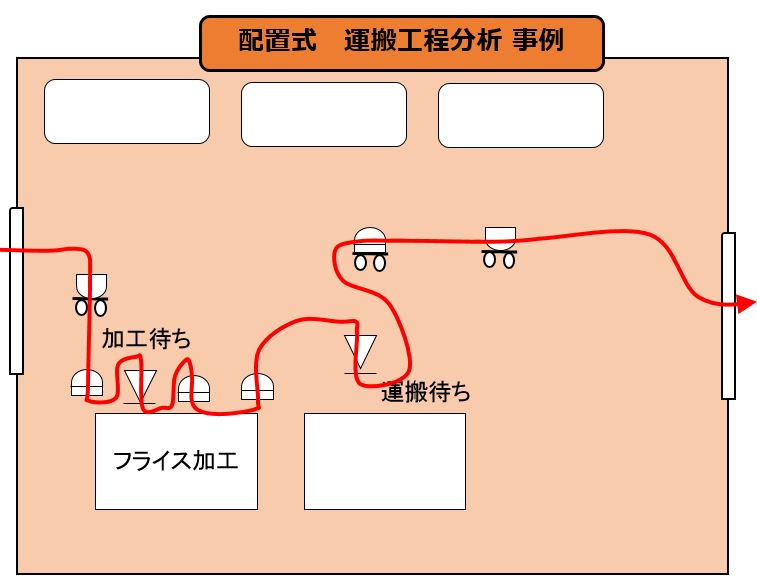
配置式 工程運搬分析
運搬工程分析の進め方
〔ステップ1〕目的,対象をきめる。
① 現状の問題点を明確にしたうえで,たとえば,運搬距離の短縮,運搬回数の削減,作業場のレイアウト改善などの目的を具体的にきめる。
② 目的に応じて,分析対象となる工程や工程の範囲をきめる。
③ 対象となる製品(特に,運搬上問題のある製品)をきめる。
〔ステップ2〕時期,方法をきめる。
① 観測準備の都合や対象部門の協力などから,分析の開始から終了までの期間を明確にする。
② どんな方法で,だれが実施するのか,を明確にする。
③ 分析を能率的に行うために,必要な分析用具や資料を準備する。
・分析用具:用紙,筆記具,ストップ・ウオッチ,巻尺など
・資料:配置図,工程分析図表,そのほか分析に必要な資料。
〔ステップ3〕運搬工程分析図(直線式工程分析図)にまとめる。
①用紙に次の事項を記入。
・対象となるライン,工程名,製品名
・調査・分析の期間,作成年月日
・分析者の所属,氏名
・そのほか特記すべき事項
② 運搬工程を,製品の流れを中心に運搬工程分析記号を使って記入する。
観察だけでは不明な点については,聞き込みで確認する。
③ 各工程の内容を調査し,所定欄に記入する。記入事項として
・移動距離,時間
・運搬物の重量,運搬具の名称
などがある。
〔ステップ4〕総括表にまとめる。
直線式運搬工程分析図に基づいて,「総括表」を作成する。この表の集計値
を分析して問題点を把握する。
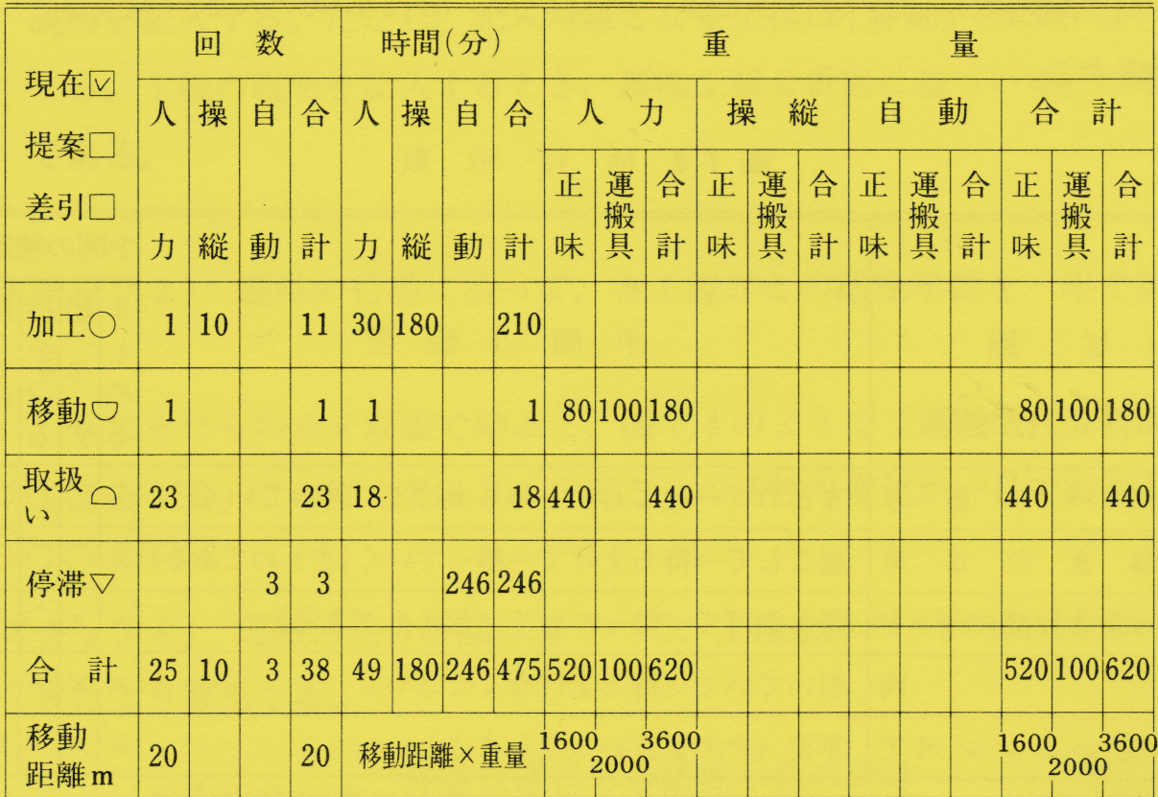
マテハン分析 総括表
〔ステップ5〕配置図式 運搬工程分析図を作成する。
① 対象職場のレイアウト図を作成する。
② 運搬経路に沿って,各工程の場所に運搬工程分析記号を記入し,これらの記号を線で結ぶ。
運搬活性分析とは?
活性示数の意味
運搬は移動距離だけが問題ではなく,運搬の前後における「取扱い」すなわち,積み込み,積みおろし作業に,より多くの時間と労力が費やされているのが実態である。
したがって,品物の置き方は,次に移動するのに手間がかからないことが大切である。置かれた品物の「移動のしやすさ」を「活性」と呼ぶ。活性を5段階に分けて,「活性示数」を使って運搬状況を分析するのが「運搬活性分析」であり(下表)、活性示数が大きいほどよいことを意味する。
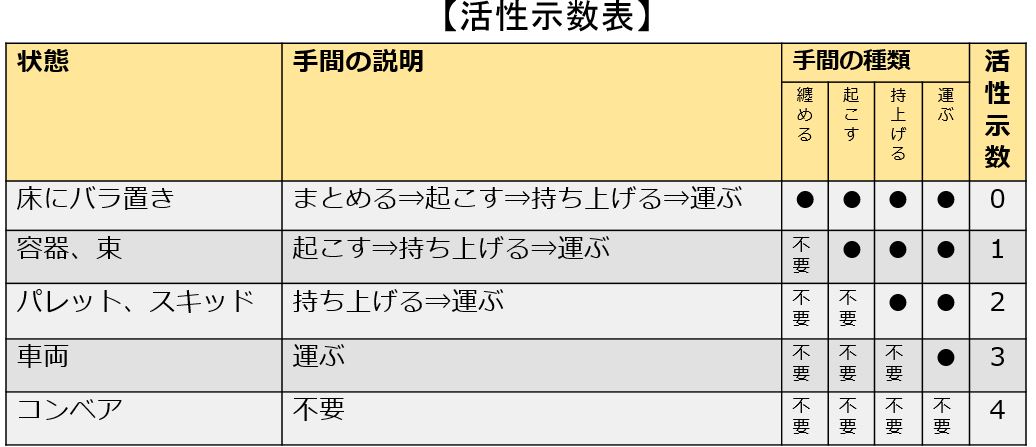
マテハン 活性示数表
運搬活性分析図の作成
運搬活性分析を行うには,「運搬活性分析図」を作成すると,現状を把握しやすい。以下,運搬活性分析図の作成手順について述べる。
〔ステップ1〕横軸に工程(ステップ)を,縱軸に活性示数をとる。
〔ステップ2〕横軸の各ステップ目盛の上方に,性示数表に基づいて,各工程の説明を記入する。ただし,記入対象となる工程は「移動」「取扱い」のみとする。工程の説明を記入するとき,運搬工程分析図に基づいて行うと便利である。
〔ステップ3〕縦軸の目盛に沿って,各工程ごとの活性示数を●印で記入する。
次にそれらの点を直線で結ぶと,次図のような「運搬活性分析図」ができあがる。この図を見ると,工程ごとの活性の変化が一目でわかる。
〔ステップ4〕運搬活性分析図に基づいて工程全体の「平均活性示数」を次式により算出する。
平均活性示数=(停滞状態にある活性示数合計 )/停滞状態の数
〔ステップ4〕
下図 例では
平均活性示数= (0+3 + 4十0+ 3+4+3+4+2 + 4)÷10=2.7
となる。この示数の値が小さいほど品物の置き方が悪く,移動のために多くの手間を要する。
このように,平均活性示数を算出すれば,品物の置き方の良し悪しを比較することができる。要は活性示数を高めることである。
そのためには,コンテナやパレットなどを積極的に利用し,また,人力による運搬をできるだけ機械力に変えることが望ましい。
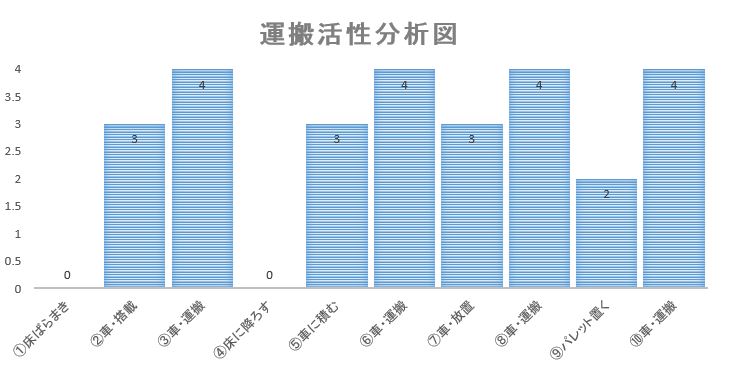
運搬活性分析図
カラ運搬分析とは?
「カラ運搬」とは文字通り,原材料・部品などを積み込まないで,空の状態で移動することである。多くの工場において,原材料・部品,製品の運搬にはそのものの移動の2倍以上の距離の歩行,運搬車の移動が行われている、カラ運搬は,まったくムダでしかない。
工場内での運搬を考える場合,従来は,品物を工程のすすむ方向に移動させることのみを重視して,そのために必要な人や運搬車の移動をあまり考えていない。
しかし,品物の移動だけにとらわれずに,人や車の動きを調査してみると運搬改善に結びついてくる。その改善の手がかりとして「カラ運搬係数」を求める。
カラ運搬係数=
((人の移動距離)ー(品物の移動距離))/品物の移動距離
=(カラ移動距離 )/品物の移動距離
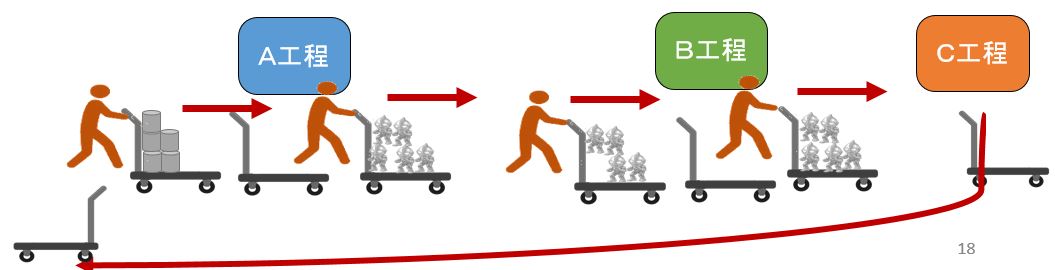
カラ運転分析
マテハン改善案の検討
マテハン改善の検討
マテハン分析によって実態が把握できると,以下に示すような着眼点に基づいて,問題点を把握し,改善案を提起する。
(1)運搬工程分析図表の改善着眼点
① 台記号を調べて活性の低いものは,高める方法を考える。
② 停滞が多くないか。できるだけ停滞をなくせないか。
③ 停滞の前後の取扱いをなくせないか。
④ カラ運搬をできるだけ減らせないか。
⑤ 人力運搬をできるだけ機械力,重力利用に変えられないか。
⑥ 運搬距離を短縮する方法はないか。
⑦ 移動線の逆行や屈曲はないか。それを減らすためにレイアウトを変えられないか。
(2)運搬活性分析の改善着眼点
① ユニット化を図る
容器に入れた状態で運べるようにして,活性示数を0から1にあげる(コンテナ,運搬箱,袋など)。
② パレット化を図る
フォークリフトで運搬できる荷姿にして,活性示数2の状態にする(パレッド,スキッドなど)。
③ 車両化を図る
車両にのせた状態で置き,すぐ運搬できるようにして,活性示数を3に上げる(手押し車,台車,置台兼用の運搬車など)。
④ コンベアの利用
コンベアにのせて自動的に運べるようにすれば,活性示数4の状態になる(ベルト・コンベア,スラット・コンベアなど)。
活性の改善をすすめるにあたって,当然個々に活性示数が大きい状態ほどよいが,同時に一連の工程の流れをたどってみて,工程全体の活性示数(平均活性示数)が大きくなるようにすることが必要である。
よくみられる事例として,コンベアとコンベアの継ぎ目で手運搬が行われていて,そこが工程の流れのネックになっていることがある。運搬改善で見落としてはならない点は,アンバランスな継ぎ目運搬を改善することによって,全体の生産性を高めることである。
平均活性示数による改善着眼点
① 0.5未満:コンテナ,パレット,手押し車の活用をすすめる。
② 0.5~1.3未満:動力運搬車,フォークリフトの活用を考える。
③ 1.3~2.3未満:コンベア,トレーラ列車方式の活用を考える。
④ 2.3以上:コンベアやフォークリフトの活用をすすめ,運搬工数の節減を図る。
*トレーラ列車方式:
あらかじめ作業場所の傍にトレーラ(被けん引車)を置き,できたものを直接トレ一ラにのせ,積み終ったトレーラを出しておく。これをトラクタ(けん引車)が引いていって,所定の場所にトレーラごと切り離して置いていく方式。この方式では,移動の前後の再取扱いがなくなりトラクタ、運転手の有効稼働が向上する。「TTT方式」ともいわれる。
運搬の基本原則によるマテハン改善
① 品物の活性についての原則
・活性荷物の原則:品物を動かしやすい状態に保つこと。活性示数を維持し,向上すること。
・単位荷物方式(ユニット・ロードの原則):荷物をまとめた形で取扱うこと。荷姿を統一し,運搬具や運搬方式を標準化すること。
・パレット化の原則:品物をパレットにのせて,取扱いやすくすること。
・再取扱いの原則:積み替えなどの再荷役作業をやめること。
・トレーラ列車方式:トレーラを有効に活用し,再取扱い,横持ちをなくすこと。
② 機械化・自動化についての原則
・重力化の原則:重力を活用して人の手間を省くこと(重カローラ・コンベア,シュータの利用)。
・機械化・自動化の原則:品物の移動,取扱いを機械化・自動化すること。
・継ぎ目の原則:移動と移動の継ぎ目に起こる取扱いの手間を省くこと。
③「手待ち」と「カラ運搬」についての原則
・チームワークの原則:共同作業を行うとき,仕事の関係で相互に手待ちを生じないようにすること。
・定時運搬方式:運行時刻を組んで,定時に運搬車が巡回して集配する方式。カラ運搬や手待ちが減り,運搬車と人員のムダが省ける。
・稼働率の向上:運搬設備の稼働率を上げること。
④ 能力向上,作業改善についての原則
・融通性の原則:運搬設備は融通性と弾力性のあるものを選ぶこと。
・スピードの原則:取扱い回数の減少,取扱い時間の短縮,移動速度の増
加で総合的に運搬のスピードアップを図ること。
・スペース活用の原則:バラ置き,しか置きを除去し,パレットにのせて
積み上げるなど,床面積を活用すること。
・自重軽減の原則:運搬具の自重を減らすことにより,運搬効率を上げる
こと。
・標準化の原則:運搬機器のタイプ,大きさおよび方法を標準化すること。
⑤ 移動経路についての原則
・配置の原則:運搬と配置の関係を重視し,配置の合理化・適正化を図る
ごと。カラ運搬の減少,運搬経路の単純化,距離・回数の減少を考える。
・流れの原則,直線化の原則:運搬経路は逆行や屈曲をさけ,なるべく直
線にすること。
MHの改善をすすめるにあたって留意すべきことは,1工程あるいは1部門のみの最適化にとらわれることなく,生産活動全体からみて最適なMHシステムを構築しなければならない。そのためには,MHの改善を行うにあたって経営上の問題が何であり,どこまで改善すべきかという目標を明確に設定してから取組む。
マテハン 改善事例
事例①運搬距離を改善
・部品置き場の位置を組立台(コンベアー)に近づけ、交差を無くした。
・電源工事を行いエージング位置を組立台(コンベアー)に配置。
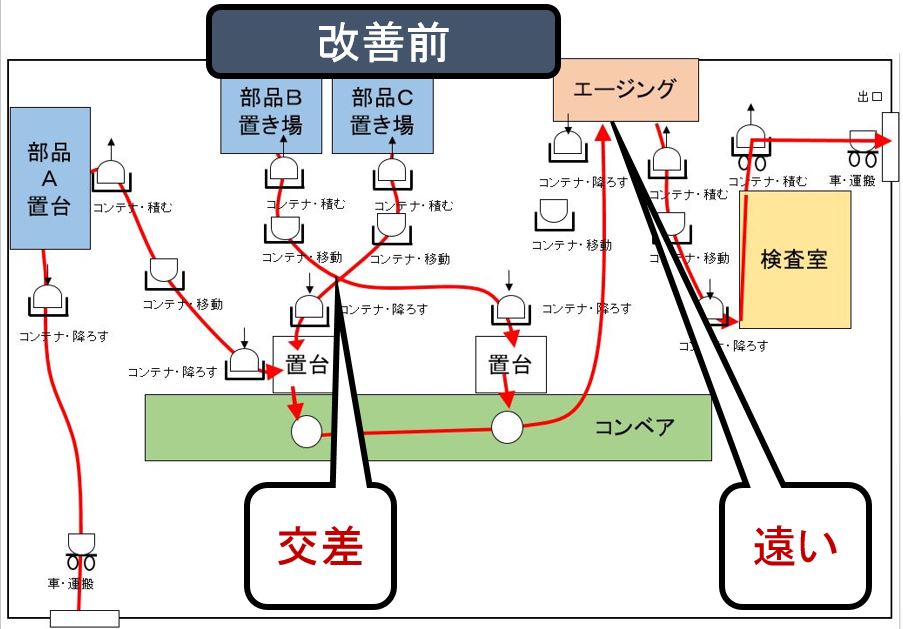
マテハン 改善前
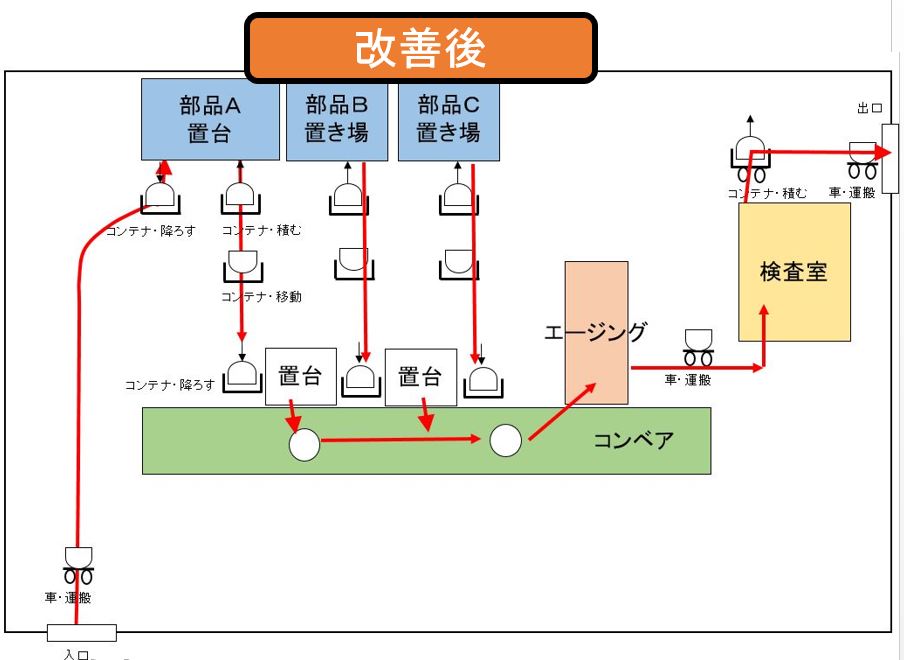
マテハン 改善後
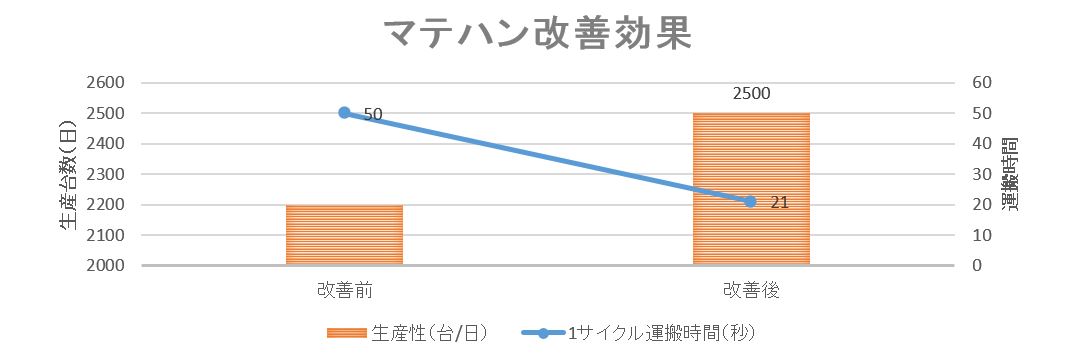
マテハン改善効果
事例②物流の整流化
・物流の整流化を行い、各工程を加工順に並べて停滞・追い越し・逆流を排除。
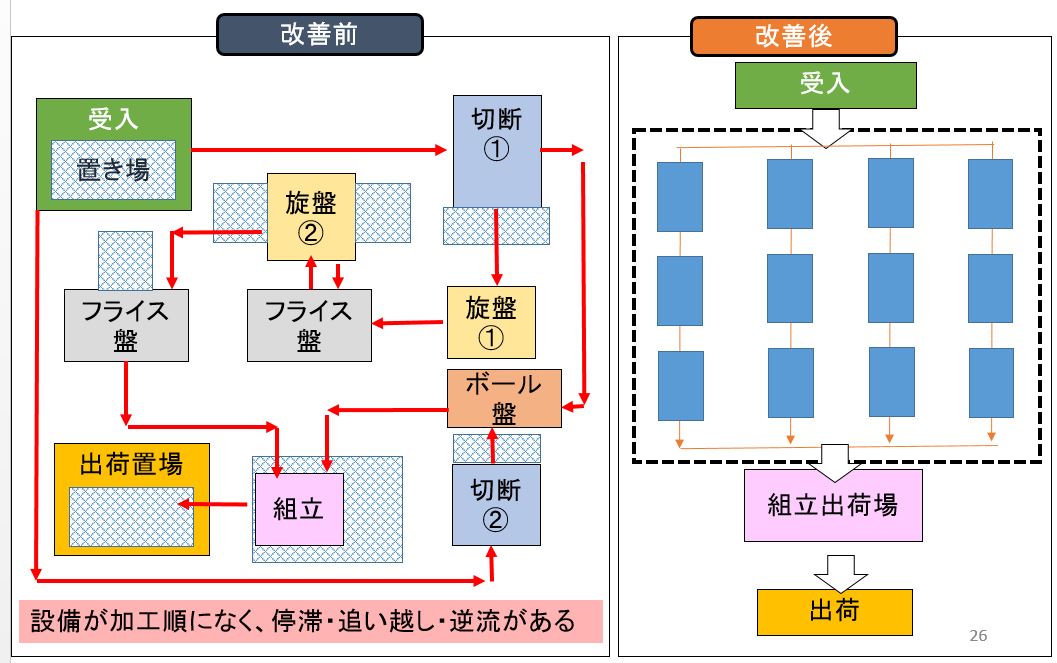
マテハン 整流化
自動化によるマテハンの進化
なぜマテハンの自動化が求められるのか?
人手不足の深刻化
倉庫や物流業界では慢性的な人手不足が進行。特に少子高齢化の影響が大きく、人海戦術が限界に。業務効率の向上
膨大な出荷量をさばくため、ミスなくスピーディーな処理が必要に。手作業では限界がある。DX(デジタルトランスフォーメーション)推進
製造・物流業界にもデジタル化の波が到来。自動化によるデータ取得・分析が競争力に直結。
主なマテハン自動化の技術と機器
AGV(無人搬送車)/AMR(自律走行ロボット)
決められたルートを走るAGV、柔軟にルートを選択できるAMR。倉庫内の搬送作業を自動化。自動倉庫(AS/RS)
自動で製品の出し入れを行う高層型倉庫。省スペース化・高密度保管が可能。ピッキングロボット
商品を自動で取り出して仕分けるロボット。AI画像認識で多品種にも対応可能。コンベヤ+ソーター
大量の商品を効率よく仕分け・搬送。EC物流などで広く活用。WMS(倉庫管理システム)との連携
機器だけでなく、システム連携によって「見える化」や「最適化」が進む。
マテハン設備の選び方とその効果
そもそもマテハン設備とは?
マテハン(マテリアルハンドリング)設備は、物の「移動」「保管」「仕分け」「搬送」などの作業を支援・自動化する装置やシステムの総称です。
例:コンベヤ、AGV、フォークリフト、自動倉庫、仕分け機、リフター、ロボットアームなど。
マテハン設備を導入する目的とは?
作業の省人化・省力化
人手不足への対応、作業負荷の軽減。業務の効率化
作業時間の短縮、動線の最適化。品質・精度の向上
ヒューマンエラーの削減、作業の均質化。安全性の確保
重量物や危険作業の機械化で事故リスクを低減。
マテハン設備の選び方【5つの視点】
① 扱う物量・品種
大量一括搬送なのか、小ロット多品種対応なのか?
ピース品? パレット? 重量物? それとも軽量品?
② 作業工程の見直し
どの工程を自動化したいのか?(入荷、保管、ピッキング、出荷など)
ボトルネックになっている工程はどこか?
③ スペースとレイアウト
導入スペースは確保されているか?
レイアウト変更の必要があるか?
④ 費用対効果(ROI)
初期導入費用 vs 人件費削減効果、作業時間の短縮など
リース・サブスクリプションモデルの活用も検討
⑤ システム連携
WMS(倉庫管理システム)などと連携できるか?
将来的な拡張性やメンテナンス性も重要
比較表:主要マテハン設備の特徴と適用範囲
設備名 | 特徴 | 適用範囲 | 導入コスト | 柔軟性 |
---|---|---|---|---|
コンベヤ | 単純な直線搬送に強い | 入荷~出荷全般 | ★★☆☆☆ | ★☆☆☆☆ |
AGV | ルート指定型の無人搬送車 | 搬送・保管 | ★★★☆☆ | ★★☆☆☆ |
AMR | 自律走行で柔軟なルート変更が可能 | ピッキング・搬送 | ★★★★☆ | ★★★★★ |
自動倉庫 | 高密度保管・高速出し入れ | 保管 | ★★★★★ | ★★☆☆☆ |
ピッキングロボット | AI画像認識対応で自動ピックアップ | ピッキング | ★★★★★ | ★★★★☆ |
ソーター | 大量の荷物を自動仕分け | 仕分け・出荷 | ★★★★☆ | ★★★☆☆ |
※★は目安(最大5つ)。導入コストは機器本体+システム連携等を含む。
導入による効果【実例付き】
効果1:作業時間の短縮
例:AMR(自律走行ロボット)の導入で、ピッキング時間が30%削減
効果2:人件費の削減
例:ソーター導入で1ライン3名体制 → 1名体制に減少
効果3:誤出荷率の低下
例:バーコード連携ピッキングロボットで、出荷ミスがほぼゼロに
効果4:従業員の安全向上
例:重量物のリフター導入で、腰痛などの労災が大幅減
現場にフィットする選定がカギ
マテハン設備は万能ではありません。「自社の業務フロー」や「現場の課題」に合った設備選びが最も大切です。
短期的なコストだけでなく、長期的な効率化・安全性・働きやすさへの投資として検討することが重要です。
よくある導入失敗パターン
機器を導入したが、現場に合わず稼働率が低い
スタッフ教育不足で活用しきれない
保守費用やシステム更新の想定漏れ
マテハン導入における問題点と解決策
マテハン(マテリアルハンドリング、Material Handling)とは、製造や物流の現場での資材・製品の運搬、保管、仕分けなどを効率化するための設備やシステムのことです。自動倉庫、コンベヤー、AGV(無人搬送車)、ピッキングシステムなどが含まれます。
マテハン導入にあたっては、さまざまな問題点が発生することがあり、事前の計画や対策が重要です。以下に主な問題点とその解決策を紹介します。
■ マテハン導入における主な問題点と解決策
1. 初期投資コストの高さ
問題点:マテハン機器やシステムは高額なものが多く、初期費用が大きくなりがち。
解決策:
ROI(投資対効果)を事前にシミュレーションして費用対効果を可視化する。
リースやサブスクリプションモデルを活用して、初期コストを抑える。
段階的に導入し、まずはボトルネック解消から始める。
2. 既存業務との整合性が取れない
問題点:既存の作業フローや施設レイアウトに合わず、逆に効率が落ちることも。
解決策:
導入前に現場のオペレーションを詳細に分析し、最適な導入方法を検討。
柔軟性のあるモジュール型マテハン機器を選ぶ。
実証実験(PoC)を行ってから本格導入する。
3. 従業員の抵抗や教育コスト
問題点:現場の作業員が新しい機械やシステムに慣れず、反発や混乱が起きる。
解決策:
初期段階で現場の意見を取り入れ、導入への納得感を高める。
操作研修・マニュアル整備・OJTを丁寧に行う。
成果が見えるようなKPIを設定し、導入の意義を共有する。
4. メンテナンスや故障時の対応
問題点:マテハン設備の故障で業務が停止してしまうリスク。
解決策:
導入時に保守契約や予備部品の確保など、リスク対策をセットで行う。
IoTなどによる状態監視(予防保全)を活用する。
重要工程に関してはバックアッププランを用意しておく。
5. システムの拡張性や柔軟性の不足
問題点:将来的な業務変更や成長に対応できないケースがある。
解決策:
拡張性のあるオープンプラットフォーム型システムを選ぶ。
初期導入時点で将来の拡張計画を見据えた設計を行う。
データ連携性のあるシステム(API対応など)を選定する。
■ 導入成功のためのポイント
現場ヒアリングを重視し「使いやすさ」に配慮。
小規模トライアルから始め、段階的な導入を検討。
外部パートナーとの連携(SIer・メーカー)をしっかり行う。
業務改善とのセットでマテハンを導入し、全体最適を目指す。
今後のマテハン改善に向けた展望
今後のマテハン(マテリアルハンドリング)分野における改善・進化の展望については、以下のようなトレンドや方向性が挙げられます。物流の高度化、労働力不足、デジタル化といった社会背景を受けて、マテハンも急速に進化していくと考えられます。
自動化・省人化のさらなる加速
背景:少子高齢化による人手不足、働き方改革。
展望:
AGV(無人搬送車)やAMR(自律走行ロボット)の高性能化と低価格化。
ロボットアームによる自動ピッキングの普及。
音声・画像認識を使った自動仕分け技術の導入。
スマートファクトリー・スマートロジスティクスとの連携
背景:製造・物流をデジタルで一元管理する動きが活発に。
展望:
IoTセンサーでマテハン設備の稼働状況をリアルタイム監視。
WMS(倉庫管理システム)やMES(製造実行システム)との連携による最適化。
AIによる需要予測・在庫最適化・人員配置の自動調整。
フレキシブルな運用が可能なモジュール型マテハンの普及
背景:需要変動・SKU(品目)の多様化に対応する必要性。
展望:
組み替え可能なモジュール式コンベヤや棚搬送ロボット。
季節変動や短期プロジェクトに対応できる柔軟な設計。
サブスクリプション型マテハンサービスの拡大。
AI・ビッグデータ活用による最適化
背景:データ駆動型経営の浸透。
展望:
ロボットや機器の動線分析 → 無駄の削減。
過去の作業実績から最適ピッキング順をAIが提案。
故障予測や自動メンテナンス通知によるダウンタイム削減。
サステナブルなマテハン機器の開発
背景:脱炭素社会・SDGsの実現に向けた取り組み。
展望:
省エネ型モーターや再生可能エネルギー対応マテハン機器。
モジュール再利用・リサイクル可能な設計。
環境負荷の見える化(LCA:ライフサイクルアセスメント)対応。
ヒューマン・マシン・コラボレーションの進化
背景:完全自動化よりも“協働”へのシフト。
展望:
危険作業のみロボットが担い、作業員は高付加価値作業に集中。
ウェアラブル端末やAR技術によるサポートで作業精度向上。
人間とロボットの共存による“スマート現場”の実現。
今後のマテハン導入に向けたキーワード
「柔軟性(フレキシビリティ)」
「データドリブン」
「スモールスタート」
「安全性と快適性」
「持続可能性(サステナビリティ)」
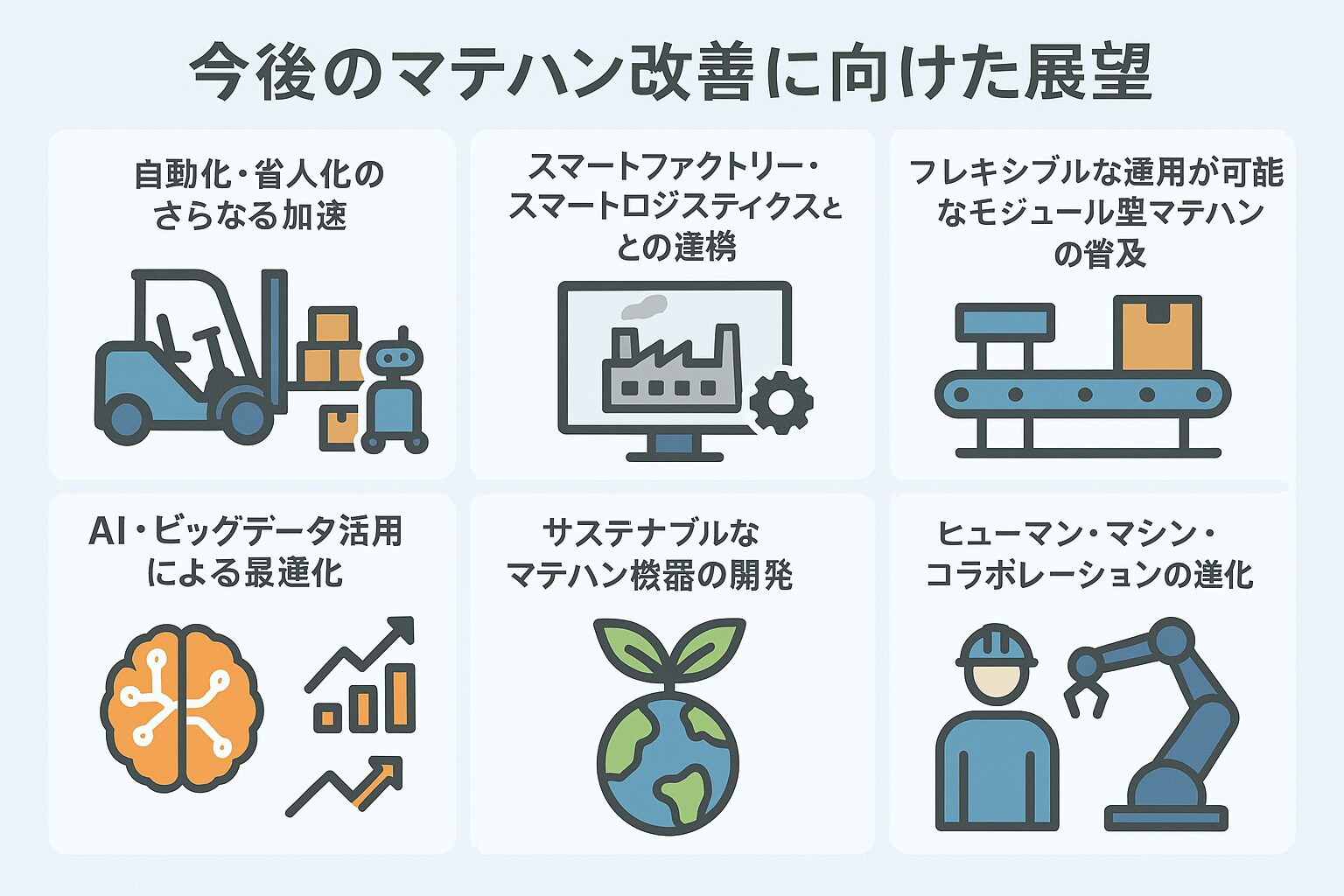
今後のマテハン改善に向けた展望
Slideshare 無料 ダウンロード資料
参考文献:
コメント
[…] 引用元:改善.net マテハン分析の進め方~事例で学ぶマテハン改善 […]