IE手法とは|カイゼンの基本
トヨタ生産方式が体系的にまとめられマニュアル化されたのは、昭和40年代後半のことです。トヨタではそれまでに種々のカイゼンを実施し、ようやく、一つの生産方式ができあがってきたことによるものと思われます。
カイゼンの過程で、現在活用されるようになった、さまざまなトヨタ独自の用語が生まれています。
この間、トヨタでは昭和30年から昭和50年代にかけて、繰り返しIE手法の教育がなされました。IEとは、Industrial Engineering(インダストリアルエンジニアリング)の略で、適当な訳語がないため、そのままIEと呼んでいます。
IE手法とは、モノと人の動きを細かく見る技術です。内容は、人・モノ・設備および情報を総合して、もっとも経済的な仕事のシステムをつくリあげていこうとするものです。
ムダや問題が解決しないのは、ムダや問題が見えないからで、モノの見方が粗いからです。IEはモノの動きを細かく見ていく方法ですから、IEを学ぶと、今まで分からなかった問題が見えてくるようになります。
IEの特色は、下図のように仕事を工程→作業(単位作業→要素作業)→動作(要素動作:サーブリッグ)とだんだん細かく分けていき、それぞれについて、「ムリ」「ムダ」「ムラ」をなくしていくことにあります。
下図は、教師の仕事を分析した例です。工程単位で見た場合、教師の仕事の付加価値を上げるためには、さしあたっては、○の部分(授業等)の占める割合を増やす必要があります。どんなにがんばって移動しても、付加価値は生まれません。○の部分で問題が見つからなければ、次は、単位作業の分析をします。
IEの基礎となる作業研究
IEは、テイラーの時間研究と、ギルブレス夫妻の動作研究を源に今日に至っています。そして、両者が発展、融合して体系化されたものが「作業研究」です。体系化の過程で、IE技術の適用範囲は非常に広範囲になり、IEの分析技術と内容も高度、複雑になり、習得するのが容易でない状況になりました。
このようなことから、IEは一時衰退しました。
しかし、VTR等の分析機器の発展にともない、専門的なIEの分析技術を知らなくとも、ムダを見つけることは容易になっています。
IEを大まかに整理すると、下図のように、工程や作業方法、手順を調査分析して改善する方法研究と、作業に必要な時間を測定して無効時問を排除したり、標準時問を設定する作業測定の2面からなっています。
方法研究:3ム(ムリ、ムダ、ムラ)のある工程や作業、および動作を分析し、経済的かつ安全で楽な作業方法をつくリ出すことです。主な着眼点として、「動作経済の原則」があります。
作業測定:作業システムや構成要素の働きを時間という尺度で数値化し、改善や維持の目安とするものです。大別すると、連続時間分析法とW・S(ワークーサンプリング)法になります。
理解を容易にするために、製品の検査に全数検査と抜き取り検査があるように、仕事の全数検査が連続時間分析法で、仕事の抜き取り検査がW・S法と見ればよいでしょう。
作業研究に必要な工程分析
作業研究で、まず必要なのは「工程分析」です。工程分析では、原材料が加工されて完成品へと変化していく過程を調べて、製品工程分析表を作成します。工程分析は、加工、運搬、検査、停滞の4つに分けられます。
①加工…数種類の部品を組み立てたり、分解および材料を変形、変質させるプロセスをいいます。
②運搬…モノを移動させることで、機械運搬と人による運搬に大別されます。
③検査…測定器等で基準との比較をすることで、量の検査と質の検査に大別されます。
④停滞…材料や部品が加工、運搬、検査されないで置かれている状態をいい、停滞(工程間の一時的な待ち)と貯蔵(指定された保存)に大別されます。停滞期間の短縮が生産期間短縮に大いに寄与すると言われています。
工程分析を行うと、職場の実態が明確になってきます。たとえば、一回ですむはずの運搬を何箇所も積み降ろして、繰り返し運搬されている場合、分析することで運搬のムダがよく見え、レイアウトの設計や運搬(回数と距離)の減少に役立てることができます。
生産量を前工程受け入れ数量と後工程の払い出し数量の差で把握すると、仕掛数量と仕掛期間が分かり、仕掛数量の減少に役立てることができます。分析した4つの各工程に時問を入れると、付加価値を生み出さない工程の割合が分かり、問題工程として改善の的が絞りやすくなります。
要素動作改善のための動作分析
同じ作業でも、慣れた人と慣れていない人とでは、仕事のスピード、正確性に違いがあります。慣れた人はキーボードに目はいっていません。目は資料とディスプレイを交互に見ているだけで、両手は迅速にキ-をたたいています。
現場の作業もまったく同じことが言えます。慣れた人は慣れない人に比べ、作業は何倍も速く、正確で楽に仕事をこなしているのです。そこで、ムリ・ムダ・ムラのない作業方法や手順を研究し、作業に慣れていない人でも効率の良い作業ができるよう、体系的に研究されたのが「動作分析」です。
問題が見えないのは、モノの見方が粗いからにほかなりません。作業内容を細かい動作に分解していくと、「要素動作」となり、作業を分析するときの最小単位になります。
ギルブレスによって始められ、現在、要素動作(基本要素)となっているものは、下図のとおりです。生産現場では、第2類、第3類の要素動作を排除することが望まれます。
動作経済の原則
動作分析をして作業を改善するといっても、どこに絞つて着眼するかが大切です。改善は人の動作を改善するだけでなく、部品、治工具、機械などの置き方、レイアウト等を含め、人が効率良くしかも経済的で安全かつ楽に作業できるような方法が必要になってきます。
動作経済の原則とは、ギルブレスが経験からまとめた「人間が最小限の疲労で最高の能率をあげられるように、もっとも良い作業動作を実現するための方法」を、その後の動作研究者が充実させていったものです。
動作経済の原則には次のような4つの基本原則があります。
①動作の数を減らす
②身体部位を同時に使う
③動作の距離を短くする
④動作を楽にする
さらに、この4つの基本原則を次のように3つに分類します。
①動作方法の原則(身体の使用に関する動作経済)
②作業環境の原則(作業配置に関する動作経済)
③治工具・機械の原則(工具および機械の設計に関する動作経済)
(1)動作の数を減らす
不必要な動作はなくし、動作の数を減らします。
必要な動作もできるだけ少なくしていくと、作業は楽で速くできるようになります。
不必要な動作とは、よく分析してみるとその仕事の目的に何の役にも立っていない動作のことです。
動作の数を少なくする着眼点は、要素動作改善の目安で説明した、第2類と第3類の動作を排除することです。
(2)身体部位を同時に使う
作業をつぶさに観察すると、片方の手はよく動いているのですが、他方の手はまったく遊んでいたり、その援助をしているだけの場合が多いものです。両手は同時に動作を始めて終わるようにし、両手が遊ばないようにします。手だけでなく同時に足を使う工夫をすると、作業はさらに楽で速くできるようになります。
(3)動作の距離を短くする
動作で時間を必要とするものを見つけ、短縮していきます。動作時間短縮の着眼点は、次の事柄が考えられます。
①歩行の排除
②腕の移動は正常作業域で
③かがむ、立つことの排除
④身体の回転(横を向く、後ろを向く)の排除以上のことから、材料や工具は作業場所のできるだけ近いところに置き、正常作業域で作業することを考えて、時間短縮の工夫をします。
(4)動作を楽にする
ムリな姿勢の作業や重い荷物運びなどに対し、楽で、力をそれほど必要としない仕事のやり方を考えます。また、作業台の高さは作業者の身長に合わせ、照明もルクス管理(検査、精密作業等)を行い、継続する作業の場合、疲労で能率や精度が落ちない工夫が必要です。騒音、振動、粉塵、臭気等の対策も考え、職場環境をよくする必要があります。
標準時間とは?
作業システムや構成要素の働きを、時間という尺度で数値化し、計画や作業の目安とするとき、時間は作業のやり方や作業をする人の熟練度などで違ってきます。このようなとき、標準になる時間、つまり標準時間があれば、計画は楽に立てることができます。
標準時間は、次のように定義づけることができます。
①作業をするために必要な熟練度を持った作業者が
②所定の仕事を定められた作業条件のもとで
③無理のない良好な作業方法と作業速度で
④顧客の要求品質をつくり出し
⑤所定の量の作業を達成するために必要な時間
標準時間は、日程計画、原価の見積り、外注単価の決定、適正人員の算定など、経営における諸管理の基準として大変重要なものです。標準時間が設定されてないと、計画はドンブリ勘定となり、あらゆる箇所でロスを生じます。
一方、標準時間を完全に設定しようとすると、多くの工数が必要となります。すべての作業に同レベルの標準時間を設定する必要はありません。重要なものだけ必要な精度で、設定するのも一つの方法です。
たとえば、問題工程は精度の高い分析をして、標準時間を設定するが、一度分析した類似工程や全体を把握するためだけのものは、粗い精度で分析してもよいでしょう。
標準時間の基本的な手順を示すと、下図のようになります、標準時間の設定法はいろいろあります。精度の高いものはかなり技術を必要とします。
具体的なIE分析の改善事例については下記のサイトを参照してください。
関連記事:事例で学ぶIE分析~科学的な作業改善
トヨタ生産方式に学ぶIE手法の活用
「トヨタ生産方式に学ぶIE手法の活用」というテーマは、生産性向上や業務改善に関心のある読者に非常に有益です。以下に、記事の構成案とポイントをまとめてみました。
はじめに:なぜ今、IE(Industrial Engineering)なのか?
現代の製造業における課題(人手不足、コスト圧力、多品種少量生産)
トヨタ生産方式(TPS)がなぜ世界的に評価されているか
TPSに深く根差したIE(インダストリアル・エンジニアリング)手法の重要性
トヨタ生産方式の概要
ジャストインタイム(JIT)
自働化(じどうか)=人の知恵を活かす機械化
ムダの排除の徹底
現場・現物・現実(3現主義)
トヨタ生産方式 × IE手法の具体的な活用事例
1. 動作経済の原則の活用
工具や部品の配置を見直すことで動作を削減
例:組立ラインでの手の移動距離を30%削減
2. 標準作業の設定と多能工化
工程ごとの標準時間を設定し、習熟度の平準化
例:一人三工程の対応で人員配置最適化
3. 工程分析を活かしたレイアウト改善
IEの工程分析図とTPSの「1個流し」を融合
例:直線ラインからU字ラインへの変更で、リードタイムを半減
TPSとIEの相互補完性
TPSは哲学・思想、IEは技術・手法
TPSはIEを「どう活かすか」の方向性を与える
IEはTPSの実現に必要な分析力と改善ツールを提供
IE手法を活かした“考える現場”づくり
現場の改善は“数字”と“動き”の両方を見ることが重要
IE手法で「見える化」→ TPSで「改善の文化」へ
トヨタに学びつつ、自社にあった現場改善スタイルを築くことが大切
作業分析の重要性とその実施方法
〜ムダを見抜く目を養い、現場改善を加速させる〜
1. 作業分析とは何か?
作業分析とは、現場の作業を「分解・観察・記録」して、その中に潜むムダ・ムリ・ムラを明らかにする手法です。
IE(インダストリアル・エンジニアリング)の基本中の基本であり、トヨタ生産方式(TPS)でも根幹を支える技術のひとつです。
ポイント:
作業の「見える化」
問題の根拠を“感覚”でなく“データ”で捉える
改善活動の出発点
2. なぜ作業分析が重要なのか?
(1)ムダの発見と排除
トヨタ生産方式の基本は「ムダの徹底排除」です。
作業分析を通じて、次のようなムダが可視化できます。
運搬のムダ(材料を何度も移動)
動作のムダ(手の無駄な動き)
待ちのムダ(次の工程が空かない)
(2)標準化のベース
作業のばらつきを把握し、最適なやり方(標準作業)を決めるための基礎資料になります。
(3)教育と伝承
新人教育においても、分析された作業があると、指導内容が明確になります。
3. 作業分析の実施方法
以下のステップで進めるのが基本です。
Step 1:現場観察・作業の把握
まずは“何をやっているか”を全体的に観察
3現主義(現場・現物・現実)を大切に
Step 2:作業の分解と記録
「主作業」「付随作業」「ムダな作業」などに分類
ストップウォッチなどを使って時間測定
📋 使えるツール例:
作業票(作業手順の一覧)
時間観測表
フローダイアグラム(流れ図)
動作分析図(サーブリッグチャートなど)
Step 3:ムダの抽出と課題設定
「この動作、本当に必要?」を問い直す
動作経済の原則(両手同時使用、反復動作の削減など)を活用
Step 4:改善案の立案と実行
工具の配置変更、作業順の見直し、人員配置の再検討など
小さな改善でも実行が大切
4. 具体事例:作業分析からの改善成功例
例:組立ラインの工具配置見直し
【Before】
作業者が1工程で3回、工具を取りに屈伸動作。
→ 1日あたり300回の余分な動作。
【After】
工具を目線の高さに配置し、取りやすく変更。
→ 動作時間を1日30分削減、腰痛予防にも効果あり。
作業分析は“現場の鏡”
作業分析は、単なるデータ取りではありません。
現場の人たちが「なぜこのやり方をしているのか?」を見直し、知恵を出し合うための“対話の土台”になります。
✅ 改善は、気合いや根性でなく、分析と仕組みで。
✅ 作業分析は、地味だけど最も確実な改善の第一歩です。
IE分析ツールの活用方法
具体的なツールの種類とその使い方をわかりやすく解説していきます。トヨタ生産方式と絡めつつ、即実践できる内容を意識して構成します。
〜ムダの可視化と改善アイデアの創出に役立つ必須ツール〜
1. なぜIE分析ツールが必要なのか?
IE(Industrial Engineering)の本質は、**“作業を見える化し、合理的に改善すること”**です。
そのためには、現場で起きていることを客観的に捉える“道具”が不可欠です。
IE分析ツールは、作業の流れ・時間・動作などを数値や図で「見える化」し、改善のヒントを与えてくれます。
2. 主なIE分析ツールとその活用方法
① フロープロセスチャート(工程分析図)
✅ 何を分析する?
作業を「運搬」「加工」「検査」「待ち」「貯蔵」などに分類し、工程全体を整理。
✅ どんな場面で使う?
製造ラインや事務業務など、業務フローの全体を把握したいとき。
✅ 活用ポイント:
工程数を減らせないか検討
「加工以外の比率」が高ければ改善余地あり
② フローダイアグラム(流れ図)
✅ 何を分析する?
作業者やモノの移動経路を、平面レイアウトに沿って図示する。
✅ どんな場面で使う?
工場や作業エリアのレイアウト改善、ムダな運搬の削減に有効。
✅ 活用ポイント:
動線がジグザグなら改善チャンス
「1個流し」「U字ライン」などTPSと連携しやすい
③ 稼働分析表(時間分析・ワークサンプリング)
✅ 何を分析する?
作業者の1日の時間を、「作業時間」「待ち時間」「ムダな時間」に分類して割合で捉える。
✅ どんな場面で使う?
人の稼働率、作業の平準化、設備との兼ね合いを見たいとき。
✅ 活用ポイント:
稼働率が60%未満なら、非稼働時間を見直す
多能工化やセル生産導入の判断材料にも
④ サーブリッグチャート(動作分析図)
✅ 何を分析する?
作業を細かく「取る・運ぶ・使う・置く」などの動作に分解して記録。
✅ どんな場面で使う?
組立作業、検査作業などの繰り返し動作におけるムダ取り。
✅ 活用ポイント:
片手が遊んでいる時間を削減
動作経済の原則(最短距離、左右対称動作)を意識
⑤ 時間研究(ストップウォッチ法)
✅ 何を分析する?
作業ごとの時間をストップウォッチで測定して、標準時間を設定。
✅ どんな場面で使う?
標準作業の確立、作業のばらつき是正に。
✅ 活用ポイント:
観測回数はなるべく多く
熟練者と初心者の差異を分析して教育に活用
3. IEツールを使った改善事例(簡単に)
事例:ある組立工程の動線見直し
【分析】フローダイアグラムで、工具棚との往復移動が1日100回以上あることが判明。
【改善】作業台に工具を配置 → 1日30分の作業短縮、腰痛も軽減。
4. 活用のコツと注意点
📌 目的を明確にして使うこと!
→「ツールを使うこと」が目的になっては本末転倒。👀 現場の声を聞きながら進めること!
→ 現場の納得がないと、改善は定着しません。📈 定量データと定性観察のバランスが大事!
→ 数字だけでなく、「なぜその動作があるか」の背景も大切。
IEツールは“現場の知恵”を引き出すカギ
IE分析ツールは、単なる図や表ではなく、「気づきと改善」を生み出すための“対話の起点”です。
トヨタ生産方式が重視する「現地現物主義」と組み合わせて使うことで、机上の空論ではない、実践的な改善が可能になります。
生産管理とIE手法の関係性
「生産管理とIE手法の関係性」は、工場や現場改善を担う担当者だけでなく、マネジメント層にも刺さる内容です。
ここでは、「生産管理=マネジメントの視点」「IE=現場改善の技術」という視点で、それぞれの役割と関係性をわかりやすくまとめてみます。
〜“計画”と“改善”の両輪で回す、ものづくりの仕組み〜
1. 生産管理とは何か?
生産管理とは、「QCD」(品質・コスト・納期)を満たすために、生産活動を計画・調整・統制するマネジメントのことです。
主な目的:
必要なときに、必要な量を、ムダなく作る
品質・納期・コストの最適化
作業者や設備の能力を最大限に活かす
主な機能:
生産計画(需要予測、資材計画、工程設計など)
作業指示・進捗管理
在庫管理・購買管理
3. 生産管理とIE手法の関係性とは?
🔄 補完関係:計画 × 実行 × 改善
項目 | 生産管理 | IE手法 |
---|---|---|
目的 | 生産の最適化(QCD管理) | 作業の効率化・改善 |
視点 | マネジメント・全体最適 | 作業・現場の最適化 |
方法 | 計画・統制・指示 | 分析・改善・標準化 |
役割 | 何を・いつ・どれだけ作るか | どうやって効率よく作るか |
→ 生産管理が“地図”を描き、IEが“道”を整備するような関係
4. 両者が連携することで得られるメリット
✅ 計画が実行に落とし込める
IEがあるからこそ、生産計画が現場で無理なく実現可能に。
✅ 改善が数字に直結する
IEによる作業効率化が、コスト・納期短縮に直結。
✅ 改善PDCAが回しやすくなる
生産管理がKPI(例:生産性、在庫回転率)を提示 → IEが現場で改善実行 → 結果を再び管理にフィードバック。
5. 具体事例:生産管理×IEの連携による改善
事例:組立ラインの生産性向上プロジェクト
【生産管理】
生産計画上、1人あたり10台/日の生産が必要。【IE分析】
現場では実際に7台/日が限界 → 作業分析でムダ発見。【改善内容】
部品配置の見直し、標準作業の再設定、工具の自動化。【結果】
生産性が10台/日に到達し、納期遅れゼロを実現。
生産管理とIEは“現場と経営をつなぐパートナー”
生産管理が**「全体を最適化する計画」**を描き、
IEが**「現場を最適化する改善」**でそれを支える。
現場改善にIE、経営判断に生産管理。
この両輪がかみ合うことで、持続可能な強い現場が実現できます。
時間の最適化とIE手法
「時間の最適化とIE手法」は、業務改善・生産性向上の核心に迫る内容です。IE(Industrial Engineering)における**“時間”はコストそのもの**とも言えるため、読者にとっても興味深い切り口になります。
以下に、記事構成と本文案を提案します(現場目線+マネジメント視点も意識してます)。
~「1秒を削る」改善が、現場を変える~
1. なぜ「時間の最適化」が重要なのか?
時間は全ての生産活動の基礎です。
製造業では、「時間=コスト」「時間=納期」「時間=人の負荷」とも言えます。
1つの作業が3秒縮まる → 年間で100時間以上の工数削減
リードタイムの短縮 → 顧客満足と在庫削減につながる
IE手法を活用すれば、**「時間を科学的に見える化・最適化」**できます。
2. 時間を最適化するIE手法とは?
以下のようなIEの代表的な分析・改善手法が「時間最適化」に直結します。
① 時間研究(タイムスタディ)
概要:
作業ごとの所要時間をストップウォッチなどで測定し、「標準時間」を設定。
活用場面:
作業時間のばらつき是正
過剰な工数の可視化
標準作業の策定
ポイント:
観測回数を十分に取る
熟練者と初心者の差も把握する
② ワークサンプリング(作業比率の見える化)
概要:
作業者をランダムに観察し、作業時間と非作業時間(ムダ時間)を確率的に把握する。
活用場面:
非稼働時間(待ち、手待ち)の把握
工数配分の最適化
ポイント:
観測は無作為に、長時間にわたって行う
稼働率の数値化 → 改善KPIになる
③ 動作分析(サーブリッグチャートなど)
概要:
作業を「取る・持つ・使う・置く」などの細かい動作に分解し、不要な動作を削除。
活用場面:
工具の取り回し改善
部品配置の見直し
作業動線の短縮
ポイント:
動作経済の原則(両手同時、最短距離など)を応用
たとえ1秒でも、毎日の積み重ねが大きな改善に
④ 標準作業の設定
概要:
最も効率的かつ安全な手順と時間を「標準作業」として定義し、全員がそれに沿って作業。
活用場面:
作業のばらつき防止
教育・多能工化の基礎資料
改善後の再評価
ポイント:
改善→標準化→再評価、のPDCAサイクルを回すこと
3. 時間最適化による効果(事例あり)
事例:組立ラインでの時間研究
【Before】 工程ごとのばらつきが大きく、後工程がしょっちゅう待ち状態
【改善策】 時間研究で各作業時間を可視化 → 工程バランスを調整
【After】 総生産時間が15%短縮。人員の配置も最適化
4. 時間最適化のポイントは“全体を見る目”と“1秒を惜しむ意識”
IEは単なる“作業効率化”に見られがちですが、
本質は**「最小の時間で最大の価値を生み出すための現場設計」**です。
全体の流れ(リードタイム)を意識する
現場の声を聞いて、ムリ・ムダ・ムラを見つける
時間短縮が人の負担にならない工夫も必要
5. まとめ:時間短縮は、“現場力”の指標になる
時間はウソをつきません。
だからこそ、IE手法で時間を測り、分析し、改善していくことが、確実な生産性向上につながります。
時間の最適化は「ムダの可視化」から
1つひとつの動作・工程の“意味”を問い直す
IE手法は、その“見える化”と“改善”をサポートする強力なツール
実践的なIE 改善手法の導入事例
「実践的なIE 改善手法の導入事例」は、多くの現場担当者にとって”すぐに参考にできるリアルなネタ”として非常に有益です。
~現場が変わる!ムダ取り・時間短縮・生産性向上のリアル事例~
1. 組立ラインでの動作分析による時間短縮
背景と課題
ある電子機器メーカーの組立ラインでは、作業時間のばらつきが大きく、ラインバランスが崩れていた。熟練者と新人で1台あたり約40秒の差。
活用したIE手法
動作分析(サーブリッグチャート)
動作経済の原則(両手使用、動作の簡素化)
実施内容
組立台のレイアウト変更(工具・部品の配置最適化)
作業の順序を見直し、標準手順を明確化
両手が同時に使えるよう治具を導入
効果
1台あたりの組立時間を約15%削減(平均40秒→34秒)
作業のばらつきが小さくなり、ラインバランス改善
教育時間も短縮され、多能工化が進展
検査工程におけるワークサンプリングで稼働率向上
背景と課題
検査部門で作業者がよく“手待ち状態”になっているとの声。
ただし、明確なデータがなかったため改善が進まない状況。
活用したIE手法
ワークサンプリング
時間稼働比率の分析
実施内容
3日間、5分間隔で作業者の状態を無作為に観察(観測回数:200回)
作業中:60%、待機中:30%、ムダ作業:10%という結果
待機の要因は、前工程の遅れ+検査対象の偏りと判明
効果
検査スケジュールの平準化、作業割当の見直し
検査の前工程にバッファエリアを設けて連携強化
稼働率が60% → 85%に改善し、納期遅れがゼロに
3. 工場レイアウト変更による運搬のムダ削減
背景と課題
金属加工工場で、工程間の部品運搬が多く、台車の往復が1日300回以上。運搬時間が全体の20%を占めていた。
活用したIE手法
フローダイアグラム(動線分析)
工程分析(フロープロセスチャート)
実施内容
現行レイアウトの動線を図に起こし、ムダな往復を可視化
工程の配置をU字型セルラインに変更
台車運搬を自動搬送車(AGV)に一部置換
効果
運搬回数が300回→100回に削減
作業者の歩行距離は1日5km→2kmに
年間150万円の労務コスト削減を実現
標準作業票を活用した教育効率化
背景と課題
新人作業者の習熟に時間がかかり、ベテランの手が取られる状況が続いていた。
活用したIE手法
標準作業票の作成と活用
動作と時間の分解 → 作業教育資料に転用
実施内容
ベテラン作業者の動作・時間を分析し、標準手順として文書化
写真と図を用いたマニュアルを作成
5Sも意識して作業環境を整備
効果
新人の独り立ちまでの期間が30%短縮
教育担当の負荷が軽減 → 他業務との両立が可能に
教育の“バラツキ”が減り、品質も安定
IE手法は“現場の課題”を数字で解決する
実際の現場にIE手法を導入することで、
目に見えなかった「ムダ」や「非効率」を可視化できる
科学的なアプローチで説得力ある改善ができる
改善の効果が「数字」で実感できる
IE手法のデジタル化と未来の展望
~“ストップウォッチからセンサーへ”、IEの進化と新しい改善のかたち~
1. なぜIEのデジタル化が求められているのか?
従来のIE手法は、ストップウォッチによる時間観測、手書きの工程図、紙ベースの作業票など、「人の目と手」に大きく依存していました。
しかし現在、製造現場には以下のような課題が迫っています:
熟練IE人材の高齢化・減少
多品種少量生産と短納期への対応
正確かつ迅速な改善サイクルの要求
データドリブン経営への移行
その解決策として、「IEのデジタル化」が進んでいます。
2. デジタルIE手法の代表例と活用イメージ
① 動作解析ツール(ビデオモーション分析)
📹 概要:
作業者の動きをカメラで撮影し、動作・時間を自動分析。
手動でのストップウォッチ計測を不要にし、精度もアップ。
💡 メリット:
作業のばらつきやムダ動作を瞬時に可視化
データ蓄積により継続的改善が可能
🛠 活用ツール例:Time Prism、MotionBoardなど
② IoTセンサー × 稼働分析
概要:
作業台や設備にセンサーを設置し、人や機械の稼働・停止・動線をリアルタイムで把握。
メリット:
ワークサンプリングが“自動化”される
停止時間や待機の要因が明確に
生産性やOEE(設備総合効率)を定量的に把握
③ デジタル標準作業帳票(タブレット化)
概要:
標準作業を動画やアニメーション、図入りでデジタル化。タブレットやスマホで現場に提示可能。
メリット:
教育スピードが向上
多言語対応や習熟度に応じた指導がしやすい
改訂や共有もクラウドで即時反映
④ AIによる工程改善提案(生成AI・機械学習)
概要:
工程データや動作映像から、AIがボトルネックや改善ポイントを自動抽出。
メリット:
人の目では気づけないパターンを発見
例えば「工具を右に置くと0.8秒短縮」など提案可能
改善サイクルのスピードが飛躍的に向上
3. IEデジタル化の導入事例(簡略)
事例:部品組立工場での動作解析ソフト導入
作業映像をAI分析 → 不要な“部品の探し動作”が多いと判明
部品棚を見やすい位置に変更
結果:1人あたりの作業時間が7秒短縮、1日で30分の工数削減
4. 未来のIEは「人とAIの共創」へ
IE手法は、デジタルによって「より速く・広く・深く」進化しています。
従来のIE | これからのIE(デジタルIE) |
---|---|
人の経験と勘に頼る | データとAIに基づく判断 |
手作業で測定・記録 | センサー・映像で自動取得 |
局所的な改善 | 全体最適視点での改善 |
ただし、「現場を見る力」や「改善の哲学(ムダ取り・3現主義)」は今後もIEの本質として残ります。
AIが分析しても、改善を形にするのは人の知恵と現場力です。
デジタル化はIEの“進化”、“代替”ではない
デジタルIEは、作業分析を加速させる“エンジン”
未来のIEは「人×データ×テクノロジー」の融合
トヨタ式の“現場主義”と、最新技術のハイブリッドが鍵
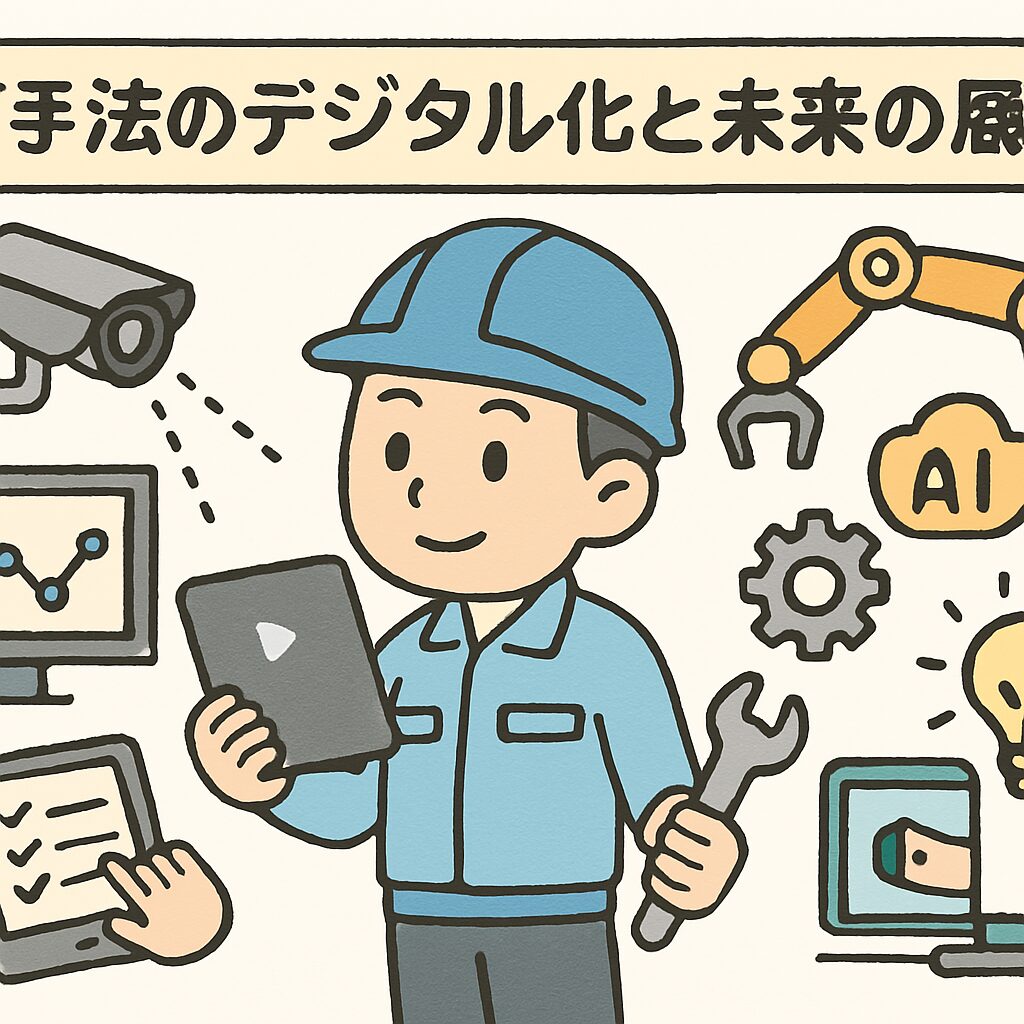
未来のIEは「人とAIの共創」へ
*工場のIE手法については下記の文献に色々な活動事例等が更に詳細に記載されています。
参考文献: